-
Номинальный размер, предельные размеры, действительный размер.
Номинальный
размер – это
основной (расчетный) размер, показанный
на чертеже. Он обычно указывается на
чертеже целыми числами миллиметра, но
иногда встречаются и доли миллиметра.
Предельный
размер –
называются такие размеры, между которыми
колеблется действительный размер. Один
из предельных размеров (верхняя граница)
называется наибольшим предельным
размером, а другой (нижняя граница)
-наименьшим предельным размером.
Действительный размер не должен быть
выше наибольшего предельного размера
и ниже наименьшего предельного размера.
Действительный
размер -это
размер готовой детали, определенный в
результате непосредственного измерения.
-
Предельные отклонения, допуск
Предельные
отклонения – разность
между допускаемым предельным наибольшим
или наименьшим и номинальным размерами.
Допуск
– разность
между наибольшим и наименьшим предельными
значениями параметров (размеров, массовой
доли, массы), задаётся на геометрические
размеры деталей, механические, физические
и химические свойства. Назначается
(выбирается) исходя из технологической
точности или требований к изделию
(продукту). Любое значение параметра,
оказывающееся в заданном интервале,
является допустимым.
-
Посадка, зазор, натяг.
Посадка
– характер соединения деталей, определяемый
разностью диаметров отверстия и вала
до сборки. В зависимости от взаимного
расположения полей допусков отверстия
и вала посадка может быть с зазором, с
натягом или переходной, при которой
возможно получение как зазора так и
натяга.
Зазор
– называют
разность между действительными размерами
отверстия и вала, когда отверстие больше
вала;
Натяг
– называют разность между действительными
размерами вала и отверстия, когда вал
больше отверстия.
-
Системы посадок, система вала, система отверстия.
Система
посадок – Различают
две системы допусков и посадок в
зависимости от того, что считается в
соединении основным – вал или отверстие:
в системе отверстия основной деталью
служит отверстие, оно обозначается
буквой А, а в системе вала основной
деталью является вал, который обозначается
буквой В.
Система
вала – характеризуется
тем, что в ней для всех посадок одной и
той же степени точности (одного класса),
отнесенных к одному и тому же номинальному
диаметру, вал имеет постоянные предельные
отклонения, разнообразие же посадок в
этой системе осуществляется за счет
изменения предельных отклонений
отверстия.
Система
отверстий –характеризуется
тем, что в ней для всех посадок одной и
той же степени точности (одного класса),
отнесенных к одному и тому же номинальному
диаметру, отверстие имеет постоянные
предельные отклонения, разнообразие
же посадок получается за счет изменения
предельных отклонений вала.
-
Виды посадок, посадки с зазором, посадки с натягом, переходные посадки.
Виды
посадки – Различные
посадки определяют степень свободы
относительного перемещения деталей;
их назначают исходя из условий работы
машин и механизмов, их точности и условий
сборки. Посадки по характеру соединения
деталей делятся на 3 группы.
Посадка
с зазором
-посадка, при которой обеспечивается
зазор в соединении поле допуска отверстия
расположено над полем допуска вала, а..
К посадкам с зазором относятся также
посадки, в которых нижняя граница поля
допуска отверстия совпадает с верхней
границей поля допуска вала, т. е. Smin= 0.
Переходная
посадка –
посадка, при которой возможно получение
как зазора, так и натяга (поля допусков
отверстия и вала перекрываются частично
или полностью
Посадка
с натягом –
посадка, при которой обеспечивается
натяг в соединении поле допуска отверстия
расположено под полем допуска вала.
Соседние файлы в предмете [НЕСОРТИРОВАННОЕ]
- #
- #
- #
- #
- #
- #
- #
- #
- #
- #
- #
Не совсем так, вернее совсем не так
РМГ 29-2013 https://files.stroyinf.ru/Data2/1/4293772/4293772305.pdf в помощь
Цитата
3.2 размер величины: Количественная определенность величины, присущая конкретному материальному объекту или явлению.
…..
5.1 результат (измерения величины): Множество значений величины, приписываемых измеряемой величине вместе с любой другой доступной и существенной информацией.
Примечания 1 Определение понятия результата измерения претерпело существенное изменение по сравнению с определением РМГ 29—99 и вобрало в себя выражение точности измерения. Информация, приводимая в результате измерения, определяется особенностями конкретного измерения и соответствует требованиям, предъявляемым к этому измерению. В большинстве случаев информация относится к точности измерения и выражается показателями точности, в обоснованных случаях содержит указание методики измерений и др.
2 Результат измерения может быть представлен измеренным значением величины с указанием соответствующего показателя точности. К показателям точности относятся, например, среднее квадратическое отклонение, доверительные границы погрешности, стандартная неопределенность измерений, суммарная стандартная и расширенная неопределенности. VIM3 [1] предусматривает также представление результата измерений плотностью распределения вероятностей на множестве возможных значений измеряемой величины.
3 Если значение показателя точности измерений можно считать пренебрежимо малым для заданной цели измерения, то результат измерения может выражаться как одно измеренное значение величины. Во многих областях это является обычным способом выражения результата измерения, с указанием класса точности применяемого средства измерений.
5.2 измеренное значение (величины): Значение величины, которое представляет результат измерения.
……
5.6 действительное значение (величины): Значение величины, полученное экспериментальным путем и настолько близкое к истинному значению, что в поставленной измерительной задаче может быть использовано вместо него.
Изменено 11 Ноября 2019 пользователем владимир 332
Учитывая, что с повышением точности уменьшается производительность труда и удорожается изготовление изделия, а c уменьшением точности снижается качество его работы, на практике точность изготовления выбирают такой, чтобы она обеспечивала необходимую долговечность работы изделия, взаимозаменяемость деталей и узлов и чтобы стоимость изготовления их не выходила за пределы допустимого.
Точность изготовления назначается в виде допустимых отклонений действительных размеров от номинальных. Для этой цели установлены системы допусков и посадок.
В нашей стране с 1977 года действует единая система допусков и посадок (ЕСКД), в которой даны основные термины и определения, поля допусков, посадки и основные отклонения. Все механизмы и машины состоят из деталей, которые в процессе работы совершают относительные движения или находятся в состоянии относительного покоя. Каждая деталь – это комбинация простейших геометрических тел, называемых элементами, ограниченных простейшими поверхностями: плоскими, цилиндрическими, коническими и т. д. Две детали, элементы которых входят друг в друга, образуют соединение и называются сопрягаемыми деталями, а поверхности соединяемых элементов – сопрягаемыми поверхностями. Остальные поверхности называются несопрягаемыми. В соединении элементов двух деталей один из них называется охватывающим, другой – охватываемым. Для цилиндрических соединений они носят название соответственно отверстие и вал. Эти термины условно применимы и к другим охватывающим и охватываемым поверхностям.
Номинальный размер соединения d (рис. 1) служит началом отсчёта отклонений и соответствует нулевой линии.
![]() |
Действительным размером называют размер, полученный измерением с допускаемой погрешностью
Размеры, между которыми может находиться действительный размер, называются предельными. Один из них называется наибольшим предельным размером (Dmax, dmax), другой – наименьшим предельным размером (Dmin, dmin). Алгебраическую разность между действительным и номинальным размерами называют действительным отклонением. Оно может быть положительным и отрицательным.
Верхнее предельное отклонение (ES – для отверстия, es – для вала):
ES = Dmax ─ d, еs = dmax ─ d , (1)
Нижнее предельное отклонение (EI – для отверстия, ei – для вала):
EI = Dmin ─ d, ei= dmin ─ d. (2)
Отверстие, имеющее нижнее отклонение, равное нулю (EI = 0), называется основным. Вал, имеющий верхнее отклонение, равное нулю (es = 0), называется основным.
Разность между наибольшим и наименьшим размерами называют допуском (IT) размера (всегда положительное число):
для отверстия
IT = TD = Dmax− Dmin = ES −EI, (3)
для вала
IT = Td = dmax− dmin = es−ei. (4)
Поле допуска − поле, ограниченное верхними и нижними отклонениями, − определяется числовым значением допуска размера и его положением относительно номинального размера (нулевой линии).
Поле допуска принято обозначать буквой (или двумя буквами) латинского алфавита: прописной для отверстия и строчной для вала (например, H5, F7, h8 и т. д.).
При увеличении допуска на размер требование к точности снижается, и производство детали упрощается и удешевляется. При одном и том же допуске деталь большего размера изготовить сложнее, чем деталь меньшего размера. Поэтому допуск размера IT назначают в зависимости от диаметра, вводя единицу допуска
(5)
(в формуле (2.5) диаметр d в мм).
Тогда допуск размера
IT = a∙i , (6)
где а − число единиц допуска.
В зависимости от числа а единиц допуска i стандартом установлено 19 квалитетов степеней точности − степеней градации значений допусков: 01; 0; 1; 2; 3; …..15; 16; 17. Например, IT3 означает допуск по 3-му квалитету.
В общих чертах можно указать на следующее применение квалитетов:
−01…3-ий квалитеты предназначены для калибров, измерительных инструментов;
−4-ый и 5-ый квалитеты − для особо точных соединений (применяются сравнительно редко);
−6-ой 7-ой квалитеты − для ответственных соединений в механизмах, где к посадкам предъявляются высокие требования в отношении зазоров и натягов для обеспечения механической прочности деталей, точных перемещений, плавного хода, герметичности соединений и обеспечении точности сборки деталей;
−8-ой…10-ый квалитеты − для посадок, обеспечивающих среднюю точность сборки;
−11-ый…13-ый − в тех случаях, когда необходимы большие зазоры и допустимы их колебания;
−14-ый…17-ый квалитеты − для несопрягаемых (свободных) размеров.
Величины верхнего и нижнего предельных отклонений указываются на чертежах тремя способами:
1) мелкими цифрами (в мм) за номинальным размером (отклонения, равные нулю, не проставляются). Отклонения могут иметь одинаковые или разные знаки, например:
2) условным обозначением поля допуска, состоящим из буквы и цифры, обозначающей квалитет, например:
12G8, 20h10;
3) одновременным указанием поля допуска и цифровых значений отклонений (в скобках), например:
Характер соединения (сопряжения) деталей определяется посадкой.
Она зависит от действительного размера вала и отверстия. Если диаметр отверстия больше диаметра вала, то в соединении между ними будет зазор S (рис. 2 а), обеспечивающий свободное осевое и окружное перемещение одной детали относительно другой:
S = D − d (7)
Если размер отверстия меньше размера вала, то в соединении образуется натяг N (рис. 2 б):
N = d − D (8)
Все посадки разделяют на три группы: с зазором, с натягом и переходные.
Посадка с зазором (подвижная посадка) характеризуется наличием зазора в соединении. При графическом изображении этой посадки поле допуска отверстия расположено над полем допуска вала (рис. 3). К посадкам с зазором относятся также посадки, в которых нижняя граница поля допуска отверстия совпадает с верхней границей поля допуска вала. Эту посадку применяют в подвижных соединениях (в подшипниках скольжения, в соединениях, подвергаемых частой разборке-сборке).
Наиболее часто употребляемыми посадками с зазорами являются:
Посадка с натягом (неподвижная посадка) – посадка, которая в сопряжение обеспечивает натяг (поле допуска вала расположено над полем допуска отверстия) (рис. 4). Их применяют для неподвижного соединения деталей без дополнительного крепления.
![]() |
Наиболее часто назначают посадки с натягом:
Переходные посадки – посадки, которые в зависимости от соотношения действительных размеров отверстия и вала могут быть как с зазором, так и с натягом (рис. 5). Их применяют для центрирования сопрягаемых деталей без дополнительного крепления.
Наиболее часто назначают переходные посадки:
Наташа — контент-маркетолог и блогер, но все это не мешает ей оставаться адекватным человеком. Верит во все цвета радуги и не верит в теорию всемирного заговора. Увлекается «нефрохиромантией» и тайно мечтает воссоздать дома Александрийскую библиотеку.
Здравствуйте, на этой странице я собрала полный курс лекций по предмету «Метрология стандартизация и сертификация», кстати студенты обычно называют этот предмет просто «Метрология».
Метроло́гия (от греч. μέτρον «мера» + λόγος «мысль; причина») — наука об измерениях, методах и средствах обеспечения их единства и способах достижения требуемой точности[1]. Предметом метрологии является извлечение количественной информации о свойствах объектов с заданной точностью и достоверностью; нормативная база для этого — метрологические стандарты. wikipedia.org/wiki/Метрология
Если что-то непонятно — вы всегда можете написать мне в WhatsApp и я вам помогу!
Метрология стандартизация и сертификация
Измерительная техника является неотъемлемой частью материального производства. Без развернутой системы измерений, позволяющей контролировать технологические процессы, оценивать свойства и качество продукции, не может существовать ни одна область техники. Измерения служат основой научных знаний.
В машиностроении наиболее распространены линейные и угловые измерения, т. е. измерения линейных и угловых геометрических размеров изделий, шероховатости и волнистости поверхностей, отклонений расположения и формы поверхностей. Высокоточные линейные и угловые измерения обеспечивают взаимозаменяемость изделий, высокое качество, надежность и долговечность машин и приборов. Автоматизация и механизация измерений повышают производительность труда.
Важнейшими требованиями, предъявляемыми к техническим измерениям, являются единство и точность измерений. Единство измерений — такое состояние измерений, при котором их результаты выражены в узаконенных единицах и погрешности измерений известны с заданной вероятностью. Единство измерений обеспечивает взаимозаменяемость изделий, например деталей, изготовляемых по одному чертежу на разных предприятиях. Точность измерений — качество измерений, отражающее близость их результатов к истинному значению измеряемой величины. Чем меньше разность между измеренным и истинным значениями, тем выше точность. Наука об измерениях, методах и средствах обеспечения их единства и способах достижения требуемой точности называется метрологией.
Слово «метрология» происходит от греческих слов metron (мера) и (понятие).
Основные задачи метрологии — это развитие общей теории измерений, установление единиц физических величин, разработка методов и средств измерений, разработка способов определения точности измерений, обеспечение единства измерений и единообразия средств измерений, установление эталонов и образцовых средств измерений, разработка методов передачи размеров единиц от эталонов и образцовых средств рабочим средствам измерений.
Физические величины и их измерение
Измерения основаны на сравнении одинаковых свойств материальных объектов. Для свойств, при количественном сравнении которых применяются физические методы, в метрологии установлено единое обобщенное понятие — физическая величина. Физическая величина — свойство, общее в качественном отношении многим физическим объектам, но в количественном отношении индивидуальное для каждого объекта, например, длина, масса, электропроводность и теплоемкость тел, давление газа в сосуде н т. п. Но запах не является физической величиной, так как он устанавливается с по> мощью субъективных ощущений.
Мерой для количественного сравнения одинаковых свойств объектов служит единица физической величины — физическая величина, которой по определению присвоено числовое значение, равное 1. Единицам физических величин присваивается полное и сокращенное символьное обозначение — размерность. Например, масса — килограмм (кг), время — секунда (с), длина — метр (м), сила — Ньютон
Значение физической величины — оценка физической величины в виде некоторого числа принятых для нее единиц — характеризует количественную индивидуальность объектов. Например, диаметр отверстия — 0,5 мм, радиус земного шара — 6378 км, скорость бегуна — 8 м/с, скорость света —
Измерением называется нахождение значения физической величины с помощью специальных технических средств. Например, измерение диаметра вала штангенциркулем или микрометром, температуры жидкости — термометром, давления газа — манометром или вакуумметром. Значение физической величины полученное при измерении, определяют по формуле
где
— числовое значение (размер) физической величины;
— единица физической величины. Так как значения физических величин находят опытным путем, они содержат погрешность измерений. В связи с этим различают истинное и действительное значения физических величин. Истинное значение — значение физической величины, которое идеальным образом отражает в качественном и количественном отношениях соответствующее свойство объекта. Оно является пределом, к которому приближается значение физической величины с повышением точности измерений.
Действительное значение — значение физической величины, найденное экспериментальным путем и настолько приближающееся к истинному значению, что для определенной цели может быть использовано вместо него. Это значение изменяется в зависимости от требуемой точности измерений. При технических измерениях значение физической величины, найденное с допустимой погрешностью, принимается за действительное значение.
Погрешность измерения есть отклонение результата измерений от истинного значения измеряемой величины. Абсолютной погрешностью называют погрешность измерения. выраженную в единицах измеряемой величины: где
— истинное значение измеряемой величины. Относительная погрешность — отношение абсолютной погрешности измерения к истинному значению физической величины:
Относительная погрешность может быть выражена также в процентах.
Поскольку истинное значение измерения остается неизвестным, на практике можно найти лишь приближенную оценку погрешности измерения. При этом вместо истинного значения принимают действительное значение физической величины, полученное при измерениях той же величины с более высокой точностью. Например, погрешность измерения линейных размеров штангенциркулем составляет мм, а микрометром —
мм. Точность измерений может быть выражена количественно как обратная величина модуля относительной погрешности. Например, если погрешность измерения
то точность измерения равна 100.
Международная система единиц, механические единицы
Между единицами физических величин существует взаимосвязь, обусловленная законами природы и выраженная физическими формулами. Единицы большинства физических величин могут быть выражены через некоторое число независимых одна от другой основных единиц. Совокупность выбранных основных и образованных производных единиц называется системой единиц.
Международная система единиц содержит семь основных и две дополнительные единицы. Основные единицы: длина — метр (м); масса — килограмм (кг); время — секунда (с); сила электрического тока — ампер (А); термодинамическая температура — Кельвин (К); сила света — кандела (кд); количество вещества — моль (моль).
Дополнительные единицы приняты для измерения плоского угла — радиан (рад) и телесного угла — стерадиан (ср). Производные единицы Международной системы образуются на основании определений физических величин или законов, устанавливающих связь между физическими величинами, например сила — Ньютон угловая скорость (рад/с), ускорение
Метр — длина, равная 1650763,73 длин волн в вакууме излучения соответствующего переходу между уровнями и
атома криптона-86 (оранжевая линия спектра). Килограмм—масса, равная массе международного прототипа килограмма (приблизительно равен массе
чистой воды при температуре 4°С). Секунда — время, равное 9 192 631 770 периодам излучения, соответствующего переходу между двумя сверхтонкими уровнями основного состояния атома цезия-133 (приблизительно равна 1/86400 средних солнечных суток). Радиан — угол между двумя радиусами окружности, длина дуги между которыми равна радиусу. В градусном исчислении радиан равен
В Международной системе для выражения больших или малых значений физических величин приняты кратные и дольные единицы, которые получаются при умножении исходных единиц на число 10 в соответствующей положительной (для кратных единиц) или отрицательной (для дольных единиц) степени от до
Кратные и дольные единицы обозначаются путем присоединения к размерности исходной единицы соответствующих приставок:
— мега (М),
— кило (к),
— гекто (г),
— дека (да),
— деци (д),
— санти (с),
— милли (м),
— микро (мк) и др. В машиностроении используют дольные единицы длины: миллиметр —
м и микрометр — 1 мкм =
м. Для измерения плоских углов применяются градус —
рад; минута —
и секунда —
Возможно эта страница вам будет полезна:
Классификация средств измерений
Средства измерений — технические средства, используемые при измерениях и имеющие нормированные метрологические свойства. Средства измерений делят на меры, измерительные приборы, измерительные преобразователи, впомогательные средства измерений, измерительные установки и измерительные системы.
Мера — средство измерений, предназначенное для воспроизведения физической величины заданного размера. Однозначная мера воспроизводит физическую величину одного размера, например концевая мера длины и мера массы (гиря). Многозначная мера воспроизводит ряд одноименных величин различного размера, например, штриховая мера длины и угловая мера (многогранная призма). Специально подобранный комплект мер, применяемых не только самостоятельно, но и в различных сочетаниях в целях воспроизведения ряда одноименных величин различного размера, называется набором мер, например наборы плоскопараллельных концевых мер длины и наборы угловых мер.
Измерительные приборы — средства измерений, предназначенные для выработки сигнала измерительной информации в форме, доступной для непосредственного восприятия наблюдателем. По характеру показаний они могут быть показывающие и аналоговые, а по принципу действия — приборы прямого действия, сравнения, интегрирующие и суммирующие. Для линейных и угловых измерений широко используются показывающие приборы прямого действия, допускающие только отсчет показаний. По назначению приборы делят на универсальные, предназначенные для измерения одинаковых физических величин различных объектов, и специализированные, используемые для измерения параметров однотипных изделий (например, размеров резьб или зубчатых колес) или одного параметра различных изделий (например, шероховатости или твердости). По принципу действия, который положен в основу измерительной системы, приборы подразделяют на механические, оптические, оптико-механические, пневматические, электрические, рентгеновские, лазерные и др.
Во многих случаях название прибора определяется конструкцией измерительного механизма. Универсальные приборы для линейных измерений с механической измерительной системой делят на: штангенприборы с нониусом; микрометрические приборы с микрометрическим винтом (микровинт); рычажно-механические приборы с зубчатыми, рычажно-зубчатыми и пружинными механизмами. По установившейся терминологии простейшие приборы, например штангенприборы и микрометрические приборы, называют также измерительным инструментом.
Метрологические показатели средств измерений
Меры характеризуются номинальным и действительным значениями. Номинальное значение меры — значение величины, указанное на мере или приписываемое ей. Действительное значение меры — действительное значение величины, воспроизводимой мерой.
Измерительные приборы состоят из чувствительного элемента, который находится под непосредственным Воздействием физической величины, измерительного механизма и отсчетного устройства. Отсчетное устройство показывающего прибора имеет шкалу и указатель, выполненный в виде материального стержня — стрелки или в виде луча света — светового указателя.
Шкала (рис. 1) представляет собой совокупность отметок и проставленных у некоторых из них чисел отсчета, соответствующих ряду последовательных значений величины. Шкалы с делениями постоянной длины называют равномерными.
Длина деления шкалы — расстояние между осями (или центрами) двух соседних отметок шкалы. Цена деления шкалы
— разность значений величины, соответствующих двум соседним отметкам шкал. Чувствительность прибора определяется отношением сигнала на выходе прибора к вызывающему его изменению измеряемой величины. Абсолютную чувствительность прибора определяют по формуле
При измерениях длин чувствительность прибора является безразмерной величиной и называется также передаточным отношением прибора.
Начальное и конечное значения шкалы — наименьшее и наибольшее значения измеряемой величины, указанные на шкале. Диапазон показаний — область значений измеряемой величины, для которой нормированы допускаемые погрешности прибора. Предел измерений — наибольшее или наименьшее значение диапазона измерений. Вариация показаний — разность показаний прибора, соответствующих данной точке диапазона измерений, при двух направлениях медленных измерений показаний прибора. Стабильность средства измерения — качество средства измерений, отражающее неизменность во времени его метрологических свойств.
Измерительное усилие прибора — сила, создаваемая прибором при контакте с изделием и действующая по линии измерения. Оно обычно вызывается пружиной, обеспечивающей контакт чувствительного элемента прибора, например измерительного наконечника, с поверхностью измеряемого объекта. При деформации пружины происходит изменение усилия: разность между наибольшим и наименьшим значениями — максимальное колебание измерительного усилия.
Погрешности средств измерений
Погрешности средств измерений возникают в результате воздействия большого числа факторов, обусловленных их изготовлением, хранением, эксплуатацией и условиями проведения измерений. Абсолютная погрешность меры представляет собой разность между номинальным значением меры и истинным значением воспроизводимой ею величины. Абсолютная погрешность прибора — разность между показаниями прибора и истинным значением измеряемой величины. Однако в связи с тем, что истинное значение величины неизвестно, на практике вместо него используют действительное значение величины. Приведенной погрешностью прибора является отношение абсолютной погрешности к нормируемому значению, за которое принимают значение, равное верхнему пределу измерений, или диапазону измерений, или длине шкалы и т. п. Так, для вольтметра с верхним пределом измерений 150 В н абсолютной погрешностью в приведенная погрешность, которую обычно выражают в процентах, будет
(нормирующее значение в данном случае равно верхнему пределу, т. е. 150 В).
На погрешность средств измерений большое влияние оказывают условия его применения. Величина, которую не измеряют данным средством измерения, но которая оказывает влияние на результаты измерений этим средством, называется влияющей физической величиной, например, температура, давление, влажность, запыленность окружающей среды, механические и акустические вибрации и т. п. Условия применения средств измерения, при которых влияющие величины имеют нормальное значение или находятся в пределах нормальной области значений, называют нормальными условиями. Нормальные условия для линейных и угловых измерений — температура 20 °С, атмосферное давление 101,32472 кПа (760 мм рт. ст.), относительная влажность 58 % и др.
Основной погрешностью является погрешность средства измерений, используемого при нормальных условиях; дополнительной погрешностью — изменение действительного значения меры или показания прибора при отклонении одной из влияющих величин за пределы, установленные для нормальной области ее значений. Наибольшая погрешность средства измерений, при которой оно может быть признано годным и допущено к применению, называется пределом допускаемой погрешности.
Класс точности средства измерений — это обобщенная характеристика средства измерений, определяемая пределами допускаемых и дополнительных погрешностей, а также другими свойствами средств измерений, влияющими на их точность и определяемыми стандартами на отдельные виды средств измерении. Например, класс точности концевых мер характеризует близость их размера к номинальному значению, допускаемое отклонение от плоскости, а также притираемость и стабильность.
Классификация и методы измерений
По способу получения значений физической величины измерения могут быть прямыми, косвенными, совокупными и совместными. При прямом измерении искомое значение величины находят непосредственно из опытных данных. Примерами прямых измерений являются измерения длины с помощью линейных мер или температуры термометром.
Прямые измерения составляют основу более сложных косвенных, совокупных и совместных измерений. При косвенном измерении искомое значение величины находят на основании известной зависимости между этой величиной и величинами, подвергаемыми прямым измерениям, например тригонометрические методы измерения углов, при которых острый угол прямоугольного треугольника определяют по измеренным длинам катетов и гипотенузы, или измерение среднего диаметра резьбы методом трех проволочек. Косвенные измерения в ряде случаев позволяют получить более точные результаты, чем прямые измерения. Например, погрешности прямых измерений углов угломерами на порядок выше погрешностей косвенных измерений углов с помощью синусных линеек.
Измерения могут быть абсолютными или относительными. Абсолютное измерение основано на прямых измерениях одной или нескольких основных величин и (или) использовании значений физических констант. При линейных и угловых абсолютных измерениях, как правило, находят одну физическую величину, например диаметр вала штангенциркулем. Относительное измерение — измерение отношения величины к одноименной величине, играющей роль единицы, или измерение величины по отношению к одноименной величине, принимаемой за исходную. Относительное измерение основано на сравнении измеряемой величины с известным значением меры. Искомую величину при этом находят алгебраическим суммированием размера меры и показаний прибора.
Для повышения точности измерений разработан ряд методов измерений. Метод измерений — это совокупность приемов использования принципов и средств измерений. Принципом измерений называется совокупность физических явлений, на которых основаны измерения. Метод непосредственной оценки — метод измерений, при котором значение величины определяют непосредственно по отсчетному устройству измерительного прибора прямого действия. Например, измерение длины тела линейкой, силы электрического тока амперметром.
Метод сравнения с мерой основан на сравнении измеряемой величины с величиной, воспроизводимой мерой. Например, измерение диаметра вала блоком концевых мер в державке с притертыми боковичками или на оптиметре, массы тела на рычажных весах с уравновешиванием гирями. В технике измерений применяют несколько методов сравнения с мерой — методы противопоставления, замещения, совпадений, нулевой метод. При линейных и угловых измерениях часто используют дифференциальный метод — метод сравнения с мерой, при котором на измерительный прибор воздействует разность измеряемой величины и известной величины, воспроизводимой мерой. Этот метод применяют, например, при измерениях пневматическими, индуктивными и другими приборами.
Все методы измерений могут осуществляться контактным способом, при котором измерительные поверхности прибора взаимодействуют с проверяемым изделием, или бесконтактным способом, при котором взаимодействия нет.
Методы и средства контроля
На производстве наиболее производительной операцией измерения является контроль. Контроль качества — проверка соответствия качества продукции установленным требованиям. При контроле проверяют, находятся ли действительные значения параметров изделия в допускаемых пределах, но числовые значения величин не определяют. Например, проверяют, укладывается ли действительный размер диаметра вала в границы допуска, указанные на чертеже. Это дает возможность увеличить производительность и снизить стоимость измерений.
Применяются два метода контроля. Дифференцированный (поэлементный) контроль заключается в независимой проверке каждого параметра изделия в отдельности, например контроль значений среднего диаметра, шага и половины угла профиля резьбы метчиков; комплексный контроль — в одновременной проверке суммарной погрешности нескольких параметров, например контроль качества резьбы изделия проходной резьбовой пробкой. Дифференцированный метод контроля позволяет установить причины брака изделий, а комплексный метод обеспечивает проверку годности изделий.
Для контроля геометрических параметров используются калибры. Калибр — однозначная мера специальной конструкции, предназначенная для проверки соответствия действительных значений геометрических параметров изделий заданным параметрам без определения их числового значения. К ним относятся гладкие предельные калибры (пробки и скобы), резьбовые калибры, калибры конусов и шлицевых изделий, шаблоны и др.
Погрешности измерений и их оценка
Погрешность измерения возникает в результате наложения элементарных погрешностей, вызываемых разными причинами. Рассмотрим отдельные составляющие суммарной погрешности измерений. Инструментальная погрешность измерения определяется погрешностью применяемых средств измерения — измерительных приборов и мер. Погрешность отсчитывания возникает ввиду недостаточно точного отсчитывания показаний прибора. Погрешность интерполяции при отсчитывании происходит от недостаточно точной оценки на глаз доли деления шкалы, соответствующей положению указателя.
Погрешность от параллакса возникает вследствие визирования (наблюдения) стрелки, расположенной на некотором расстоянии от поверхности шкалы в направлении, не перпендикулярном к поверхности шкалы. Погрешность от параллакса (рис. 2) прямо пропорциональна расстоянию
указателя 1 от шкалы 2 и тангенсу угла
линии зрения наблюдателя к поверхности шкалы:
Погрешность от перекоса возможна в приборах, в конструкции которых не соблюден принцип Аббе, заключающийся в том, что линия измерения должна являться продолжением линии шкалы. Например, перекос рамки штангенциркулей (рис. 3) изменяет расстояние между
губками 1 и 2. Погрешность определения измеряемого размера из-за перекоса При выполнении принципа Аббе
и соответственно
Внешние погрешности возникают вследствие отклонения от нормальных условий измерения. Например, отклонение температуры от нормального значения 20°С приводит к изменению длины деталей, средств измерений и изделий. Если невозможно создать нормальные условия, то в результате линейных измерений следует вводить температурную поправку:
где — измеряемый размер;
— коэффициенты линейного расширения материалов средства измерения и изделия;
— температуры средства измерения и изделия
Погрешности измерений от измерительного усилия возникают вследствие контактных деформаций в месте соприкосновения поверхностей средства измерения и изделия; деформации формы изделия, например тонкостенных деталей; упругих деформаций установочного узла, например скоб, стоек или штативов. Погрешность метода измерений обусловлена несовершенством метода измерения, например неправильно выбранной схемой базирования (установки) изделия, неправильно выбранной последовательностью проведения измерений.
Рассмотренные выше причины вызывают появление систематических и случайных погрешностей, из которых складывается суммарная погрешность измерения. Эти причины могут приводить к грубым погрешностям измерений. Систематическая погрешность является составляющей погрешности измерения, которая остается постоянной или закономерно изменяется при повторных измерениях одной и той же величины. К систематическим относятся, например, погрешности от неисправности прибора или от несоответствия действительного значения меры ее номинальному значению. Систематические погрешности могут быть изучены опытным путем и исключены из результатов измерений. В целях исключения систематической погрешности вводится поправка — значение величины, одноименной с измеряемой, прибавляемое к полученному при измерениях значению. Поправка суммируется с номинальным значением меры или с показаниями прибора
Случайная погрешность — составляющая погрешности измерения, изменяющаяся случайным образом при повторных измерениях одной и той же величины, вследствие большого числа неподдающихся учету причин, например погрешности от вариации показаний измерительного прибора, погрешности округления или отсчитывания показаний прибора. Случайные погрешности нельзя исключить из результатов измерений, но их влияние можно уменьшить путем многократных повторных измерений одной величины и обработкой опытных данных. Грубая погрешность — погрешность измерения, существенно превышающая ожидаемую при данных условиях погрешность. Результаты измерений, содержащие грубые погрешности, исключают как недостоверные.
Для оценки возможной погрешности измерений необходимо знать закономерности появления случайных погрешностей. При большом числе измерений их значения, как правило, распределяются по закону Гаусса: погрешности измерений могут принимать непрерывный ряд значений; вероятность (частота) появления погрешностей, равных по значению и обратных по знаку, одинакова; большие по абсолютному значению погрешности встречаются реже малых; средняя арифметическая погрешность стремится к нулю при увеличении числа измерений.
Распределение значений случайных погрешностей зависит от точности измерений и может быть определено по их среднему квадратическому отклонению, которое вычисляется по формуле:
где — число измерений, содержащих погрешность
— общее число измерений.
Вероятность (частота) появления погрешности -равна отношению
Так как погрешности могут принимать непрерывный ряд, т. е. бесконечное множеств значений, вероятность каждого отдельного значения
равна нулю. Вероятность появления погрешностей в каком-либо интервале значений определяется по плотности распределения вероятности случайных погрешностей
которую вычисляют по формуле:
Для графического определения вычерчивается кривая при заданном значении
(рис. 4). Вероятность погрешностей в выбранном интервале значений, например
равна отношению площади под кривой в этом интервале (показано штриховкой) ко всей площади под кривой. Кривые распределения стремятся к нулю при увеличении абсолютных значений погрешностей. Вероятность появления погрешностей равна
т. е. практически исключена. Погрешность
называют предельной погрешностью измерений. Погрешности измерений
относят к грубым погрешностям.
Случайную погрешность можно уменьшить путем многократных измерений. Если какую-либо величину измерять много раз, то вероятным значением этой величины, или ее математическим ожиданием, будет среднее арифметическое значение х, подсчитанное по результатам этих измерений jc,:
Погрешность среднего арифметического значения и среднее квадратическое отклонение для ряда измерений вычисляют по формулам:
Погрешность среднего арифметического значения уменьшается при увеличении числа измерений. Например, при
а при Если при обработке результатов измерений выявлены измерения, содержащие грубые погрешности, то их исключают и выполняют повторные расчеты и т. д.
При измерениях случайные и систематические погрешности проявляются одновременно. Если систематические погрешности отсутствуют или учтены поправками, то суммарная предельная погрешность измерения
где — предельные погрешности измерительных приборов, установочных мер, температурных деформаций, деформаций от измерительного усилия, базирования приборов и других факторов, из которых складывается суммарная погрешность данного измерения.
Возможно эта страница вам будет полезна:
Выбор средств измерений
При выборе средств измерений учитываются их метрологические параметры, эксплуатационные факторы (организационная форма контроля, особенности конструкции и размеры изделий, производительность оборудования и т. п.), экономические соображения и др. Важное значение имеет правильный выбор допускаемой погрешности средств измерений: недостаточная точность измерений приводит к снижению качества продукции и увеличению ее себестоимости, завышенная точность повышает трудоемкость и стоимость измерений и ведет к увеличению затрат на производство.
Принцип выбора точности средств измерений пока зан на рис. 5. Истинные размеры изделий х вследствие воздействия при изготовлении многих факторов распределяются случайным образом, например, по закону Гаусса. Плотность распределения вероятности измеряемого параметра показана на рис. 5 Для параметра, исходя из условий работы, качества, надежности и взаимозаменяемости изделий, материала, технологии изготовления, себестоимости и других факторов, устанавливается предельно допустимое отклонение параметра
от номинального значения
Отношение заштрихованной площади к общей площади под кривой показывает процент годных изделий для заданного технологического процесса и установленного поля допуска параметра при погрешности измерений, равной нулю.
Действительные значения параметра зависят от по грешности измерений которые так же, как погрешности изготовления, распределяются случайным образом (см. кривые 2 и 3 на рис. 5). Поэтому случайные погрешности измерений приводят к неопределенности (случайности) оценки действительных значений
параметра вблизи границ поля допуска. При этом может оказаться, что часть годных изделий с отклонением параметра
будет отнесена к браку и, наоборот, некоторые бракованные изделия с отклонением параметра будут приняты как годные. Вероятность погрешности можно оценить по отношению заштрихованных площадей под кривыми 2 и 3 к заштрихованной площади под кривой. Таким образом, чем меньше допуск на изделие и чем больше погрешность измерений, тем больше вероятность погрешности контроля и ниже качество продукции. Число необнаруженных бракованных изделий и фиктивного брака определяется отношением предельной погрешности измерений к допуску параметра
Выбор средств измерений выполняется в соответствии с государственными стандартами, которые устанавливают допускаемую погрешность измерений в зависимости от предельных отклонений контролируемого параметра. Например, ГОСТ 8.051—81 устанавливает допускаемые погрешности при измерении линейных размеров до 500 мм. Допускаемые погрешности измерений включают погрешности мер и измерительных приборов, условий их применения и метода измерений.
Метрологи участвуют в выборе измерительных средств совместно с технологами производства и конструкторами изделия, разрабатывают заводские инструкции по выбору средств измерений и рекомендации по оснащению производства ими.
Пример. Подобрать установочную концевую меру длины для контроля диаметра вала с помощью индикатора часового типа класса точности 0. Условия измерения — нормальные, погрешность базирования индикатора составляет 4 мкм, номинальный диаметр вала мм, отклонения размеров вала соответствуют квалитету Л6.
По ГОСТ 8.051—81 для вала мм и квалитета
находим допуск размера вала
мкм и допускаемую погрешность измерения
мкм.
Индикатор часового типа класса точности 0 в пределах участка шкалы мкм, в который укладывается допуск размера вала, имеет предельную основную погрешность
мкм (см табл. 5).
Допускаемая погрешность установочной меры
где мкм — погрешность базирования
Предельные погрешности концевых мер длины классов точности 2 и 3 равны (см. табл. 2), соответственно,
где м — номинальная длина меры.
Условия требуемой точности измерений выполняются для меры класса точности 2:
Передача единицы длины от эталонов рабочим средствам измерений
По точности средства измерений делятся на эталоны, образцовые и рабочие средства измерений. Эталон единицы — средство измерений (или комплекс средств измерений), обеспечивающее воспроизведение и хранение единицы в целях передачи ее размера менее точным средствам измерений. Эталоны воспроизводят размер единицы с наивысшей точностью.
Эталонный метод воспроизведения метра в длинах световой волны заключается в следующем. При прохождении электрического тока через пары и газы атомы излучают свет с линейным спектром. Каждая линия спектра соответствует монохроматическому потоку света с определенной длиной волны При распространении в вакууме
где с — скорость света в пустоте; h — постоянная Планка;
— энергии двух состояний атома.
В качестве международного эталона принята длина волны оранжевой линии излучения криптона-86, свечение которого осуществляют в специальных газоразрядных лампах при строго установленных условиях. Длина волны в вакууме первичного излучения равна 0,60578021 мкм.
Государственный первичный эталон метра состоит из источника (лампы) первичного эталонного излучения криптона-86 и эталонного интерферометра, применяемого для измерения длины штриховых и концевых мер (вторичные эталоны). Он обеспечивает воспроизведение единицы длины в диапазоне 0…1 м со средним квадратичным отклонением результатов измерений, не превышающим что соответствует предельной погрешности одного измерения
Размер единицы передается от эталонов рабочим средствам измерений путем поверки менее точных средств измерений более точными. Поверка — определение метрологическим органом погрешностей средства измерения и установление его пригодности к применению.
Образцовым средством измерений служит мера или измерительный прибор, применяемые для поверки по ним других средств измерений и утвержденные в качестве образцовых. Использование образцовых мер и приборов только для поверки уменьшает их износ, увеличивает срок службы и надежность передачи единицы. Рабочее средство измерений применяется для измерений, не связанных с передачей единицы.
Поверочная схема — утвержденный в установленном порядке документ, определяющий средства, методы и точность передачи размера единицы от эталона или исходного образцового средства измерений рабочим средствам измерений. Поверочные схемы по их назначению подразделяются на общесоюзные, охватывающие все средства измерения данной физической величины в стране, и локальные, которые распространяются на измерения, проводимые отдельными органами метрологической службы.
Общесоюзная поверочная схема для средств измерения длины состоит из двух частей: для штриховых мер, у которых заданное значение длины определяется расстоянием между штрихами, нанесенными на плоской поверхности; для концевых мер, у которых заданный размер равен расстоянию между плоскостями, ограничивающими меру. Рассмотрим сокращенную часть поверочной схемы для концевых мер длины (рис. 6). От Государственного первичного эталона длины размер единицы передается эталонам-копиям и затем рабочим эталонам. Соподчинение средств измерений на схемах обозначено соединительными линиями, на которых в кругах указаны методы поверки.
Основными образцовыми средствами измерения для передачи размера единицы от эталонов к рабочим приборам и мерам являются образцовые меры. В порядке понижения точности образцовые средства измерений делят
на разряды: 1-й, 2-й и т. д. Разряд образцовых средств измерений — это категория образцовых средств измерений, отнесенных к одной и той же ступени поверочной схемы. Он характеризуется предельной допускаемой погрешностью и устанавливается метрологической аттестацией. Метрологическая аттестация — исследование средства измерений, выполняемое метрологическим органом для определения метрологических свойств этого средства измерений, и выдача документа с указанием полученных данных.
Рабочие измерительные приборы группируют по основной допускаемой погрешности а рабочие меры подразделяют по классам точности. Погрешность образцовых мер должна быть в 2—3 раза меньше погрешности рабочих мер и приборов, для поверки которых они предназначены.
Меры длины и плоского угла, штриховые меры длины
Штриховые меры длины изготовляют в виде брусков четырех типов с различными формами поперечного сечения (табл. 1). Однозначные меры имеют два штриха на краях бруса. Шкалы многозначных мер могут имет^ деления шкалы 1 дм, 1 см, 1 мм, 0,2 мм и 0,1 мм на всей длине или на ее отдельных участках. Шкалы наносят на нейтральной плоскости мер типа I и на верхней или боковой поверхности мер типа II—IV.
Брусковые штриховые меры длины применяют для измерения линейных размеров и перемещений, в качестве шкал приборов и станков, а также в качестве образцовых средств измерений при поверке мер длины, измерительных линеек, шкал приборов, станков, машин и линейных преобразователей.
Общую длину и цену деления шкалы штриховых мер поверяют путем сравнения с образцовыми штриховыми мерами на специальных оптических приборах — компараторах, которые имеют отсчетные микроскопы с ценой деления 0,001 мм. Допускаемые погрешности мер в .микрометрах можно рассчитать в зависимости от номинального значения интервала шкалы L (м) и различных классов точности меры по следующим формулам: для
Плоскопараллельные концевые меры длины
Плоскопараллельные концевые меры длины имеют форму прямоугольного параллелепипеда (плитки) с двумя параллельными измерительными поверхностями, расстояние между которыми равно номинальному значению длины меры L. Конструкция и размеры основных типов концевых мер показаны иа рис. 7, а. Длина мер измеряется в пределах L=0,1…1000 мм через определенные интервалы-градации, равные 0,001; 0,005; 0,01; 0,1; 0,5; 1,0; 10; 25; 50 и 100 мм.
Рабочие концевые меры длины предназначены для регулировки и настройки на размер показывающих измерительных приборов, для непосредственных измерений размеров изделий, а также для выполнения особо точных разметочных работ и наладки станков. Образцовые меры применяют для передачи размера единицы длины от первичного эталона концевым мерам меньшей точности и для поверки и градуировки измерительных приборов длины.
Рассмотрим нормируемые параметры концевых мер. Длина концевой меры в любой точке измерительной поверхности равна длине перпендикуляра, опущенного из данной точки на противоположную поверхность. Отклонение длины концевой меры — наибольшая по абсолютному значению разность между длиной меры в любой
точке и номинальной длиной. Отклонение от плоскопа-раллельности концевой меры есть разность между наибольшей и наименьшей длинами.
Протираемость концевых мер — это свойство измерительных поверхностей мер прочно сцепляться между собой или с плоскими стеклянными пластинами при накладывании одной меры на другую или меры на пластину. Притираемость мер объясняется молекулярным притяжением тщательно обработанных поверхностей в присутствии тончайших слоев смазки толщиной
~0,02 мкм, которая остается на мерах после промывки их в бензине. Притираемость позволяет составлять блоки концевых мер требуемого размера (рис. 7, б). Перед составлением блока нужно отобрать входящие в него меры, вытереть смазку чистой салфеткой, промыть меры в бензине и высушить. Размер блока мер Lc равен сумме длин мер, входящих в него. Предельные отклонения длины блока рассчитывают по отклонениям составляющих его мер.
Концевые меры длины выпускаются наборами, которые обеспечивают составление блока мер любого размера с интервалом I мкм. В машиностроении наиболее распространены набор № 1, содержащий 83 меры, и набор № 3, содержащий 112 мер. В наборы входят две пары дополнительных мер, которые притираются к блоку всегда одной стороной и служат для защиты основных мер блока от изнашивания и повреждений.
Выбор мер блока заданного размера выполняют в следующем порядке:
- 1) подбирают меру, которая содержит наименьшую долю размера;
- 2) размер выбранной меры вычитают из размера блока и определяют остаток;
- 3) подбирают меру, которая содержит наименьшую долю остатка, и определяют новый остаток и т. д. Из всех возможных вариантов состава блока следует выбирать тот, который содержит наименьшее число мер.
Наборы принадлежностей к концевым мерам длины позволяют с помощью концевых мер осуществлять проверку наружных и внутренних размеров изделий и разметочные работы. В наборы (рис. 8) входят державки / для крепления блоков мер с плоскопараллельными 2. радиусными 3, центровыми 4 и чертильными 5 боковиками; основание 6 для установки блоков при разметке; стяжки 7 для крепления блоков с мерами размером L^t ^100 мм, которые имеют отверстия; зажимные сухари 8 для крепления стяжками 7 боковиков к мерам; отвертка с нормированным усилием.
Концевые меры длины выпускают шести классов точности 00, 01. 0, 1. 2 и 3. Для мер, находящихся в эксплуатации, установлены также классы точности 4 и 5. Допускаемые отклонения длины мер можно приближенно рассчитать по формулам, приведенным в табл. 2. Размеры концевых мер отличаются высоким постоянством во времени. Изменение длины концевых мер не превышает значений, указанных в табл. 2. Для уменьшения износа концевые меры изготовляют из высококачественной стали и подвергают закалке. Выпускаются также плоскопараллельные концевые меры длины из твердого сплава.
Разряд образцовых концевых мер устанавливается путем аттестации рабочих концевых мер соответствующего класса точности. На рис. 6 приведены формулы для расчета пределов допускаемой погрешности образцовых мер 1, 2, 3, 4 и 5-го разрядов (ГОСТ 8.020—75).
Пример Составить блок мер размером 50,625 мм из набора Кч 1 класса точности 0 и определить его предельную погрешность. Выбраны следующие меры:
- мера 1 — размер
= 1,005 мм, остаток 49,62 мм;
- мера 2 — размер
= 1,12 мм, остаток 48,5 мм;
- мера 3 — размер
=8,5 мм, остаток 40 мм;
- мера 4 — размер
=40 мм, остаток 0.
Допускаемые отклонения длины выбранных мер по ГОСТ 9038—83 составляют мкм и
мкм. Предельное отклонение длины блока (см. рис. 7,6)
Угловые призматические меры
Угловые призматические меры являются наиболее точным средством измерения углов в машиностроении. Они предназначены для передачи размера единицы плоского
угла от эталонов образцовым и рабочим угловым мерам и приборам, для поверки и градуировки мер и приборов и для измерения углов изделий.
Конструкции однозначных и многозначных угловых мер показаны на рис. 9. Рабочие углы мер заключаются между смежными измерительными поверхностями у угловых плиток — мер типа 1, II и III; между нормалями к измерительным поверхностям у угловых призм — мер типа IV; между рабочими гранями и основанием у мер типа V. Число граней угловых призм может быть
Измерительные поверхности угловых плиток обладают свойством притираемости. Плитки комплектуются в наборы. Порядок составления блоков плиток такой же, как у концевых мер длины. У кромок рабочих поверхностей плиток имеются отверстия, через которые с помощью набора принадлежностей плитки соединяются в блоки. В комплект наборов входят следующие принадлежности: державка 3 для крепления двух мер (рис. 10, а); державка 4 для крепления трех мер (рис. 10, б); державка 5 для крепления мер и лекальной линейки 6 для образования внутренних углов (рис. 10, в). Соединение осуществляется винтами 2 и клиновыми штифтами, пропускаемыми через отверстия державки и мер.
Угловые плитки и блоки из них применяют для измерения углов методом «на просвет». Измерительные грани мер совмещают с поверхностями изделия и определяют размер просвета между ними путем сравнения с «образцом просвета» (рис. 11), который состоит из концевых мер длины 2, притертых к стеклянной пластине 3 и накрытых лекальной линейкой 1. При хорошей освещенности и определенном навыке просвет размером 4 мкм можно оценить с погрешностью ~1 мкм, погрешность
измерения угла при этом ~15″. Бесконтактные измерения угловыми мерами выполняются на автоколлимационных приборах.
Угловые меры выпускаются трех классов точности О,
1, 2. Многогранные призмы могут иметь также класс 00. Предельные погрешности угловых мер типов I, II, III составляют для класса 0,
для класса 1 и
для класса 2. Соответственно, погрешности углов многогранных призм равны
Меры типа V используются для поверки синусных линеек и выпускаются класса точности 1 (погрешность
).
Для образцовых угловых мер установлены четыре разряда. Предельные погрешности углов у мер 1-го разряда равны 2-го разряда
3-го разряда
и 4-го разряда
Разряд образцовых мер устанавливается аттестацией рабочих угловых мер соответствующего класса точности по поверочной схеме для средств измерения плоского угла, приведенной в ГОСТ 8.175—75.
Инструменты для линейных измерений
Штангенинструменты
Штангенинструменты представляют собой показывающие приборы прямого действия, у которых размер изделия определяется по положению измерительной рамки, перемещающейся вдоль штанги со штриховой шкалой. Штангенинструменты с отсчетом показаний по нониусу (рис. 12) просты по конструкции и наиболее распространены на производстве.
Штангенциркули, предназначенные для измерения наружных и внутренних размеров изделий, выпускаются четырех типов: ШЦ-I (рис. 12, а); ШЦТ-I (ШЦ-1 — без верхних губок и с нижними губками, выполненными из твердого сплава); ШЦ-Н (рис. 12, б) и ШЦ-Ш (ШЦ-II без верхних губок). Они состоят из штанги /, измерительных губок 2 (верхних и нижних), рамки 3, зажима рамки 4, нониуса 5, глубомерной линейки 6 и микрометрической подачи 7 для установки рамки на точный размер.
Штангенглубиномеры (рис. 12, в), применяемые для измерения глубины отверстии и пазов, имеют штангу / без губок и рамку 3 с основанием 2 и нониусом 4. Измерительными поверхностями яеляются торцы штанги и основания 2.
Штангенрейсмассы (рис. 12, г) используются для измерения высот и разметки изделий, установленных на плите. Штанга 7 установлена в массивном основании 8, нижняя плоскость которого является началом шкалы. Рамка 6 с нониусом 5 имеет кронштейн 1, иа котором хомутом 3 крепится измерительная 2 или разметочная 4 ножки.
При измерениях рамка перемещается по штанге инструмента так, чтобы измерительные поверхности плотно, но без перекоса, прилегали к поверхности изделия, которая ограничивает определяемый размер или
изделий (отмеченных штриховкой на рис. 12). Перекос рамки относительно штанги недопустим.
На штанге инструментов нанесена основная шкала с ценой деления мм, а на рамке установлена или нанесена дополнительная штриховая шкала — нониус. По положению нулевого штриха нониуса на основной шкале определяют целое число миллиметров в размере. Дробные доли миллиметра находят с помощью нониуса.
При измерениях наружной стороной губок штангенциркулей ШЦ-П и верхней стороной губки штангенрейсмас-сов ширина губок мм прибавляется к отсчету.
Штангенинструменты с автоматическим отсчетом показаний повышают качество и производительность измерений. В штангу индикаторного штангенциркуля (рис. 13, а) вмонтирована зубчатая рейка. Зубчатое колесо индикатора 3, закрепленного на рамке 2 с подвижной губкой, перемещается по зубчатой рейке. Поворот зубчатого колеса преобразуется в перемещение стрелки индикатора. По шкале, нанесенной на штанге, отсчитывают десятки миллиметров, по шкале индикатора — единицы, десятые и сотые доли миллиметра. Инструмент с электронным цифровым отсчетом показан на рис. 13,6.
Устройство нониуса
Ноннус — это равномерная дополнительная шкала с пределом измерений, равным цене деления основной
шкалы
Нониусы имеют различные цену С деления шкалы (отсчет по нониусу) и модуль который показывает, через какое число делений основной шкалы будут располагаться штрихи нониуса, смещенные на значение отсчета. Линейные нониусы бывают нескольких типов (рис. 4). Число делений шкалы нониуса
длина деления шкалы нониуса
полная длина шкалы нониуса
Если нулевой штрих нониуса совпадает со штрихом основной шкалы, например при плотно сдвинутых губках штангенциркуля, рис. 14, а, то 1-й штрих нониуса смещен от штриха основной шкалы на значение С отсчета по нониусу, 2-й штрих — на 2С, 3-й штрих — на 3С и т. д. При перемещении нулевого штриха нониуса между делениями основной шкалы штрихи нониуса будут поочередно «совпадать со штрихами основной шкалы. Когда дробная доля размера составит со штрихом шкалы совпадает 1-й штрих нониуса, при
— 2-й штрих, при
— 3-й штрих и т. д. Таким образом, указателем для нониуса служит штрих основной шкалы.
совпадающий со штрихом нониуса. Число десятых долей миллиметра при отсчете по нониусу равно номеру этого штриха нониуса, умноженному на отсчет по нониусу С. На рис. 14, б—г значения отсчетов равны 91,7, 43,25 и 141,6 мм.
Пределы измерений и отсчеты по нониусам штанген-инструментов приведены в табл. 3. Основная допускаемая погрешность равна отсчету по нониусу если измеряемый размер
При измерении больших размеров
Микрометры
Микрометрические инструменты основаны на применении микрометрических винтовых пар. Их конструкции разнообразны. Ниже рассмотрены микрометры общего назначения.
Гладкие микрометры МК (рис. 15, а) предназначены для измерения наружных размеров изделий. К основным деталям и узлам относятся скоба 1, пятка 2, микровинт 4, стопор 5 винта, стебель 6, барабан 7 и трещотка 8 микрометрической головки, преобразующей вращательное движение барабана в поступательное движение микровинта.
На стебле 6 вдоль продольного штриха нанесена основная шкала прибора с ценой деления мм и пределом измерений 25 мм. Для удобства отсчета четные штрихи шкалы, имеющие целые значения размера, отложены снизу продольного штриха. На коническом срезе барабана 7 нанесено 50 делений круговой шкалы с ценой деления, равной
мм. При одном обороте барабан и микровинт 4 перемещаются на одно деление основной шкалы. Торец барабана является указателем для основной шкалы, а продольный штрих на стебле — указателем для круговой шкалы.
При измерении изделие помещают без перекоса между пяткой и микровинтом и, вращая барабан за трещотку до тех пор, пока она не начнет проворачиваться, плотно прижимают измерительные поверхности прибора к поверхности изделия. Ближайший к торцу барабана штрих основной шкалы показывает число целых и десятых долей миллиметра в размере. К отсчету по основной шкале прибавляют отсчет по круговой шкале, равный произведению цены деления на номер деления, который находится напротив продольного штриха. Отсчет на рис. 15,
Пределы измерений микрометров зависят от размера скобы и составляют 0…25; 25…50; …; 275…300; 300…400; 400…500 и 500…600 мм. Микрометры для размеров более 300 мм оснащены сменными (рис. 15, б) или передвижными (рис. 15, в) пятками, обеспечивающими диапазон измерений 100 мм. Передвижные пятки 2 крепятся в требуемом положении фиксатором /, а сменные пятки 3— гайками / и 2. Перед измерением микрометры устанавливают в исходное (нулевое) положение, при котором пятка и микровинт прижаты друг к другу или поверхностям установочных мер 3 (см. рис. 15, а) под действием силы, обеспечиваемой трещоткой. При правильной установке нулевой штрих круговой шкалы барабана должен совпадать с продольным штрихом на стебле, а торец барабана с нулевым штрихом основной шкалы.
Допускаемая погрешность микрометров класса точности 1 составляет мкм для диапазона измерений 0…100 мм;
мкм для диапазона 100…200 мм;
мкм для ди апазона 200…300 мм;
мкм для диапазона 400 ..500 мм и
мкм для диапазона 500 ..600 мм. Микрометры для размеров 0…25 мм выпускаются также класса точности 0 и имеют погрешность
мкм.
Микрометры с циферблатом MЛ (рис. 16, а) применяют ДЛЯ измерения толщины листов и лент. К их отличительным особенностям относятся увеличенный вылет скобы 3, сферическая измерительная поверхность пятки 4, отсчетное устройство, выполненное в виде неподвижного циферблата 1 и стрелки 2, вращающейся вместе с барабаном 5.
Микрометры МТ (рис. 16., б) используют для измерения толщины стенок Труб с внутренним диаметром 12 мм и более. У них пятка 2 имеет сферическую форму, а скоба
в месте крепления пятки сделана тонкой для измерения труб небольшого диаметра.
Микрометры настольного МГ (рис. 16, в) имеют корпус 1 с жестким стационарным основанием, пятку 2, измерительные наконечники 3, микровинт 4, стебель 5, барабан 6 с круговой шкалой, у которой С=0,01 мм ил= = 100, а также трещотку 7 и измерительный стол 8. Сменные измерительные стержни крепятся к пятке и микровинту с помощью винтов. Они имеют различные формы измерительных поверхностей — плоские, тарельчатые, ножевидные. Пятка 2 может переставляться на 10 мм в зависимости от размера детали.
Микрометры с цифровым отсчетом показаний повышают качество и производительность измерений. Числовой механизм может располагаться или в стебле микровинта (рис. 17, а), или в скобе микрометра (рис. 17, б).
Устройство микрометрических головок
Микрометрические головки могут иметь различную конструкцию. На рис. 18, а показана микрометрическая
головка, которой оснащают микрометры с верхним пределом измерений до 100 мм. Микрометрический винт / проходит через гладкое направляющее отверстие стебля 2 и ввинчивается в разрезную микрогайку 4, которая стягивается регулирующей гайкой 5 так, чтобы устранить зазоры в винтовой паре. На микровинте установочным колпачком 6 закреплен барабан 3. Палец 9, помещенный в глухое отверстие колпачка, прижимается пружиной 10 к зубчатой поверхности трещотки 7, которая крепится на колпачке винтом 8. При вращении трещотка передает микровинту через палец вращающий момент, обеспечивающий измерительное усилие Б…9 Н. Если измерительное усилие больше, то трещотка проворачивается с характерными щелчками. Винт 12 ввинчивается во втулку 11 и фиксирует микровинт в требуемом положении.
Микрометрические головки микрометров с нижним пределом измерений свыше 100 мм имеют несколько отличное устройство (рис. 18, б). Микровинт 1 стопорится гайкой 2, которая зажимает разрезную втулку 3. Барабан 4 затягивается установочным колпачком 5 на конусную поверхность микровинта. Палец 6 прижимается к торцовой зубчатой поверхности трещотки 7.
Установка микрометрических головок на нуль осуществляется в следующем порядке: 1) устанавливают микрометр в исходное положение; 2) закрепляют микровинт стопором; 3) отворачивают установочный колпачок на пол-оборота; 4) барабан поворачивают до совпадения нулевого штриха круговой шкалы на барабане с продольным штрихом на стебле; 5) закрепляют барабан колпачком; 6) освобождают микровинт; 7) проверяют установку микрометра на нуль и в случае несовпадения нулевого штриха на барабане с продольным штрихом на стебле повторяют операции в той же последовательности.
Микрометрические глубиномеры и нутромеры
Микрометрический глубиномер состоит из микрометрической головки /, запрессованной в основание 2(рис. 19). В отверстие на торце микровинта вставляются смен-, ные стержни 3 с разрезными пружинящими концами и со сферической измерительной поверхностью. Микровинт зажимается стопором 4. Диапазон измерений глубиномерами составляет 0…25, 25…50, 125…150 мм. Цифры у штрихов стебля н барабана нанесены в обратном порядке по сравнению с микрометрами, так как чем больше глубина, тем дальше выдвинут микровинт. Глубиномеры выпускают 1-го и 2-го классов точности. Допускаемые погрешности равны соответственно и
мкм при пределах измерения до 100 мм и
и
мкм при больших размерах. При настройке нулевого положения торец основания глубиномера прижимают к торцу специальной установочной меры 5, которую ставят на плите. Микровинт прижимают к поверхности плиты, вращая трещотку. Порядок установки головки на нуль такой же, как у микрометров.
Микрометрические нутромеры предназначены для измерения внутренних размеров от 50 до 6000 мм. Нутромеры состоят из микрометрической головки (рис. 20, а), сменного удлинителя (рис. 20, б) и защитного наконечника (рис. 20, в). Микрометрическая головка имеет стебель 6, в один конец которого ввинчивается микровинт 5, а в другой конец запрессован измерительный наконечник 7. Зазоры в микрометрической паре устраняются конической гайкой 3. Барабан 4 соединяется с микровинтом гайкой 2 и контргайкой 1. Винтом 9 зажимают микровинт в нужном положении. В резьбу присоединительной муфты 8 ввинчиваются удлинители или защитные наконечники. На палец микровинта навинчивают сферические измерительные наконечники.
Нутромеры имеют следующие поеделы измерений: 50…75; 75… 150; 75…600; 150… 1250; 600…2500; 1250…400; 2500…6000 мм. Нутромеры с верхним пределом измерений свыше 2500 мм имеют микрометрическую головку, оснащенную индикатором часового типа.
Допускаемые погрешности нутромеров изменяются от мкм при размерах изделий
до
мкм при
мм. Микрометрическую головку настраивают на начальное значение шкалы с помощью установочных скоб (рис. 20, г). После установки нуля микрометрическую головку свинчивают с удлинителями до требуемого размера. При измерениях повышенной точности действительный размер нутромера определяют на измерительной машине.
Сведения о поверке и ремонте инструментов
Инструменты, находящиеся в эксплуатации, а также после ремонта, должны подвергаться поверке. Перед поверкой инструменты промывают в авиационном бензине, протирают жесткой салфеткой и выдерживают на рабочем месте не менее 3 ч. В помещении, где проводится поверка, температура должна быть равна
Погрешность штангенинструментов определяют с помощью концевых мер длины класса точности 3. Поверку осуществляют в шести точках, равномерно распределенных по шкале, если отсчет по нониусу мм, и в трех точках, если
мм. При определении погрешностей штангенциркулей блок концевых мер длины помещают между измерительными поверхностями губок: измерительные поверхности должны прижиматься с силой, которая обеспечивает их нормальное скольжение по поверхности мер при отпущенном винте рамки. При поверке штангенглубиномера его основание прижимают к двум одинаковым блокам мер, притертым к плоской стеклянной пластине или поверочной плите. Штангенрейс-массы поверяют по мерам, установленным на поверочной плите. Показания штангенинструментов поверяют при свободной и закрепленной рамках.
Погрешность микрометров и микрометрических глубиномеров определяют по концевым мерам длины класса точности 2-го или 5-го разряда. Показания микрометрических головок проверяют в точках шкалы, равных 5,12; 10,24; 15,36 и 25 мм. Микрометры при поверке укрепляют в стойке, а глубиномеры устанавливают на двух концевых мерах, притертых к стеклянной пластине или плите. Погрешности микрометрических головок нутромеров и суммарные погрешности микрометрической головок нутромеров и суммарные погрешности микрометрической головки с присоединенными удлинителями определяют на горизонтальном оптиметре или измерительной машине. Точки поверки показаний такие же, как у микрометров.
Основная погрешность инструментов складывается из погрешностей отдельных элементов, которые подлежат поверке. При поверке инструментов осматривают внешний вид, проверяют взаимодействие частей, шероховатость, отклонение от плоскостности, прямолинейности и параллельности измерительных поверхностей и установку прибора на нуль. У штангенинструментов с помощью щупов размером 0,25 и 0,3 мм определяется также расстояние от верхней кромки края нониуса до поверхности шкалы штанги. У микрометров проверяют измерительное усилие, положение конического торца барабана относительно нулевого штриха шкалы стебля в исходном положении, перекос измерительной поверхности микровинта при зажиме стопора, кривизну и биение сферических измерительных поверхностей, рабочие размеры установочных мер.
При эксплуатации штангенинструментов наиболее часто встречаются следующие дефекты: износ измерительных поверхностей губок и их непараллельность, износ и деформация штанги, ослабление пружины рамки, коррозия деталей, смещение нониуса, износ резьбы фик-саторных и стопорных винтов. Эти дефекты устраняются проведением ремонтных операций. Наиболее характерные из них — доводка измерительных поверхностей губок, рихтовка и доводка штанги, устраняющие неплотность и непараллельность измерительных поверхностей; регулировка положения нониуса, замена пружины и винтов. Доводку измерительных губок выполняют микроабразивными пастами с помощью чугунного притира толщиной 14…17 мм и диаметром 30 мм. Притир со следами пасты перемещают между губками возвратно-поступательными движениями, периодически поворачивая его на 6…8°. Для совмещения нулевых штрихов основной миллиметровой шкалы и нониуса в планке нониуса предусматриваются специальные пазы под крепежные винты, позволяющие его продольную передвижку.
При эксплуатации микрометров наиболее характерны изнашивание измерительных поверхностей пятки и микровинта, резьбы микровинта, направляющего отверстия микровинта и зубцов трещотки, смещение нулевой установки, деформация скобы и ослабление пружины. При небольшом износе измерительных поверхностей осуществляют их совместную доводку с помощью комплекта ряда цилиндрических притиров, разность размеров которых составляет 0,25 мм, что соответствует перемещению микровинта при повороте на 0,5 оборота. При значительных износах применяют раздельную доводку торца микровинта в призме. Выбор зазора в резьбе обеспечивается подтягиванием гайки с конусной посадкой.
Существует ряд приспособлений, которые механизируют операции поверки и ремонта инструментов для линейных измерений.
Классификация калибров
По методу контроля калибры делят на нормальные и предельные. Нормальные калибры копируют размеры и форму изделий. Предельные калибры воспроизводят размеры, соответствующие верхней и нижней границам допуска изделий. При контроле используют проходной и непроходной предельные калибры. Комплексные калибры предназначены для проверки нескольких размеров изделий, а дифференциальные (простые) калибры — одного размера.
По конструкции предельные калибры делят на: нерегулируемые (жесткие) и регулируемые, которые позволяют компенсировать износ калибра или установить его на другой размер: однопредельные и двухпредельные, объединяющие проходной и непроходной калибры; односторонние, у которых оба предельных калибра расположены с одной стороны, и двусторонние. В соответствии с принципом подобия проходные калибры должны иметь поверхностный контакт с изделием, иепроходные калибры могут иметь линейный контакт.
По назначению различают рабочие калибры для контроля изделий при изготовлении, калибры контролера для проверки изделий работниками ОТК; приемные калибры для контроля изделий заказчиком; контрольные калибры для проверки размеров рабочих и приемных калибров. В качестве калибра контролера и приемных калибров используются частично изношенные проходные и новые иепроходные рабочие калибры.
Преимуществом калибров является экономичность и высокая производительность измерений при массовом и серийном производстве. Основные требования к калибрам — высокая точность изготовления, большая жесткость при малой массе, износоустойчивость, коррозионная стойкость, стабильность рабочих размеров, удобство в работе.
Калибры для измерения гладких валов и отверстий
Для контроля размеров валов применяют предельные калибры-скобы, а размеров отверстий — предельные
калибры-пробки. Условные обозначения гладких калибров Р—ПР (Р-НЕ) — рабочий проходной (непроходной); К—ПР (К—НЕ) -контрольный для поверки рабочих новых скоб проходной (непроходной); К—И — кон- t г j трольный для поверки износа рабочих проходных скоб; К—П — контрольный для поверки приемных проходных скоб.
Гладкие двухпредельные калибры-скобы, предназначенные для контроля валов с допусками по квалитегу 7 и выше, выпускаются трех основных типов: листовые двусторонние (рис. 21, а); листовые (или штампованные) односторонние (рис. 21. б); односторонние со сменными губками (рис. 21, в). Регулируемые скобы для диаметров 0…340 мм (рис. 22) имеют неподвижные пятки 2,
которые запрессованы в корпусе 1, и подвижные пятки 3, которые при установке на размер по концевым мерам длины перемещают винтами 4 и зажимают винтами 5.
Гладкие калибры-пробки выпускаются восьми типов, например двусторонние с вставками / и 3, насаженными коническими хвостовиками на ручку 2 (рис. 23, а); одно-предельные с насадкой 1, крепящейся на ручке винтами (рис. 23, б); однорядные с неполной насадкой / и коническими хвостовиками 2 (рис. 23, в); листовые односторонние (рис. 23, г).
При контроле проходные калибры должны свободно проходить в изделие под действием собственного веса, а непроходные не должны входить в изделие более чем на длину фасок. При дополнительных усилиях возникают погрешности контроля вследствие деформаций.
У калибров проверяют внешний вид, чистоту поверхности и рабочие размеры. Размеры рабочих скоб поверяют концевыми мерами длины и контрольными калибрами. Размеры рабочих и контрольных пробок измеряют универсальными приборами, например оптиметрами. Измерения осуществляют в трех равномерно распределенных вдоль оси калибра сечениях. В каждом сечении выполняют два измерения в двух взаимно перпендикулярных направлениях.
Калибры для измерения линейных размеров
Для контроля линейных размеров — длины, глубины и высоты уступов — применяют предельные листовые калибры. Калибры-скобы (рис. 24, а) предназначены для контроля длины изделий 10…500 мм. Длину отверстий контролируют листовыми пробками (рис. 24, б).
Основные методы контроля глубины и высоты уступов — надвиганием, на просвет, по рискам и осязанием. При надвигании калибра большая сторона Б должна проходить над уступом, а малая сторона М находить на него (рис. 25, а) или наоборот. При определении просвета между изделием и калибром (рис. 25, б) каждая сторона калибра должна иметь лезвиеобразную и плоскую грани для уменьшения погрешностей контроля вследствие неровностей поверхности. Калибры с рисками (рис. 25, в)применяют, когда допуск проверяемого размера составляет ~0,5 мм. Ступенчато-стержневыми калибрами
(рис. 25, г) контролируют по осязанию допуски размером до 0,01 мм.
Щупы, предназначенные для проверки зазоров между близко расположенными поверхностями, представляют собой пластины с параллельными измерительными поверхностями шириной 10 мм, длиной 100 или 200 мм и толщиной 0,02…1 мм. Щупы имеют класс точности 1 и выпускаются в виде отдельных пластин и наборов, которые состоят из пластин 1 разной толщины, собранных в обойме 2 (рис. 26).
Калибры для измерения шлицевых изделий
Шлицевые соединения могут иметь прямобочный (рис. 27, а), эвольвентный (рис. 27, б) и треугольный (рис. 27, в) профили зубьев. Центрирование вала и отверстия может осуществляться по внутреннему диаметру d, по наружному диаметру D и по боковым сторонам зубьев. Шлицевые изделия проверяют дифференцированным или комплексным способом. Для дифференцированного контроля наружного и внутреннего диаметров и толщины зубьев наружных шлицев применяют предельные калибры-скобы (рис. 28, а), а размеров внутренних шлицев — предельные калибры-пробки (рис. 28, б).
При комплексном контроле проверяют суммарные отклонения толщины зубьев валов и ширины впадин втулок проходными калибрами-пробками и калибрами кольцами
Калибры-пробки (рис. 29, а) выпускаются с одной направляющей 1 для проверки изделий с центрированием по наружному диаметру и боковым сторонам и с двумя направляющими 2 и 3 для изделий с центрированием по внутреннему диаметру. Калибры-кольца (рис. 29, б) также имеют шлицевую часть и гладкую направляющую поверхность А, которой их надевают на вал.
Профильные шаблоны
Для контроля размеров и формы изделий со сложным профилем применяют нормальные профильные шаблоны. Шаблоны 1 могут прикладываться к проверяемому профилю изделия 2 (рис. 30, а) или накладываться на изделие 2 с совмещением профилей (рис. 30, б). В первом случае отклонения профиля изделия от профиля шаблона Д определяют «припасовкой на краску», если мкм, или методом «на просвет», если
мкм; во втором случае Д измеряют с помощью индикатора 3, если
мкм, или оценивают визуально, если
мкм.
Радиусные шаблоны (рис. 31) для определения радиусов закруглений от ! до 25 мм представляют собой стальные пластины с профилем дуги окружности. Они комплектуются в наборы, состоящие из пластин с выпуклым / или вогнутым 3 профилем, и собираются в обойме 2. При контроле шаблоны, как правило, прикладываются к профилю изделия. Если в сопряжении нет зазора, то радиусы изделия и шаблона равны.
Средства и методы для измерения углов и конусов
Методы измерения углов
Углы изделий измеряют тремя основными методами: методом сравнения с жесткими контрольными инструментами — угловыми мерами, угольниками, конусными калибрами и шаблонами; абсолютным гониометрическим методом, основанным на использовании приборов с угломерной шкалой; косвенным тригонометрическим методом, который заключается в определении линейных размеров, связанных с измеряемым углом тригонометрической функцией.
К универсальным средствам измерения углов относятся нониусные, оптические и индикаторные угломеры, а также другие приборы. Углы наклона поверхностей изделий измеряют уровнями и оптическими квадратами.
Угольники и конусные калибры
Угольники поверочные 90° предназначены для проверки и разметки прямых углов изделий, для контроля изделий при сборке или монтаже и т. п. Угольники выпускаются
двух типов: лекальные (рис. 32, а) и слесарные (рис. 32, б). Они имеют измерительные А, Б и опорные В, Г поверхности. Размеры поверхностей измеряются в диапазоне от 60×40 до 1600×1000. Угольники выпускаются трех классов точности 0, 1 и 2. При измерениях опорная поверхность угольника плотно без зазора прижимается к поверхности изделия (рис. 32, в). По размеру зазора Ь между измерительной поверхностью и поверхностью изделия на расстоянии
определяют отклонение от прямого угла
Например, при
мм и
мм
Зазор определяют щупом 1 (или концевыми мерами длины) или методом «на просвет», используя «образец просвета», показанный на рис. 11.
Калибры для измерения конусов инструментов представляют собой нормальные калибр-пробки (рис. 33, а) и калибр-втулки (рис. 33, б). При контроле базорасстояния (расстояния от базы конуса до его основного расчетного сечения) торец годного внутреннего конуса должен находиться между рисками, нанесенными на поверхности калибр-пробок, а торец годного наружного конуса — между контрольными плоскостями уступа калибр-втулок. Размер опре-
деляет допускаемые отклонения размеров конусов.
При комплексном контроле конусности калибры припасовывают к конусам на краске. Краску наносят на предварительно очищенную наружную поверхность слоем толщиной 2…10 мкм. Калибр сопрягают с конусом и поворачивают не более чем на оборота при нажатии вдоль оси. У годных конусов пятно контакта без круговых разрывов располагается со стороны большего диаметра и составляет не менее 90 % площади.
Толщину слоя краски определяют по «образцу интенсивности окраски» (см. рис. 11), который получают на концевых мерах длины 2, притертых к плоской стеклянной пластине 3. На поверхности мер, кроме крайних, наносят краску, которую затем снимают лекальной линейкой, опирающейся на крайние меры.
Толщина слоя краски на мерах составляет 1, 2, … мкм и различается по интенсивности цвета.
Для проверки наружных конусов изделий применяют конусные скобы 1 с рисками, скобы 2 с уступами и двух-предельные конусные скобы 3 (рис. 34).
Универсальные угломеры
Угломеры с нониусом выпускаются двух типов: УН — для измерения наружных и внутренних углов; УМ — для измерения наружных углов. Наружными называют углы 0…I800, так как измерительные поверхности приборов охватывают изделие, а внутренними — углы больше 180°.
Угломер УН (рис. 35, а) состоит нз основания 2 с угловой шкалой, имеющей диапазон показаний 90° и цену деления На основании 2 закреплены основная линейка 3 и подвижный сектор 5 с нониусом 1. Стопор 4
фиксирует сектор в нужном положении. С помощью дер жавки 9 к сектору можно прикрепить угольник 6, к которому державкой 8 можно присоединять съемную линейку 7. Последнюю можно устанавливать на сектор 5. В полностью собранном виде между плоскостями основной и съемной линейки измеряют углы 0…500. Если на секторе 5 установлена съемная линейка 7, то измерения выполняются в пределах 140 ..200°. Между плоскостями сектора 5 и основной линейки 3 углы измеряются в пределах 230 . 320°. Полный диапазон измерений угломера УН составляет 0…3200.
Угломер УМ (рис. 35, б) также имеет основание 4 с угловой шкалой с диапазоном показаний 90°. С основанием жестко скреплена съемная линейка 3. Подвижная линейка 10 выполнена заодно с сектором 9, несущим нониус 7. Сектор поворачивается вокруг оси а и фиксируется стопором 8. На подвижной линейке 10 с помощью державки 1 может быть установлен угольник 2. Для точной установки нониуса сектор перемещают
микровинтом 6, застопорив винт 5. Диапазон измерений угломера УМ составляет 0…1800. Измерения в диапазоне 0…900 проводят с угольником 10, а в диапазоне 90…180° — без угольника, прибавляя к отсчету по шкале угломера 90°.
Принцип конструирования и расчета угловых и линейных нониусов, а также отсчет по ним одинаковы. Основные параметры нониусов угломеров приведены в табл. 4 (полный угол ). Допускаемые погрешности угломеров равны значению отсчета по нониусу.
Оптический угломер (рис. 36), предназначенный для измерения углов 0…1800, состоит из корпуса 2, с которым жестко связана сдвоенная линейка 5. Сменная линейка 4 поворачивается и перемещается в продольном направлении. Съемная подставка 7 с зажимным винтом 8 используется при измерениях углов цилиндрических или конических поверхностей.
При измерении линейку 4 выдвигают на длину, которая обеспечивает полноту охвата поверхности изделия, и стопорят поворотом рычага 6. Рабочие грани линеек 4 и 5 прижимают к плоскостям изделия, образующим измеряемый угол, и поворотом контактного кольца 1 фиксируют установленное положение. Отсчет осуществляют с помощью лупы 3. В лупу видны основная градусная шкала, а также прямая и обратная минутные шкалы с ценой деления 5′. Отсчет выполняют по делению градусной шкалы, находящемуся в пределах минутной шкалы. На рис. 38 показан отсчет, равный Допускаемая погрешность оптического угломера составляет
а при измерениях с подставкой 7 —
Методы и средства поверки угломеров изложены в ГОСТ 13006—67. Операции, выполняемые при поверке, аналогичны операциям при поверке штангенинструментов. Показания угломеров поверяют угловыми мерами 4-го разряда или класса точности 2. При поверке измерительные поверхности линеек совмещают без просвета с измерительными гранями мер. Поверяемые углы: 0°; 15 °Ю’; 30 °20′; 45°30′; 60°40′; 75°50′ и 90°.
Тригонометрические методы и средства измерений
Косвенные измерения углов конусов можно выполнять универсальными средствами измерений с помощью калиброванных роликов и шариков. Для измерений конусов используют синусную или тангенсную схему в зависимости от того, какие стороны треугольника, образующего угол, будут измерены. При тангенсной схеме измерения наружного конуса (рис. 37, а) деталь устанавливают на плите 3 и микрометром измеряют расстояния между наружными диаметрами роликов 2, помещенных на плите и на концевых мерах длины 1 размером L. Угол конуса определяют по формуле
При синусной схеме измерения внутреннего конуса (рис. 37, б) в отверстие вводят шарики 1 диаметрами и с помощью глубиномера или длиномера находят расстояния
от наружной грани конуса до шариков. Угол конуса находят из выражения
Синусные линейки для косвенных измерений углов 0…450 выпускают трех типов: 1 — без опорной плиты с одним наклоном; II — с опорной плитой с одним наклоном, III — с опорной плитой с двумя наклонами. Синусная линейка типа I (рис. 38) имеет стол / с обработанной поверхностью 5, установленный на двух роликовых
опорах 2. Боковые 3 и передняя 4 планки служат упорами для изделий, которые крепятся к столу прижимами, входящими в комплект, с помощью резьбовых отверстий 6. Расстояние между осями роликов может быть 100, 200, 300 и 500 мм. Синусные линейки выпускают классов точности 1 и 2. Допускаемые погрешности при предельном угле измерения
для линеек типа I класса точности 1 (2) не превышают
(10″), для линеек типа II —
(12″), для линеек типа III — ±10″ (15″).
При измерении углов конусов на синусной линейке (рис. 39) стол 3, на котором закреплен конус , устанавливают на требуемый номинальный угол к плоскости поверочной плиты 5 с помощью концевых мер 4. Размер блока концевых мер находят по формуле
Индикатором 2, укрепленным на универсальном штативе, определяют разность положений
поверхности изделия на длине I. Отклонения угла при вершине конуса рассчитывают по формуле
Действительный угол проверяемого конуса
Погрешность измерения синусной линейки зависит от угла
, погрешности
блока концевых мер и погрешности
расстояния между осями роликов:
Методы и средства поверки синусных линеек изложены в ГОСТ 8.165—75. Расстояние между осями роликов и диаметры роликов измеряют на горизонтальном оптиметре. Погрешность синусных линеек определяют автоколлимационным методом с помощью угловой меры типа V (см. рис. 9) или контактным методом, используя поверочные плиты класса точности 0, угловые клинья УКСЛ, концевые меры длины класса точности 1, измерительную головку с ценой деления 0,001 мм и специальные стойки.
Уровни
Уровни предназначены для контроля горизонтальности и вертикальности расположения плоских и цилиндрических поверхностей. Брусковые (рис. 40,а) и рамные (рис. 40, б) уровни имеют корпус 1 с измерительными поверхностями 4, основную ампулу 2 и установочную ампулу 3. Уровень устанавливают на проверяемой поверхности с помощью ампулы 3 так, чтобы ампула 2 находилась в горизонтальной плоскости. По ампуле 2 измеряют отклонение поверхности от горизонтальности и вертикальности (только рамным уровнем).
Ампула уровней (рис. 40, в) представляет собой запаянную цилиндрическую трубку, заполненную жидким эфиром так, что внутри трубки остается пузырек воздуха, насыщенный парами эфира. Внутренняя поверхность ампулы имеет бочкообразную форму, поэтому при горизонтальном расположении уровня пузырек занимает верхнее положение. На наружной поверхности ампулы нанесена шкала с интервалом делений 2 мм. При наклоне
уровня пузырек перемещается относительно нейтрального положения пропорционально углу наклона. По шкале ампулы измеряют наклон уровня в миллиметрах, отнесенный к длине, равной 1 м. Цена деления ампул уровней составляет 0,02; 0,05; 0,10 и 0,15 мм/м и погрешность не должна превышать соответственно ±0,004; 0,0075; 0,015 и 0,02 мм/м.
Наклон поверхности уровня на 0,01 мм/м соответствует углу 2″. При поверке нуль-пункта уровень устанавливают на плите класса точности 0, поверхность которой выставлена горизонтально. Выполняют отсчет положения конца пузырька по шкале. Затем уровень поворачивают на 180°, ставят на то же место плиты и выполняют отсчет по другому концу пузырька. Разность отсчетов не должна превышать половины деления шкалы. Нуль-пункт рамных уровней по отношению к боковым рабочим плоскостям поверяют, прижимая их сначала одной, а затем другой сторонами к вертикальной поверхности прямоугольной призмы.
Погрешность и цену деления ампулы уровней поверяют на экзаменаторах (рис. 41). Уровень 2 или ампулу устанавливают на планку 1 экзаменатора. Наклоняя планку с помощью дифференциального микровинта 4, совмещают последовательно края пузырька ампулы с делениями шкалы и снимают отсчеты по измерительной головке 3 экзаменатора. Измерение проводят при прямом и обратном перемещениях пузырька и за результат поверки принимают среднее арифметическое.
Оптические делительные головки и квадранты
Оптические делительные головки предназначены для угловых измерений и делительных работ при разметке и обработке деталей. Прибор состоит из головки (рис. 42) и задней бабки 13 с пинолью, установленной на литой станине 14. Внутри неподвижного корпуса 5 головки находится подвижный корпус 6, в подшипниках которого может вращаться шпиндель 12. В корпусе 6
Рис. 42. Оптическая делительная головка
размещены также осветитель 8 и оптическая система с отсчетиым устройством 7, предназначенные для измерения углов поворота шпинделя. На конце шпинделя в посадочное отверстие с конусом Морзе № 4 вставляется центр 11с хомутиком 10 или иное крепежное приспособление (патрон, планшайба). Измеряемое изделие устанавливают в центрах 11 шпинделя и задней бабки или закрепляют на шпинделе приспособлением. Шпиндель может быть установлен с углом наклона к горизонтали 0 . 90°; угол наклона измеряют по шкале 3 с ценой деления 1° и нониусу 2 с отсчетом 1 или 6′. При измерении шпиндель вращают маховичком / и фиксируют стопором 4. Угол поворота шпинделя грубо устанавливают по внешнему лимбу 9, точное измерение выполняют по от-счетному устройству 7, которое может иметь окуляр или экран. Оптические делительные головки выпускают четырех типов с ценой деления шкалы С=1; 2; 5 и 20″, например, ОГДЭ-2, ОГД-1. Допускаемая погрешность измерений
где — измеряемый угол,
Оптические квадранты — приборы, в которых угломер соединен с уровнем. Они предназначены для измерения углов наклона плоских и цилиндрических поверхностей различных изделий. Квадрант (рис. 43) имеет основание 1, корпус 2, внутри которого установлен неподвижный лимб, вращающуюся крышку 3. на которой укреплены уровень 4 и микроскоп 5. Для измерения угла наклона к горизонту квадрант устанавливают на поверхность изделия и вращают крышку до тех пор, пока пузырек уровня не займет среднее положение. Быстрый поворот крышки выполняют рукой при отпущенном винте 6, а тонкую
регулировку угла — микровинтом 7 при зажатом винте 6. Для грубого отсчета угла поворота служит шкала на крышке с ценой деления 5°, точные измерения выполняют с помощью микроскопа 5.
Оптические квадранты выпускают трех типов с ценой деления отсчетного устройства 2, 10, 60″ и имеют допускаемую погрешность при установке на плоскую поверхность, соответственно , 5 и 20″. При установке на цилиндрическую поверхность погрешность прибора в 2 раза больше.
Рычажно-механические приборы для измерения длины
Классификация и назначение
Рычажно-механические приборы преобразуют малые отклонения размеров изделий в удобные для отсчета перемещения стрелки по шкале. Основные типы рычаж-но-механических передач, используемых в приборах, — зубчатые, рычажные, рычажно-зубчатые, пружинные и рычажно-пружинные.
Рычажно-механические приборы делятся на три основные группы:
1) измерительные головки — съемные отсчетныеустройства, предназначенные для оснащения приборов и контрольно-измерительных приспособлений; 2) приборы со съемными отсчетными устройствами — индикаторные скобы, нутромеры и глубиномеры и др.; 3) приборы со встроенными отсчетными устройствами — рычажные скобы и микрометры н др.
Приборы применяют для измерения линейных размеров, а также отклонений размеров от заданной геометрической формы — овальности, биения, огранки, прямолинейности и т. п. Как правило, их используют для измерения методом сравнения с мерой. Если размеры изделий меньше диапазона показаний прибора, то применяют метод непосредственной оценки.
Измерительные головки устанавливают на стойках или штативах, которые выполняются нескольких типов: стойки C-I и С-П (рис. 44. а), стойки малогабаритные C-III (рис. 44,6), стойки C-IV (рис. 44,в), штативы Ш-I…LLJ-III (рис. 44.г), штативы с магнитным основанием ШМ-1…ШМ-Ш (рис. 44,). Тип стойки или штатива определяется ценой деления измерительной головки: C-I — до 0,5 мкм; С-И — от 1 до 5 мкм; Ш-I и ШМ-1 —от 2 до 5 мкм; С-Ш, Ш-И и ШМ-И — до 10 мкм; С IV, Ш-Ш и ШМ-Ш — свыше 10 мкм.
Стойки имеют основание с измерительным столом 2 и колонку 3 с кронштейном 4 или стержнем 9. Измерительную головку 6 зажимают на стойках винтом 5. Кронштейн может перемещаться по колонке гайкой 8 и закрепляться
винтом 7. Стержень зажимают в хомуте 10 винтом 11.
Штативы не имеют измерительного стола и применяются при измерениях на поверочных плитах и на станках. Измерительные головки закрепляют в державке 12, которую зажимают винтом 13 на стержне 9, имеющем пружинные пальцы 14 и винт 15 для тонкой установки на размер. Назначение остальных деталей штативов такое же, как у стоек.
Зубчатые измерительные головки
Зубчатые измерительные головки — индикаторы часового типа с ценой деления 0,01 мм — изготовляются следующих основных типов:
И402, И405, ИЧ10 и ИЧ25 — перемещение измерительного стержня параллельно шкале, диапазоны измерений соответственно 0…2, 0…5, 0…10 и 0…25 мм;
ИТ02 — перемещение стержня перпендикулярно к шкале и диапазон измерений 0…2 мм.
Индикаторы типа ИЧ5 и ИЧ10 выпускаются в корпусе диаметром 60 мм, а индикаторы ИЧ2 и ИТ2 — в корпусе диаметром 42 мм (малогабаритные).
Устройство и принципиальная схема индикатора типа ИЧ показаны на рис. 45. Основными узлами индикатора являются циферблат / со шкалой, ободок 2, стрелка 3, указатель 4 числа оборотов стрелки, гильза 5, измерительный стержень 6 с наконечником 7, корпус 8, ушко 9 и головка 10 стержня. Гильза и ушко служат для крепления индикатора на стойках, штативах и приспособлениях. Поворотом ободка 2, на котором закреплен циферблат, стрелку совмещают с любым делением шкалы. За головку 10 стержень отводят при установке изделия под измерительный наконечник.
Принцип действия индикатора заключается в следующем (рис. 45, б). Измерительный стержень 12 перемещается в точных направляющих втулках 2, запрессованных в гильзы корпуса. На стержне нарезана зубчатая рейка 11, которая поворачивает триб 10 с числом зубьев (трибом в приборостроении называют зубчатое колесо с числом зубьев (
). Зубчатое колесо
установленное на одной оси с трибом 10, передает вращение трибу
На оси триба 8 закреплена стрелка 3. В зацеплении с трибом 8 находится также зубчатое колесо
на оси которого закреплены указатель 4 и втулка 6 с пружинным волоском 5, другой конец которого прикреплен к корпусу. Колесо 7, находясь под действием волоска, обеспечивает работу всей передачи прибора на одной стороне
профиля зуба и тем самым устраняет мертвый ход передачи. Пружина создает измерительное усилие на стержне.
Передаточное отношение зубчатого механизма выполнено так, что при перемещении измерительного стержня на расстояние мм стрелка совершает полный оборот, а указатель поворачивается на одно деление. Шкала индикатора имеет число делений
Цена деления шкалы циферблата
В корпусе малогабаритных индикаторов нельзя разместить полные зубчатые колеса с числом зубьев поэтому они заменены зубчатыми секторами. У торцовых индикаторов ИТ2 (рис. 46) перемещение измерительного стержня передается рейке зубчатого механизма через двухплечий рычаг, имеющий передаточное отношение, равное единице. Индикаторы ИТ имеют такие же основные элементы и цену деления шкалы, как индикаторы ИЧ.
Индикаторы часового типа выпускаются классов точности 0 и 1. Основные допускаемые погрешности этих индикаторов приведены в табл. 5.
Настройка индикаторов на размер изделия выполняется в следующем порядке: 1. Индикатор закрепляют на кронштейне стойки или в державке штатива (см. рис. 44, б), установленного на плите. Для индикаторов часового типа используют стойки C-IV и штативы Ш-П. 2. При относительных измерениях на стол стойки или плиту устанавливают блок концевых мер, размер которого равен номинальному размеру изделия. При абсолютных измерениях меры не используются. 3. Опускают индикатор по колонке так, чтобы наконечник соприкоснулся с поверхностью меры или плиты и стрелка отклонилась от нулевого положения. Предварительное отклонение
трелки называют «натягом прибора». Значение натяга должно быть больше, чем допускаемые отклонения размера изделия от номинального значения. Обычно дают стрелке сделать один оборот. При работе с универсальным штативом для создания натяга пользуются винтом микроподачи 4. Зафиксировав положение индикатора, шкалу устанавливают на нулевое положение, поворачивая ободок. 5. Поднимая и опуская измерительный стержень за головку, проверяют постоянство показаний индикатора. Если наблюдается отклонение стрелки от нуля, настройку повторяют. 6. Отведя стержень, снимают блок мер.
Измерения выполняют в таком порядке: приподняв наконечник прибора, устанавливают на стол или плиту изделие; затем опускают наконечник на поверхность изделия и выполняют отсчет показаний. По указателю числа оборотов стрелки находят число миллиметров в размере. Дробная доля размера равна числу делений циферблата против стрелки, умноженному на мм. При вращении стрелки против часовой стрелки отсчет по индикатору складывается с длиной блока концевых мер, в противном случае вычитается.
Область применения индикаторов расширяется благодаря использованию приспособлений. Струбцина для установки индикатора на валы (рис. 47, а) имеет скобу 5 с губкой 6, которая перемещается винтом 7. К струбцине привинчивается стержень 4 с хомутом 3 для крепления державки 2 с индикатором 1. Прямой (рис. 47, б) и угловой (рис. 47, в) рычаги применяют при измерениях в труднодоступных местах. Рычаги 2 под действием измерительного стержня 5 индикатора поворачиваются вокруг оси 3 кронштейнов 4, прикрепленных к гильзе индикатора, и упираются сферическими наконечниками 1 в поверхность изделия.
Рычажно-зубчатые измерительные головки
К рычажно-зубчатым измерительным головкам относятся индикаторы ИГ и многооборотные индикаторы МИГ, выпускаемые с ценой деления 0,001 и 0,002 мм.
Индикатор ИГ (рис. 48, а) состоит из корпуса 1, циферблата 2, стрелки 3, ёрретира 4, присоединительной гильзы 5, измерительного стержня 6, наконечника 7, указателя 9 поля допуска изделия и винта 8 точной установки механизма в нулевое положение. Арретир (рычаг) необходим для подъема измерительного стержня перед установкой изделия.
Механизм головки ИГ (рис. 48, б) состоит из двух неравноплечих рычажных пар и одной зубчатой передачи. Перемещение измерительного стержня 10 через рычаг 6 передается малому плечу рычага 13. Большое плечо рычага 13 передает движение рычагу 1 зубчатого сектора 2. Зубчатый сектор вращает триб 3, на оси которого установлены стрелка 15 и втулка со спиральным волоском
14, устраняющим зазоры в передаче. Измерительное усилие создается двумя пружинами 7, прикрепленными к рычагу 6. Весь механизм индикатора смонтирован на плате 4, которая для установки на нуль поворачивается вокруг оси 5 и пружинами 16 прижимается через рычаг 12 к установочному винту.
Многооборотный индикатор МИГ имеет те же основные узлы, что и индикатор ИГ. На циферблате нанесено 200 делений круговой шкалы и расположен указатель числа оборотов стрелки, полное число оборотов которой равно 5. Механизм многооборотного индикатора (рис. 49, а) содержит две рычажные и две зубчатые передачи. Перемещение измерительного стержня / передается рычагу 11, а затем рычагу 10 зубчатого сектора 2, который находится в зацеплении с трибом 4. Зубчатое колесо 5, посаженное на одну ось с трибом 4, вращает триб 3 и закрепленную на его оси стрелку 6. На оси зубчатого колеса 8, зацепляющегося с трибом 3, установлен указатель 7 числа оборотов стрелки и пружинный волосок 9.
Весь механизм многооборотного индикатора (рис. 49, (5) собран на плате 2, которая пружинами прижимается к упору рычага 3 и винту 4 установки индикатора на
нуль. Штифт 5 обеспечивает движение измерительного стержня без поворота, а винт 6 ограничивает нижнее положение стержня.
Основные допускаемые погрешности рычажно-зубча-тых измерительных головок приведены в табл. 6.
Рычажно-зубчатые головки при измерениях устанавливают на стойки C-III и штативы Ш-I. При настройке индикаторов ИГ на размер по блоку концевых мер кронштейн с индикатором опускают по колонке стойки так, чтобы измерительный наконечник коснулся меры и стрелка установилась около нулевого положения. Затем поворотом шкалы стрелку устанавливают на нуль и проводят несколько раз арретирование (подъем и опускание) стержня, проверяя правильность настройки. По показаниям прибора находят как отклонения размера изделия от размера меры, так и его знак. Измерения многооборотными индикаторами выполняют так же, как индикаторами часового типа.
Пружинные измерительные головки
Пружинные измерительные головки являются наиболее точными рычажно-механическими приборами. Они выпускаются трех основных типов. 1) ИГП — микрока-торы; 2) ИПМ — микаторы (малогабаритные); 3) ИРП — миникаторц
В качестве чувствительного элемента в этих приборах (рис. 50,а, 51,а; 52,а) используется специальная ленточная
ная пружина 2, завитая спирально от середины в разные стороны и закрепленная по концам на плоских пружинах. К середине пружины приклеена стрелка 3. Переме-
измерительного 7 вызывает изменение длины пружины 2 и поворот ее средней части. Смещение стрелки относительно шкалы прибора пропорционально ; перемещению измерительного стержня. Преимущества пружинных передач: высокая чувствительность ленточных
пружин, обеспечивающая большую точность измерений; отсутствие внешнего трения и минимальная разность прямого и обратного хода.
Основные параметры пружинных измерительных головок приведены в табл. 7.
У микрокаторов (рис. 50, а) ленточная пружина 2 закреплена на угольнике 1 и консольной пружине 4, установленной на угловом выступе. Изменяя положение пружины 4 с помощью винтов, которыми она крепится к выступу, регулируют натяжение ленточной пружины и устанавливают прибор на нуль. Измерительный стержень 7 подвешен на мембранах 6 и жестко связан с угольником I. Перемещение стержня вызывает поворот угольника вокруг точки и и растяжение пружины. Измерительное усилие создается пружиной 5.
Пружинная передача микрокатора (рис. 50, б) размещена в корпусе , к которому присоединена измерительная гильза 5. Положение шкалы 2 регулируется в пределах делений винтом 4 для установки прибора на нуль. Указатели 3 поля допуска перемещаются рычажками, расположенными на задней стороне корпуса. На конце гильзы с помощью хомута, зажимаемого винтом 7, установлен арретир 8, соединенный с измерительным наконечником 9 со сферической поверхностью. Фиксатором 10 измерительный стержень зажимают при транспортировании.
Микрокаторы применяют для высокоточных относительных измерений размеров, а также отклонений формы изделий со стойками C-I и С-И и приспособлениями, имеющими присоединительный диаметр 28 мм. При настройке на нулевое положение по блоку концевых мер используется микроподача стола стойки. Выпускают также микрокаторы ИГПУ и ИГПР с уменьшенным и регулируемым измерительным усилием, ИГПГ с герметизированным корпусом и ИГПВ виброустойчивые.
Микаторы (рис. 51, б) могут быть использованы в качестве отсчетных устройств в различных приборах и приспособлениях. Назначение узлов и деталей и их обозначение на рис. 51 такие же, как на рис. 50. Ввиду небольшого диаметра (8 мм) гильзы 5 (см. рис. 51, б) измерительный стержень перемещается в шариковых направляющих 6 (см. рис. 51, а) и шарнирно связан с рычагом , к которому прикреплен конец пружины 2..
Миникаторы (рис. 52) предназначены для измерений в труднодоступных местах изделий. Они представляют собой рычажно-пружинные головки бокового действия с перемещением измерительного стержня перпендикулярно к плоскости шкалы. Перемещение стержня 7 (рис. 52, а) через рычаг 6, подвешенный на плоской мембране 5 и поворачивающийся относительно оси 8, передается угольнику пружинной передачи. Миникаторы (рис. 52, б) применяются в державке с микроподачей для удобства установки на размер. Державку закрепляют на стержне 2. Цена деления миникаторов составляет 1 мкм при длине измерительного наконечника, равной 72 мм и 2 мкм при длине 30 мм.
Скобы с отсчетным устройством
Скобы с отсчетным устройством предназначены для точных измерений наружных размеров изделий методом сравнения с мерой. Скобы выпускаются двух типов: СИ — индикаторные, оснащенные измерительной головкой с ценой деления 0,01 мм и диапазоном измерений 3 мм, и CP — рычажные со встроенным в корпус отсчетным устройством с ценой деления 0.002 мм и диапазоном измерений мм.
Индикаторные скобы (рис. 53) имеют корпус 9 с теплоизоляционной накладкой 10, в котором установлены индикатор / часового типа, подвижная пятка 3 и сменная передвижная пятка 5. Диапазон перемещения передвижной пятки равен 50 мм. Измерительное усилие создается пружиной 2. Упор 4 служит для правильной установки изделия. Винты 6 фиксируют положение индикатора и передвижной пятки. Рычагом 8 отводят подвижную пятку 3 перед установкой изделия. Колпачок 7 предохраняет пятку 5 от сбоя.
Пределы измерений индикаторных скоб составляют 0…50, 50… 100, 100…200….. 600…700, 700…850 и 850… 1000 мм. Основная допускаемая погрешность изменяется от 5 до 20 мкм в зависимости от типоразмера скобы и длины используемого участка шкалы индикатора.
Рычажные скобы (рис. 54, а) состоят из корпуса, в котором размещено отсчетное устройство со шкалой 4, указателями поля допуска 3 и стрелкой 5. Положение указателей регулируют винтами при снятой крышке 6.
Пружина 12 сообщает подвижной пятке измерительное усилие. Передвижная пятка 10 перемещается винтом 8, закрываемым колпачком 7, н зажимается стопором 9. Пятка 11 отводится кнопкой 2 арретира. Встроенное отсчетное устройство скобы имеет рычажно зубчатый механизм (рис. 54,6). Подвижная пятка 4 поворачивает рычаг 3, большое плечо которого заканчивается зубчатым сектором 6, находящимся в зацеплении с трибом 7. На оси триба укреплены стрелка 5 и пружинный волосок 8. Арретир 2 перемещает пятку 4 при нажатии кнопки /. Пределы измерений рычажных скоб составляют 0…25, 26 ..50, …. 125…150 мм; диапазон перемещения переставной пятки 25 мм. Основная допускаемая погрешность не превышает 2 мкм.
Скобы устанавливают на размер по блоку концевых мер длины. Передвижную пятку приводят в соприкосновение с поверхностью меры так, чтобы стрелка индикаторной скобы показала «натяг», а стрелка рычажной скобы установилась на нуль. Закрепив пятку стопором, закрывают ее колпачком от повреждений и загрязнений. Действительный размер изделия определяют как сумму размера блока мер и разности показаний отсчетного устройства при установке меры, а затем изделия.
Рычажные микрометры
Микрометрам рычажным присущи свойства микрометров МК и скоб с отсчетным устройством. Они устроены так же, как скобы, но вместо передвижной пятки имеют микрометрическую головку 2 без трещотки (рис. 55).
Рычажные микрометры MP (рис. 55, а) имеют встроенное в корпус I отсчетное устройство 3 с ценой деления
2 мкм и диапазоном показаний мм. Пределы измерений микровинта равны 0…25, 25…50, 50…75, 75…100 мм, а основная допускаемая погрешность 3 мкм.
Рычажные микрометры МРИ (рис. 55, б) оснащены измерительной головкой / с ценой деления 10 мкм и диапазоном показаний 2, 5 или 10 мм. Пределы измерений составляют 100 ..125, 125…150, 150…200, 150…300, …, 900… 1000, 1000…2000, …, 1800…2000 мм, а допускаемая погрешность 4…36 мкм в зависимости от типоразмера.
При абсолютных измерениях барабан микрометрической головки вращают так, чтобы поверхности пятки и микровинта соприкоснулись с поверхностью изделия, а стрелка отсчетного устройства установилась на нуль. После этого барабан поворачивают в том же направлении до совпадения штриха круговой шкалы барабана с продольным штрихом на стебле.
Размер определяют суммой показаний микрометрической головки и отсчетного устройства.
Индикаторные нутромеры и глубиномеры
Индикаторные нутромеры предназначены для измерения внутренних размеров и диаметров отверстий в пределах 2… 1000 мм на глубине до 500 мм. Их конструкции разнообразны. Они могут оснащаться индикаторами с ценой деления 1, 2 и 10 мкм и в зависимости от диапазона измерений и типа индикатора имеют пределы допускаемой погрешности 1.8…22 мкм. Нутромеры с пределами измерений 3…6, 6…10, 10…18 мм (рис. 56) оснащены рычажно-зубчатыми головками ИГ. К корпусу 1 нутромера крепится на резьбе сменная вставка 2, в отверстиях которой расположены два измерительных 8 и два центрирующих 7 шарика. Перемещение измерительных шариков при входе в отверстие передается игле 6 и через нее измерительному стержню индикатора. Центрирующие шарики, диаметр которых на 0,01 мм меньше диаметра измерительных шариков, не позволяют сместиться линии измерения относительно диаметра отверстия. Упор 5 для установки индикатора фиксируется в нужном по высоте положении винтом 4. Индикатор вставляется в пружинную разрезную втулку корпуса 1 и зажимается гайкой 3.
Нутромер для измерения размеров до 450 мм показан на рис. 57. В насадке 10 закреплена втулка 7, в которую
с одной стороны ввернут регулируемый стержень 9, с другой свободно входит подвижный стержень 12. При установке нутромера на размер положение стержня 9 регулируют таким образом, чтобы кольцевая риска на стержне 12 находилась в плоскости
торца втулки 7. При этом плечи рычага 11 располагаются перпендикулярно к осям стержней 9 и 5, что обеспечивает минимальные погрешности рычажной передачи. Положение стержня 9 после регулировки фиксируют гайкой 8. Перемещение стержня 12 через рычаг 11. в плечи которого впрессованы шарики 6, и стержень 5 передается индикатору 1, установленному на корпусе 4 с теплоизолированной ручкой 3. Измерительное усилие создается пружиной индикатора и пружиной 2. В отверстия насадки 10 вставлены направляющие стержни 14 центрирующего мостика 13. Пружины 15 прижимают мостик к поверхности отверстия.
Основные погрешности прн измерениях нутромерами возникают вследствие смещения линии измерения относительно диаметра отверстия (рис. 58, а) и перекоса нутромера в отверстии (рис. 58, б). Линия измерения устанавливается по диаметру отверстия с помощью центрирующего мостика. Погрешности центрирования не превышают 3 мкм. Погрешности перекоса уменьшают, покачивая нутромер в плоскости осевого сечения отверстия. При наименьших показаниях прибора линия измерения совпадает с диаметральной плоскостью отверстия.
Перед измерением нутромеры устанавливают на номинальный размер отверстия с помощью аттестованного кольца, или блока концевых мер с боковиками, или микрометра, закрепленного либо в стойке, либо на измерительной машине.
Индикаторные глубиномеры (рис. 59), предназначенные для относительных измерений глубины пазов и отверстий, высоты уступов и т. п., имеют основание 2 с державкой 3, индикатор 4 часового типа ИЧ10 и сменный измерительный стержень 1. Набор сменных стержней обеспечивает пределы измерений 0..10, 10…20, …, 90… 100 мм. Перед измерением глубиномер устанавливают иа нуль с помощью двух концевых мер длины или аттестованной втулки. Установив глубиномер иа концевые меры, помещенные на плите, индикаторную головку перемещают в державке так, чтобы стрелка показала «натяг» приблизительно на один оборот. Зажав стопор 5, шкалу индикатора ставят на нуль поворотом ободка. При измерениях показания прибора суммируют с размером меры.
Оптико-механические приборы
Классификация и назначение
Оптико-механические приборы предназначены для высокоточных измерений размеров изделий и отклонений от геометрической формы. В их механизме сочетаются оптические и механические измерительные системы.
Оптическая система — совокупность оптических узлов к деталей (линз, призм, зеркал, объективов, окуляров и т. п.), предназначенная для формирования пучков световых лучей. В измерительных приборах используются основные свойства оптических систем: 1) возможность получать действительные и мнимые увеличенные изображения шкал приборов или объектов измерения с помощью линз; 2) пропорциональность углов поворота зеркал п отраженных от него лучей; 3) дисперсия света; 4) интерференция цвета и др.
Оптико-механическне приборы разнообразны по назначению и принципу действия как оптической, так и механической измерительных систем. К ним относятся оптикаторы, оптиметры, длиномеры, измерительные машины, контактные интерферометры, измерительные микроскопы и проекторы. В измерительном механизме оптиметров и оптикаторов сочетаются механический и оптический рычаг, поэтому такие приборы иногда называют рычажно-оптическими.
По положению линии измерений приборы делят на вертикальные (В) и горизонтальные (Г), а по способу отсчета показаний — на окулярные (О) и экранные (Э). Пример маркировки оптиметра: ОБО — оптиметр вертикальный окулярный. Метрологические показатели основных типов оптиметров приведены ниже.
Основы оптических методов измерений
С точки зрения физической оптики, видимый свет представляет собой электромагнитное излучение в диапазоне длин волн от мкм (фиолетовый цвет) до
мкм (красный цвет). Скорость света зависит от среды, в которой он распространяется. Показатель преломления характеризует оптические свойства среды и определяется отношением
где С — скорость света в пустоте;
— скорость света в данной среде, Он зависит от длины волны света: чем больше длина волны, тем меньше показатель преломления. Это явление называется дисперсией света и используется для разложения света, например, с помощью призм.
С точки зрения геометрической оптики, источником света является точка, луч света — линия, по которой распространяется свет, световой поток — совокупность световых лучей. В однородной прозрачной среде свет распространяется от источника прямолинейно во все стороны с одинаковой скоростью. Световые лучи в пучке не влияют один на другой. Угол отражения луча от поверхности равен углу падения, а угол падения и преломления на границе двух сред связаны зависимостью
Оптические приборы часто содержат зеркала и линзы. Линза — прозрачное тело, ограниченное поверхностями, из которых хотя бы одна представляет собой поверхность вращения. Для получения качественного изображения, как правило, используются системы линз. Объектив — система линз и зеркал, расположенная со стороны объекта измерения и дающая его первичное изображение. Окуляр — система линз, обращенная к глазу наблюдателя.
В оптических приборах часто применяется оптический рычаг. Принцип действия оптического рычага, полученного с помощью зеркала, показан на рис. 60. На зеркало 1 падает луч света 2 и отражается на шкалу 3 прибора. Если зеркало наклонить на угол а, то отраженный луч сместится на расстояние где L — расстояние шкалы от зеркала. Путем многократного отражения луча света между поворачивающимся и неподвижным зеркалами (см. рис. 66, б) размер оптического рычага может быть увеличен.
Оптический рычаг можно получить также с помощью объектива и зеркала. Объектив превращает рассеянный свет, исходящий из источника, расположенного на фокальной поверхности MN объектива, например в точке А, в пучок параллельных лучей и собирает падающие на него параллельные лучи на фокальной плоскости в точке В (рис. 61, а). Фокальной плоскостью объектива называют плоскость, проходящую через его фокус F перпендикулярно к главной оптической оси OF. Направление параллельных лучей после объектива совпадает с направлением оптической оси АО, так как лучи, проходящие через оптический центр объектива О, не преломляются. Соответственно, точка В лежит на пересечении луча ОВ, идущего через оптический центр, с фокальной плоскостью ММ. Если источник света поместить в точку А фокальной плоскости и за объективом поставить зеркало (рис. 61, б, в), то лучи, отразившись от зеркала и пройдя снова через объектив, соберутся в точке на фокальной плоскости. Точка
называется автоколлимационным изображением точки А, так как
эти точки находятся в одной плоскости. Оптические приборы, которые предназначены для получения автоколлимационного изображения объекта, называются автоколлиматорами.
Возможны два случая автоколлимации:
- Источник света А расположен на расстоянии AF от главной оптической оси объектива 1, а плоскость зеркала 2 перпендикулярна к главной оптической оси (рис. 61,6). Автоколлимационное изображение
располагается симметрично точке А относительно фокуса F. Так как угол отражения лучей от зеркала равен углу падения
то
Из равенства прямоугольных треугольников
следует равенство
- Источник света А расположен в фокусе F объектива, а зеркало наклонено к главной оптической оси под углом а (рис. 61, в). Угол отраженных лучей с главной оптической осью составляет 2а. Отклонение автоколлимационного изображения
от точки А
где — фокусное расстояние объектива.
В оптиметрах поворот зеркала происходит под действием измерительного стержня прибора. Перемещение стержня, плечо
механического рычага, поворачивающего зеркало, и угол поворота связаны соотношением
Передаточное отношение автоколлимационной оптической системы
и не зависит от расстояния между зеркалом и объективом. При малых углах поворота зеркала, близких к нулю,
Оптикаторы
Оптикаторы представляют собой измерительные пружинно-оптические головки, в которых механическая пружинная передача сочетается с оптическим рычагом. Они отличаются высокой точностью и стабильностью измерений, предназначены для поверки концевых мер и особо точных измерений ответственных изделий и применяются в универсальных стойках С-1 и приспособлениях с присоединительным диаметром 28 мм.
Оптикатор (рис. 62, а) имеет такое же устройство пружинной передачи, как микрокатор, но вместо стрелки в середине пружинной ленты 1 приклеено миниатюрное зеркало 2. Свет от лампочки 6 проходит через конденсор 5 и щель диафрагмы 4, по середине которой натянута нить. Конденсор — это оптическая система, служащая
для освещения рассматриваемого или проецируемого предмета параллельными лучами света. Изображение нити проецируется объективом 3 на зеркало 2 и, отразившись от него, попадает на шкалу прибора. Так как перемещение по шкале равно удвоенному углу поворота зеркала, умноженному на расстояние от зеркала до шкалы, передаточное отношение оптикатора в 2 раза больше, чем у микрокатора. Оптнкаторы имеют больший диапазон показаний и меньшие погрешности измерений и вариации показаний, чем микрокаторы с той же ценой деления шкалы. Их основные показатели приведены в табл. 8.
Оптикатор (рнс. 62, б) имеет корпус 4, на котором установлены осветитель 6 и присоединительная трубка /. Положение шкалы 5 в пределах ±6 делений регулируют винтом 3. Поворотом кнопок 2 перемещают два светофильтра (зеленый и красный), которые служат указателями поля допуска изделий.
Оптикаторы используют для относительных измерений методом сравнения с мерой. Порядок настройки прибора и измерений такой же, как для пружинных измерительных головок.
Вертикальный окулярный оптиметр
Вертикальные оптиметры применяют для точного измерения наружных размеров изделий: длины плоскопараллельных концевых мер, диаметров гладких калибр-пробок, резьбовых калибров, шариков и проволоки, толщины тонких листов и т. п.
Оптическая схема измерительной трубки оптиметра с окулярным отсчетом и его шкала показаны на рис. 63, а. Световой поток от внешнего источника света а, отразившись от зеркала 3, через призму 2 полного внутреннего отражения освещает шкалу, нанесенную на левой стороне окулярной сетки 4, которая находится в фокальной плоскости объектива 6. Сеткой называется стеклянная пластина, на которой различными способами нанесены штрихи, цифры, шкалы, марки, профили объектов различной конфигурации (резьбы, зубья) и т. п. Призма 5 поворачивает ход лучей на 90° и позволяет придать трубке удобную форму колена. Световой поток проходит через объектив и, отразившись от зеркала 7, дает автоколлимационное обратное изображение шкалы в правой части окулярной сетки, на которой нанесен указатель, что соответствует схеме автоколлимации, показанной на рис. 61, б. Зеркало 7 прижимается двумя пружинами к шарикам 8 и измерительному стержню 9. При отклонении зеркала, вызванном перемещением стержня, изображение шкалы на окулярной сетке смещается относительно указателя в соответствии со схемой автоколлимации, показанной на рис. 61, в. Увеличенное изображение шкалы наблюдается через окуляр 1.
В трубках оптиметров фокусное расстояние мм, а длина механического рычага
мм, что обеспечивает передаточное отношение
Шкала оптиметра имеет число делений
с интервалом делений
мм. Цена деления
мм. Увеличение окуляра
обеспечивает удобное наблюдение шкалы. Видимый интервал деления шкалы составляет
мм. Пределы измерений по шкале
Все детали трубки оптиметра собирают и устанавливают в коленообразной трубке (рис. 63, б). Измерительный стержень с наконечником 15 и зеркало 18, установленное на основании 10, собирают иа втулке 12, которая закрепляется в трубке гайкой 16 с наружной резьбой. Основание 10 прижимается пружиной 17 к шарикам на шайбе И и стержню. Шайба 13 ограничивает ход стержня, упираясь в крышку 14. Линзы 8 объектива собраны в трубке 9. Призма 6 установлена на плате 7. Окулярная сетка 4, на которой фотографическим путем нанесены шкалы и указатель, и осветительная призма 3 закреплены в тубусе 5, который тремя радиальными винтами укреплен во втулке 2. На втулку с помощью многоходовой резьбы навинчивается окуляр 1, что позволяет регулировать четкость изображения шкалы.
Вертикальный оптиметр ОВО-1 (рис. 64) представляет собой сочетание трубки 2 оптиметра со стойкой типа C-II. На трубку надет арретир 5 для отвода измерительного наконечника
6. Трубка зажимается винтом 4 в разрезной муфте кронштейна 11, который перемещается по колонке при вращении кольца 13 и зажимается винтом 12. Колонка запрессована в устойчивое основание 14, на котором расположен предметный стол 7. Горизонтальное положение стола устанавливают вращением микровинтов 8. В вертикальном направлении стол перемещают в пределах нескольких миллиметров вращением гайки 10 микрометрического механизма и фиксируют винтом 9.
Перпендикулярность оси измерительного стержня плоскости стола проверяют при надетом на стержне плоском измерительном наконечнике с помощью плоскопараллельной концевой меры размером приблизительно 10 мм. Меру притирают к столу и, ослабив винт 12, вращением кольца 13 опускают кронштейн 11, пока наконечник 6 не коснется меры. Момент касания отмечают по перемещению изображения шкалы в окуляре 3. Зеркальцем 1 направляют свет в осветительную призму. Застопорив кронштейн винтом 12, выполняют ряд измерений, устанавливая меру относительно наконечнн-ка в положениях I, II, III и IV (рис. 65, а). Если плоскость наконечника не параллельна плоскости стола (рис. 65, б), то показания оптиметра при различных положениях меры будут отличаться одно от другого. Вращением микровинтов 8 (см. рис. 64) стол устанавливают так, чтобы во всех четырех положениях меры показания были одинаковыми.
Оптиметр устанавливают на нуль (на размер исходной меры) в следующем порядке. Меру заданного размера притирают к столу с гладкой поверхностью. Стол предварительно переводят в нижнее положение. Кронштейн 11 с трубкой 2 (см. на рис. 64) плавно опускают до касания без толчка с поверхностью меры. Вращением кольца 13 устанавливают изображение шкалы так, чтобы нулевой штрих был несколько ниже указателя, и кронштейн закрепляют винтом 12. Установку прибора на нуль осуществляют, поднимая стол вращением гайки 10, и фиксируют винтом 9. Установку на нуль проверяют, поднимая и опуская арретиром измерительный наконечник 2—3 раза. Если показания оптиметра не стабильны, то прибор снова устанавливают на нуль кольцом 13. При измерениях, подняв наконечник арретиром, заменяют меру изделием. По показаниям оптиметра находят отклонение размера изделия от размера меры. Цилиндрические изделия, например гладкие калибры-пробки, прокатывают под измерительным наконечником; наибольшее показание соответствует диаметру изделия в измеряемом сечении.
Оптиметры комплектуют сменными измерительными наконечниками. Сферические наконечники используют для измерения плоских и цилиндрических изделий диаметром более 10 мм, ножевидные наконечники — для цилиндрических изделий диаметром менее 10 мм, плос кие наконечники— для сферических изделий, например шариков. Измеряемые изделия устанавливают или непосредственно на предметный стол, или на накладной стол с ребристой поверхностью, который притирается к предметному столу. Площадь ребристой поверхности легче довести до требуемой плоскостности, и она меньше. чем гладкая поверхность подвержена загрязнениям, приводящим к погрешностям изменений.
Вертикальные экранные оптиметры
Оптиметры ОВЭ являются усовершенствованной моделью оптиметра ОВО-1. Наличие экрана облегчает процесс измерения и повышает его производительность. В оптической схеме экранного оптиметра (рис. 66, а) лучи света от лампы 1 через конденсор 2, светофильтр 3, линзу 4 и призму 5 освещают правую сторону стеклянной пластины 6, на которую нанесена шкала, расположенная в фокальной плоскости объектива 8. Между объективом и пластиной находится зеркало 7, изменяющее направление хода лучей. После объектива параллельные лучи света отражаются от неподвижного 9 и качающегося 10 зеркал и, совершив обратный путь через объектив и зеркало 7, дают обратное автоколлимационное изображение шкалы на левой части пластины 6 с указателем отсчета. Изображение шкалы и указателя
проецируется объективом 11 через систему зеркал 12, 13 и 15 на матовый стеклянный экран 14. Зеркало 10 связано механическим рычагом с измерительным стержнем прибора. У оптиметров ОВЭ-1 угол между зеркалами 9 к 10 составляет и лучи света отражаются от качающегося зеркала один раз, поэтому чувствительность прибора такая же, как у 6) оптиметров ОВО-1. У оптиметров ОВЭ-2 — ультраоптиметров — угол между зеркалами 9 и 10 составляет 15°, что обеспечивает многократное
отражение лучей от качающегося зеркала (рис. 66, б). За счет многократного отражения достигается большое результирующее отклонение лучей от зеркала 10. Поэтому передаточное отношение оптической системы больше, а цена деления шкалы оптиметра ОВЭ-02 меньше, чем у оптиметра ОВЭ-1.
Оптиметр ОВЭ-1 (рис. 67, а) состоит из измерительной головки 2 с осветительной системой 1. Все оптические части прибора размешены внутри корпуса на передней части которого установлен экран, защищенный от внешнего света блендой 3. Головка закреплена винтом 5 в кронштейне 4 стойки C-II. Положение стола 6 с ребристой поверхностью регулируют маховичками 7 и фиксируют винтами 8. Упор 9, закрепленный в державке 10, используют для проверки партий сферических и цилиндрических изделий одинакового размера. На столе 6 имеются резьбовые отверстия для крепления накладных столов и приспособлений. Для измерения изделий, установка которых на стол с ребристой поверхностью затруднена, например калибров-пробок и шариков, используют стол СТ-6 с гладкой поверхностью.
Оптиметр ОВЭ-02 (рис. 67, б) имеет стойку, которая состоит из жесткого литого основания 1 и призматической колонки 2. Кронштейн 3 перемещается по направляющим колонки с помощью кремальеры и стопорится винтами 4. Головка 5 оптиметра крепится в кронштейне винтами 6. Предметный стол 7 с ребристой поверхностью можно перемещать в вертикальном направлении винтом 9 микроподачи и стопорить в установленном положении винтом 8.
Горизонтальный окулярный оптиметр
Горизонтальный оптиметр ОГО-1 (рис. 68, а) позволяет измерять наружные размеры до 350 мм, наружные диаметры до 225 мм и внутренние диаметры до 150 мм. Внутренние измерения в пределах 1 …13 мм выполняют с помощью электроконтактной головки ГК-3, а свыше 13,5 мм — с помощью приспособления ИП-3. На массивном основании / закреплены горизонтальные направляющие 2, по которым перемещаются и фиксируются в нужном положении кронштейны 3. В кронштейнах винтами 7 зажаты пиноль 4 и трубка 12 оптиметра. Изделие устанавливают на стол 11 между измерительными
наконечниками 9, закрепленными на стержнях пиноли и трубки. Стержень пиноли перемещают мнкровинтом 5 и фиксируют винтом 6. Стол 11 имеет механизм для перемещения в трех взаимно перпенднкулярных направлениях и для вращения вокруг поперечной горизонтальной и вертикальной осей. Вертикальное перемещение стола выполняют вращением ручки 19, ограничивают винтом 14 и фиксируют винтом 18. Поперечное перемещение стола осуществляют вращением винта 13. В продольном направлении свободно перемещается только накладная верхняя часть стола, установленная на шариковых опорах. Вокруг вертикальной оси стол поворачивают ручкой 20. Покачивание относительно поперечной горизонтальной оси осуществляют эксцентриком 17. В установленном положении стол фиксируют винтом 15. Вертикальный штатив 10 служит для установки приспособлений, например упора при проверке серий изделий одинакового размера или электроконтактной головки ГК-3. Регулировочными винтами 16 устанавливают стойку в горизонтальное положение по уровню.
Перед измерением взаимное положение наконечников регулируют так, чтобы оси стержней пиноли и трубок находились на одной прямой. Для этого между наконечниками на столе устанавливают концевую меру размером 0.5…2 мм. Перемещая кронштейны 3 и пнноль 4, наконечники приводят в соприкосновение с поверхностями меры. Микровинтом 5 устанавливают шкалу оптиметра на некоторое показание. Регулировку выполняют винтами 8. расположенными под углом 90°, которые смещают стержень пиноли в радиальных направлениях.
Вращая отверткой поочередно винты 8, добиваются наибольшего показания оптиметра для сферических наконечников и наименьшего показания для плоских.
При установке оптиметра на нуль по блоку концевых мер длины линия измерения должна проходить перпендикулярно к измерительным граням мер. Предметный стол с блоком мер и кронштейны устанавливают в положение, при котором измерительные наконечники пиноли и трубки соприкасаются в срединной точке мер. Микровинтом 5 устанавливают шкалу прибора в положение около нулевой точки. Поочередными поворотами стола вокруг вертикальной оси ручкой 20 и покачиваниями стола эксцентриком 17 добиваются наименьшего показания оптиметра. Затем, вращая винт 5 пиноли, устанавливают шкалу на нулевое положение. Отводя наконечник трубки арретиром, проверяют правильность установки нулевого положения.
При измерении наружных размеров установку изделия в правильное положение по отношению к линии измерения осуществляют несколькими способами в зависимости от формы изделия.Измерение размеров плоскопараллельных изделий, например поверку концевых мер длины, выполняют так же, как установку оптиметра на нуль. Поворотами и наклонами стола добиваются наименьших показаний оптиметра, которые будут соответствовать отклонению от длины установочной меры. При этом линия измерения перпендикулярна к параллельным плоскостям изделия.
При измерении наружных диаметров цилиндрических изделий, например калибр-пробок, линия измерения должна пересекать ось изделия под прямым углом. Цилиндр следует устанавливать так, чтобы его ось была параллельна или вертикальна поверхности стола. В первом случае после установки оптиметра на нуль по блоку концевых мер измерительный наконечник трубки оптиметра отводят арретиром, меры снимают, стол опускают вниз и изделие закрепляют на столе в горизонтальном положении с помощью струбцины. Затем стол устанавливают в положение, при котором измерительные наконечники касаются цилиндра по диаметру. Для этого ручкой 19 (см. рис. 68) перемещают стол в вертикальном положении, добиваясь наибольших показаний по шкале оптиметра. При этом линия измерения должна пересекать ось изделия.
Затем поворотами стола ручкой 20 добиваются наименьших показаний оптиметра, при которых ось изделия перпендикулярна оси измерения. Так как предшествующая установка при этом может быть нарушена, измерения повторяют и продолжают до тех пор, пока наибольшее показание при перемещении стола не совпадает с наименьшим показанием при повороте. Если цилиндр ставят на стол так, что его ось перпендикулярна к плоскости стола, то стол перемещают в поперечном направлении перпендикулярно к оси измерения, вращая винт 13, и покачивают стол эксцентриком 17. Наибольшее показание при перемещении должно совпасть с наименьшим показанием при покачивании.
При измерении шариков линия измерения должна проходить через центр сферы. Стол перемещают в вертикальном и поперечном направлениях до тех пор, пока наибольшие показания оптиметра при этих операциях не совпадут.
Внутренние размеры изделий (калибр-колец, скоб и т. п.) на горизонтальном оптиметре измеряют с помощью приспособления ИП-3, которое состоит из двух почти одинаковых дуг 21 и 22, надеваемых на пиноль и трубку оптиметра (рис. 68, б). На стержни пиноли и грубки при этом устанавливают плоские наконечники. Дуга, которую надевают на трубку оптиметра (рис. 69), состоит из кронштейна 4 и серьги 1, представляющей собой П-образный рычаг с измерительным наконечником 13 на конце. Серьга крепится винтом 3 на оси 2. которая поворачивается на шарикоподшипниковых опо pax кронштейна 4. Кронштейн надевают на трубку 8 оптиметра до упора в резьбовое кольцо 10, положение
которого во втулке кронштейна фиксируется винтом 9. Пружина 6 через захват 7 прижимает шарик 12 серьги 1 к плоскому наконечнику 11 трубки. Отвод серьги осуществляют рычагом 5 арретира. Положение кронштейна на трубке проверяют установочным калибром 14. Калибр упирают во втулку кронштейна. Если показания оптиметра выходят за пределы мкм или изображение шкалы не перемещается в поле зрения, то освобождают стопорный винт 9 и, пользуясь обратной стороной установочного калибра 14 как торцовым ключом, регулируют положение резьбового кольца 10.
Перед измерением внутренних размеров оптиметр устанавливается на нуль по блоку концевых мер с притертыми боковиками или по аттестованному кольцу. Последовательность перемещений стола при установке на размер по блоку мер и измерении калибр-скоб такая же, как при измерениях наружных размеров изделий с плоскими поверхностями. При измерениях внутренних диаметров изделий и установке на нуль по кольцу стол перемещают так же, как при измерениях наружных цилиндров.
Оптические длиномеры
Оптические длиномеры предназначены для абсолютных и относительных измерений размеров изделий. Длиномеры выпускаются трех типов: ДВО—вертикальные окулярные, ДВЭ — вертикальные с проекционным экраном и ДГЭ — горизонтальные с экраном. Принцип действия длиномеров заключается в измерении перемещения образцовой линейной шкалы, установленной на одной оси с измерительным стержнем.
У вертикального окулярного длиномера ИЗВ-1 (тип ДВО) (рис. 70, о) миллиметровая стеклянная шкала 3 установлена в сквозном отверстии штока 2 с измерительным наконечником 1. Шток перемещается в корпусе прибора в шариковых направляющих 5. Он подвешен на гибкой стальной ленте, перекинутой через блоки 7 и 8 и прикрепленной на другом конце к противовесу 11, который перемещается в цилиндре 10, заполненном вазелиновым маслом. Это обеспечивает плавное опускание штока, исключающее возможность ударов и повреждения наконечника 1. Шток поднимают за тросик 9. Шкала 3 освещается лампочкой 12 через конденсор 13. Перемещение
шкалы относительно проверяемого изделия измеряют с помощью спирального отсчетного микроскопа 4 с ценой деления 0,001 мм. Длина шкалы равна 100 мм, что соответствует верхнему пределу абсолютных измерений.
Длиномер ИЗВ-1 (рис. 70, б) состоит из корпуса 7 и стойки CTI с предметным столом, имеющим ребристую _ поверхность. Стойка позволяет измерять размеры в пределах 100…250 мм методом сравнения с мерой. Корпус
перемещается по колонке гайкой 8 и крепится винтами 5. На корпусе установлены осветитель 6 и микроскоп 1 с окуляром 12. Шток 3 поднимают за кнопку 9 и фиксируют в любом положении гайкой 10. Измерительное усилие на штоке регулируется съемными грузовыми шайбами 4.
Спиральный микроскоп (рис. 71, а) состоит из объектива 5, который фокусирует изображение основной шкалы длиномера в плоскость между поворотной 3 и неподвижной 2 шкалами, и окуляра 1. Увеличение объектива составляет 5х, а увеличение окуляра—12,8х. Ручка 4 служит для вращения поворотной шкалы 3. Винтом 6 окуляр вместе с нониусом перемещается относительно объектива. На поворотную шкалу 2 нанесена двойная спираль Архимеда с расстоянием между нитями 0,012 мм и шагом спирали 0,1 мм, а также круговая шкала, имеющая 100 делений (рис. 71, б). За один оборот поворотной пластины любая точка спирали смещается для наблюдателя на 0,1 мм по радиусу в направлении от центра, а круговая шкала поворачивается от 0-го до 100-го деления. На неподвижную шкалу нанесены два параллельных штриха, равномерная шкала с диапазоном показаний 1 мм и ценой деления 0,1 мм и указатель. В окуляр видны длинные штрихи основной миллиметровой шкалы и спиральный нониус. Для отсче та ручку 4 вращают до тех пор, пока длинный штрих миллиметровой шкалы не окажется между нитями спирали. Цифра около этого штриха показывает число миллиметров в размере (46 мм). Десятые доли миллиметра отсчитывают по линейной окулярной шкале относительно длинного штриха (0,3 мм). Сотые и тысячные доли миллиметра показывает на круговой шкале неподвижный указатель (0,072 мм). Отсчет по шкале микроскопа равен 46,372 мм.
Перед измерением длиномер (см. рис. 70, б) устанавливают на нуль. При освобожденном стопоре 10 шток прибора опускается до соприкосновения с поверхностью измерительного стола или с поверхностью концевой меры длиной 100 или 150 мм, притертой к столу. Вращая ручку 11 отсчетного микроскопа, круговую шкалу переводят в положение 00 относительно указателя (см. рис. 71, б). При этом все штрихи окулярной шкалы (короткие штрихи) расположатся между нитями двойной спирали. При правильной установке нулевой штрих
или штрих 100 мм (при настройке по концевой мере) также должны лежать между нитями спирали. Если последние условия не выполнены, то винтом 2 (см. рис. 70, б) смещают окуляр микроскопа в нужное положение. При измерениях за кнопку 9 поднимают шток и устанавливают изделие на стол, затем шток под действием силы тяжести опускается на поверхность изделия, после этого осуществляют отсчет показаний.
Горизонтальный длиномер ИКУ-2 (тип ДГЭ) основан на сочетании принципов действия вертикальных длиномеров и оптиметра. Свет от лампы 1 (рис. 72, а) через осветительную систему 2 направляется зеркалами 9 и 4 и призмой 5 на линзу 6 и освещает стеклянную миллиметровую шкалу 3. Изображение шкалы проецируется объективом 8 через призму 10 в плоскость неподвижной биссекторной шкалы 11 с ценой деления 0,1 мм. Шкала 11 вместе со штрихом основной шкалы через призму 12 проецируется объективом 13 через зеркала 14 и 25 на экран 7. Осветительная система 26 через призму 18 освещает сетку 19, которая имеет шкалу с ценой деления 0,001 мм на одной половине. Оптическая система, состоящая из призм 20, 21, 23 и объектива 22, который расположен в фокальной плоскости сетки 19, и зеркала 24, связанного с измерительным стержнем прибора, создает автоколлимационное изображение шкалы на другой половине окулярной сетки 19, на которую нанесен отсчетный индекс. Изображение шкалы и индекс проецируется объективом 17, зеркалами 16 и 25 на экран 7. С помощью вспомогательной линзы 15 регулируется правильная установка лампы.
Горизонтальный длнномер (рис. 72,6) имеет станину 1, измерительную 10 и пинольную 2 бабки и предметный стол 7. Измерительная пиноль 8, в которой расположены основная шкала, измерительный стержень н зеркало оптиметра, грубо перемещается маховиком 11, тонко — мнкровинтом 12 и стопорится винтом 13. Пинольную бабку перемещают маховиком 4 и стопорят винтом 3. Тонкую подачу наконечника 6 пиноли осуществляют мнкровинтом 5. Предметный стол 7 в вертикальном направлении перемещается маховиком 17, в поперечном направлении — винтом 14. Верхняя часть стола свободно перемещается на шариках в продольном направлении. Стол поворачивают вокруг вертикальной оси маховиком 15, а вокруг поперечной горизонтальной оси — маховиком 16.
При абсолютных измерениях прибор устанавливают на нуль, сведя измерительные наконечники до соприкосновения и регулируя их соосность так же, как на горизонтальном оптиметре. Винтом 12 устанавливают на нуль верхнюю шкалу экрана 9, а затем винтом 5 — нижнюю шкалу экрана. При измерении измерительную пиноль отводят, на столе закрепляют изделие и затем перемещают измерительную пиноль до тех пор, пока показания на нижней шкале экрана 9 не станут близкими к нулю. Микровинтом 12 совмещают штрих основной шкалы с ближайшим биссектором — двойным штрихом отсчетной шкалы с ценой деления 0,1 мм. Затем предметный стол перемещают в зависимости от вида изделия так же, как при измерениях на оптиметре. По верхней шкале экрана отсчитывают целые и десятые доли миллиметра, а по нижней шкале — сотые и тысячные. Отсчет на экране длиномера составляет 4,572 мм (см. рис. 72, а). Относительные измерения выполняют так же, как на оптиметре. Показания длиномера (верхняя шкала) не учитывают.
Оптико-механические машины для измерения длины
Оптико-механические машины ИЗМ имеют цену деления 0,001 мм и пределы измерений 0…1 м (ИЗМ-1), 0…2 м (ИЗМ-2) и 0…4 м (ИЗМ-4). Они предназначены для абсолютных и относительных измерений нутромеров, концевых мер длины, калибр-пробок, скоб, колец и других инструментов и точных изделий больших размеров.
Принцип действия измерительных машин заключает-:я в следующем. Вдоль станины 1 (рис. 73, а) в окнах размещены образцовые оптические шкалы — метровая и лиллиметровая. Метровая шкала представляет собой >асположенные через 100 мм стеклянные пластины 6, на <оторые нанесены двойные штрихи (биссекторы) и цифры, показывающие число дециметров. Миллиметровая стеклянная шкала 10 имеет интервал делений 0,1 мм и диапазон показаний 100 мм. Вдоль станины над метровой шкалой перемещается пинольная бабка 5 с осветителем, над миллиметровой шкалой — измерительная бабка 7. Свет от лампы 2 через конденсор 3 и зеркало 4 освещает одну из пластин б, которая расположена в фокальной плоскости объектива 13. Призмы 11 и 14 отклоняют ход световых лучей на 90°. Объектив 13 направляет световой поток с изображением биссектора в измерительную бабку 7. Объектив 12 фокусирует изображение на шкалу 10, которую наблюдают в микроскоп 9. Для отсчета сотых и тысячных долей миллиметра служит шкала трубки оптиметра с окуляром 8.
Перед абсолютными измерениями машину (рис. 73, б) устанавливают на нуль. Пинольную бабку
перемещают маховиком 13 и закрепляют над крайней правой пластиной, соответствующей нулю дециметров. Измерительную бабку 8 сначала грубым маховиком 9, а затем микровинтом И перемещают так, чтобы изображение биссектора приходилось на нулевое деление шкалы (см. рис. 73, в). При этом наконечники пиноли 3 и трубки оптиметра 6 соприкасаются. Измерительные стержни устанавливают на одной оси (центрируют) так же, как у оптиметров. Затем, вращая микровинт 2 пи-нольной трубки, устанавливают на нуль оптиметр.
При измерениях пинольную бабку устанавливают ориентировочно по вспомогательной металлической линейке 12 с дециметровыми делениями на требуемый размер. Измерительную бабку отодвигают вправо и устанавливают изделие на предметный стол или на люнеты 4 и 5, которые используют при измерениях длинных цилиндрических изделий диаметром до 50 мм. Затем измерительную бабку, пользуясь для ориентации металлической линейкой 10, перемещают маховиком 9 до соприкосновения наконечников пиноли и оптиметра с изделием. Показание оптиметра не должно выйти за пределы шкалы. Если изделие закреплено на предметном столе, то поверхности изделия устанавливают перпендикулярно к линии измерения путем перемещений стола, как у горизонтального оптиметра (см. § 44). Затем измерительную бабку, наблюдая в окуляр микроскопа 7, перемещают микровинтом 11 до совмещения биссектора с ближайшим штрихом миллиметровой шкалы и проводят отсчет целых и десятых долей миллиметра. Отсчет десятых долей миллиметра в размере ведут по штриху миллиметровой шкалы, расположенному между биссектором. По шкале оптиметра отсчитывают сотые и десятые доли миллиметра. Положительные показания оптиметра суммируют с отсчетом микроскопа, а отрицательные вычитают. Отсчет по шкалам измерительной машины (рис. 73, г) составляет мм.
Относительные измерения размеров на машинах проводят так же, как на горизонтальном оптиметре. Оптическую систему машины при этом не используют. Измерительные машины комплектуют разнообразными приспособлениями, которые позволяют измерять наружные и внутренние размеры различных изделий, например приспособления с дугами.
Возможно эта страница вам будет полезна:
Инструментальные и универсальные микроскопы
Измерительные микроскопы предназначены для линейных и угловых измерений разнообразных изделий в прямоугольных и полярных координатах. На микроскопах измеряют наружные линейные размеры изделий, диаметры валов и отверстий, углы режущего инструмента и шаблонов, основные элементы профиля резьбовых инструментов и калибров, радиусы закруглений профилей
размеры конусов, расстояние между центрами отверстий и т. п. В машиностроении наиболее распространены малый (ММИ) и большой (БМИ) инструментальные микроскопы и универсальные микроскопы УИМ-21, УИМ-23 и УИМ-24. Они имеют один принцип измерений и различаются конструкцией, диапазоном измерений и областью применения.
Оптическая схема микроскопа приведена на рис. 74. Осветитель, состоящий из лампы 16, сменного конденсора 15, зеленого светофильтра 14 и ирисовой диафрагмы 13, освещает через зеркало 12 и объектив 11 изделие 9, установленное иа предметном стекле 10. Сменный объектив 8 визирного микроскопа М проецирует теневой контур изделия в фокальную плоскость окуляра 1 угломерной головки, в которой расположена поворотная сетка 2. Стекла 6 предохраняют объектив от грязи и повреждений при замене окулярной головки ОГ. Оборачивающая призма 7 позволяет наблюдать в окуляр прямое изображение контура изделия. Угол поворота окулярной сетки 2 измеряют по жестко закрепленной на сетке 2
угловой круговой шкале — лимбу 4 с ценой деления 1°. Лимб наблюдают в окуляр 3 микроскопа с значением отсчета. Зеркало 5 подсвечивает лимб от внешнего источника света или осветительного приспособления.
На поворотную окулярную сетку угломерной головки (рис. 75) нанесены две сплошные линии под углом 60° одна к другой, штриховое перекрестие и четыре параллельные линии, отстоящие от центра на расстоянии 0,3 и 0,9 мм. На их фоне виден теневой контур изделия. Окуляр микроскопа имеет градусную шкалу 2 и минутную шкалу 3. Отсчет на рис. 75 составляет 30°25′.
При измерениях теневой контур граней изделия, ограничивающих проверяемый размер , совмещают со штрихами окулярной головки путем перемещений стола с предметным стеклом и поворота окулярной сетки. Значения перемещений определяют по отсчетным устройствам.
Малый и большой инструментальные микроскопы (рис. 76) имеют массивное основание 1, внутри которого смонтированы узлы оптической системы, а на задней стороне расположен осветитель 16. Осветитель имеет накатное кольцо для регулирования диафрагмы, правильный выбор которой повышает точность измерений. На основании установлены салазки 3 с предметным столом 4, имеющим сквозное отверстие, закрытое стеклом. Микрометрические головки 2 и 18 с ценой делений 5 мкм и пределами измерений 0…25 мм перемещают салазки в продольном и поперечном направлениях. Для расширения диапазона измерений между торцами микровинтов и опорными площадками салазок устанавливают концевые меры длины. Салазки прижимаются к микровинтам пружинами. Поворот стола вокруг вертикальной оси осуществляют маховиком 19. У ММИ угол поворота стола составляет
Углы поворота стола БМИ в пределах 0…3600 отсчитывают по лимбу 20 с нониусом. Винт 21 зажимает стол в нужном положении. При измерениях стол поворачивают так, чтобы линия его перемещений совпадала с линией измерений. На основании установлена опора 15 с колонкой 14. Колонка поворачивается на угол в пределах от вертикали маховиком 17, который имеет угломерную шкалу с ценой деления 3(У. Кронштейн 11 с тубусом 6 визирного микроскопа перемещается на колонке маховиком 12 и зажимается винтом 13. На тубусе закреплена угломерная головка 7 с окуляром 9, в который наблюдают изделие, установленное на столе. Окулярную сетку наводят на контур изделия поворотом кольца 10. Угол поворота окулярной сетки наблюдают в окуляр 8 микроскопа. Резкость изображения теневого контура регулируют поворотом кольца 5.
Пределы измерений ММИ составляют 0…75 мм в продольном и 0…25 мм в поперечном направлениях, а пределы измерений БМИ соответственно 0…150 мм и 0…50 мм. На инструментальных микроскопах измерения осуществляются с помощью комплекта принадлежностей, в который входят сменные объективы с увеличением 1…5, призматические стойки, центровые бабки, V-образ-ные подставки, призмы, прижимы и струбцины для крепления изделий на столе, концевые меры длиной 25, 50, 75 и 100 мм, контрольный валик для выставления оси изделия вдоль линии измерения, осветительное устройство для измерений в отраженном свете. Могут поставляться также револьверная головка с дугами различной кривизны и набором профилей резьбы, приспособление для фотографирования, проекционная насадка с экраном, комплект измерительных ножей с приспособлением для их крепления и т. п.
Универсальный микроскоп УИМ-21 (рис. 77) имеет станину 1, продольную 3 и поперечную 13 каретки. На продольной каретке закрепляются специальные предметные столы, центровые бабки 12 и другие принадлежности для установки изделий. На поперечной каретке смонтированы осветительная система и колонка 8, на кронштейне которой закреплен главный микроскоп 9 с угломерной окулярной головкой. Маховик 10 служит для наклона головки, маховик 11 — для регулирования диафрагмы осветителя. Каретки перемещаются микровинтами 4 и 15. Перемещения измеряют по стеклянным миллиметровым шкалам 5, укрепленным на каретках, с помощью неподвижных отсчетных микроскопов 6 и 7 ценой деления 1 мкм. Каждый микроскоп снабжен малым осветителем. Пределы измерений составляют 0…200 мм в продольном и 0…100 мм в поперечном направлениях. Порядок отсчета по микроскопам рассмотрен в § 45. Каретки можно передвигать вручную при ослабленных стопорных винтах 2 и 14.
Универсальный микроскоп УИМ-23 (рис. 78, а) в отличие от рассмотренных выше микроскопов имеет от-счетные устройства проекционного типа. Внутри основания / размещено большинство деталей оптической системы, а снаружи установлены на точных направляющих продольная 3 и поперечная 2 каретки. Продольная каретка имеет цилиндрическое ложе, в которое могут быть
установлены центровые бабки 4, служащие для закрепления цилиндрических деталей. На опорных плоскостях этой каретки могут быть закреплены приспособления, плоский и круглый стол, планки для измерительных ножей и др. На поперечной каретке расположены колонка 5 и осветительное устройство (внутри). Шкалы визирного микроскопа 6, который наводится на измеряемое изделие, проецируются на экран 7. На каждой каретке жестко закреплена стеклянная шкала, но которой измеряют перемещения изделия в продольном или поперечном направлениях. Изображение штрихов стеклянных шкал вместе со шкалами отсчетных устройств проецируется на экран 8. По миллиметровому штриху, расположенному между двойным штрихом линейной шкалы, находят целые и десятые доли миллиметра, а по индексу на подвижной круговой шкале — сотые н тысячные доли. Отсчеты по шкалам микроскопа составляют для поперечной каретки 93,030 мм, для продольной каретки 192,661 мм.
Универсальные микроскопы отличаются от инструментальных более широким диапазоном и большей точностью измерений. УИМ-24 имеет подъемное устройство для детален массой до 100 кг; диапазон измерений в продольном направлении составляет 0…500 мм, а в поперечном — 0…200 мм; цена деления отсчетных устройств проекционного типа равна 1 мкм. Универсальность обеспечивается разнообразными принадлежностями, в комплект которых входят круглый предметный стол СТ9, стол с высокими центрами СТ-2, измерительная бабка ИБ-21 и др.
Измерения на микроскопах можно проводить теневым методом в проходящем свете, контурным методом в отраженном свете и методом осевого сечения с помощью измерительных ножей. В отраженном свете с помощью съемного осветителя измеряют размеры изделий, которые перекрываются выступающими частями от проходящего света. При измерениях плоские изделия закрепляют на предметном столе, а цилиндрические изделия— в центровых бабках, на призмах и других приспособлениях. Перед измерением плоских изделий диафрагму . осветителя устанавливают на диаметр 20…25 мм. При измерении цилиндрических изделий диаметр диафрагмы выбирают по специальной таблице. Объектив наводят на плоскость, в которой выполняют измерения. Положение изделия регулируют так, чтобы измеряемый размер наблюдался в окулярную головку, а направление размера совпадало с направлением перемещения стола. Для цилиндрических (гладких и резьбовых) изделий фокусировку объектива и выверку направления оси изделия осуществляют по контрольному валику, установленному в центрах.
Процесс измерений заключается в совмещении штриховых линий окулярной сетки с линиями контура изделия, ограничивающими проверяемый размер. Точность совмещения штриховых линий значительно выше, чем сплошных. При совмещении одна половина линии должна находиться в пределах теневого контура, а другая — вне его. При линейных измерениях, например диаметра калибра-пробки, совмещения добиваются путем последовательных перемещений стола в поперечном или продольном направлениях. Измеряемая длина равна разности показаний микрометрических устройств или отсчетных микроскопов при двух совмещениях с каждой стороны размера. При угловых измерениях совмещение обеспечивается поворотом окулярной головки визирного микроскопа и перемещениями стола (см. рис. 75). Например, линейные и угловые измерения на микроскопах выполняются при проверке основных размеров резьбы (см. §67).
Для проверки резьбовых, радиусных и других профилей на микроскопах применяют револьверные головки, окулярные сетки которых показаны на рис. 79. Совмещая
контур изделия с соответствующим профилем на окулярной сетке, можно проверить правильность параметров резьбы 1 или радиус кривизны изделия 2.
На микроскопах измеряют плоские изделия, например шаблоны со сложным контуром, размеры которых на чертеже задаются в виде координат, отсчитываемых от какой-либо точки. Такие измерения проводят в прямоугольных или полярных координатах. При измерениях в прямоугольных координатах изделие ОАВС устанавливают базовыми сторонами OA и ОС параллельно направлениям перемещения стола (рис. 80. а). Точку О совмещают с центром перекрестия окулярной сетки и записывают показание отсчетных устройств. Перемещая стол, совмещают перекрестие с точками 1, 2, 3,… профиля
По разности показаний отсчетных устройств определяют действительные размеры профиля:
Полученные значения координат сравнивают с заданными на чертеже. При измерениях в полярных координатах (рис. 80, б) изделие ОАВ устанавливают так, чтобы исходная точка О совпала с центром стола и перекрестием окулярной сетки. Стол поворачивают на углы
таким образом, чтобы направления линий
совпадали с продольным перемещением стола. По разности показаний микрометра определяют длину радиусов
Полученные значения координат
сравнивают с заданными.
Проекторы
Измерительные проекторы предназначены для измерений и контроля линейных и угловых размеров изделий со сложным контуром: профильных шаблонов, мелкомодульных зубчатых колес, режущего инструмента, резьбовых изделий и т. п. Проекторы позволяют получать на экране увеличенное изображение контура изделия при измерениях в проходящем свете (диаскопическая проекция) или изображение поверхности изделия при измерениях в отраженном свете (эпископическая проекция). Второй метод менее точен, его применяют, например, когда необходимо измерить размер на поверхности изделия.
Большой проектор БП имеет осветительную и проекционную оптические системы (рис. 81, а). Осветитель состоит из лампы /, конденсора 2, светофильтра 3, сменного конденсора 4 и зеркала 5. Параллельные лучи освещают измеряемое изделие 7, установленное на предметном стекле 6. Теневой контур изделия отражается от зеркала 8 и проецируется объективом 9 через призму 10 и зеркало 11 на экран 12. Увеличение сменных объективов 9 составляет 10, 20 и 50х. Каждому объективу соответствует свой сменный конденсор 4, обеспечивающий равномерное освещение объектива.
При измерениях в отраженном свете вместо зеркала 8 используют полупрозрачное стекло. Лучи света проходят через стекло, отражаются от поверхности изделия 7 и поверхности полупрозрачного стекла и попадают в объектив 9. Изображение на экране получается менее четкое.
Проектор БП (рис. 81,6) имеет станину 1 со стойкой 3, внутри которой штурвалом 5 при освобожденном стопоре 4 перемещается вертикальная колонка 2. На колонке установлено основание 6 измерительного стола 8 с осветителем 7. На средней части станины имеется патрубок, в котором крепятся объективы 9 и револьверное устройство 10 со сменными зеркалами П. В верхней части станины на кронштейне установлено зеркало 12 н предусмотрена драпировка 13 для затемнения экрана 14. Диаметр экрана равен 600 мм. Конструкция и основные метрологические показатели отсчетных устройств измерительного стола проектора такие же, как у микроскопа БМИ.
Осветитель 7 проектора можно установить так, чтобы изделие освещалось сбоку горизонтальными потоками света, которые направляются непосредственно в объектив 9. Револьверное устройство при этом поворачивают на 90° и открывают объектив. При измерениях в отраженном свете осветитель 7 устанавливают вертикально над револьверным устройством, в котором зеркало заменяют полупрозрачным зеркалом, пропускающим свет на поверхность изделия. Лучи, отраженные полупрозрачным зеркалом от изделия, направляются в объектив 9.
Фокусировку объектива 9 на изделие перед измерением осуществляют вертикальными перемещениями стола штурвалом 5. Резкость изображения теневого контура
изделия на экране регулируют, изменяя диаметр диафрагмы конденсора 4. Для измерения длины и углов изделий на экран 14 нанесены штриховые перекрестия, направление линий которого совпадает с направлением перемещений стола, и две сплошные линии, проходящие через центр перекрестия под углом одна к другой.
Часовой проектор типа ЧП используют для контроля и измерений мелких изделий Лампа 1 (рис. 82, а) через конденсор 2 со светофильтром 3 освещает изделие, установленное на предметном столе 4. Объектив 5 с защитным стеклом 6 через зеркало 7 проецирует теневой контур изделия на экран 8. При работе в отраженном свете изделие освещается снизу через предметное стекло специальным осветителем. На корпусе 1 проектора (рис. 82, б) установлены сменный объектив 3 и стойка 10, на которой закреплены осветитель 7 и перемещающийся измерительный стол 5 с предметным стеклом. Стол имеет продольный 11 и поперечный 4 микровинты. Маховик 8 перемещает стол вертикально при фокусировании
вании объектива. Сменные конденсоры 6 установлены на поворотном револьверном устройстве 9, они имеют увеличение 10, 20, 50, 100 и Размеры экрана 2 составляют
мм.
Для контроля и измерения изделий на проекторах используют следующие методы: 1) совмещение проецируемого контура с номинальным контуром изделия, выполненным в масштабе, соответствующем увеличению объектива; 2) сравнение изображения с чертежом, на который нанесены два контура изделия, соответствующие его предельным размерам; профиль годного изделия должен лежать между его предельными контурами; 3) измерение размеров контура изделия с помощью микрометрических устройств измерительного стола; 4) измерение отклонений изображения контура от образцового профиля с помощью измерительного стола или масштабной линейки.
Чертеж изделия изготовляют на ватмане, кальке, целлофане, плексигласе и укрепляют на экране. Увеличение объектива следует выбирать так, чтобы можно было наблюдать весь измеряемый размер. Процесс измерений на проекторах аналогичен измерениям на микроскопах.
Проекторы массового контроля ПМК изделий основаны на методе совмещения. Лучи света от лампы 1 (рис. 83, а) через конденсор 2 освещают изделие АВ. Объектив 3 проецирует теневой контур через зеркала 4 и 5 на экран 6, расположенный над объективом. Если поверхность зеркал перпендикулярна к оси объектива, то на экран проецируется теневой контур изделия и экран затемнен. По образцовому изделию угол поворота зеркал выбирают таким образом, чтобы линии контура А’ и В’ сошлись на одной линии К экрана. При этом экран освещается равиомерно полутенью: одна половина экрана освещена зеркалом 4, а другая — зеркалом 5. При замене образца проверяемым изделием СД большого размера на экране появится темная полоса К1К.2. Соответственно, если размер изделия меньше образца, то на экране появляется светлая полоса за счет наложения световых потоков от двух зеркал. Ширина затемненных и освещенных полос на экране
где
— отклонение размера изделия образца; Г—увеличение проектора. Для контроля используют две пары зеркал, первую из которых настраивают по наименьшему предельному размеру изделия, вторую—по наибольшему. Светлая полоса для первой пары зеркал и темная полоса для второй пары свидетельствуют о браке.
Проектор (рис. 83, б) состоит из корпуса 1, предметного стола 2, осветителя 4, объектива 3 и экрана 5 с козырьком. Внутри корпуса у задней стенки установлены две вертикальные штанги, по которым могут перемещаться и фиксироваться в нужном положении держатели зеркал. На проекторе можно одновременно контролировать до пяти размеров Для каждого размера используются две пары зеркал. Зеркала можно поворачивать вокруг горизонтальной оси для сближения отдельных изображений на экране и вокруг вертикальной оси — для настройки по размеру.
Пневматические длиномеры
Принцип действия и классификация
Пневматические измерения длины могут выполняться бесконтактным и контактным методами. По первому методу (рис. 84, а) воздух под постоянным давлением РI проходит через входное сопло 1 в камеру 2, из которой выходит через измерительное сопло 3. Давление Р и расход воздуха Q в камере зависят от расстояния 5 между соплом 3 и поверхностью детали 4 значение 5 определяется отклонениями размера детали и может быть измерено расходомером или манометром, градуированными в единицах длины. При измерениях контактным методом (рис. 84, б) прибор реагирует на изменение расстояния между соплом 1 и заслонкой 2, соединенной с измерительным наконечником 3. Погрешности пневматических измерений зависят от чистоты сжатого воздуха и колебаний его давления, конструкции измерительных сопел и изделий. Поэтому воздух тщательно фильтруют, а его давление поддерживают строго постоянным. Для измерений используют специальные насадки — сопла, пробки, установочные кольца, контактные головки и т. п.
Пневматические длиномеры различают низкого и высокого давления, по измерительному механизму — манометрические и ротаметрические, по методу измерений — дифференциальные и недифференциальные. Они имеют следующие преимущества: 1) высокую точность измерений (до 0,1 мкм); 2) возможность бесконтактных измерений; 3) удобство измерений в труднодоступных местах; 4) осуществимость одновременного контроля нескольких размеров и др.
Длиномеры низкого давления
В пневматических длиномерах низкого давления чувствительным элементом является водяной манометр. Воздух через вентиль 1 (рис. 85) поступает в прибор, затем через фильтр 2 и предварительный стабилизатор давления 3 проходит в камеру 6 и далее через входные сопла 7 и рабочую камеру 8 направляется к измерительной оснастке, например соплу 10. Избыток воздуха из камеры 6 выходит в атмосферу через трубку 5, которая погружена на глубину 500 мм в воду, заполняющую корпус 4, поэтому давление в камере 6 строго постоянно и равно 5 кПа. Давление в камере 8 определяется по уровню воды в манометрической трубке 9, соединенной с корпусом 4. По постоянной миллиметровой шкале 13 проверяют заполнение прибора водой. Сменная шкала 12 служит для измерения отклонений измеряемого размера изделия 11.
Длиномеры изготовляют с числом манометрических трубок 1…7. Цена деления шкалы 12 изменяется в пределах 0.5…20 мкм. Диапазон измерений в зависимости от оснастки составляет 0,02…0,63 мм. Предел основной допускаемой погрешности приблизительно равен цене деления шкалы.
Длиномеры высокого давления
В пневматическом длиномере высокого давления ротаметрического типа (рис. 86) воздух после блока 1 фильтра со стабилизатором давления разделяется на два потока. Один поток проходит через ротаметр 2, другой — через вентиль 7 параллельного пропуска воздуха. Ротаметр представляет собой коническую стеклянную трубку, в которой находится поплавок. После ротаметра воздух проходит дроссель 3, соединяется с потоком от вентиля 7 и поступает к измерительной оснастке (например, пневматической пробке 5) и к вентилю 6 для выпуска воздуха в атмосферу. Дроссель 3 и вентиль 6 расположены в корпусе прибора. Положение поплавка в трубке ротаметра зависит от расхода воздуха, который изменяется пропорционально расстоянию S между измерительной оснасткой и изделием. По шкале 4 ротаметра измеряется отклонение размеров изделия. Цена деления шкалы измеряется в пределах 0.2…10 мкм, диапазон показаний 0,01…0,16 мм. Предел основной допускаемой погрешности зависит от цены деления шкалы и типа оснастки и составляет
Длиномер высокого давления манометрического типа с оптико-рычажным механизмом (рис. 87) предназначен для дифференциальных измерений. Очищенный и стабилизированный воздух после блока 15 проходит входные сопла 14 и выходит в атмосферу через измерительные сопла 12, установленные перед деталями 11. Одно из сопел устанавливается перед образцовым
изделием. Его можно заменить вентилем 10 противодавления. Разность давлений перед соплами 12. которая зависит от разности зазоров 5, и Si, воспринимается силь-фонамн 13, внутренние концы которых закреплены неподвижно на сухаре 9, а подвижные концы жестко связаны с рамкой 7. Ход рамки зависит от разности давлений в сильфонах; он ограничен упорами 8. Рамка 7 контактирует с шариком качающегося рычага 6, на котором закреплено зеркало 4. Световой указатель из осветителя 5 отражается от качающегося зеркала 4 и от зеркал 2 н 3, увеличивающих оптический рычаг, и падает на шкалу 1. Значения перемещений указателя зависят от хода рамки 7, они пропорциональны разности зазоров перед измерительными соплами. Цена деления шкалы прибора составляет 0,1…0,5 мкм, диапазон показаний — 10…50 мкм, а допускаемая погрешность — 0,1.. 0,8 мкм.
Методы и средства поверки плоскопараллельных концевых мер длины и мер плоского угла
При эксплуатации, хранении и ремонте поверка мер включает следующие операции: внешний осмотр, проверку притираемости измерительных поверхностей, определение их отклонений от плоскостности, определение отклонения длины или рабочего угла мер от номинального значения. Притираемость мер к вспомогательным стеклянным пластинам определяют по наличию интерференционных пятен и их цвету, а притираемость мер между собой — по усилению сдвига.
Основные методы поверки размеров плоскопараллельных концевых мер: абсолютный интерференционный, относительный интерференционный, технический интерференционный и относительный контактный на интерферометрах, измерительных машинах, оптиметрах, оптикаторах и микрокаторах. Основные методы поверки угловых мер: автоколлимацнонный, гониометрический и относительный контактный.
Перед поверкой меры промывают авиационным бензином и протирают чистой салфеткой. Уложив на специальный стол, меру выдерживают на рабочем месте не менее 5 ч. При поверке необходимо строго соблюдать нормальные условия в помещении. Результаты поверки мер, признанных годными, оформляют путем выдачи свидетельств установленной формы.
Основы интерференционных методов измерений
Свет распространяется в виде электромагнитных волн, поэтому параметры света, например освещенность, в каждой точке пространства непрерывно изменяются. Интерференция света — сложение когерентных световых потоков, при котором происходит усиление или ослабление суммарного светового потока. Когерентными называют волны, сохраняющие постоянную разность
фаз при взаимодействии. В технике, как правило, когерентные световые потоки получают путем разложения света, идущего от одного источника, на отдельные лучи.
Волны, которые в точке встречи имеют разность фаз Дф, кратную четному значению числа (числу полуволн), совпадают по фазе:
любое целое число. Амплитуды таких волн складываются (рис. 88, а) и происходит усиление освещенности. Если волны колеблются в разных фазах (рис. 88, б), т. е.
то они взаимно гасятся, и освещенность уменьшается.
Разность фаз световых волн в точке встречи связана с оптической разностью хода световых лучей и длиной
световых волн соотношением Аф = 2nAL/X. Поэтому усиление освещенности происходит в точках пространства, в которых оптическая разность хода когерентных световых волн равна четному числу полуволн:
Ослабление освещенности происходит в точках пространства, в которых оптическая разность хода равна нечетному числу полуволн:
Интерференционная картина возникает при наложении плоской стеклянной пластины 1 на зеркальную поверхность 2 под углом а, близким к нулю (рис. 89,а). Луч света I делится на нижней грани пластины на два луча. Отраженный луч II выходит из пластины, а преломленный луч III проходит воздушный зазор, отражается от поверхности и снова проходит стеклянную пластину. После выхода из пластины лучи II и III интерферируют. Интерференционную картину можно наблюдать визуально или через окуляр.
Лучи И и III проходят в пластине одинаковый путь. Оптическая разность хода лучей в воздухе При углах, близких к нулю,
На границе более плотной оптической среды с менее плотной оптической средой при отражении происходит сдвиг оптической разности хода на длину световой полуволны
поэтому для лучей II и III полная разность хода
Таким образом, оптическая разность хода лучей изменяется вдоль пластины.
При высоте воздушного зазора, равной целому числу полуволн, и т. д., разность оптического хода лучей составит нечетное число полуволн:
и т. д. и на пластине будут наблюдаться темные интерференционные полосы 0, 1, 2. 3, … (рис. 89,6). При высоте воздушного зазора
и т. д., разность оптического хода составит четное число полуволн
и на пластине будут наблюдаться светлые полосы. Первую темную полосу, совпадающую с ребром воздушного клина, принято называть нулевой полосой, а последующие — первой, второй и т. д.
Интерференционные методы линейных измерений основаны на том, что зазор между пластиной и отражающей поверхностью можно определить как произведение длины полуволны света на номер полосы.
При интерференционных измерениях используют белый (сложный) или монохроматический свет. При освещении белым светом интерференционная картина по мере удаления от ребра клина расплывается: темные полосы светлеют, а светлые (радужной окраски) теряют яркость. Практически измерения в белом свете можно проводить только до б-й или 7-й полосы. Наибольшая высота измеряемого воздушного зазора составит мкм, где
мкм — длина волны белого света.
Ширина интерференционных полос (см. рис.89,б)— расстояние между серединами двух соседних полос — зависит от длины световой волны
и угла клина
:
По ширине полос определяют угол между накладываемыми поверхностями. На этом основаны интерференционные методы контроля плоскостности поверхностей.
Монохроматический свет при технических измерениях получают, пропуская белый свет через светофильтр. Светлые полосы имеют цвет фильтра, а темные — совершенно черные. Четкость интерференционной картины сохраняется для большего числа полос, поэтому размер измеряемого зазора может быть больше 2 мкм.
Плоские стеклянные пластины
Плоские стеклянные пластины применяются для интерференционных измерений плоскостности и притирае-мости поверхностей размером до 120 мм. Пластины выпускают двух типов: 1) нижние пластины (рис. 90, а) для притирания концевых мер длины при измерениях
интерференционными методами, а также для поверки притираемости и плоскостности поверхностей концевых мер длины и угловых мер; 2) верхние пластины (рис. 90,6) для измерения концевых мер длины техническим интерференционным методом.
Нижние пластины выпускаются четырех типоразмеров и классов точности 1 и 2 (табл. 9). Верхние пластины имеют скос под углом 10…12° от ребра АВ; их выпускают одного типоразмера. На рабочую поверхность верхних пластин, имеющую допускаемую плоскостность не более 0,3 интерференционной полосы, нанесены две тонкие линии CD и EF перекрестия.
Поверка притираемости и плоскостности мер
При поверке притираемости стеклянную пластину притирают к измерительной поверхности меры и наблюдают интерференционную картину. На поверхности концевых мер длины и угловых мер 1-го и 2-го разряда, а также мер классов точности 00 и 0 не должно наблюдаться интерференционных полос и цветовых оттенков. У концевых мер длины 3-го и 4-го разряда и классов точности 1, 2 и 3, а также у угловых мер 3-го разряда и класса точности 2 допускается появление на поверхности оттенков в виде светлых пятен. У концевых мер длины 5-го разряда н классов точности 2 допускаются оттенки желтого цвета в рабочей зоне измерительной поверхности.
Сила сдвига концевых мер длины, отвечающая требованиям по притираемости, составляет 29,4…78,5 Н. Количественный критерий притираемости угловых мер заключается в том. что угловая мера типа II с углом (см. рис. 9), притертая к поверяемой мере, не должна отрываться под действием собственного веса при горизонтальном положении мер.
Отклонение от плоскостности измерительных поверхностей концевых мер длины 3-го, 4-го и 5-го разрядов и угловых мер (кроме многогранных призм) определяют с помощью нижних стеклянных пластин. Пластину накладывают на ребро меры под углом, обеспечивающим появление интерференционной картины на поверхности меры. По характеру искривления интерференционных полос судят о плоскостности поверхности. При идеально плоской поверхности полосы будут прямыми (рис. 91,а), так как высота воздушного клина в сечениях, параллельных сечению, постоянна. Если поверхность выпуклая (рис. 91,6), то высота воздушного клина, равная по краям лежит ближе к ребру меры, чем сечение, и полосы будут изогнутыми к ребру клина. Отклонение от плоскостности
можно определить по отношению отклонения
концов линий от серединных точек к ширине полосы
Для выпуклой поверхности (рис. 91, б) и
мкм. Для вогнутой поверхности (рис. 91, в) полосы будут изогнуты от ребра клина:
и
мкм.
Плоскостность мер поверяют в продольном и поперечном направлениях. Найденные отклонения сравнивают с допускаемыми по ГОСТ 9038—83 для концевых мер и по ГОСТ 2875—75 для угловых мер. Отклонение от плоскостности концевых мер длины 1-го и 2-го разряда и многогранных призм проверяют аналогично на интерферометрах, которые позволяют получить более четкую интерференционную картину. Для измерения отклонений от плоскостности концевых мер длины 3-го, 4-го и 5-го разрядов можно также использовать измерительные приборы, например, миникаторы или микаторы с малым измерительным усилием.
Технический интерференционный метод поверки концевых мер длины
Поверяемую П и исходную И меры притирают к нижней стеклянной пластине 1 (рис. 92, а) в положениях так, чтобы они плотно соприкасались вдоль длинного ребра, а короткие ребра находились на одной прямой. На поверхности мер со стороны пластины не должно быть грязно-желтых разводов, указывающих на наличие слоя воздуха или неудаленного слоя смазочного материала между мерами и пластиной. Длину меры поверяют в срединной и угловых
точках. В положение II, в котором поверяют угловые точки
и
меру П переводят из положения I, поворачивая на 180° без отрыва от пластины.
При измерениях срединной длины на поверхности мер 3 под очень малым углом накладывают верхнюю стеклянную пластину 2 (рис. 92, б). Штрих перекрестия CD должен быть параллелен коротким ребрам, а точка перекрестия должна совпадать со срединной точкой О. Слегка нажимая на верхнюю пластину и изменяя ее наклон, добиваются того, чтобы на поверяемой мере интерференционные полосы расположились параллельно штриху CD.
При измерениях наиболее часто встречаются три случая:
- Срединные длины мер П и И равны (рис. 93, а). Первые интерференционные полосы равно удалены от ребра АВ клина. В этом случае, покачивая пластину, можно добиться, чтобы полоса / на мере И проходила через точку перекрестия CD и FE, а полоса / на мере Я совпадала с линией CD.
- Срединная длина меры П меньше, чем у меры И (рис. 93, б). Полоса / на мере Я ближе к ребру АВ. Совмещают точку перекрестия с полосой 1 на мере И, на глаз оценивают отношение расстояния
между линией CD и полосой 1 на мере П к ширине полос
. Отклонение длины меры П от длины меры И составляет
В данном случае
и
мкм.
- Срединная длина у меры П больше, чем у меры И (рис. 93, в). Полоса 1 на мере И ближе к ребру АВ. Линию CD совмещают с полосой 1 меры П и смещение оценивают вдоль линии EF. В данном случае
мкм.
Если между линией CD и ребром АВ лежат не полосы 1, то при определении срединной длины нужно
учитывать не только дробную часть длины волны, но и порядок интерференционных полос.
При измерениях по угловым точкам мер можно использовать пластины без скоса. В этом случае отсчет осуществляют по линии стыка мер от ребра клина. Если меры притерты в положении I (см. рис. 92, а) и верхняя пластина прижата к ребрам мер, на которых расположены точки 3 и 4 (рис. 94), то отклонение длины меры (рис. 92, а) в точке от длины меры И в точке 4 составляет
мкм.
где — номера полос на мерах между которыми отсчитывается дробная часть
В положении (см. рис. 92, а) поверяют также отклонение длины меры П в точке от длины меры И в точке 2, прижав верхнюю пластину к противоположному ребру. В положении поверяют длину меры в точках и
Разность между наименьшей и наибольшей измеренными длинами равна отклонению концевой меры от плоскопараллельности.
Возможно эта страница вам будет полезна:
Контактные интерферометры
Контактные интерферометры применяют для поверки концевых мер длины 2-го, 3-го и 4-го разрядов и классов точности 0; 1 и 2, а также для измерения особо точных изделий методом сравнения с концевыми мерами и образцовыми деталями. Интерферометры представляют собой измерительные трубки, закрепленные в вертикальных или горизонтальных стойках.
В интерференционной трубке (рис. 95, а) свет от лампы / проходит через конденсор 2 и разделяется на полупрозрачной пластине 8 на два когерентных пучка. Один пучок проходит через пластину 8, отражается от зеркала 5, которое жестко связано с измерительным стержнем 6, и возвращается к пластине 8. Второй пучок света отражается от пластины 8, проходит через компенсационную пластину 4 и возвращается зеркалом 7 к пластине 8. Встретившиеся на пластине 8 пучки создают интерференционную картину. Объектив 9 проецирует эту картину на стеклянную пластину 10, на которую нанесена шкала. Различные участки шкалы наблюдают в окуляр //, который поворачивают вокруг оси 12. Светофильтры 3 служат для градуирования шкалы.
Если зеркала 5 и 7 перпендикулярны к пучкам света, то оптическая разность хода лучей, отраженных от различных участков поверхности зеркал до пластины 8, постоянна и шкала освещена равномерно. При наклоне зеркала 7 с помощью специальных винтов создается переменная оптическая разность хода интерферирующих лучей вдоль пластины 8 (мнимый воздушный клин), и на фоне шкалы наблюдается интерференционная картина с полосами равной ширины (рис. 95, б).
Измерения проводят при освещении белым светом (без светофильтра). На шкале видны цветные радужные полосы убывающей яркости, расположенные по обе стороны от черной полосы — указателя шкалы, по которой берется отсчет. Указатель передвигается по шкале одновременно с перемещением измерительного стержня и связанного с ним зеркала 5.
Цена деления шкалы интерферометров переменная, так как ширина интерференционных полос зависит от угла наклона зеркала 7:
Ее выбирают в зависимости от требуемого предела измерения и регулируют, изменяя наклон зеркала 7. Градуирование выполняют
при освещении монохроматическим светом через светофильтр 3, так как в этом случае интерференционная картина состоит из большого числа черных и цветных полос, которые легко поддаются счету.
Подсчитывают число интерференционных полос расположенных между
делениями шкалы, и цену деления определяют по формуле
где — длина световой волны, мкм.
Число полос для счета следует определять по формуле а число делений шкалы
Рекомендуемые значения С шкалы интерферометров равны 0,05; 0,1 и 0,2 мкм. При пропускаемой светофильтром длине волны = 0.550 мкм этим значениям С соответствует число полос для счета
равное 8, 16 и 32, и число делений шкалы —
= 44.
При настройке, поднимая измерительный стержень, выводят на середину шкалы наиболее отчетливые интерференционные полосы. Изменяя наклон зеркала 7, совмещают требуемое число полос с рассчитанным числом делении шкалы
. Регулировку считают удовлетворительной, если при многократном арретировании измерительного стержня погрешность совмещения
полос с
делениями не превысит десятой доли деления.
Шкала интерферометров содержит по 50 делений слева и справа от нулевого штриха. Пределы показании составляют мкм; при цене деления
мкм допускаемая погрешность
мкм.
У вертикального интерферометра (рис. 96) трубка 2 стандартного диаметра 28 мм закреплена в стопке. Кремальера 4 перемещает кронштейн 3 в направляющих колонки 5. Винт позволяет передвигать шкалу прибора в пределах делений. На трубке закреплен прозрачный теплозащитный экран 7. Трансформатор
6 служит для питания осветительной системы. Назначение узлов стойки такое же, что и у оптиметра ОВЭ-02 (см. рис. 67, б).
При настройке прибора на нуль черную ахроматическую полосу устанавливают как указатель на нулевой штрих шкалы. При измерении концевую меру заменяют изделием, находят перемещением указателя по шкале и определяют отклонение размера изделия, умножая отсчет на цену деления шкалы. В комплект прибора входят сферический и плоский измерительные наконечники и три плоских сменных стола: основной плоский стол для измерения цилиндрических и сферических изделий размером до 150 мм; ребристый стол с выступающей сферической вставкой для концевых мер длиной до 20 мм и ребристый стол для плоскопараллельных изделий размером до 150 мм. К прибору прилагаются также амортизаторы и юстировочный инструмент, кроме того, могут быть приложены приспособления для измерения диаметров шариков и роликов и толщины тонкой ленты.
На горизонтальных интерферометрах (рис. 97) измеряют изделия размером до 500 мм. Трубка интерферометра 4 и пиноль 2 закреплены на измерительных бабках 1. которые перемещаются с помощью маховиков 5 по направляющим станины 6. Предметный стол 3 может перемещаться в трех взаимно перпендикулярных направлениях и поворачиваться относительно вертикальной и поперечной горизонтальной осей. Верхняя часть предметного стола свободно перемещается вдоль линии измерения на шариковых опорах, благодаря чему измеряемое изделие постоянно находится в контакте с измерительными наконечниками трубки и пиноли.
Измерения на горизонтальном интерферометре выполняют так же, как на горизонтальном оптиметре.
Возможно эта страница вам будет полезна:
Интерференционные методы измерений концевых мер длины
Абсолютный интерференционный метод предназначен для измерения длины образцовых мер 1-го разряда и рабочих мер класса точности 00 в длинах световых волн. В интерферометре (рис. 98) для абсолютных и относительных измерений (интерференционного компаратора Кестерса) свет от источника 6, пройдя конденсор 5, поступает в коллиматор 3 — оптическую трубу, предназначенную для получения параллельного пучка лучей. Входная щель 4 трубы расположена в фокусе объектива 2. Лучи света, выходящие из коллиматора, освещают специальную призму 1, с помощью которой в интерферометр можно направлять свет разной длины волны (любого цвета спектра). Свет, идущий от призмы , разделяется на полупосеребренной полупрозрачной стеклянной пластине 10 на два потока.
Один поток отражается от пластины 10, проходит через компенсационную пластину 11, отражается от
зеркала 12, снова проходит через пластины 11 к 10 и попадает в зрительную трубу, имеющую объектив 9, щель 8 и окуляр 7. Второй поток света проходит через пластину 10, отражается от поверхностей концевой меры 13 и стеклянной пластины 14, к которой притерта мера. Затем, отразившись от пластины 10, второй поток также поступает в зрительную трубу. Интерференционную картину наблюдают в окуляр 7. Перемещениями стола 15 интерферометра добиваются, чтобы расстояния jt пластины 10 до поверхностей зеркала 12 и пластины 14 были одинаковыми. При этом пути световых лучей, отразившихся от зеркала 12 и от пластины 14, будут равны, а лучи, отразившиеся от зеркала 12 и меры 13, будут иметь постоянную разность хода. Наклоняя стол 15, создают мнимый воздушный зазор (переменную разность хода) между поверхностями меры 13 и пластины 14, с одной стороны, и поверхностью зеркала 12, с другой. В окуляр зрительной трубы при этом наблюдают две системы интерференционных полос (рис. 99). Одна система полос возникает на поверхности пластины, вторая — на поверхности меры. В окуляр видны также две взаимно перпендикулярные нити перекрестия, нанесенного на зеркало 12. Стол перемещают так, чтобы интерференционные полосы на пластине были параллельны вертикальной линии перекрестия.
Если поверхности меры и пластины строго параллельны, то полосы на мере и пластине также параллельны (рис. 99, а). Отклонение меры от плоскопараллельности приводит к тому, что эти полосы будут лежать под углом одна к другой (рис. 99, б). Если длина меры не равна целому числу полуволн света, то полосы на пластине будут смещены относительно полос на мере. Размер смещения равен расстоянию от вертикальной линии перекрестия, совмещенной с серединой полосы на мере, до середины полосы меньшего номера на пластине. Направление отсчета на рис. 99 показано стрелками.
Длину меры определяют по уравнению где
— целое число полос;
— дробная часть полосы, которую находят непосредственным измерением. Например, на рис. 99, а
Для определения целого числа полос проводят серию измерений с световыми потоками, имеющими разные длины волн:
Целое число волн определяют методом совпадения дробных частей Предварительно длину меры измеряют с погрешностью
мм:
мм. По измеренному значению
длине световой волны
и дробной части
с помощью специальных таблиц или линеек находят целое число полос
Вычисляют длину меры
Аналогично обрабатывают результаты измерений с длинами волн
и вычисляют значение
Если значения
выбраны правильно, то значения
совпадают с требуемой точностью и равны
Если значения
отклоняются одно от другого больше, чем допускается, то значение целых чисел полос
изменяют, последовательно приближаясь к правильным значениям. Применение ЭВМ повышает скорость и точность расчета
Отклонения концевой меры от плоскопараллельно-сти определяют по наклону полос. Поверку проводят при вертикальном и горизонтальном направлениях полос на стеклянной пластине, что достигается изменением наклона стола. Центр перекрестия устанавливают на среднюю точку одной из темных полос на мере и на глаз определяют в долях полосы наибольшее отклонение поверяемой концевой меры от вертикальной (рис. 99, б) или горизонтальной (рис. 99, в) линии перекрестия.
Относительным интерференционным методом поверяют концевые меры 2-го разряда класса точности 0 путем сравнения с мерами 1-го разряда. Поверяемую П
и исходную И меры притирают к стеклянной пластине так, чтобы они соприкасались вдоль длинных граней. Пластину устанавливают на стол интерферометра. При наклоне стола в поле зрения окуляра возникают три картины полос (рис. 100, а): на каждой из мер и на пластине. Измерения проводят в белом свете, если разность длин мер не превышает 1,5 мкм. Отклонение длины поверяемой меры от длины исходной меры равно полудлине световой волны, умноженной на смещение полос одного номера на мерах. Значение отклонения определяют так же, как при техническом интерференционном методе. Если разность длин исходной и поверяемой мер превышает 1,5 мкм, то измерения выполняют в монохроматическом свете с различными длинами волн и отклонение определяют методом совпадения дробных частей полос. Длину мер предварительно измеряют с погрешностью мм.
Отклонение концевых мер от плоскопараллсльности при измерениях относительным методом определяют так же, как при абсолютном методе — по наклону полос на мере относительно полос на стеклянной пластине (рис. 100, б).
Методы и средства поверки угловых мер
Гониометрический метод поверки угловых мер заключается в сравнении измеряемого угла с точно градуированной
круговой угломерной шкалой — лимбом. Для этого используют специальные оптические приборы — гониометры. Принцип измерения углов на гониометрах показан на рис. 101. Основными узлами при-бора являются стол 5, лимб 4, коллиматор 3, отсчетный микроскоп 2 и зрительная труба 1. Современные конструкции гониометров позволяют поворачивать и фиксировать зрительную трубу, лимб и стол в любых положениях относительно коллиматора 3, жестко связанного с основанием. Труба и лимб имеют микрометрическую подачу.
Поверяемую меру П укладывают на стол так, чтобы измерительная грань АВ, ограничивающая рабочий угол меры находилась напротив коллиматора. Стол, жестко скрепленный с лимбом, поворачивают до тех пор, пока свет, отраженный от грани АВ, не попадет в объектив зрительной трубы 1. Затем с помощью микроподачи изображение щели коллиматора совмещают с вертикальной линией окулярной сетки трубы и выполняют первый отсчет по лимбу с помощью микроскопа 2. Затем стол поворачивают и все измерения проводят на второй измерительной грани АС меры. Угол
поворота стола равен разности отсчетов по лимбу в первом и во втором положениях стола. Измеряемый угол а меры дополняет угол
до 180° .следовательно,
Угловые меры 3-го разряда и класса точности 0 поверяют на гониометрах типа ГС1 с допускаемой погрешностью меры 4-го разряда и класса точности 1 — на гониометрах типа ГЗ с
а меры класса точности 2 — на гониометрах типа Г5 с
Относительным контактным методом поверяют угловые меры класса точности 2 путем сравнения с образцовыми угловыми мерами 4-го разряда. Схема поверки на приборах КПУ показана на рис. 102, а. Поворотный упор указателем 2 устанавливают по шкале 3 на номинальное значение угла сравниваемых мер и фиксируют в данном положении. Образцовую угловую меру И
прижимают измерительными поверхностями к шаровым поверхностям упоров 5. Стрелку отсчетного устройства 4 устанавливают около нуля и снимают отсчет Затем образцовую меру заменяют мерой П и выполняют второй отсчет
Действительное значение угла поверяемой меры находят по формуле
где
размер угла образцовой меры; С — цена деления отсчетного устройства прибора.
Для поверки угловых мер класса точности 2 относительным контактным методом используют также универсальные измерительные средства, например, микро-каторы и оптиметры. Поверяемую П и образцовую И угловые меры с одинаковыми номинальными значениями рабочих углов притирают одну к другой, как показано на рис. 102,6. Чтобы повысить надежность соединения мер, их можно скрепить державкой. Притертые меры устанавливают на ребристом столе вертикальной стойки и с помощью измерительной головки определяют непараллельность сторон блока мер. Для этого блок
мер сначала устанавливают в положение , а затем перемещают в положение . Отклонение угла поверяемой меры от номинального угла образцовой меры в радианах связано с перемещением
конца измерительного наконечника измерительной головки
соотношением или в секундах
где
— расстояние между точками измерений;
— показания прибора. При расстоянии между точками измерений
мм отклонение
где
выражается в миллиметрах.
Рабочий угол поверяемой меры
Возможно эта страница вам будет полезна:
Средства и методы измерения отклонений от прямолинейности и плоскостности
Форма плоских поверхностей характеризуется прямолинейностью и плоскостностью. Отклонение от прямолинейности — наибольшее расстояние от точек реального профиля 2 до прилегающей прямой 1 в пределах нормируемого участка (рис. 103, а, б). Отклонение
от плоскостности — наибольшее расстояние от точек реальной поверхности 2 до прилегающей поверхности 1 в пределах нормируемого участка (рис. 103, в). Частными видами отклонения от прямолинейности и плоскостности являются выпуклость (рис. 103, а), при которой отклонения уменьшаются от краев к середине, и вогнутость (рис. 103, б) — характер отклонений обратный.
По значению отклонений плоские поверхности делят на 16 степеней точности в соответствии с установленными допусками плоскостности и прямолинейности в пределах нормируемого участка. С увеличением степени точности размер допуска увеличивается.
В качестве рабочих средств измерений применяют поверочные линейки и плиты, оптические линейки и плоскомеры, инструментально-поверочные блоки ИПБ, автоколлиматоры, автоматические автоколлимационные и гравитационные приборы, оптические струны, гидростатические уровни, микронивелиры и уровни.
При контроле плоскостности измерительных поверхностей калибров, приборов и инструментов размером до 120 мм не грубее 2-й степени точности применяют плоские стеклянные пластины для интерференционных измерений (см. рис. 90, а). Пластины накладывают на проверяемую поверхность и наблюдают интерференционную картину. Плоскостность изделий прямоугольной формы определяют по выпуклости и вогнутости интерференционных полос так же, как при поверке плоскостности концевых мер длины (см. рис. 91, § 55). Плоскостность поверхностей изделий, имеющих форму круга, определяют по числу замкнутых интерференционных колец. На рис. 104 число замкнутых колец равно 2, следовательно,
Поверочные линейки
Поверочные линейки (рис. 105) изготовляют следующих типов: ЛД — лекальные с двусторонним скосом; ЛТ — лекальные трехгранные; ЛЧ — лекальные четырехгранные; ШП — с широкой рабочей поверхностью прямоугольного сечения; ШД— с широкой рабочей поверхностью двутаврового сечения; ШМ — с широкой рабочей поверхностью, мостики; УТ — угловые трехгранные.
Лекальные линейки выпускают двух классов точности: 0 и 1. Линейки класса точности 0 применяют для поверки поверхностей 2-й и 3-й степеней точности, а класса точности 1 — 4-й степени точности. Длина лезвий линеек типа ЛД составляет 50…500 мм, а линеек типов ЛТ и ЛЧ — 200…500 мм.
Лекальные линейки предназначены для контроля прямолинейности методом «на просвет». Лезвие линейки 1 накладывают на поверхность изделия 2 (рис. 106, а). Сзади, на уровне глаз контролера, помещают источник света и наблюдают просвет между линейкой и изделием. Отклонение от прямолинейности равно наибольшему просвету размер просвета определяют по «образцу просвета» (см. рис. И).
Линейки с широкой рабочей поверхностью выпускают трех классов точности: 0, 1 и 2. Линейки класса 0 применяют для проверки поверхностей 4-й степени точности, класса 1 — для 6-й и 7-й степени точности и класса 2 — для проверки поверхностей 7-й и 8-й степени точности. Размеры линеек различных типов имеют следующие значения: для линеек типа ШП —
для линеек типа ШД —
для линеек типа ШМ —
Линейки с широкой рабочей поверхностью применяют для проверки прямолинейности методом линейных отклонений и для проверки плоскостности узких поверхностей методом «на краску».
При контроле прямолинейности методом линейных отклонений (рис. 106, б) линейку 1 укладывают рабочей поверхностью на две одинаковые концевые меры 3 размером установленные на проверяемой поверхности 2. Для уменьшения погрешностей измерений вследствие прогибов линейки опоры располагают в точках наименьшего прогиба (точки Эри), которые отмечены рисками на боковой поверхности линеек. Точки Эри лежат на расстоянии
от концов линейки. На боковую поверхность линейки наносят мелом отметки на расстояниях, равных
В отмеченных точках
измеряют расстояние
между поверхностями линейки и изделия, вводя между ними блоки концевых мер или щупы 4. Используются также специальные приспособления с индикаторными приборами. По результатам измерений определяют разность
Построив график
(рис. 106, в), через крайние точки ломаной линии проводят прямую АВ. Отклонение от прямолинейности поверхности
находят как наибольшее расстояние от ломаной линии до прямой АВ.
Угловые линейки типа УТ изготовляют длиной 400, 630 и 1000 мм с двумя шабренными рабочими поверхностями, образующими угол а, равный 45, 55 и 60°. По отклонениям граней от плоскостности эти линейки делят на классы точности 0, 1 и 2. Угловые линейки используют для одновременного контроля плоскостности пересекающихся поверхностями 7-й и 8-й степеней точности методом «на краску», например, при поверке направляющих типа «ласточкин хвост».
Возможно эта страница вам будет полезна:
Поверочные и разметочные плиты
Поверочные и разметочные плиты выпускают двух исполнений: 1 — с ручной шабровкой рабочих поверхностей классов точности 00, 0 и 1; И — с механически обработанными поверхностями классов точности 1, 2 и 3. Плиты классов 00 и 0 применяют для поверки плоскостности поверхностей особо точных деталей, а классов 1 и 2 — точных деталей. Плиты класса 3 используют для разметочных работ.
Плиты (рнс. 107) изготовляют из чугуна и из твердых горных пород — гранита, диорита, диабаза. Размеры
поверхности плит составляют
Плиты размером 1000X630 мм и более имеют регулируемые опоры. При установке плит опоры регулируют так, чтобы обеспечить равномерное распределение нагрузки на все опорные точки и выравнивание поверхности плиты.
Плиты предназначены для контроля плоскостности изделий методом «на краску» и методом линейных отклонений. В первом случае рабочую поверхность покрывают тонким слоем краски. Рекомендуется применять типографскую краску № 219 или берлинскую лазурь и турбуленовую синь, разведенные в машинном масле. Толщина слоя краски для плит класса точности 00 рекомендуется 0,4…1 мкм; класса 0 — 0,6… 1,6 мкм; класса 1 — 1,0…2,5 мкм и класса 2 — 2,5… 10 мкм. Толщину слоя краски контролируют по «образцу интенсивности окраски» (см. рис. 11).
Окрашенную плиту накладывают на проверяемую поверхность и слегка перемещают. Отклонение от плоскостности определяют по числу пятен в квадрате со стороной 25 мм, оставшихся на выступающих частях проверяемой поверхности. Для подсчета используют пластины с окном Проверка на «краску» не позволяет определить значение неплоскостности. По числу пятен судят о степени точности поверхности. При хорошей плоскостности пятна располагаются равномерно, и чем больше пятен, тем меньше неплоскостность.
При проверке плоскостности методом линейных отклонений изделие устанавливают проверяемой поверхностью на три опоры одного размера, располагаемые на поверочной плите и не лежащие на одной прямой. Отклонение от плоскостности определяют по разности показаний специального индикаторного прибора, вводимого между плитой и изделием. Прибор устанавливают в заранее намеченных точках. Наибольшее показание прибора, предварительно настроенного на размер опор, равно отклонению от плокостности поверхности. Это значение сравнивают с допуском плоскостности.
Измерение уровнями
Измерение отклонений от плоскостности брусковыми уровнями (см. § 30) выполняют шаговым методом. Проверяемую поверхность изделия 1 устанавливают
грубо в горизонтальное положение (рис. 108, а). На поверхности в заданном направлении наносят отметки О, 1, 2, 3, …, 10 с интервалом проверяемой длины. Уровень 2 закрепляют на подставке 3 с опорами 4, расстояние между которыми равно выбранному интервалу
. Подставку последовательно устанавливают на участки 0—1, 1—2, 2—3, … Отклонение от прямолинейности поверхности обусловливает различный наклон ее отдельных участков относительно горизонтальной линии, проведенной через точку 0, принятую за начало отсчета.
Наклон участка поверхности определяют по уровню (рис. 108, б). Отсчеты выполняют по смещению пузырька относительно штрихов А и Б на ампуле уровня, которые расположены симметрично относительно нуль-пункта на расстоянии один от другого, равном длине пузырька. Показание уровня равно алгебраической полусумме обоих отсчетов. Отсчет считают положительным, если пузырек смещается по ходу перемещения уровня, что соответствует подъему поверхности. На рис. 108, б отсчет деления шкалы.
Смещение по вертикали смежных точек поверхности где С — цена деления шкалы ампулы, мм/м.
Результаты измерений сводят в таблицу и по ней строят график (рис. 108, в) отклонений точек поверхности от горизонтали. Через первую и последнюю точки графика проводят прямую линию, учитывающую общий наклон поверхности. Отклонение от прямолинейности поверхности равно наибольшему отклонению точек графика от прямой линии.
Контроль плоскостности уровнем осуществляется аналогично контролю прямолинейности. Схема перемещения уровня по плоскости показана на рис. 109. Сначала измерения проводят по замкнутому контуру в точках 0, 1, 2, 3, …, 15,0. Затем проверяют точки 15, 16…..6
и 14, 20, 21, 22, 23,7. Подставку перемещают последовательно на все участки поверхности. Показания отсчитывают по обоим концам пузырька при двух положениях уровня, отличающихся на 180°. Результирующее показание определяют по четырем отсчетам. При обработке результатов измерений учитывают наклон поверхности как в продольном, так и в поперечном направлениях.
Гидростатические уровни (рис. 110), применяемые для контроля горизонтально расположенных поверхностей большой протяженности, основаны на принципе сообщающихся сосудов. Они состоят из двух измерительных головок 1 и 4, наполненных водой и соединенных между собой гибкими шлангами. Шланг 6 обеспечивает переток воды, а шланг 3 — переток и выравнивание давления воздуха. Каждая головка имеет микрометрические глубиномеры 2 и 5 с острием на конце микровинта. При контроле прямолинейности и плоскостности одну измерительную головку устанавливают неподвижно на поверхность, а другую последовательно перемещают по заданным точкам поверхности. Отклонение Д различных участков поверхности относительно горизонта находят по разности показаний микрометров. Результаты измерений обрабатывают так же, как при измерениях уровнями.
Для контроля прямолинейности и плоскостности также используют микрометрические и электронные уровни.
Вопросы для самопроверки
1. Что такое отклонение от плоскостности? 2. Как контролируют прямолинейность лекальной линейкой? 3. Какие типы поверочных линеек и плит Вы знаете? 4. Как осуществляют контроль плоскостности методом на краску? 5. Какие параметры плоской поверхности можно измерить методом линейных отклонений? 6. Как выполняют контроль прямолинейности уровнем? 7. Что представляют собой гидростатические уровни?
Средства и методы измерения резьбы
Резьбой называется один или несколько равномерно расположенных выступов резьбы, постоянного сече-ння, образованных на боковой поверхности прямого кругового цилиндра или прямого кругового конуса. Выступы ограничиваются винтовой поверхностью резьбы и разделены канавками. Основные элементы резьбы (рис. Ill) — ось, относительно которой образована винтовая поверхность резьбы; профиль резьбы, который состоит из профилей выступа и канавки резьбы в плоскости осевого сечения; вершина резьбы 1; впадина резьбы 2; боковая сторона профиля 3, расположенная между вершиной и впадиной и имеющая в плоскости осевого сечения прямую линию; радиус впадины резьбы По типу поверхности резьбы делят на цилиндрические и конические; по расположению
поверхности — на наружные (болт) и внутренние (гайка); по направлению вращения винтовой линии — на правые и левые; по числу заходов резьбы — на однозаходные и многозаходные; по типу профиля — на метрические, дюймовые, трубные, упорные и трапецеидальные.
Основные контролируемые параметры цилиндрической резьбы — угол профиля, углы
и
наклона боковой поверхности, наружный диаметр
или D, внутренний диаметр
или
средний диаметр
или
шаг резьбы Р. По среднему диаметру ширина канавки равна половине шага резьбы. Для резьбы с симметричным профилем
Полные сведения о резьбах и их параметрах изложены в ГОСТ 11708—82. Размеры резьб стандартизованы по диаметру и шагу. Диаметр, условно характеризующий размеры резьбы и используемый при ее обозначении, называется номинальным диаметром резьбы.
Наружный диаметр болта и внутренний диаметр
гайки измеряют универсальными приборами, например штангенциркулем или на оптиметре. Шаг резьбы контролируют резьбовыми шаблонами 1 (рис. 112), которые выпускают наборами в обойме 2. Для метрической резьбы шаг изменяется в пределах 0.4…6 мм, а для дюймовых резьб число ниток на один дюйм — 4…28. Номинальному шагу резьбы соответствует тот шаблон, который наилучшим образом сопрягается с профилем резьбы.
Резьбовые калибры
Контроль цилиндрической резьбы, обеспечивающий ее взаимозаменяемость, осуществляется комплексными предельными калибрами. Проходные калибр-пробки и калибр-кольца имеют полный профиль; с их помощью контролируют приведенный средний диаметр резьбы, учитывающий влияние всех ее параметров на свинчиваемость. Непроходные калибры имеют укороченный профиль и небольшое число витков резьбы; ими контролируют только средний диаметр резьбы. Непроходные калибры не должны свинчиваться с годным изделием более чем на два витка.
Калнбр пробки для метрической резьбы выпускают нескольких типов: двухсторонние калибры с вставками, проходные и непроходные (рис. 113, а); однопре-дельные калибры с насадкой (рис. 113, б); калибры с ручками (рис. 113, в). Непроходные пробки имеют гладкие цилиндрические направляющие. Жесткие калибр-кольца (рис. 114, а) применяют для контроля резьбы диаметром 1…300 мм; непроходное кольцо имеет проточку. В кольца диаметром 105…300 мм ввинчиваются ручки, облегчающие работу. Регулируемые калибр-кольца (рис. 114, б) имеют резьбовую пробку 2, которой через втулку 3 разжимают кольцо 1 до необходимого размера Винтом 4 фиксируют установленный размер. Глухие выточки обеспечивают подпружинивание корпуса.
Для контроля отдельных участков наружной резьбы применяют скобы, не требующие длительной операции свинчивания. Жесткие резьбовые скобы (рис. 115, а) имеют коническую 1 и призматическую 2 вставки, которые вводятся во впадины резьбы. Роликовые регулируемые
скобы (рис. 115, б) имеют две пары проходных 2 и непроходных / роликов, свободно вращающихся на эксцентричных валиках 3. Поворот валиков дает возможность изменять расстояние между осями роликов в пределах 0,6…1 мм. Установленный размер фиксируют винтом 4 и гайкой 5.
Условные обозначения резьбовых калибров: ПР (НЕ) — рабочие кольца и пробки, проходные (непроходные); КПР—ПР (КПР—НЕ) — контрольные пробки для нерегулируемых проходных колец, проходные (непроходные); КНЕ—ПР (КНЕ—НЕ) — контрольные пробки для нерегулируемых непроходных колец, проходные (непроходные); К—И (КНЕ—И) — непроходные пробки для контроля износа нерегулируемого и регулируемого кольца, проходные (непроходные); У— ПР (У—НЕ) — установочные пробки для регулируемого кольца, проходные (непроходные).
Измерение среднего диаметра и шага наружной резьбы
Микрометр со вставками для измерения среднего диаметра резьбы (рис. 116, а) имеет в пятке 1 и микровинте 4 отверстия, в которые вставляются сменные призматические
2 и конические 3 вставки. Для измерения метрических и трапецеидальных резьб используют по иосемь пар вставок, для измерения дюймовых резьб — шесть пар вставок. Чтобы компенсировать изменение длины вставок, барабан изготовляют раздвижным; он состоит из частей 5 и 7, стягиваемых гайкой 6. При установке микрометра на нуль вращением трещотки коническую вставку подводят до соприкосновения с призматической вставкой или установочной мерой 8, помещаемой между ними, и стопорят микровинт. Правильное положение края барабана относительно начального штриха шкалы стебля устанавливают вращением гайки 6 и перемещением передней части барабана. Поверхности вставок при измерениях приводят в соприкосновение с профилем резьбы (рис. 116, б). Погрешность измерения может составлять 0,1…0,2 мм.
Более точным методом измерения среднего диаметра резьбы является косвенный метод трех калиброванных проволочек (рис. 117). Во впадины резьбы 1 закладывают три проволочки 2 и измеряют размер М. Диаметр проволочек выбирают в зависимости от типа и шага резьбы по специальным таблицам. Для резьбы с симметричным профилем
Средний диаметр вычисляют по формулам: для метрической резьбы для дюймовой резьбы
для трапецеидальной резьбы
где С — поправка, учитываемая при точных измерениях.
В зависимости от требуемой точности размер М можно измерить на микрометрах, оптиметрах, длиномерах и т. п. Измерение на микрометрах (рис. 118, а) выполняют с помощью державок 1, 2, надетых на микровинт и пятку. Микрометр 4 закреплен в стойке 5. На плоскости державок закреплены проволочки 3. Державки поворачиваются вокруг своих опор, что дает возможность устанавливать проволочки по углу подъема винтовой линии.
В горизонтальном оптиметре (рис. 118, б) калибры-пробки 5 закрепляют на столе 6 горизонтально с помощью приспособлений 4. Проволочки 2 подвешивают за бирку 3 на кронштейне 1. Порядок измерений описан в § 47. Предварительно по известным теоретическим параметрам проверяемой резьбы подсчитывают размер М и по нему подбирают блок концевых мер для установки прибора на нуль.
Шаг резьбы можно измерить с помощью индикаторных шагомеров. Шагомер для калибр-пробок диаметром свыше
250 мм (рис. 119) состоит из пружинной головки 4, на которой закреплены ножка 3 и рычаг 1 с шариковыми наконечниками. Головку устанавливают на нуль по образцовому резьбовому калибру. Ножки вставляют во впадины резьбы, и отклонение рычага 1 передается измерительному наконечнику 2.
Измерение параметров наружной резьбы на микроскопах
На микроскопах основные параметры наружной резьбы измеряют теневым методом в проходящем свете. Проверяемое изделие, например калибр-пробку, закрепляют в центрах. Предварительно ось центров устанавливают параллельно продольному ходу стола с помощью контрольного валика, входящего в комплект принадлежностей. Диафрагму осветителя выбирают по инструкции, прилагаемой к микроскопу, в зависимости от среднего диаметра резьбы. Колонку микроскопа наклоняют на угол подъема резьбы, который можно подсчитать по формуле Объектив микроскопа наводят на резкое изображение.
При измерении среднего диаметра (рис. 120, а) штриховую линию перекрестия окулярной головки совмещают с боковой стороной профиля резьбы и проводят первый отсчет по поперечной микрометрической головке. Затем стол микроскопа перемещают так, чтобы та же линия окулярной сетки совместилась с противоположной стороной профиля резьбы. Колонку микроскопа
при этом наклоняют на угол
в противоположную сторону. Выполняют второй отсчет. Разность отсчетов равна среднему диаметру. Аналогично проводят измерения по второй стороне профиля. Среднее арифметическое результатов двух измерений принимают за средний диаметр резьбы:
При измерении шага резьбы точку перекрестия совмещают с серединой профиля резьбы (рис. 120, б) и делают первый отсчет по продольному микровинту. Затем стол перемещают так, чтобы та же штриховая линия совпадала с одноименной стороной следующего профиля. Разность отсчетов равна шагу резьбы. Измерения выполняют по левым и правым сторонам профиля с обеих сторон контура. Среднее арифметическое четырех измерений принимается за шаг резьбы:
При измерении половины угла профиля резьбы (рис. 120, в) горизонтальную штриховую линию перекрестия совмещают с профилем резьбы и выполняют отсчет по угломерной шкале окулярной головки. Значение отсчета равно половине угла профиля. Измерения осуществляют по четырем сторонам профиля и за половину угла профиля принимают среднее арифметическое.
Большая точность измерений параметров резьбовых калибр-пробок на микроскопах достигается с помощью измерительных ножей (рис. 121, а). Ножи 1 размещают на установочных плоскостях микроскопов и прижимают к контуру резьбы так, чтобы между лезвием ножа и боковыми сторонами профиля резьбы 2 не оставалось щели. На верхнюю плоскость ножей наиесены
тонкие риски. Расстояние между лезвием ножа и риской, называемое рабочим размером ножа, равно 0,3 мм (при измерении резьб с шагом 3.5…6 мм). При измерениях фокусируют микроскоп на тонкую риску и перемещениями стола совмещают риски с линиями
или
окулярной сетки. При этом линия аи’ совпадает с боковой стороной профиля резьбы. С помощью измерительных ножей измеряют средний диаметр резьбы (рис. 121, б), шаг резьбы (рис. 121, в), половину угла профиля и внутренний диаметр резьбы.
Возможно эта страница вам будет полезна:
Сведения об измерении внутренней резьбы
Для измерения среднего диаметра внутренних резьб применяют приборы с шаровыми наконечниками. Индикаторный прибор (рис. 122) имеет сменную резьбовую пробку 4 с шаровыми вставками 3. При измерениях пробку ввинчивают в проверяемую резьбу. Коническая игла 2, связанная со стержнем индикатора 1, раздвигает вставки 3 до контакта с профилем резьбы. Прибор устанавливают на нуль по образцовому резьбовому калибру. Индикатор 1 показывает отклонение действительного размера от размера образца. Средний диаметр внутренней резьбы свыше 18 мм измеряют на горизонтальных оптиметрах с помощью специальных приспособлений с дугами. Шаг, средний диаметр и половину угла профиля внутренней резьбы можно измерить также на универсальном микроскопе УИМ-21 с помощью приспособления ИЗК-59.
В лабораторных условиях
шаг и угол профиля внутренней резьбы можно определить с помощью слепков и отливок. Применяют отливки из серы и легкоплавких сплавов, например сплава Вуда. Слепки изготовляют из медицинского гипса, 60 частей которого разводят на 40 частей водного раствора хромпика (40 г хромпика на 1 л воды, подогретой до 40…50°С). Профиль резьбы, полученный на слепках и отливках, измеряют на микроскопах.
Средства и методы измерения зубчатых колес
Основные элементы и параметры зубчатых колес
В зубчатых передачах вращение звеньев осуществляется посредством взаимодействия выступов (зубьев) на одном звене с зубьями (выступами) другого звена. Основной деталью таких передач является зубчатое колесо, объемные элементы которого — тело зубчатого колеса, зубчатый венец и впадины. Конструкция зубчатых колес определяется типом зубчатой передачи. Их основные виды: цилиндрические, конические и гипоидные зубчатые колеса, червячное колесо, червяк и др. Цилиндрические зубчатые колеса по типу зубьев делятся на прямозубые, косозубые, шевронные и др., а по профилю зубьев — на эвольвентные, циклоидальные и др.
Установлено 12 степеней точности зубчатых колес и передач, обозначаемых в порядке убывания точности от 1 до 12 (ГОСТ 1643—81). Каждой степени точности соответствуют: нормы кинематической точности, ограничивающие погрешность углов поворота колес; нормы плавности работы, ограничивающие неравномерность хода колес за один оборот; нормы контакта зубьев, определяющие полноту прилегания рабочих поверхностей зубьев между собой. К показателям норм кинематической погрешности относятся накопленная погрешность шага по зубчатому колесу, радиальное биение зубчатого венца, колебание длины общей нормали и т. п.; к показателям норм плавности работы — местная кинематическая погрешность, отклонение шага, погрешность профиля зуба и т. п.; к показателям норм контакта зубьев — суммарное пятно контакта, погрешность направления зуба, погрешность контактной линии и т. д. Установлено шесть видов сопряжений зубчатых колес в передаче, которым соответствуют нормы бокового зазора, независимые от степеней точности зубчатых колес. Показателями, обеспечивающими гарантированный боковой зазор, являются отклонения межосевого расстояния, отклонение длины общей нормали, отклонение толщины зуба и др.
Зубоизмерительные приборы выполняются двух типов: станковые, на которых размещают проверяемые колеса, и накладные, устанавливаемые на проверяемое колесо по зубьям или впадинам.
Приборы для измерения основного и окружного шага
Шагомер для контроля основного нормального шага (рис. 124) имеет корпус 1 с подвижной измерительной губкой 3, связанной с механизмом встроенного индикатора 2. Установочную губку 4 перемещают в корпусе винтом 8 и зажимают винтом 7. Опорную губку 5 перемещают винтом 10, поворачивают винтом 9 и фиксируют винтом 6. Шагомер настраивают на номинальное значение шага, равное с помощью приспособления, состоящего из основания 14, державки 13, вильчатого боковика 12 и Г-образного боковика 11. Между боковиками помещают блок концевых мер, размер которого равен
и индикатор устанавливают на нуль.
При измерении установочную губку 4 плотно прижимают к средней части профиля зуба с помощью губки 5, которая упирается в соседний зуб. Отклонение шага зацепления от номинального значения определяют по наибольшему показанию индикатора при движении шагомера вокруг колеса.
Шагомер для контроля основного окружного шага (рис. 125) имеет корпус 5, индикатор 4, подвижную губку 9 н переставную губку 8, которая устанавливается на модуль проверяемого колеса по шкале 7 и зажимается винтом 2. Положение передних 6 и заднего 3 упоров регулируют так, чтобы измерительные губки касались зубьев в точках, близких к делительной окружности, и зажимают винтами 1. При измерениях шагомер устанавливают на нуль по любой паре зубьев, а затем последовательно накладывают на соседние пары до возвращения на исходную пару зубьев. Индикатор показывает отклонение окружных шагов зубьев. Пример измерений приведен в табл. 10.
Разность окружных шагов определяют
как абсолютную разность показаний индикатора. Наибольшая разность основного окружного шага в примере Накопленную погрешность окружного шага определяют в следующем порядке: 1) подсчитывают сумму ряда показаний шагомера
и определяют среднее арифметическое ряда показаний
2) определяют отклонение шага от среднего значения
3) полученные отклонения шага последовательно суммируют; 4) накопленную погрешность шага
определяют как разность наибольшего и наименьшего чисел из полученного ряда.
Методы и приборы для контроля профиля зубьев
Профиль зубьев проверяют следующими методами: 1) сопоставлением действительного профиля зуба с образцовым контуром шаблона «на просвет»; 2) сравнением профиля зуба, увеличенного в 10…100 раз на проекторах, с теоретическим профилем, вычерченным с тем же увеличением и помещенным на экране проектора; 3) измерением на эвольвентомерах — приборах, сопоставляющих действительный профиль зуба с теоретической
эвольвентой основной ружности зубчатого колеса.
Индивидуальный дисковый эвольвснтомер (рис. 126) имеет поперечную (на рисунке не видна) и продольную 10 каретки, которые перемещаются j по направляющим 2 и 9 с помощью маховиков / и 8. На поперечной каретке на одной оси закреплены проверяемое зубчатое колесо 5 и смешанный диск 4 обката, диаметр которого равен диаметру основной окружности колеса. На каретке 10 установлены линейка 6 обката и рычаг 7, связанный с индикатором 12. Измерительный наконечник рычага расположен в одной плоскости с рабочей поверхностью линейки обката. Поперечную каретку передвигают до плотного контакта диска 4 с линейкой обката и устанавливают измерительный наконечник так, чтобы он касался профиля зуба у основания. В таком положении индикатор ставят на нуль. При перемещении каретки 10 с помощью маховика 8 диск вращается вместе с зубчатым колесом без проскальзывания относительно линейки 6. Шкала 3 показывает угол поворота колеса, а шкала 11 — смещение каретки из исходного положения.
Каждая точка линейки описывает эвольвенту относительно основной окружности зубчатого колеса и диска обката, а измерительный наконечник скользит по профилю зуба. Если профиль зуба выполнен точно на эвольвенте, то наконечник остается в одной плоскости с линейкой обката и показания индикатора равны нулю. Отклонения профиля от эвольвенты вызовут смещение измерительного наконечника. Погрешность профиля зуба 1 равна абсолютному значению разности наибольшего и наименьшего показаний индикатора.
Универсальные эвольвентомеры перед измерением их настраивают на размер делительной окружности зубчатого колеса, так как они не имеют сменных дисков обката. По конструкции эти приборы делят на две группы: с основным диском и с постоянным копиром. В универсальном приборе БВ-5062 (рис. 127) эвольвента воспроизводится
с помощью основного диска 4 радиусом Rb и ведущей каретки 1. Стальная лента 2, прикрепленная к каретке 1, охватывает диск 4 она выполняет роль линейки обката. Зубчатое колесо 3, радиус делительной окружности которой равен гь, вращается на одной оси с диском. Перемещение каретки 1 через ролик 6 и рычаг 7 с осью 8 передается упору 9, закрепленному на каретке 10, несущей измерительный узел 11. Ось упора 9 расположена в одной плоскости с контактной точкой измерительного наконечника 5, которая движется по эвольвенте основной окружности зубчатого колеса. Для настройки эвольвентомера на заданный радиус основной окружности каретка 10 перемещается в направлении к оси колеса. При этом одновременно изменяется положение упора 9 на рычаге 7, что обеспечивает требуемое передаточное отношение рычажной передачи. Отсчет перемещений каретки осуществляется по оптической шкале с помощью микроскопа 12. Отклонение профиля зуба от эвольвенты основной окружности измеряется индикатором или записывается отсчетным устройством в увеличенном масштабе на диаграммной ленте.
Приборы для контроля радиального биения зубчатого венца
Радиальным биением называется разность предельных положений исходного контура в пределах зубчатого
колеса. Радиальное биение определяют по перемещению измерительного наконечника 1 (рис. 128,а), установленного на штоке 3 с шариковыми опорами. Шток связан с индикатором 2. Наконечник поочередно вводят во все впадины колеса. Наибольшая разность показаний индикатора равна радиальному биению
Измерительные наконечники для зубчатых колес внешнего зацепления выполняются в виде усеченного конуса с углом при вершине, равным а для колес внутреннего зацепления— в виде шариков или роликов диаметром
Биениемер (рис. 128,6) состоит из станины 1, центровых бабок 2 для крепления зубчатого колеса и бабки 4. на которой расположена каретка 6 с измерительным узлом 12. Бабка 4 перемещается перпендикулярно к линии центров вручную и стопорится винтом 5. Каретку 6 перемещают вдоль линии центров маховиком 5 и стопорят винтом 7. Маховиком 9 измерительный узел 12 подводят к колесу так, чтобы наконечник 16 встал во впадину колеса, и стопорят винтом 10. Шток 15, упирающийся планкой 13 в наконечник индикатора 14, отводят от колеса ручкой 11. При контроле конических колес измерительный узел 12 поворачивают в горизонтальной плоскости при освобожденной ручке 8 и устанавливают по угломерной шкале на определенный угол.
Средства измерения смещения исходного контура и толщины зуба
Необходимые боковые зазоры в зубчатом зацеплении создаются путем смещения исходного контура зубонарезного
инструмента к оси колес при их изготовлении Смещение исходного контура и отклонение толщины зуба
по постоянной хорде связаны соотношением
(рис. 129,а).
Тангенциальные зубомеры (рис. 129,6) предназначены для определения смещения исходного контура относительно наружного диаметра колес. Исходный контур воспроизводится двумя измерительными губками 6 и 8. имеющими угол скоса 20°. Губки расположены на основании 1 симметрично относительно оси индикатора 3 с удлиненным измерительным стержнем 7. Индикатор зажимается винтом 4. Перед измерением зубомер настраивают на номинальное положение исходного контура по калиброванному ролику 9 диаметром уложенному в призме 10. Зубомер губками устанавливают на ролик. Расстояние между губками регулируют вращением винта 5 таким образом, чтобы стрелка индикатора сделала один-два оборота. Затем положение губок фиксируют винтами 2 и индикатор устанавливают на нуль. При измерении зубомер накладывают губками на проверяемый зуб и легко покачивают вокруг оси колеса. Наибольшее показание индикатора равно смещению исходного материала. Положительные отклонения стрелки указывают на уменьшение толщины зуба, а отрицательные — на увеличение толщины.
Штангензубомерами (рис. 130) измеряют толщину зубьев. Штангензу-бомеры имеют две взаимно перпендикулярные штанги 1 и 4. По штанге 1 с губкой 7 перемещается нониусная рамка 2 с упором 3, а по штанге 4 — рамка 5 с губкой 6. 7 У Измерения рекомендуется ‘ выполнять по постоянной хорде колеса, характеризующей положение исходного контура. При угле зацепления 20° расстояние от постоянной хорды до окружности выступов теоретическая толщина зуба по постоянной хорде
Обычно значения
и
находят по заранее составленным таблицам.
При измерении толщины зуба упор 3 устанавливают по нониусу 2 на расчетное значение и затем накладывают на проверяемый зуб. Губки б и 7 сдвигают и по нониусу измеряют толщину зуба
Измерение длины общей нормали
Длиной общей нормали называется расстояние между параллельными плоскостями, касательными к двум разноименным профилям зубьев. Расчетную длину обшей нормали для прямозубых колес с углом 20° при температуре 20 °С определяют по формуле
где z— число зубьев колеса; —число зубьев, охватываемых губками нормалемера.
Нормалемер БВ-5045 (рис. 131) имеет трубчатую штангу 3 и индикатор 1, связанный с подвижной измерительной губкой 9. Перед измерением кольцо 4 с переставной губкой 8 устанавливают на расчетное значение w по блоку концевых мер и зажимают винтом 5. Тонкое перемещение губки осуществляют ганкой микроподачи
6 при зажатом кольце 7. При измерении губку 9 отводят рычагом 2 и нормалемер устанавливают на зубья колеса. Наименьшие показания индикатора при легком покачивании прибора определяют отклонение длины общей нормали от расчетного значения.
Контроль контакта зубьев
Полнота контакта зубьев в передаче определяется отклонениями формы и направления контактных линий, по которым соприкасаются зубья колес. Она контролируется на специальных приборах — ходомерах, изменяющих отклонения направления зубьев, и контактомерах, предназначенных для определения погрешности формы и направления контактной линии.
Универсальные контактомеры (рис. 132,а) имеют но-жевидный тангенциальный (расположенный по касательной
к плоскости зуба) наконечник 2, который вместе ^ с измерительной кареткой * 1 перемещается вдоль контактной линии зубьев колеса 3. Накладные контакто-меры базируются на контролируемом зубчатом колесе, например на шейках ее вала с помощью призм.
Станковый прибор БВ-5028 (рис. 132,6) для установки колеса 3 имеет горизонтальные центры 5. По направляющей 4 измерительного узла 6 перемещается каретка 1 с наконечником 2. Направляющая 4 поворачивается на угол наклона контактной линии относительно оси колеса с помощью концевых мер длины 7. При перемещениях каретки I наконечник 2 фиксирует отклонения формы и направления контактной линии. Прибор оснащен самописцем и электронным блоком, который имеет шкалу для визуального наблюдения измерений.
Комплексным показателем полноты контакта зубьев является суммарное пятно контакта — часть боковой поверхности зуба колеса, на которой располагаются следы его прилегания к зубьям колеса. Полнота контакта определяется относительными размерами пятна контакта (рис. 133) по длине зуба: по высоте зуба:
Контроль осуществляется при обкатке проверяемого колеса и измерительного зубчатого колеса, установленных на контрольно-обкаточных станках или специальных стендах. Боковые поверхности измерительного колеса обезжиривают и покрывают слоем краски толщиной 4…6 мкм. При обкатке поверяемое колесо слегка тормозят, чтобы обеспечить непрерывность контакта зубчатых колес.
Контроль кинематической погрешности
Кинематической погрешностью называется разность между действительным и расчетным углами поворота зубчатого колеса, ведомого образцовым зубчатым
колесом. Измерение относительных углов поворота проверяемого и образцового колес осуществляется на приборах для комплексного однопрофильного контроля.
В приборе БВ-608к (рис. 134,а) проверяемое 1 и образцовое 4 зубчатые колеса, посаженные на соосных шпинделях 2 и 5, находятся в однопрофильном зацеплении с промежуточным образцовым колесом 3. Кинематическая погрешность проверяемого колеса приводит к отклонениям углов поворота шпинделей 2 и 5, которые воспринимаются индуктивным датчиком 6 и регистрируются в увеличенном масштабе на записывающем приборе.
Кинематическая погрешность F колеса определяется как расстояние по оси ординат между крайними точками графика, полученного при повороте колеса на один оборот (рис. 134,6). Местная кинематическая погрешность /, характеризующая плавность работы, определяется как наибольшая разность между соседними «зубцами» графика.
Прибор БВ-608к (рис. 134,в) имеет промежуточное колесо 5, установленное на каретке 1, которая перемещается маховиком 9 вдоль основания 10 и стопорится винтом 13. Соосные шпиндели для установки проверяемого 4 и измерительного 3 колес установлены на неподвижной каретке 2. Номинальное межцентровое расстояние между осями устанавливают по нониусу 11 шкалы 12. При измерении промежуточное колесо вращают вручную маховиком 8 или с помощью привода 7. Самопишущий прибор 6 вычерчивает график кинематической погрешности.
Средства и методы измерения шероховатости поверхности
Основные параметры шероховатости
Шероховатость поверхности (рис 135) —совокупность неровностей поверхности с относительно малыми шагами, выделенная на базовой длине За базовую линию, относительно которой оценивается шероховатость, принимается средняя линия профиля
которая проводится
ак, что в пределах базовой длины среднее квадратиче-ское отклонение профиля от этой линии минимально. Параметры шероховатости (ГОСТ 2789—73): —среднее арифметическое отклонение профиля;
— высота неровно-стей профиля по десяти точкам;
— наибольшая высота неровностей профиля;
— средний шаг неровностей;
—средний шаг местных выступов профиля;
—относительная опорная длина при значении
уровня сечения профиля, где
— число выбранных точек на базовой длине. Параметр
является предпочтительным.
Шероховатость поверхности можно контролировать путем сравнения с образцами шероховатости. Образцы
(рис. 136) представляют собой бруски 1 размером 30X20 мм Наборы образцов, укомплектованные по видам обработки (точение
фрезерование, шлифование, строгание) и материалам, из которых они изготовлены, собираются в оправах 2. Сравнение осуществляют визуально. Точность контроля повышается при использовании специальных микроскопов сравнения, которые позволяют одновременно рассматривать поверхность изделия и образец шероховатости.
Приборы контактного метода контроля
Контактные измерения шероховатости выполняются непрерывным ощупыванием поверхности изделия. Щуповые приборы делятся на профилометры, показывающие отдельные параметры шероховатости, как правило , и профилографы, записывающие профиль поверхности. По профилограмме определяются все параметры шероховатости.
При работе профилографа-профилометра с индуктивным датчиком (рис. 137,а) перемещение алмазной иглы 1 с радиусом закругления 2 мкм по проверяемой поверхности приводит к колебанию якоря 2, установленного на оси 3. При этом изменяется индуктивное сопротивление
датчика, состоящего из сердечника 4 и катушек 5 обмотки. Колебания напряжения на выходе дифференциального трансформатора 7, получающего питание от генератора звуковой частоты 6. усиливается электронным блоком 8. Прибор 9 показывает значение параметров шероховатости. Записывающее устройство 10 вычерчивает профилограмму.
Прибор 201 (рис. 137,6) имеет стойку 13 с кареткой, стол 3, датчик 4, привод 5, электронный блок 1 с отсчет-ным устройством 2, показывающим параметр Ra, и записывающий прибор 12. Прибор работает или как профилограф, или как профилометр. Переключение осуществляется ручкой 6. Привод грубо перемещается по стойке винтом 9 и тонко — винтом 7 и стопорится винтом 11. Поворотом рычага 8 влево до упора датчик переводится в исходное положение. Переключателем 10 изменяют скорость движения датчика. Изделие устанавливают в нужном положении относительно датчика 4 перемещениями стола.
Профилограф-профилометр 252 имеет электронный блок с цифровым отсчетным устройством, которое показывает значения параметров и
и дает возможность определить параметры
и
. Профилометры 240 и 253 предназначены для измерения параметра
.
Оптические приборы
Бесконтактные измерения шероховатости поверхности выполняют на оптических приборах. В микроскопах светового сечения МИС-11 (рис. 138,а) объектив 3 проецирует на поверхность изделия узкий пучок света, идущий от источника 1 через щель 2. На поверхности образуется освещенная полоса, представляющая собой след пересечения профиля плоскостью светового потока. Изображение щели фокусируется объективом 4 в плоскость сетки 5 окуляра 6. Лучи, отраженные от выступов и впадин профиля, иа окулярной сетке будут смещены один относительно другого. Значение смещения зависит от высоты неровностей. Совмещая линии, нанесенные на сетке окуляра-микрометра (рис. 138,6), с выступами и впадинами профиля, определяют высоту неровностей на базовой длине и затем подсчитывают параметр . Перед измерением определяют цену деления окулярного

микрометра с помощью стеклянной пластины с точной шкалой (объекта-микрометра).
Микроскоп МИС-11 (рис. 138,в), предназначенный для измерения шероховатости поверхности, имеет осве-
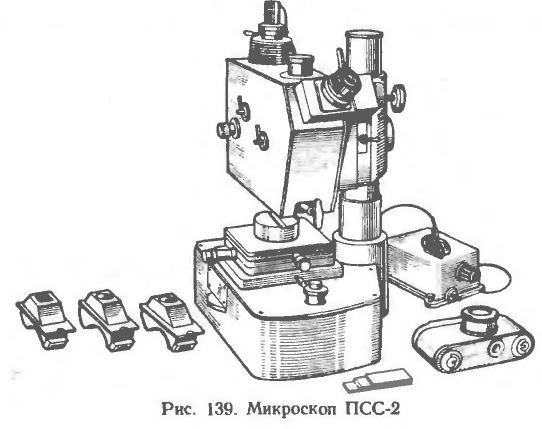
тительный тубус 7 и микроскоп 1, закрепленные в корпусе 4. Салазки корпуса перемещаются по кронштейну 6 кремальерой 5 для предварительной установки на резкость. Точная фокусировка осуществляется микроподачей 3. Винтом 9 изображение щели переводят на середину окуляра. Кольцом 8 регулируют ширину щели. Измерения выполняют окулярным микрометром 2. Стол 12 перемещается винтами 10 и поворачивается в горизонтальной плоскости при освобожденном винте 11.
Микроскоп ПСС-2 (рис. 139) в отличие от микроскопа МИС-11 имеет большее увеличение, снабжен комплектом встроенных объективов, содержит винтовой окулярный микрометр с внутренним отсчетом, сменные щели и встроенную фотокамеру. Он предназначен для измерения и фотографирования высоты микронеровностей на наружных поверхностях деталей.
Микроинтерферометры применяют для измерения шероховатости поверхности по параметрам и
. Оптическая схема (рис 140,а) представляет собой сочетание интерферометра и микроскопа. Свет из осветительного
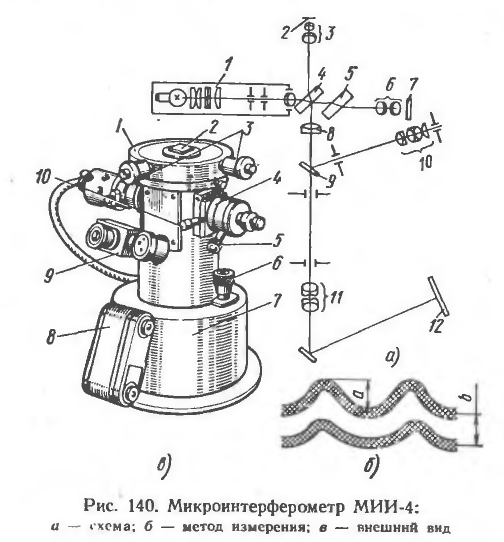
устройства 1 разделяется на пластине 4. Один световой поток проходит компенсационное стекло 5 и объектив б, отражается от зеркала 7 и возвращается к пластине 4. Другой поток света проходит объектив 3, и отразившись от поверхности изделия 2, тоже возвращается к пластине. Интерферирующий световой поток направляется объективом 8 через зеркало 9 в фокальную плоскость окуляра 10. Наблюдаемая интерференционная картина может быть сфотографирована с помощью объектива 11, который дает действительное изображение в плоскости 12. Зеркало 9 при этом выводят из хода лучей. Неровности поверхности приводят к искривлению интерференционных полос (рис. 140,6). Значения микро-неровностей измеряют по отношению высоты а искривления полос к ширине полос:
. По результатам измерений на базовой длине вычисляют параметр
. Для определения параметра
фотографируют интерференционную картину и обрабатывают фотографию на проекторе.
Микроинтерферометр МИИ-4 (рис. 140,в) имеет массивное основание 7, на которое установлен стол 1 с микрометрическими винтами 3. Изделие 2 укладывают на стол проверяемой поверхностью вниз. Винтом 6 фокусируют прибор. Поворотом корпуса 4 и винта 5 изменяют ширину и направление интерференционных полос. Головка 10 закрывает интерференционное зеркало шторкой, что позволяет рассматривать поверхность без интерференции. Искривление интерференционных полос измеряют окулярным микрометром 9. Камера 8 служит для фотографирования.
Иммерсионно-репликовый микроинтерферометр МИИ-10 по принципу действия и устройству аналогичен микроинтерферометру МИИ-4. Благодаря применению особой конструкции узла референтного (неподвижного) зеркала и двух осветительных систем прибор позволяет проводить обычные измерения высоты неровностей и измерения неровностей реплик (отпечатков), снятых с деталей на прозрачную пленку, помещаемую в специальную камеру с иммерсионной жидкостью для усиления яркости и расширения пределов увеличения изображения. Иммерсионно-репликовым микроинтерферометром можно измерять неровности высотой 1…10мкм.
Средства и методы измерения отклонений от формы цилиндрических поверхностей
Форма цилиндрических поверхностей характеризуется цилиндричностью, круглостью и профилем продольного сечения.
Отклонение от цилиндричности — наибольшее расстояние от точки реальной поверхности 2 до прилегающего цилиндра 1 (рис. 141,а). Отклонение от круглости — наибольшее расстояние от точки реального про-
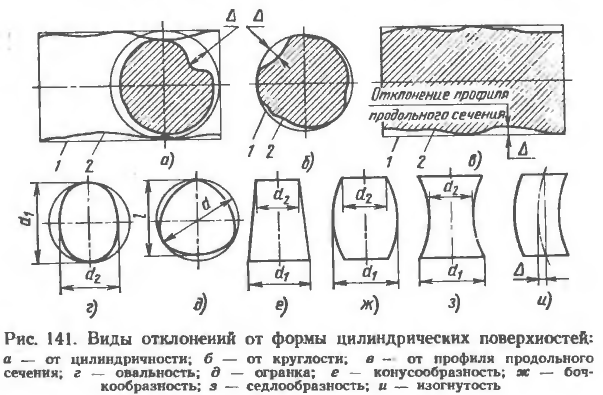
филя 2 до прилегающей окружности 1 (рис. 141,6). Отклонение профиля продольного сечения — наибольшее расстояние от точек реального профиля 2 до соответствующей стороны прилегающего профиля 1 (рис 141,в). Прилегающий профиль продольного сечения цилиндрической поверхности — две параллельные прямые, соприкасающиеся с реальным профилем и расположенные вне материала так, что наибольшее отклонение точек образующей реального профиля от соответствующей стороны прилегающего профиля имеет минимальное значение. Отклонения профиля продольного сечения характеризуют отклонения образующих цилиндра от прямолинейности и параллельности.
Частными видами отклонения от круглости являются овальность (рис. 141,г) , когда профиль представляет собой фигуру, у которой наибольший и наименьший диаметры взаимно перпендикулярны, и огранка (рис. 141,(9)
, когда профиль представляет собой многогранную фигуру. Огранка подразделяется по числу граней; при нечетном числе граней диаметры профиля поперечного сечения во всех направлениях одинаковы.
К частным видам отклонений от профиля продольного сечения относятся конусообразность (рис. 141,е), если образующие прямолинейны, но не параллельны, бочкообразность (рис. 141,ж), если образующие непрямолинейны и диаметры увеличиваются от краев к середине сечения, и седлообразность (рис. 141,з), если образующие непрямолинейны и диаметры уменьшаются от краев к середине. Количественно эти виды отклонений оцениваются так же, как отклонение профиля продольного сечения .
В некоторых случаях для оцеики отклонений формы цилиндрических поверхностей в осевом направлении можно применять отклонение от прямолинейности оси — наименьшее значение диаметра, внутри которого располагается реальная ось поверхности вращения в пределах нормируемого участка- Примером такого типа отклонений формы является изогнутость (рис. 14I,u).
Методы измерения отклонений
Отклонения от формы цилиндрических поверхностей измеряют на специальных приборах — кругломерах,
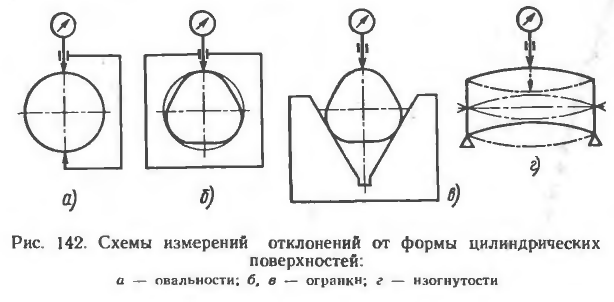
а также с помощью универсальных средств линейных измерений и приспособлений.
Овальность определяют по наибольшей разности диаметров в двух взаимно перпендикулярных направлениях. Изделие (вал) поворачивают между измерительными поверхностями универсального прибора (микрометра, рычажной или индикаторной скобы) или на столе вертикальной стойки под наконечником измерительной головки (рис. 142,а) до получения наибольшего или наименьшего показаний. Затем вал поворачивают на 90° и выполняют второй отсчет. Овальность равна полуразности показаний прибора. Овальность отверстий находят аналогично с помощью нутромеров.
Огранку с нечетным числом граней измеряют при установке вала в призме или кольце трехконтактным методом, при котором две точки профиля изделия соприкасаются с опорой, а одна точка — с наконечником прибора. При вращении вала в кольце (рис. 142,6) определяют значение огранки как наибольшую разность показаний индикатора. При определении огранки путем вращения вала в призме (рис. !42,в) используют зависимость, связывающую значение огранки с наибольшей разностью показаний индикатора , где
— коэффициент воспроизведения огранки, числовые значения которого приведены в табл. 11. Для измерений следует выбирать призму с углом, который обеспечивает наибольшее значение
.
Конусообразность определяют по диаметрам изделия, измеренным по краям продольного сечения, а бочко-
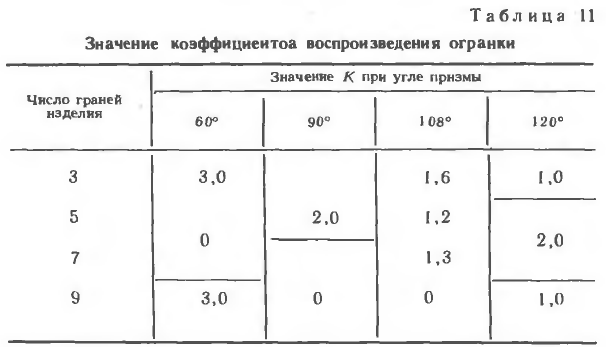
образность и седлообразность — по краям и в середине. Изогнутость измеряют при вращении детали на двух опорах под наконечником индикатора (рис. 142,г) Значение изогнутости равно полураэности наибольшего и наименьшего показаний индикатора. Для измерений отклонений от имлиндричности используют разнообразные приспособления с индикаторами.
По наибольшему допускаемому значению отклонения формы — допуску формы, цилиндрические поверхности, так же как плоские, делятся на 16 степеней точности. Измерительные средства выбирают в зависимости от степени точности. Например, вал с номинальным значением диаметра 100 мм и поверхностью 4-й степени точности должен иметь допуск формы не более 4 мкм. Для измерений может быть использован оптиметр OBO-I с ценой деления 0,001 мм.
Кругломеры
Кругломеры, предназначенные для измерения отклонения от круглости, основаны на принципе образцового вращения измерительного наконечника относительно изделия или наоборот. При измерении происходит непрерывное ощупывание цилиндрической поверхности по окружности. Кругломеры выпускают двух типов: КН — с вращающимся измерительным наконечником; КД — с вращающимся изделием.
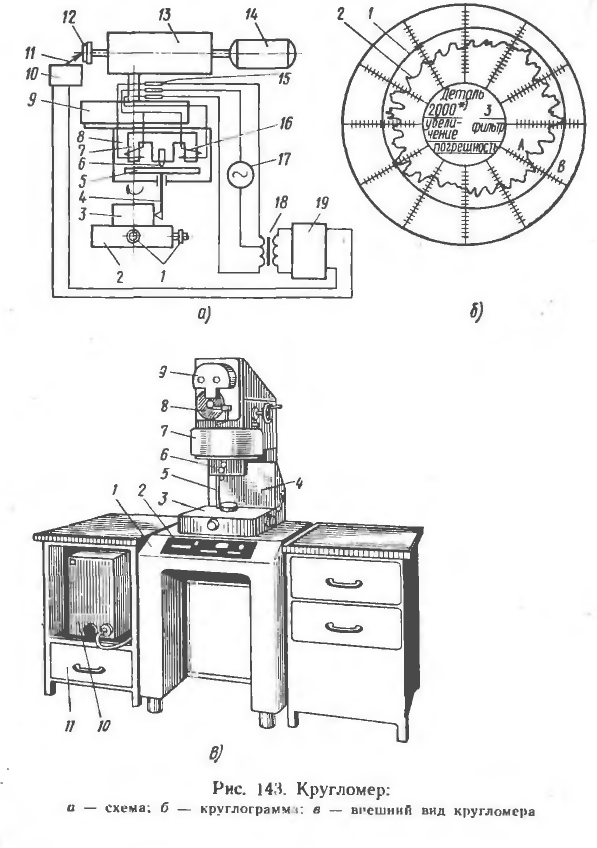
У кругломера с вращающимся наконечником (рис. 143,а) проверяемое изделие 3 установлено на предметном столе 2 Стол перемешается в двух взаимно перпендикулярных направлениях микрометрическими головками 1. Прецизионный шпиндель 9, ось которого имеет радиальные биения порядка сотых долей микрометра, приводится во вращение приводом 14 через коробку скоростей 13. На шпинделе закреплен индуктивный датчик 8 со щупом 4. При вращении шпинделя измерительный наконечник щупа скользит по поверхности изделия и вызывает колебания щупа вследствие отклонений формы изделия. В результате происходят колебания якоря 5 относительно опоры 6, изменяющие зазор между якорем и сердечником 7 индукционных катушек 16, которые через вращающиеся токосъемные кольца 15 со щетками связаны с первичной обмоткой трансформатора 18.
Питание электрической схемы осуществляется генератором звуковой частоты 17. Колебания зазора между якорем и сердечником приводят к изменению напряжения на выходе трансформатора. Сигнал усиливается электронным блоком 19 и подается на записывающее устройство 10. Запись осуществляется пером 11 на бумаге, закрепленной на электротермическом диске 12. вращающемся синхронно со шпинделем. После одного оборота диска на бумаге записывается круглограмма проверяемого поперечного сечения изделия.
На круглограмме (рис. 143,6) нанесено 12 радиусных линий со штрихами, интервал между делениями состав ляет 2 мм. Цена деления круглограммы зависит от увеличения прибора и типа наконечника Например, при увеличении 2000х цена делений равна 0,001 мм. В центре круглограммы указывается увеличение прибора, номер электрического фильтра и погрешность. Электрические фильтры позволяют изменять частоту неровностей поверхности, записываемых на круглограмме.
Для определения круглости на круглограмму наносят прилегающую окружность /, касающуюся выступающих точек записанного профиля 2. Отклонение от округлости равно наибольшему расстоянию по радиусу от круглограммы до прилегающей окружности. На рис. 143,6 наибольшее расстояние делений шкалы, а отклонение от круглости поверхности при цене делений 0,001 мм равно 6,6 мкм. При работе используют прозрачные шаблоны с концентрическими окружностями. нанесенными через 2 мм, и радиальной шкалой Шаблоны накладывают на круглограмму, что позволяет быстро определить прилегающую окружность и оценить отклонение от круглости.
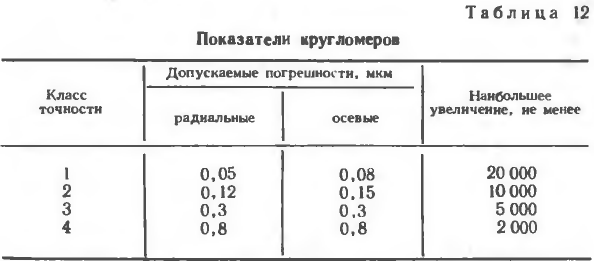
Кругломеры обеспечивают контроль изделий с верхним пределом наружных и внутренних диаметров проверяемых поверхностей 100, 160, 250, 400, 630 и 1000 мм. Нижний предел внутреннего диаметра составляет не менее 3 мм. Кругломеры изготовляют четырех классов точности (табл. 12) Кругломер 255 (рис. 143,в) широко применяется в промышленности. Станина прибора состоит из основания 1 и колонны 4; она служит для размещения панели управления 2 и всех механических узлов: предметного стола 3, шпинделя 7 с датчиком 6 и щупом 5, шпиндельной коробки с приводом Р и записывающего устройства 8. Электронный блок 10 установлен в тумбочке 11.
Проверяемое изделие устанавливают в центре стола симметрично концентрическим окружностям, нанесенным на его поверхности. Щуп датчика приводят в соприкосновение с изделием и перемещениями стола центрируют изделие, вращая шпиндель сначала вручную, а затем от привода. Перед измерением переключают частоту вращения шпинделя на 15 об/мин, устанавливают нужное увеличение прибора и требуемый фильтр. Закрепляют диаграммный диск в записывающее устройство и перо выводят на середину. Для снятия круглограммы нажимают кнопку «запись> на панели управления 2. Запись автоматически отключается, когда шпиндель совершит один оборот. Сняв круглограмму, осуществляют ее обработку.
Приборы для измерения твердости металлов
Твердомеры бринелля
Твердость — сопротивление материала внедрению в его поверхность стандартного наконечника, который представляет собой твердое малодеформирующееся тело (алмаз, твердый сплав, закаленная сталь) определенной формы (шар, конус, пирамида, игла) и размеров Микро-твердость— твердость отдельных зерен, физических и структурных составляющих материала.
Для измерения твердости предложено много методов. Основными являются методы вдавливания нако-
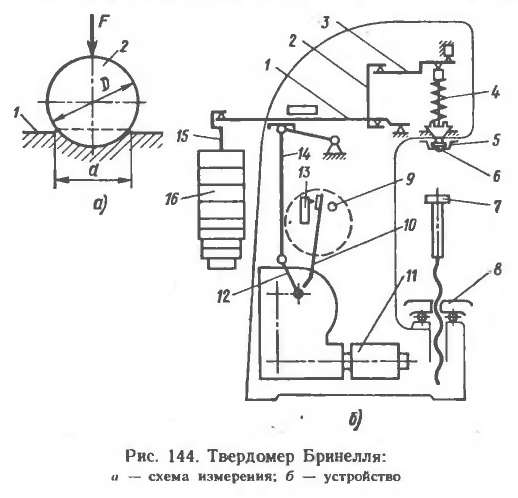
мечников в материал под действием статических нагрузок: 1) Брииелля; 2) Роквелла; 3) Виккерса. Значение твердости металлов, измеренное разными методами, выражается числами твердости в различных шкалах.
Сущность метода Бринелля (рис. 144,а) заключается во вдавливании стального шарика 2 диаметром под действием силы
, приложенной перпендикулярно к поверхности образца 1, в течение определенного времени и в измерении диаметра
отпечатка после снятия нагрузки. Твердость по шкале Бринелля
— отношение силы
к площади сферического отпечатка. Она зависит от диаметра шарика, значения нагрузки и времени
ее действия.
Диаметр отпечатка измеряют в двух взаимно перпендикулярных направлениях с помощью микроскопа или других приборов с погрешностью измерения диаметра шарика, например, микроскопа МПБ-2. Число твердости (ЧТ) находят с помощью специальных таблиц по значениям
,
и
или вычисляют по формуле

где если
выражена в Ньютонах;
и
выражены в миллиметрах.
При измерении твердости величины ,
и
устанавливают в зависимости от числа твердости и толщины
образца, которая должна быть в 10 раз больше глубины
отпечатка. Диапазоны изменения параметров испытаний: силы
. диаметра шарика
, времени действия
. Значение температуры испытаний
.
При нормальных условиях испытаний твердость по Бри-неллю обозначается числом твердости и буквами НВ, например, 185 НВ. Другие условия испытаний указываются после букв НВ в следующем порядке:
например, обозначению 185 НВ 5/750/20 соответствуют
. Метод Бринелля используют для металлов с твердостью не более, чем 450 НВ.
В приборе ТШ-2М для измерения твердости металлов по шкале Бринелля (рис. 144,6) проверяемый образец устанавливают на стол 7 и вращением маховика 8 поднимают к шариковому наконечнику 6 до упора в ограничитель 5. Затем нажимают пусковую кнопку 9 и включают привод 11. Кривошип 12, поворачиваясь, опускает шатун 14 и освобождает рычажную систему 1, 2, 3, на конце которой закреплена подвеска 15 со съемными грузами 16. Груз давит на шпиндель 4 и шариковая оправка 6 внедряется в образец. Кривошип 12 поворачивается до тех пор, пока упор 10 не коснется микропереключателя 13 и не изменит вращение привода на обратное. Затем рычажная система возвращается в исходное положение. После испытания стол опускают и измеряют диаметр отпечатка.
Твердомеры Роквелла
Сущность метода Роквелла (рис. 145,а) заключается во вдавливании в поверхность образца наконечника стандартного типа и в измерении глубины его проникновения в металл. Наконечник вдавливается в два последовательных приема: сначала на него действует предварительная сила , затем к нему прикладывается дополнительная сила
. Твердость по шкале Роквелла
— разность между условной глубиной внедрения и глубиной проникновения
наконечника после снятия дополнительной силы
, при сохранении
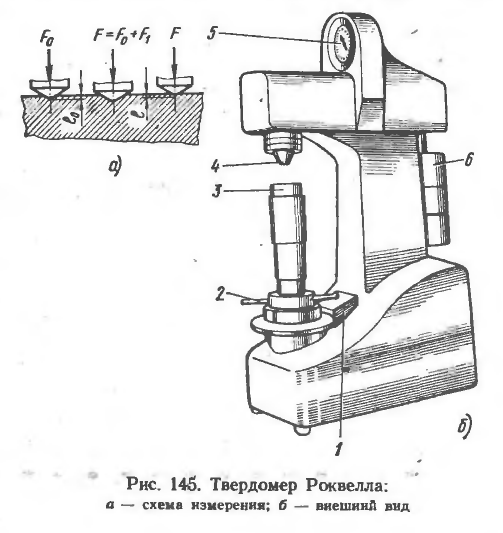
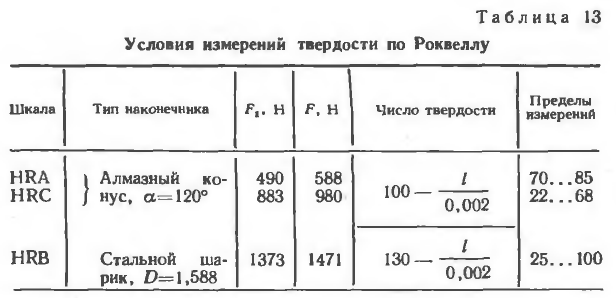
предварительной силы . Зависимость между числом твердости и значением
(мм) дана в табл. 13.
В зависимости от типа наконечника и значения силы твердость по методу Роквелла измеряется по трем шкалам
и обозначается числом твердости и буквами, указывающими шкалу. Например, обозначению 60
соответствует твердость 60 по шкале
.
При измерении твердости металлов по методу Роквелла на приборе ТК-2М (рис. 145,6) стол 3 с изделием поднимают вращением маховика 2 и прижимают изделие к наконечнику 4 до тех пор, пока малая стрелка индикатора 5 не встанет против красной точки, а большая на нуль. Этим обеспечивается предварительная нагрузка . Плавным нажатием на клавишу 1 включают привод механизма нагрузки. Под действием груза 6 наконечник внедряется в металл. Затем нагрузку снимают и грузовой рычаг отводят в исходное положение. Циферблат индикатора, по которому отсчитывают число твердости, имеет две шкалы: черную для измерений алмазным конусом и красную для измерений стальным шариком.
Измерения твердости по методу Рокаелла при малых нагрузках называют методом Супер-Роквелла. При измерениях по шкале
(твердость
) используют алмазный конус, а по шкале
(твердость
) —стальной шарик.
Измерение микротвердости
Микротвердость измеряют при небольших размерах изделия (у тонких металлических лент и покрытий.
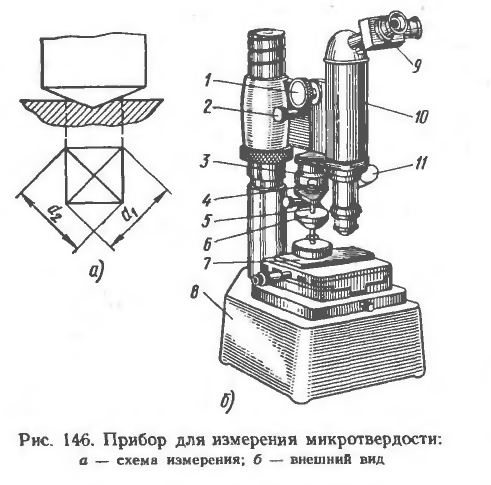
фольги, проволоки, поверхностных слоев металла, мелких изделий и т. п.), прижимая с очень незначительной силой к поверхности изделия алмазные наконечники различной формы. Основной метод «восстановленного отпечатка» заключается в использовании наконечника, имеющего форму четырехгранной пирамидки с квадратным основанием, и в измерении диагоналей отпечатка
и
с помощью микроскопа (рис. 146,а). Этот метод аналогичен методу измерения твердости по шкале Виккерса
, при котором силы составляют
.
Число микротвердости (ЧМТ) по шкале — отношение силы
к условной площади боковой поверхности отпечатка. Его находят с помощью таблиц по значениям
и
или вычисляют по формуле

где если сила выражена в ньютонах;
и
выражены в миллиметрах.
Микротвердость обозначают числом микротвердости и буквами с указанием нагрузки в килограммах силы и времени ее приложения, если время отличается от 10…15 с. Например, обозначению
соответствуют
Прибор ПМТ-3 для испытания микротвердости материалов (рис. 146,6) представляет собой микроскоп 10, установленный на стойке 8. Микроскоп имеет окулярный микрометр 9, осветитель 11 и нагружающий механизм 3. Изделие, установленное на столе 7, подводят под наконечник с алмазной пирамидкой. Рабочую гирьку 6 надевают вырезом на стержень 5. Поворотом ручки 4 опускают измерительный наконечник на поверхность изделия и выдерживают не менее 3 с. Затем нагрузку снимают той же ручкой 4.
Перемещением стола изделие подводят под объектив микроскопа, который наводят на резкость грубо кремальерой 1 и тонко микрометрическим винтом 2. Диагонали отпечатка измеряют окулярным микрометром 9.
Средства контроля режущего инструмента
Средства контроля углов резцов
Резец — наиболее распространенный режущий инструмент, применяемый при обработке материалов со снятием стружки. Конструкции резцов многообразны. Проходной резец (рис. 147,а) имеет головку 1 — рабочую часть и стержень 2, который крепится в резцедержателе.
Геометрия головки резца определяется главным и вспомогательным
углами в плане, углом
заострения клина 3, передним углом
режущей грани 4 и задним углом а грани 5. Углы
определяющие геометрию резцов,
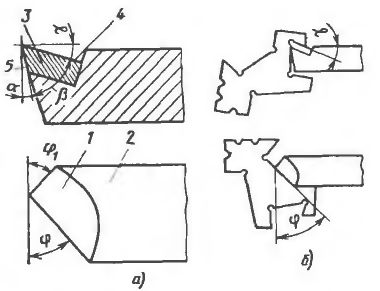
измеряют универсальными и специальными угломерами и плоскими шаблонами. На рис. 147, б показан контроль переднего угла и главного угла
в плане плоским комбинированным шаблоном. Примеры измерений с помощью универсального угломера УН (см. § 28) показаны на рис. 148.
Маятниковый угломер ЗУРИ предназначен для измерения углов режущего инструмента (рис. 149). Угломер имеет корпус 2 с опорной линейкой 1. Внутри корпуса на свободно вращающуюся ось 9 насажены тормозная шайба 3 и стрелка 8 с грузом-отвесом 10 на конце. На диске 7 нанесена круговая шкала с ценой деления 2е. Шкала разбита на четыре участка от 0 до 90°. Тормоз 4 обеспечивает фиксацию оси со стрелкой в любом положении. Стекло 6 закрывает шкалу и стрелку. При измерении режущий инструмент устанавливают боковой поверхностью на плиту, выверенную по горизонтали с помощью уровня. Угломер накладывают опорной линейкой

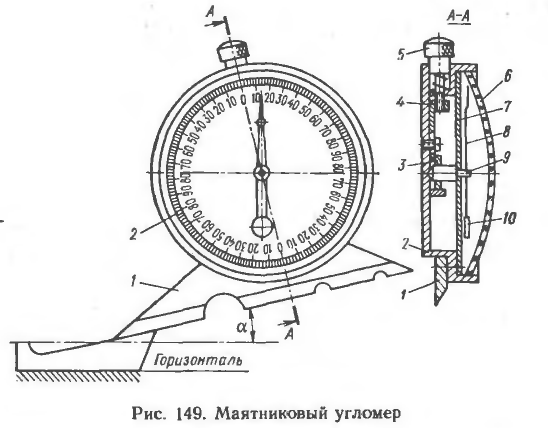
на проверяемую поверхность и освобождают стрелку нажатием тормозной кнопки 5. Когда стрелка установится в вертикальном положении под действием отвеса, тормозную кнопку отпускают и выполняют отсчет. Основная погрешность показаний равна ±1°
Приборы для контроля параметров сверл, зенкеров. Протяжек и метчиков
Сверло — режущий инструмент, предназначенный для получения отверстий в сплошном материале. Режущая часть сверла (рис. 150) состоит из главных режущих кромок, расположенных под двойным углом в плане симметрично относительно оси. Передний и задний углы режущих кромок изменяются в процессе резания. Углы заточки режущих кромок проверяют специальным шаблоном. Совпадение грани шаблона 2 с режущей кромкой сверла 4 оценивают «на просвет»; одновременно определяют длину режущей кромки по шкале 3 шаблона. Длины режущих кромок должны быть одинаковыми, иначе сверло будет разбивать отверстие. Если сверло / имеет две заточки, то углы заточек контролируют поочередно обеими сторонами шаблона.
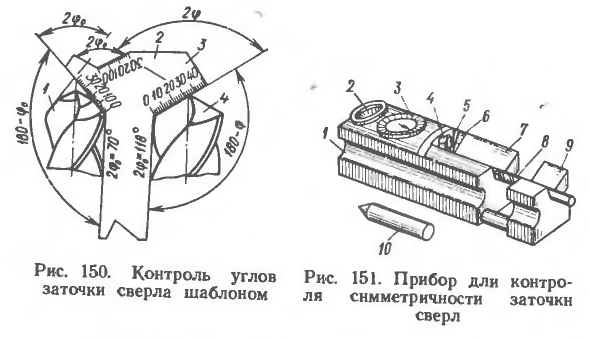
Прибор ПКС (рис. 151) предназначен для контроля симметричности заточки сверл диаметром 6…65 мм. Прибор имеет корпус 1, на котором расположена угловая шкала 2 для измерения отклонений от половины угла при вершине сверла и индикатор 3, предназначенный для измерения осевого биения режущих кромок. Сверло 8 устанавливают на основную базирующую призму 7, укрепленную на корпусе, и на подвижную призму Р. Расстояние между подвижной призмой и корпусом регулируют в зависимости от длины сверла. Кли-новый упор 6 служит для ориентации сверла. При установке сверло должно упираться в поворотный упор 4, овязанный со стрелкой угловой шкалы, и в упор 5, закрепленный на измерительном стержне индикатора. Сверло фиксируют в призмах с помощью откидного прижима.
Угловая шкала имеет цену деления Г и пределы измерений ±8°. Пределы измерения индикатора с ценой деления 0,01 мм составляют 0…10 мм. Основная погрешность показаний прибора при контроле отклонения от половины угла при вершине ие превышает 1°. Прибор снабжен мерой 10 для проверки правильности угловой шкалы.
Угломер 2УРИ предназначен для измерения передних и задних углов заточки многолезвийного инструмента с равномерным шагом зубьев от 5 до 75 мм — зенкеров, протяжек, фрез и т. п. Погрешность измерения равна 1°. Угломер (рис. 152,а) состоит из сектора 1 с градусной
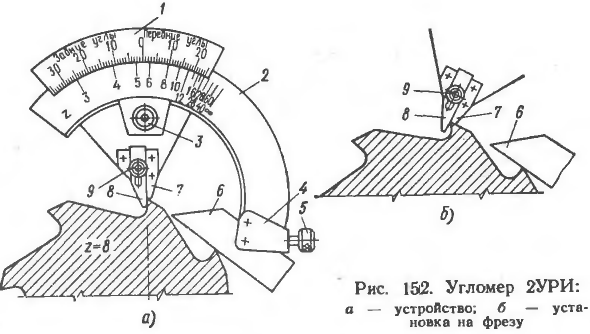
шкалой и дуги 2 с неравномерно нанесенными штрихами Правая часть градусной шкалы служит для измерения передних углов в пределах 0…250, левая часть шкалы — задних углов в пределах 0…350. На секторе 1 закреплена планка 7, в пазах которой перемещается измерительная линейка 8, зажимаемая винтом 9. На правом конце дуги 2 в держателе 4 винтом 5 зажимается опорная линейка 6. Угломер устанавливают рабочими гранями планки 7 и опорной линейки 6 на вершины двух соседних зубьев инструмента. При измерении переднего угла заточки сектор поворачивают до совпадения грани линейки 8 с передней гранью зуба. При измерении заднего угла грань планки 7 должна совпасть с задней гранью зуба (рис. 152,6). В установленном положении сектор стопорят винтом 3. Углы заточки отсчитывают относительно штриха, соответствующего числу зубьев проверяемого инструмента. Так, если число зубьев фрезы
(см. рис. 152,а), то передний угол заточки равен 10°. При измерении протяжек отсчет выполняют относительно штриха с индексом
.
Прибор РМ (рис. 153), предназначенный для контроля среднего диаметра метчиков от 3 до 33 мм, имеет цену деления 0,01 мм и основную погрешность показаний не более ±0,02 мм. В корпусе 13 установлен индикатор 14, стержень которого через рычаг 11, поворачивающийся на оси 12, связан с подвижной скалкой 8. В скалку устанавливается призматическая вставка 7. Пружина 9 создает измерительное усилие. В корпусе
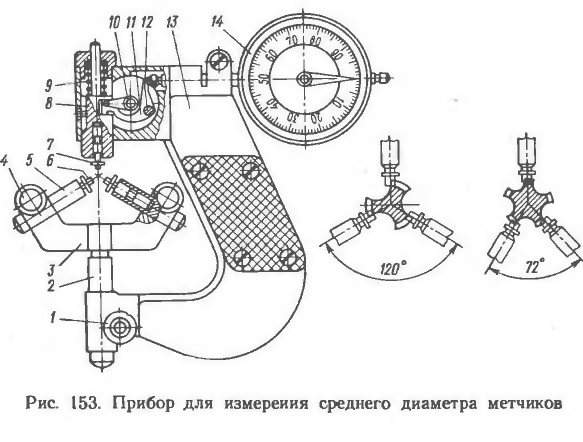
винтом 1 крепится переставная ножка 2 с вилкой 3, на которой гайками 4 зажимаются валики 5 с клиновыми вставками 6. К прибору прилагаются шесть комплектов вставок для резьб с различными шагами. Перед измерением валики 5 устанавливают на вилке 3 по делениям, нанесенным на валиках так, чтобы оси вставок 6 пересекались на оси подвижной скалки. Прибор приводят в рабочее положение по аттестованному метчику или резьбовому калибр-пробке. Подняв скалку 8 рукояткой рычага 10, на нижние вставки укладывают впадинами образцовое изделие и затем опускают призматическую вставку на вершину витка резьбы. Индикатор устанавливают на нуль в тот момент, когда при легком покачивании и поворачивании калибра его показания будут минимальными. При измерении среднего диаметра метчики устанавливают так, чтобы оси вставок проходили через их режущие кромки. При небольшом покачивании метчика отсчитывают наибольшие показания индикатора. Средний диаметр определяют по формуле , где
— средний диаметр образцового изделия;
— показания индикатора
;
—коэффициент для трехканавочного метчика;
— коэффициент для пятиканавочного метчика.
Методы и средства автоматического контроля размеров в машиностроении
Механизация производства — замена ручных средств труда машинами и механизмами, работающими от различных источников энергии — электрической, гидравлической, пневматической. Частичная механизация охватывает наиболее трудоемкие производственные операции при сохранении значительной доли ручного труда, особенно на вспомогательных разгрузочно-погру-зочных и транспортных операциях. Например, обработка деталей на станках с ручной подачей инструмента — резание, сверление.
При комплексной механизации машины и механизмы применяются на всех основных технологических операциях и вспомогательных работах, кроме отдельных нетрудоемких операций: человек контролирует и управляет производством. В машиностроении к техническим средствам механизации относятся станки для различных видов механической обработки, оборудование для сварки, термообработки, литья, окраски изделий и т. п. Для механизации вспомогательных работ применяются конвейеры, транспортеры, подъемные устройства, пневмотранспорт и т. п. Для комплексной механизации процессов механической обработки в массовом производстве предназначены агрегатные и специализированные станки, станки-автоматы и полуавтоматы, станки с числовым программным управлением, поточные линии. Для механизации измерений используются универсальные приспособления для приемочного контроля, различные приборы и устройства.
Автоматизация производства заключается в передаче управления производством и контроля за ним приборам и автоматическим устройствам. Частичную автоматизацию применяют на отдельных технологических операциях для полного освобождения человека от тяжелой, профессионально вредной, монотонной или недоступной ввиду сложности и быстротечности работы. Комплексная автоматизация — создание из технологического и вспомогательного оборудования автоматических линий, участков, цехов и заводов, работающих как единый комплекс. Функции человека при этом ограничиваются техническим обслуживанием и общим управлением работой комплекса. Полная автоматизация — высшая ступень автоматизации, при которой все функции контроля и управления производством выполняются автоматическими системами управления (АСУ).
Автоматизация основной части машиностроительного производства оставляет человеку выполнение лишь несложных, но однообразных и утомительных вспомогательных ручных операций типа подать, закрепить, снять деталь и др. Промышленный робот — стационарная или передвижная автоматическая машина для выполнения двигательных и управляющих функций, аналогичных функциям человека, при перемещении предметов производства и технологической оснастки. В общем случае робот состоит из исполнительного устройства — манипулятора, имеющего несколько степеней подвижности, и перепрограммируемого устройства программного управления — автоматического, дистанционного или ручного.
Классификация средств автоматического контроля
При автоматическом контроле функции оператора выполняются механизмом измерительного прибора. Средства автоматического контроля в машиностроении по способу связи и воздействию на производственный процесс делятся на следующие группы: 1) средства активного (технологического) контроля, предназначенные для измерения деталей и соответствующей корректировки технологического процесса; 2) средства пассивного (приемочного) контроля для измерения и сортировки готовых деталей; автоматических изменений в работе технологического оборудования не происходит; 3) универсальные приспособления для технологического и приемочного контроля; 4) координатно-измерительные машины для измерения деталей сложной формы, обработки результатов измерений и выдачи информации.
Средства контроля по степени автоматизации подразделяются на следующие виды: 1) визуальные приборы со стрелочным или цифровым отсчетом; 2) механизированные приборы со световой или звуковой сигнализацией; 3) приборы с автоматической обработкой результатов измерения; 4) полуавтоматы; 5) автоматы; 6) измерительно-контрольные системы и комплексы.
Основными элементами средств автоматического контроля являются датчики (измерительные преобразователи) и усилительные, загрузочные, транспортирующие, запоминающие и исполнительные устройства. В зависимости от типа автоматического контроля эти устройства могут входить в конструкцию приборов в различных сочетаниях.
Измерительные датчики
Измерительные датчики воспринимают изменение измеряемого параметра и вырабатывают сигнал измерительной информации в форме, удобной для передачи и дальнейшего преобразования. По принципу действия датчики линейных и угловых измерений, используемые в машиностроении, делятся на электроконтактные, индуктивные, пневматические, емкостные, фотоэлектрические, механотронные, пневмоэлектроконтактные, радиоизотопные, пьезоэлектрические, гальваномагнитные и др.
Принцип действия электроконтактных датчиков заключается в изменении электрического сопротивления в измерительной цепи при замыкании контактов датчика. По методу контроля они делятся на предельные датчики, предназначенные для контроля наибольших и наименьших размеров изделий, и амплитудные датчики, предназначенные для контроля отклонения от формы цилиндрических изделий и взаимного расположения
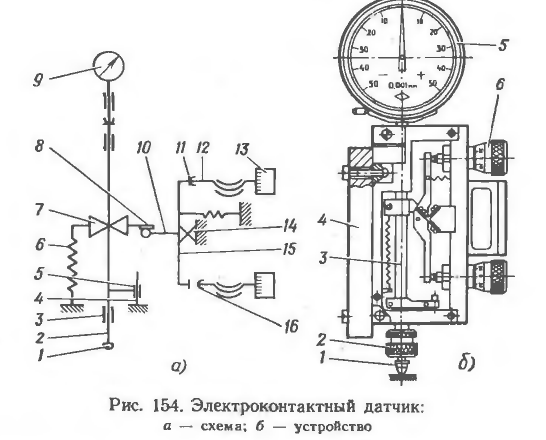
поверхностей, например, овальности, биения, огранки и т. п. По конструкции различают датчики рычажные и безрычажные, с регулируемыми и нерегулируемыми контактами, а по количеству измеряемых размеров — одно- и многопредельные.
В электроконтактном двухпредельном датчике с рычажным механизмом (рис. 154,а) в бронзовых направляющих втулках 3 перемещается шток 2, на который навернут измерительный наконечник 1. Хомутик 5 с регулируемым пазом ходит вдоль штифта 4 и предохраняет шток от поворота. На штоке закреплен хомутик 7 с твердосплавной пяткой 8. Измерительное усилие создается пружиной 6. В корпусе крепится измерительная головка 9 типа 1МИГ или 1ИГ, которая используется при установке датчика на нуль. На корпусе также закреплены пружинный крест 14 и винты 12 с микрометрическими головками 13. На кресте 14 установлен рычаг 15 с подвижными вольфрамовыми контактами 11, а в винтах 12 запрессованы неподвижные контакты 16. Через твердосплавную пятку 8, которая упирается в корундовый штифт 10, запрессованный в рычаг 15, шток при перемещении вызывает угловое отклонение рычага 15 и замыкание или размыкание контактов, которые соединены с источником электрического тока и усилителем электрического импульса.
Для установки датчика (рис. 154,6) на нуль наконечник 1 помещают на меру или образцовое изделие. Микрогайкой 2 перемещают шток 3, который упирается в торец измерительной головки 5, закрепленной в отверстии корпуса 4, имеющего форму скобы. Для настройки контактов датчика на предельные размеры изделия используют микрометры 6, регулирующие расстояние между неподвижными контактами.
При замыкании контактов датчика в процессе измерений электрический сигнал поступает к исполнительному механизму.
Для усиления, запоминания и размножения сигналов от предельных и амплитудных датчиков применяются электронные усилители реле, которые включают исполни-
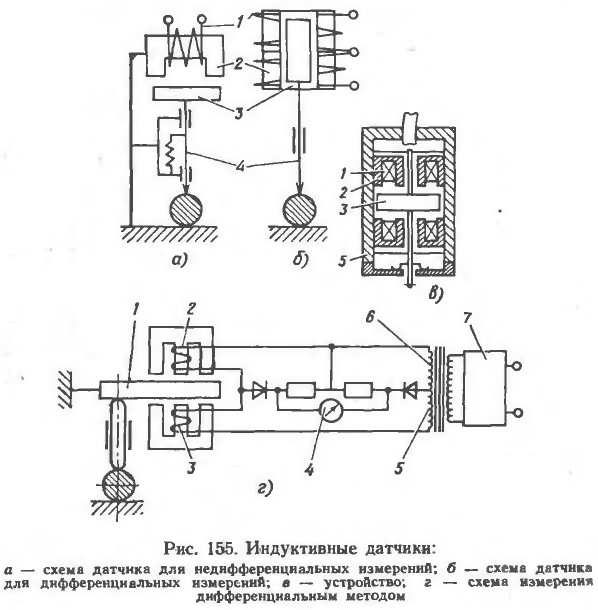
тельный механизм, например световую или звуковую сигнализацию.
Принцип действия индуктивных датчиков (рис. 155,а, б) заключается в изменении индуктивного сопротивления катушки 1, намотанной на магнитопро-вод 2, при перемещении якоря 3, который связан с измерительным стержнем 4. В большинстве случаев детали преобразователя расположены в корпусе 5 (рис. 155,в), который защищает от внешних помех. Датчики для измерений дифференциальным методом (рис. 155,6, в) имеют две катушки: при увеличении индуктивности одной катушки индуктивность второй катушки уменьшается, что повышает чувствительность прибора. Датчики работают совместно с электронным блоком с отсчетным устройством. При индуктивном методе измерений (рис. 155,в, г) отклонения якоря I приводят к разбалансу электрического моста, образованного катушками 2, 3, 5 и 6, получающего питание от стабилизированного генератора 7 звуковой частоты. В результате в диагонали моста возникает ток, направление которого определяется направлением перемещения измерительного стержня из среднего положения. Отсчетный прибор 4 показывает значение отклонений размера.
В емкостных датчиках (рис. 156) линейные или угловые перемещения преобразуются в изменения емкости электрической цепи: датчик является электрическим конденсатором с переменной емкостью. Изменение емкости может происходить за счет изменения зазора между неподвижной обкладкой / и подвижной обкладкой 2, связанной с измерительным стержнем 3, или за счет изменения площади перекрытия обкладок. Датчики могут иметь плоские и цилиндрические поверхности обкладое.
В фотоэлектрических даточиках в качестве чувствительных органов используются фотоэлементы. Конструкции этих датчиков разнообразны. Практическое применение в средст-
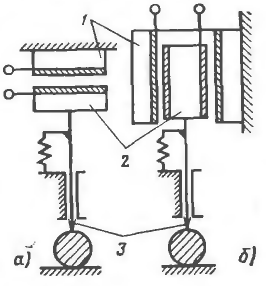
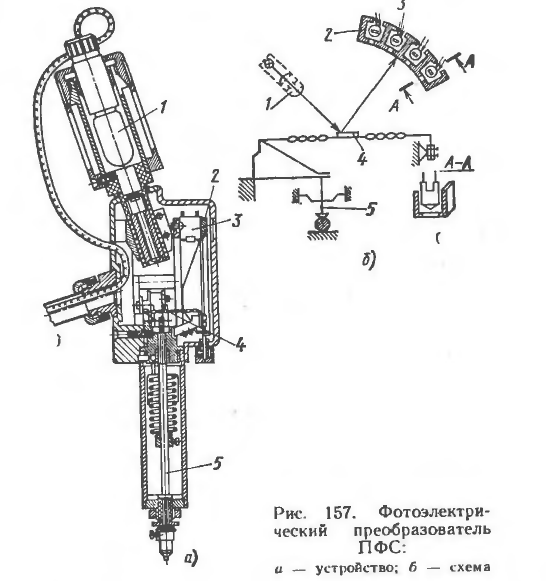
вах автоматического контроля получили преобразователи, фиксирующие наличие или отсутствие светового излучения, т. е. фотореле.
Фотоэлектрический пружинный преобразователь ПФС (рис. 157,а) предназначен для контрольно-сортировочных автоматов. Световой поток (рис. 157,6) от осветителя 1 узкой полосой направляется на зеркало 4, закрепленное на ленточной пружине. Конструкция механизма датчика аналогична конструкции оптикатора (см. § 41). Световой поток, отражаясь от зеркала, одновременно освещает один из фото резисторов 3 и шкалу прибора. Фоторезисторы расположены в корпусе 2 со щелями, что повышает чувствительность прибора. При изменении положения измерительного штока 5 меняется номер освещаемого фоторезистора в соответствии с размером изделия. Электрическое сопротивление фоторезистора при освещении резко уменьшается. При этом в цепи возрастает сила тока, срабатывает реле исполнительного механизма и происходит замыкание контакта запоминающего устройства.
Универсальные приспособления для приемочного контроля
Для приемочного контроля размеров деталей широко используются механизированные приспособления. Универсальные приспособления представляют собой набор нормализованных устройств, количество и размещение которых зависят от конструкции детали.
К ним относятся:
1) устройства крепления измерительных средств (универсальных измерительных приборов, измерительных преобразователей и отсчетных устройств измерительных микроскопов); 2) устройства базирования измеряемых деталей — призмы, центры, оправки, столы; 3) устройства крепления деталей — баянетные патроны, рукоятки, прижимы; 4) передаточные механизмы — рычаги, коромысла, пружинные параллелограммы; 5) исполнительные устройства — световые табло, экра ны, блоки с цифровой индикацией; 6) устройства для установки и снятия деталей; 7) вспомогательные устройства для поворота и перемещения деталей при измерениях; 8) электронные блоки (усилители, реле, пороговые устройства).
Универсальные приспособления применяют при контроле диаметров, длин, радиального и торцового биения валов, диаметров отверстий, высот уступов деталей и т. п.
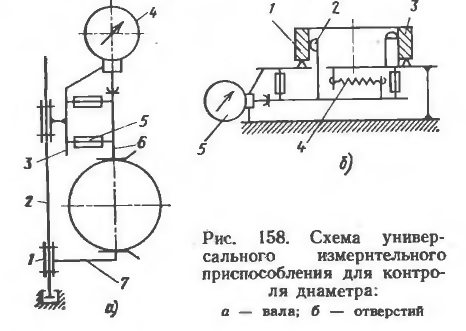
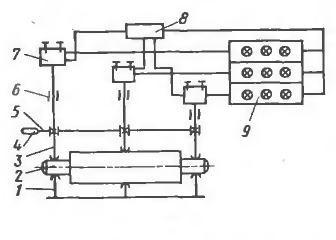
Универсальное приспособление для контроля диаметров вала (рис. 158, а) представляет собой регулируемую скобу, губки которой настраивают на соответствующий диаметр вала. Губки 3 и 7 перемещаются и крепятся на колонке 2, установленной в основании 1 приспособления. Наконечник 6, подвешенный на губке 3 плоскими пружинами 5, контактирует с валом, а также с измерительной головкой 4. Изделие поворачивают при контроле вручную или используют механический привод. По показаниям измерительного средства определяют годность изделия.
Универсальное измерительное приспособление для контроля диаметра отверстий (рис. 158,6) имеет жесткий упор 3, от которого измеряется диаметр отверстия детали 1 по двухконтактной схеме. Плавающий штырь 2 плоскими пружинами прикреплен к планке 4. Перемещения планки регистрируются измерительным прибором 5.
Многомерные приспособления для повышения производительности труда контролера выполняют светосигнальными. Приспособление для контроля диаметров ступенчатых валов (рис. 159) имеет электроконтактные датчики 7, установленные в кронштейнах 6. Измерительные штоки 3 датчиков контактируют с измеряемыми сечениями вала 2, установленного на опорах 1. При установке вала в приспособление штоки поднимаются оператором за ручку 4 арритирующего устройства 5. Сигнал от датчиков подается через электронное реле 8 на светофорное табло 9 с тремя рядами лампочек и экраном. На экран наносится контур вала с размерными линиями контролируемых сечений вала: сигнальные лампы установлены на этих линиях. Свет верхних лампочек означает наличие «брака плюс» в соответствующем сечении вала, свет средних лампочек — «годный размер», а нижних лампочек — «брак минус».
Контрольно-сортировочные автоматы
Для автоматического приемочного контроля готовых изделий в массовом производстве применяются контрольно-сортировочные автоматы. В общем случае автомат состоит из загрузочного, транспортного, измерительного, запоминающего и исполнительного устройств, а также включает командоаппарат и пусковую цепь. Контрольный полуавтомат содержит автоматическое измерительное устройство, но одну или несколько функций, как правило, загрузку и выгрузку изделий, выполняет с участием оператора.
В автоматах используются механические измерительные системы и системы с электроконтактными, индуктивными и фотоэлектрическими измерительными преобразователями.
В контрольном автомате с измерительным преобразователем (рис. 160) для сортировки игольчатых роликов подшипников ролики 3 из кассеты 1 загрузочного бункера через пружинный отсекатель 2 под действием собственного веса падают на два диска //, которые подают их на позицию измерения. Кулачок 12 арретирует (поднимает) измерительный шток 5 в момент подхода детали. При измерении ролики фиксируются двумя плоскими пружинами 6. Фотоэлектрический датчик 4 измеряет диаметр ролика и определяет номер его сортировочной группы, фоторезистор подает сигнал на контакт
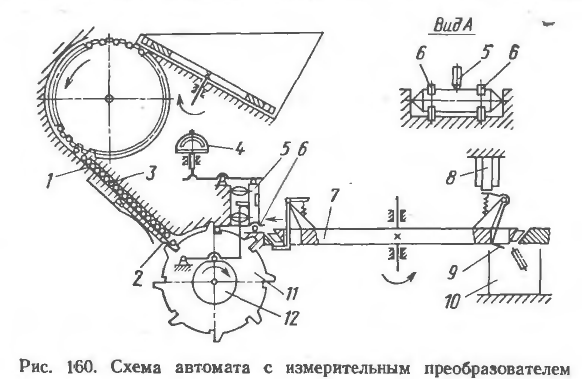
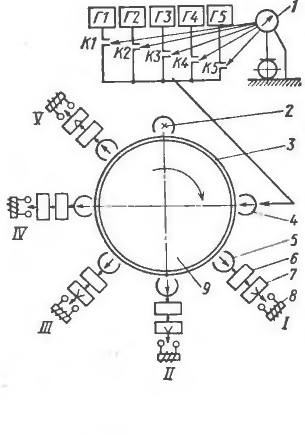
запоминающего устройства. Затем ролик сталкивается с измерительной позиции очередной деталью в карман диска 7, который вращается над рядом бункеров 10. Когда ролик проходит над бункером своей сортировочной группы, запоминающее устройство включает цепь электромагнита 8, якорь которого открывает заслонку 9. Все механизмы автомата приводятся в движение через распределительный вал, вращающийся от электродвигателя. При конструировании автоматов используют унифицированные узлы.
Запоминающее устройство с магнитной записью сигнала датчика (рис. 161) содержит фотоэлектрический преобразователь /, который, измерив изделие, через электромагнитное реле подает сигнал-команду на один из замыкающих контактов К, соединяющих звуковые генераторы Г с записывающей головкой 4 магнитофона. Каждому фоторезистору датчика соответствует генератор определенной частоты. При замыкании контакта К записывающая головка 4 намагничивает ферромагнитную пленку 3 с заданной частотой. Пленка нанесена на диск 9, вращающийся синхронно с транспортным устройством автомата; время прохождения намагниченного участка пленки вдоль исполнительных узлов I—V совпадает с моментом прохождения изделия над бункерами автомата. При прохождении намагниченного участка пленки мимо считывающих головок 5 в них вырабатывается электросигнал. Если частота сигнала совпадает с частотой полосового фильтра 6, то он поступает на усилитель 7 и включает электромагнит 8 заслонки соответствующего бункера. Перед записывающей головкой 4 пленка размагничивается стирающей головкой 2.
Средства активного контроля
Средства активного контроля предназначены для управления режимом обработки деталей в зависимости от результатов измерений размеров деталей. Их подразделяют на средства, измеряющие размер деталей в процессе обработки и переключающие режимы обработки при достижении заданного размера, и на средства, измеряющие размеры готовых изделий и регулирующие положение режущего инструмента относительно обрабатываемой поверхности (подналадчики). Наибольшее распространение средства активного контроля получили на заключительных операциях обработки деталей — шлифовании, хонинговании.
Показывающий механизированный прибор активного контроля (рис. 162) представляет собой трехконтактную скобу, которая шарнирно крепится на пружинном кронштейне 9 к кожуху 10 шлифовального круга 11. Скоба может свободно откидываться оператором при смене деталей. На корпусе 6 скобы расположены два базирующих наконечника 1, на пружинном параллелограмме 3 подвешен рычаг 5 с измерительным наконечником 2 и установлен индикатор часового типа 8. Движение измерительного рычага 5 через качающийся рычаг 7 передается наконечнику индикатора 8. Измерительное усилие создается пружиной 4. По показаниям индикатора оператор регулирует процесс обработки детали.
Автоматические средства активного контроля для управления технологическим процессом имеют отсчетно-командные устройства, в основном пневматического и индуктивного принципа действия.
Двухконтактная скоба с индуктивным датчиком (рис. 163) имеет измерительные губки 4 и 5, которые прикреплены к корпусу 1 скобы на плоских пружинах 2 и
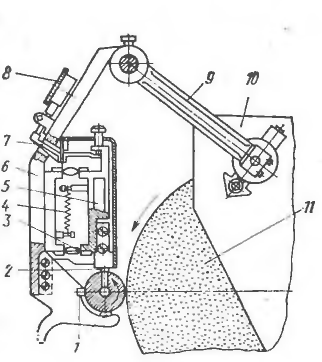
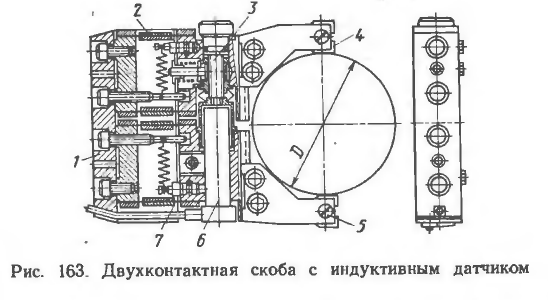
На губке 5 закреплен датчик 6, а на губке 4 — упор 3. Скоба устанавливается на подводящем устройстве, которое крепится к столу или станине станка. Упором 3 выполняется установка скобы на точный размер по образцовой детали или мере. Измерительная информация от датчика передается в отсчетно-командное устройство.
Двухконтактная скоба с пневматическим датчиком (рис. 164) предназначена для контроля внутреннего диаметра деталей. На корпусе скобы 10 плоскими пружинами 9 подвешены каретки 1 и 2 с зубчатыми рейками 3 и 6. На рейках закреплены губки 4 и 5 с измерительными наконечниками. Губки при грубой настройке скобы на размер перемещаются по рейкам относительно кареток. На каретке 1 укреплено сопло 7 пневмодатчика. на каретке 2 имеется винт 8 для точной настройки прибора. В процессе обработки детали изменяется зазор между соплом 7 и винтом 8, при этом в пневмоприводе сопла изменяется давление, которое регистрируется прибором.
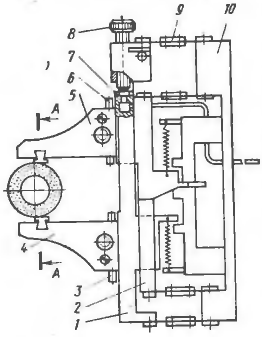
Отсчетно-командное устройство с пневмоэлектрокон-
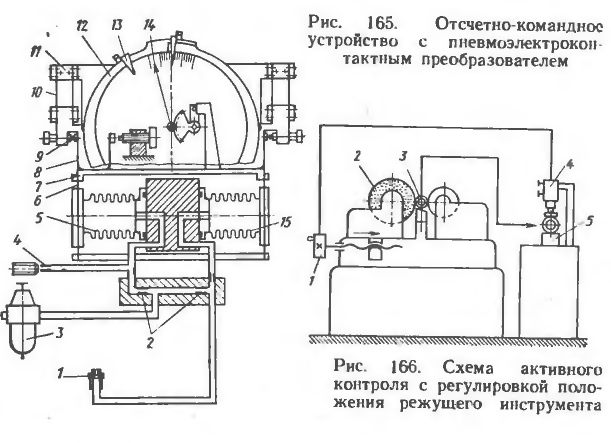
тактным преобразователем работает следующим образом (рис. 165): воздух из блока 3 фильтрации и стабилизации через выходные сопла 2 поступает к измерительному соплу 1 и соплу 4 противодавления, которые соединены соответственно с внутренними полостями сильфонов 15 и 5. К сильфонам на плоских пружинах 6 прикреплена планка 7, которая приводит в действие рычажно-зубчатый механизм отсчетиого устройства. На планке также расположены подвижные электрические контакты 8. Соосно с ними на плоских пружинах 10 к корпусу 11 подвешен ряд неподвижных электроконтактов 9, каждый из которых настраивается на определенный размер детали с помощью нескольких кулачков 12. Указатели 13, закрепленные на кулачках, показывают интервал размеров между командами.
Изменение давления в измерительном сопле вследствие разности давлений воздуха в сильфонах приводит к перемещению планки 7 отсчетно-командного механизма: стрелка 14 показывает значение отклонения размера. При достижении заданных размеров детали контакты 8 и 9 замыкаются и в электрической схеме прибора возникают импульсы. С помощью электронного реле импульсы преобразуются в команду управления режимами работы станка.
При активном контроле с регулированием положения режущего инструмента (рис. 166) обработанная деталь 3 поступает в измерительный прибор с базирующим элементом 5 и датчиком 4. Износ шлифовального круга 2 приводит к увеличению размера детален. Когда размер достигает установленного предела, датчик 4 подает команду на электромагнит, управляющий храповым механизмом 1. При этом связанный с храповым механизмом ходовой винт перемещает шлифовальную бабку станка на установленное значение.
Координатно-измерительные приборы и машины
Для контроля изделий сложной конфигурации с большим числом измеряемых размеров применяются координатно-измерительные приборы и машины с ручным управлением и автоматической обработкой результатов изменений, а также с полностью автоматизированным процессом измерений. Универсальные координатно-измерительные приборы УИМ-29 и ДИП, созданные на базе универсальных микроскопов (см. §47), имеют ручное управление и выполняют плоские измерения по двум координатам, а результаты измерений фиксируются цифропечатающим прибором.
Координатно-измерительная машина (КИМ) (рис. 167) работает в автоматическом режиме и обеспечивает пространственное движение щупа с датчиками по трем осям координат и
(рис. 167,6). На массивном ос-
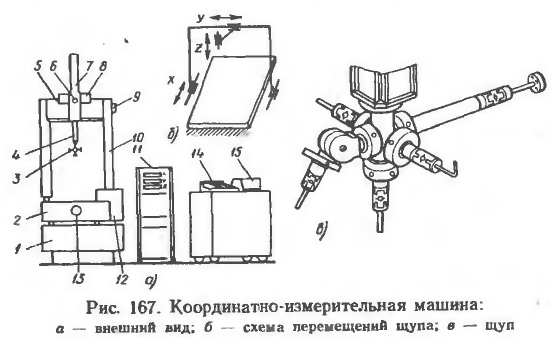
новании 1 расположен измерительный стол 2, вдоль которого по направляющей /2 перемещается арка 10. Вдоль перекладины 5 арки движется каретка 8 с пинолью 7, в которой устанавливается измерительный преобразователь 4 с многоточечным щупом 3 (рис. 167, в); в большинстве случаев используются индуктивные преобразователи. Результат измерений складывается из значений перемещений арки, каретки и пиноли, а также из отклонений шупа от нулевого положения по соответствующей координате. Значения измеряемого размера фиксируются по каждой координате на цифровом табло 11, а также на цифропечатающем устройстве 15. Схема перемещений каретки задается через программирующее устройство 14. Настройку КИМ выполняют вручную с помощью микрометрических винтов 6, 9 и 13, перемещающих пиноль, каретку и стол вдоль координатных осей . Некоторые модели КИМ обеспечивают измерения в шести координатах: например, измеряются перемещения датчика вдоль осей
и
, а также поворот датчика вокруг горизонтальных осей
и
и поворот детали вокруг вертикальной оси
.
Прогресс в автоматизации производства в настоящее время неразрывно связан с внедрением микроэлектроники. К достижениям микроэлектроники относится создание управляющих и вычислительных микропроцессоров, которые имеют миниатюрные размеры, высокую надежность и незначительный расход энергии. Это позволяет внедрять их на всех стадиях производственного процесса.
Одним из основных направлений применения средств вычислительной техники в производстве является создание автоматической системы управления технологическими процессами (АСУ ТП). В машиностроении основ-нон областью применения микропроцессоров и микро-ЭВМ являются станки с числовым программным управлением (ЧПУ), робототехника и измерительная техника, где в настоящее время ведутся работы по замене электронных приборов микропроцессорами. Например, ЭВМ применяются в КИМ для проведения измерений в соответствии с заданной программой, для обработки результатов измерений и выработки измерительной информации. Цифровая индикация результатов измерений повышает точность и производительность измерений и облегчает труд контролера.
Стандартизация и контроль качества продукции в машиностроении
Развитие общественного производства связано с развитием новой техники и технологии, выпуском все более .разнообразных и сложных изделий, материалов и товаров. Стандартизация заключается в рациональном ограничении видов и типов нужной народному хозяйству продукции и способов ее производства в целях механизации и автоматизации труда, улучшения качества продукции, лучшего использования производственных фондов, экономии материальных и трудовых ресурсов, охраны здоровья населения, безопасности труда, развития международного сотрудничества, совершенствования управления производством и т. п. К основным задачам стандартизации относятся: 1) установление требований к качеству продукции; 2) определение единой системы показателей качества; 3) установление норм, требований и методов в области проектирования и производства продукции; 4) обеспечение единства и достоверности измерений в стране; 5) установление единых терминов и обозначений в важнейших областях науки, техники и других отраслях народного хозяйства и т. п.
Нормативно-технический документ по стандартизации, устанавливающий комплекс норм, правил и требований к объему стандартизации и обязательный для исполнения, называется стандартом. В зависимости от сферы действия и уровня утверждения стандарты делятся на четыре категории: государственные (ГОСТ); отраслевые (ОСТ); республиканские (РСТ); предприятий (СТП). Применяются также стандарты единые для нескольких стран, например стандарты СЭВ. Объектами стандартизации являются: 1) материальные предметы (продукция); 2) нормы, правила и требования организационно-методические и общетехнические, связанные с созданием и потреблением продукции; 3) термины, определения и обозначения.
Стандарты на продукцию в зависимости от содержания (назначения) подразделяются на виды: устанавливаются стандарты технических условий, технических требований, параметров, размеров, типов, конструкции, марок, сортамента, эксплуатации и ремонта, типовых технологических процессов и т. д. Стандарты технических условий устанавливают эксплуатационные (потребительские) характеристики, правила приемки, методы контроля качества, требования к маркировке, упаковке, транспортированию и хранению, комплектность и гарантии изготовителя. Стандарты технических требований включают требования к качеству, надежности, внешнему виду продукции и т. п. Примеры стандартов: 1) ГОСТ 10905—75. Плиты поверочные и разметочные. Технические требования; 2) ГОСТ 8.162—75. Головки измерительные пружинно-оптические. Оптикаторы. Методы и средства поверки; 3) ГОСТ 16263- 70. Метрология. Термины и определения. Несоблюдение стандартов преследуется по закону: ответственность несут министерства и ведомства, а также предприятия и организации.
Стандартизация и качество продукции
Одной из главных задач стандартизации является повышение качества продукции. Стандартами установлены номенклатура показателен качества и методы их определения, методы оценки качества и организации управления качеством. Совокупность свойств продукции, обусловливающих ее пригодность удовлетворять определенные потребности в соответствии с ее назначением, называется качеством продукции. Количественная характеристика одного или нескольких свойств продукции, составляющих ее качество, рассматриваемая применительно к определенным условиям ее создания и эксплуатации или потребления, является показателем качество-Единичный показатель качества характеризует одно из свойств продукции, комплексный показатель — несколько свойств. Определяющий показатель качества — комплексный показатель, по которому принимается решение об оценке качества. Уровень качества — относительная характеристика качества продукции, основанная на сравнении значений показателей качества оцениваемой продукции с базовыми значениями показателей.
Показатели качества продукции группируются по характеризуемым ими свойствам. Показатели назначения устанавливают область применения и основные параметры изделий, например, мощность и угловую скорость двигателей, производительность машин и аппаратов, цену деления и диапазон показаний приборов. Одним из основных требований к продукции машиностроения является надежность — свойство изделия выполнять ладанные функции, сохраняя во времени установленные эксплуатационные показатели в требуемых пределах. Показатели надежности включают показатели безотказности, долговечности, ремонтопригодности и сохраняемости. Показатели безотказности — вероятность безотказной работы, средняя наработка до отказа и др. — показывают свойство изделий сохранять работоспособность в течение определенного времени или до заданной наработки. Показатели долговечности — средний ресурс, средний срок службы и другие характеризуют свойства продукции сохранять работоспособность до наступления предельных состояний, установленных системой технического обслуживания и ремонта. Показатели ремонтопригодности и сохраняемости определяют способности изделий восстанавливать свои свойства при ремонте и сохранять их при хранении без эксплуатации. Качество продукции характеризуют также следующими группами показателей — эргономическими, технологическими, эстетическими, стандартизации и унификации, патентно-правовыми, экологическими, безопасности.
Показатели качества определяют несколькими методами. Измерительный метод осуществляется с помощью технических средств измерения. Регистрационный метод заключается в наблюдении и подсчете числа определенных событий, предметов и затрат. Расчетный метод основан на использовании теоретических и эмпирических зависимостей показателей качества от параметров продукции. Органолептический метод заключается в анализе восприятия продукции органами чувств. Экспертный метод осуществляется на основе решения, принимаемого экспертами. Социологический метод основан на сборе и анализе мнений фактических или возможных потребителей продукции.
Оценка уровня качества продукции дает возможность определить годную продукцию, дефектные изделия и брак, а также установить сорт и категорию качества продукции. При дифференцированном методе оценки ка чества используются единичные показатели, при комплексном методе — комплексные показатели, при смешанном методе — единичные и комплексные показатели.
Статистический метод оценки качества продукции заключается в использовании правил математической ста тистики при определении показателей качества. Этот метод позволяет оценивать качество изделий по результатам контроля части изделий из изготовленной партии. Согласно теореме Чебышева при достаточно большом числе независимых опытов среднее арифметическое показателей, определенных из этих опытов, равно (близко) среднему арифметическому всей партии.
Контроль качества продукции
Повышение качества продукции в соответствии с достижениями научно-технического прогресса является важнейшей народнохозяйственной проблемой. Управление качеством продукции — это действия, которые осуществляют при ее проектировании, изготовлении и эксплуатации или потреблении, чтобы установить, обеспечить и поддерживать необходимый уровень качества. Эти задачи решаются путем разработки стандартов на основе достижений науки, техники и передового опыта.
В машиностроении разработаны системы стандартов для всех стадий создания продукции. Единая система консфукторской документации (ЕСКД) — комплекс стандартов, устанавливающих правила и положения по разработке, оформлению и обращению конструкторской документации.
Единая система технологической документации (ЕСТД), устанавливает правила по разработке комплектации, оформлению и обращению документации, применяемой при изготовлении и ремонте изделий. Единая система технологической подготовки производства (ЕСТПП) устанавливает широкое применение прогрессивных типовых технологических процессов, стандартной технологической оснастки и оборудования, средств механизации и автоматизации.
Одним из основных элементов системы управления качеством продукции является контроль производства. Технический контроль — проверка соответствия продукции или процесса, от которого зависит ее качество, установленным техническим требованиям. Виды технического контроля: I) контроль качества продукции, который устанавливает значение показателей качества; 2) контроль технологического процесса (его режимов, характеристик, параметров); 3) контроль проектирования, охватывающий процесс разработки конструкторской или технологической документации; 4) производственный контроль, при котором проверяются результаты процесса на стадии изготовления; 5) эксплуатационный контроль, связанный с проверкой продукции поставщика, поступившей к потребителю.
В зависимости от количества проверяемой продукции и протяженности во времени технический контроль может быть сплошной, выборочный, летучий, непрерывный, периодический; по воздействию на продукцию — разрушающий и неразрушающий. По используемому методу контроль подразделяется на измерительный, регистрационный, визуальный, органолептический, по контрольному образцу. Инспекционный контроль осуществляется уполномоченными представителями в целях проверки эффективности ранее выполнявшегося контроля; ведомственный контроль качества продукции проводится министерством; государственный контроль — специальными государственными органами. Для осуществления постоянного контроля на предприятиях создаются отделы технического контроля (ОТК). Приемочный контроль продукции выполняется также органами Госприемки.
Метрологическое обеспечение качества продукции
Качество продукции во многом зависит от качества измерений.
Метрологическое обеспечение — установление и применение научных и организационных основ, технических средств, правил и норм, необходимых для достижения единства и требуемой точности измерений. Его научной основой является метрология. Правила и нормы метрологического обеспечения устанавливает Государственная система обеспечения единства измерений (ГСИ).
- Стандарты ГСИ устанавливают:
- единицы физических величин;
- государственные эталоны и общесоюзные поверочные схемы;
- методы и нормы точности измерении;
- номенклатуру нормируемых метрологических показателей средств измерений;
- методы и средства поверки средств измерений и т. п.
Организацией метрологического обеспечения в стране занимается метрологическая служба СССР, возглавляемая Госстандартом, и состоящая из государственных и ведомственных метрологических служб. Метрологическая служба предприятия является основным звеном ведомственной службы и создается как самостоятельное подразделение (отдел), возглавляемое главным метрологом. Она может включать комплексные и специализированные лаборатории, лаборатории по внедрению новой техники; контрольно-поверочные пункты в цехах; мастерские по ремонту приборов и др. На небольших предприятиях создаются центральные лаборатории измерительной техники (ПЛИТ).
Основные задачи измерительной лаборатории: анализ состояния измерений на предприятии и разработка мероприятий по совершенствованию метрологического обеспечения; совершенствование и внедрение современных методов и средств измерений, механизированных и автоматических средств контроля; установление оптимальных норм точности измерений; поверка и метрологическая аттестация средств измерений; аттестация методик выполнения измерений; контроль за состоянием условиями применения и .ремонтом средств измерений и соблюдения требований, норм и правил ГСИ.
Рабочие и выходяшие из ремонта меры и приборы подлежат поверке на предприятии или в ведомственных базовых лабораториях или органах Комитета по стандартам.
Результаты поверки оформляются свидетельствами, аттестатами или отметками в паспортах. Паспорт — постоянный документ, служащий для учета и наблюдения состояния средств измерений в эксплуатации. Аттестат — разовый документ, подтверждающий пригодность средства измерений для эксплуатации на определенный срок, в котором указаны погрешности или поправки, подлежащие учету при точных измерениях.
Приборы должны храниться в сухих отапливаемых, закрытых помещениях на стеллажах или в шкафах при значениях температуры Ю…35°С, относительной влажности воздуха до 80%, без примесей агрессивных газов, вызывающих коррозию. На рабочих местах приборы надрывают колпаками или чехлами. Металлические части после работы промывают бензином, вытирают салфеткой и покрывают смазкой. Приборы нужно держать в чистоте, оберегать от механических повреждений и коррозии, эксплуатировать в строгом соответствии с инструкциями.
Особо бережного обращения и ухода требуют высокоточные оптико-механические приборы.
Бригадная форма организации и стимулирования труда рабочих
В соответствии с Конституцией трудовые коллективы являются неотъемлемой частью политической системы социалистического общества. Производственная бригада — первичное звено трудового коллектива предприятия. Ее полномочия определяются законом «О трудовых коллективах и повышении их роли в управлении предприятиями, учреждениями и организациями».
Бригадная форма организации и стимулирования труда наиболее полно отвечает современным требованиям производства и научной организации труда, возросшему образовательному и культурному уровню трудящихся; способствует интенсификации цроизводства, росту производительности труда, лучшему использованию рабочего времени и оборудования, экономии материальных и топливно-энергетических ресурсов; открывает возможности для улучшения организаторской и политико-воспитательной работы и укрепления трудовой дисциплины; утверждает дух подлинного коллективизма, взаимной требовательности и товарищеской взаимопомощи; создает широкие возможности для проявления творческой энергии и трудовой активности как всего коллектива, так и каждого рабочего; ускоряет рост квалификации и приобретение профессиональных навыков, особенно молодыми рабочими; расширяет профессиональный профиль и повышает содержательность труда Она является одним из основных направлений повышения эффективности работы предприятий, широкого вовлечения трудящихся в управление производством и воспитание людей.
Формирование и организация деятельности бригад
Бригада объединяет рабочих для совместного выполнения производственных заданий на основе взаимопомощи; общей заинтересованности и ответственности за результаты работы. Она создается по приказу руководителя предприятия или подразделения. Зачисление в бригаду выполняется с согласия работников.
Комплексная бригада включает рабочих различных профессии, выполняющих комплекс технологически разнородных, но взаимосвязанных работ, охватывающих полный цикл производства продукции или ее законченной части. Специализированная бригада обычно объединяет рабочих одной профессии, занятых на однородных технологических процессах. При двух- и трехсменной работе создаются сквозные бригады, объединяющие рабочих всех смен.
Бригаде отводится рабочая зона, охватывающая технологический процесс, за ней закрепляется производственная площадь, оборудование, средства труда, поставляются необходимые ресурсы и техническая документация. Бригада самостоятельно выполняет производственный процесс, управляет им в своей рабочей зоне и несет коллективную ответственность за результаты своей работы: выполнение производственных и встречных планов и социалистических обязательств; повышение производительности пруда; обеспечение высокого качества продукции и работы; рациональное использование оборудования, рабочего времени, материалов и энергии; сохранность социалистической собственности. В бригаде действует также и персональная ответственность каждого члена бригады в соответствии с его обязанностями
Бригадир — передовой квалифицированный рабочий, обладающий организаторскими способностями и пользующийся авторитетом у членов бригады. Его назначает руководитель предприятия или подразделения при согласии коллектива бригады. Коллектив бригады открытым голосованием избирает совет бригады, который возглавляет бригадир.
Коллектив (или совет) бригады имеет следующие права: 1) участвует в комплектовании бригады; 2) дает согласие администрации на назначение бригадира и вправе требовать его снятия, если он не оправдал доверия; 3) участвует в аттестации и рационализации рабочих мест бригады; 4) утверждает предложения бригадира по установлению коэффициентов трудового участия (КТУ) членам бригады; 5) рекомендует членов бригады к установлению (или отмене) надбавок и доплат за профессиональное мастерство и совмещение профессии; 6) ходатайствует об изменении в установленном порядке квалификационных разрядов; 7) заключает со смежными бригадами договоры о взаимных обязательствах и ответственности за поставки; 8) определяет победителей соцсоревнования в бригаде и размеры их поощрения; 9) выдвигает членов бригады на материальное и моральное поощрение по итогам внутризаводского соцсоревнования; 10) увеличивает оплату ученикам сверх размеров, установленных действующим положением, с учетом вклада ученика в коллективный заработок бригады; !!) рассматривает очередность предоставления отпусков; 12) разбирает случаи нарушения трудовой дисциплины и дает предложения о наложении взысканий; 13) проводит воспитательную работу в коллективе, организует наставничество, рассматривает вопросы производственных и внепроизводственных отношений членов бригады, развивает чувство коллективизма, товарищества, взаимной помощи и ответственности за выполнение производственных планов.
Положение о бригадире и совете бригадиров
Бригадир выполняет свою работу в тесном взаимодействии с советом бригады. Основные обязанности бригадира: 1) обеспечивать слаженную и ритмичную работу бригады на основе равномерной загрузки всех ее работников, взаимопомощи и взаимозаменяемости, соблюдение смены режима труда и отдыха,.2) давать производственные задания членам бригады и контролировать их выполнение; 3) обеспечивать соблюдение технологического процесса, выполнение инструкций по эксплуатации оборудования и правил по охране труда; 4) проверять обеспеченность рабочих мест сырьем, материалами, инструментами, приспособлениями, технической документацией и т. п; 5) активно участвовать во внедрении научной организации труда, бригадного хозрасчета и подряда; 6) систематически совершенствовать свое профессиональное мастерство, идейно-политический и культурно-технический уровень; 7) организовывать соцсоревнования в бригаде.
Бригадир имеет право: 1) принимать участие в разработке производственных и встречных планов и соцобязательств бригады; 2) требовать от администрации своевременного обеспечения всем необходимым для своевременного выполнения производственного плана; 3) предъявлять претензии к смежным бригадам, по вине которых срывается выполнение плана; 4) вносить администрации предложения о совершенствовании организации работы бригады, ее структуры, увеличении сменности, улучшении технологии и условий труда, изменении условий его оплаты в целях повышения производительности труда; 5) подготавливать и выносить на утверждения коллектива (совета) бригады предложения по установлению коэффициентов трудового участия членам бригады и их поощрению; 6) вносить предложения администрации о зачислении (отчислении) рабочих; 7) приостанавливать работу в тех случаях, когда нарушение правил по технике безопасности угрожает здоровью работников, не допускать к работе члена бригады, находящегося в состоянии, ведущем к таким же последствиям (нетрезвое состояние, болезнь и др.); 8) представлять предложения администрации о применении мер воздействия и дисциплинарных взысканий на членов бригады, не выполняющих возложенные на них обязанности и нарушающих трудовую дисциплину.
Советы бригадиров создаются на предприятиях и в подразделениях в целях содействия развитию и повышению эффективности бригадной формы организации и стимулирования труда. Совет бригадиров избирается общим собранием бригадиров или собранием председателей советов бригадиров цехов и утверждается соответствующим руководителем. Он является совещательным органом. Его примерные функции: 1) рассмотрение предложений о создании новых и совершенствовании действующих бригад, а также вопросов планирования и учета их работы, организации нормирования и оплаты труда и материально-технического обеспечения; 2) обеспечение слаженности в работе бригад и оказания им помощи в улучшении работы; 3) обобщение и распространение передового опыта производственной и воспитательной работы; 4) изыскание резервов повышения эффективности производства и т. п.
Организация и оплата труда в бригаде
Производственный план бригаде устанавливается, исходя из технически обоснованных норм труда и производственных мощностей. Для его выполнения разрабатываются и осуществляются необходимые организационно-технические мероприятия и создаются условия для повышения производительности труда. Бригадная форма организации и стимулирования труда дает наибольший эффект при введении хозрасчета. Хозрасчетной называется бригада, которой наряду с плановыми производственными заданиями устанавливают фонд заработной платы, нормы расхода по сырью, материалам, полуфабрикатам, топливу, энергии и другим ресурсам, использование которых непосредственно зависит от ее деятельности. Взаимные обязательства администрации и бригады, а также формы и размеры ее поощрения заключаются в договоре или трудовом паспорте бригады. Бригаде, работающей в условиях подряда, в соответствии с договором ‘поручается выполнить определенный объем работ установленного качества. За ней закрепляются орудия и средства труда, предоставляются необходимые производственные ресурсы, создаются условия для успешного выполнения работы и устанавливаются долгосрочные нормативы средств на оплату труда.
В целях усиления материальной заинтересованности членов бригады в общих итогах работ начисление им заработной платы осуществляется на основе единого наряда по конечным результатам работы бригады. Коллективный заработок между членами бригады распределяется в соответствии с тарифными разрядами и фактически отработанным временем. Индивидуальный вклад каждого работника в результаты коллективного труда бригады учитывается при распределении надтарифной части заработка бригады (приработка, премия и др.) путем применения К.ТУ, который для каждого работника обсуждается и утверждается на собрании коллектива (или совета) бригады. Минимальный размер заработной платы членов бригады не может быть ниже размера установленной им тарифной ставки. На учащихся профессионально-технических училищ, закрепленных за производственными бригадами, с начала производственной практики распространяется с согласия этих бригад действующий в них порядок распределения коллективного заработка с учетом КТУ.
Кстати, дополнительная теория из учебников по метрологии тут.
Основные положения законодательства по охране труда
Охрана труда — система законодательных актов, социально-экономических, организационных, технических, гигиенических и лечебно-профилактических мероприятий и средств, обеспечивающих безопасность, сохранение здро»ья и работоспособности человека в процессе труда. Улучшение охраны труда постоянно находится в центре внимания партийных и государственных органов и рассматривается как важная социальная задача развития страны.
Охрана труда обеспечивается совместными действиями администрации и работников. Администрация обязана проводить техническое оснащение рабочих мест; создавать безопасные условия труда, внедрять современные средства техники безопасности, разрабатывать инструкции но охране труда, проводить инструктаж работников и контролировать выполнение инструкций, расследовать несчастные случаи на производстве и устранять их причины, привлекать работников к дисциплинарной ответственности за нарушение техники безопасности.
В зависимости от вредности условий труда работники должны получать спецодежду, обувь, рукавицы, очки и другие средства индивидуальной зашиты; моюшие и обеззараживающие средства; молоко и лечебно-профи-лактическое питание.
Рабочие и служащие обязаны: 1) соблюдать трудовую и производственную дисциплину, требования правил внутреннего распорядка; 2) выполнять инструкции по охране труда; 3) пользоваться выдаваемыми средствами защиты; 4) точно и своевременно исполнять распоряжения администрации; 5) беречь социалистическую собственность.
Предприятия несут материальную ответственность за ущерб, причиненный работникам при исполнении служебных обязанностей. Должностные лица, виновные в нарушении законодательства об охране труда, несут дисциплинарную, административную, уголовную и материальную ответственность. Материальная ответственность возникает при необходимости денежных выплат потерпевшему от несчастного случая, а уголовная, если нарушение правил по охране труда могло повлечь или повлекло несчастные случаи с людьми.
Надзор и контроль за соблюдением законов о труде осуществляют: 1) Генеральный Прокурор СССР через органы прокуратуры; 2) министерства и ведомства; 3) Советы народных депутатов; 4) профессиональные союзы; 5) специально уполномоченные государственные органы и инспекции; Госгортехнадзор, Госэнергонадзор, Государственные пожарный и санитарный надзоры; ГАИ.
Основы безопасности труда
Безопасность труда — условия труда, при которых исключено воздействие на работающих опасных и вредных производственных факторов. Техника безопасности — система организационных мероприятий и технических средств, обеспечивающих безопасность труда. Несчастный случай на производстве возникает при воздействии на работающего опасного производственного фактора при выполнении трудовых обязанностей или заданий руководителя. К несчастным случаям относятся травматизм, профессиональные отравления или заболевания. Причины несчастных случаев на машиностроительном производстве делятся на четыре группы.
Организационные причины — некачественное обучение работников безопасным методам (работы; отсутствие инструкций и недостаточный контроль охраны труда; неправильная организация труда и рабочего места; нарушение правил безопасности движения, технической и линейной эксплуатации транспорта; отсутствие или плохое состояние индивидуальных средств защиты.
Технические причины — несоответствие нормам безопасности конструкции технологического оборудования, подъемно-транспортных устройств, технологической оснастки, коммуникаций, ручного механизированного инструмента, а также их неисправность; неправильный выбор методов и режимов работы оборудования, сборки и транспортирования; несоответствие конструкции оборудования эргономическим требованиям (неудобство в обслуживании и управлении и т. п.); недостаточная оснащенность производства средствами техники безопасности.
Санитарно-гигиенические причины — загазованность, запыленность и ионизация воздуха; повышенные или пониженные температуры, влажности, давления и подвижности воздуха; неудовлетворительная освещенность (недостаток естественного или искусственного света, повышенные яркость или пульсации светового потока); высокий уровень шума, вибраций; наличие вредных веществ, излучений и микроорганизмов.
Психофизиологические причины — значительные физические нагрузки, напряженность и монотонность труда, которые приводят к совершению ошибочных действий; недостаточная профессиональная подготовленность; нарушение правил по охране труда, трудовой и производственной дисциплины; несоответствие психофизиологических данных работника требованиям производства или болезненное состояние работника.
Обучение работающих безопасности труда проводится путем инструктажей. Инструктажи подразделяют на вводный, шервичный, повторный, внеплановый и текущий. Вводный инструктаж проводит инженер по охране труда в кабинете охраны труда, другие виды инструктажа — руководитель работ на рабочем месте в соответствии с инструкциями по охране труда. Повторный инструктаж необходим для повышения уровня знаний по охране труда. Внеплановый инструктаж проводят при изменении правил охраны труда, изменении условий работы (технологических режимов, оснастки, оборудования, материалов и др.) и при нарушении работниками правил охраны труда. Текущий инструктаж выполняют перед работами, на которые оформляется наряд-допуск.
Расследованию и учету подлежат все несчастные случаи, которые произошли на территории или вне предприятия при выполнении работ по его заданию и при транспортных перевозках предприятия. О несчастном случае пострадавший или очевидец должен известить мастера, начальника цеха или руководителя работ. Мастер обязан организовать первую помощь пострадавшему, направить его в медпункт и сообщить о происшествии начальнику цеха. Администрация цеха и предприятия совместно с профкомом расследуют причины и обстоятельства несчастного случая, составляют акт о нем и намечают профилактические мероприятия для устранения подобных происшествий в будущем.
Общие требования безопасности труда на предприятии
Производственные процессы выделяют дым, пыль, газы, неприятные запахи, шум, излучения и др., поэтому предприятия следует располагать на специальных площадках, отделенных от жилых районов санитарно-за-щитными зонами. Территория предприятия должна быть ровной, с уклоном для стока вод и хорошо освещаться. Расположение зданий и сооружении и разрывы между ними должны обеспечивать благоприятные условия для естественного освещения и проветривания помещений. Взрывопожароопасные объекты размещают иа отдельных участках и защищают зелеными полосами. Дороги и пешеходные дорожки должны быть прямолинейными, иметь твердое покрытие, хорошо освещаться, иметь автоматические шлагбаумы и светофоры в местах пересечения с рельсовыми средствами транспорта на одном уровне.
Помещения цехов должны иметь: объем и площадь на одного работающего соответственно не менее 15 м3 и 4,5 м2; решетки и ограждения каналов и углублений в полах, теплоизолирующие настилы на холодных и скользких полах; раздельные входы и выезды с дверями и воротами, открывающимися наружу; дополнительные эвакуационные выходы на случай пожара; тамбуры или тепловые завесы у входов и выездов с улицы; разметку проходов и проездов внутри цехов белыми линиями. Для создания безопасных и здоровых условий труда в помещениях устанавливают устройства и приборы для отопления, естественного и искусственного освещения, для вентиляции и очистки воздуха, водоснабжения и канализации, защиты от шума, вибраций, излучений и других вредных факторов. В санитарно-бытовых помещениях цехов располагаются гардеробные с умывальниками и душевыми, комнаты по обеспыливанию, просушиванию и обезвреживанию одежды, помещения для отдыха и приема пищи, здравпункты.
Помещение измерительной лаборатории должно быть расположено на 1-м этаже, защищено от пыли, вызывающих коррозию веществ и вибрации. Высота потолка помещений не менее 3,5 м и площадь на каждое рабочее место, значения температуры воздуха
и влажность
. Полы должны быть покрыты линолеумом. Помещения должно иметь внутреннюю электропроводку с напряжением 220, 127 и 6… 12 В, а при использовании пневматических приборов — воздухопровод с давлением
.
На территории и в цехах запрещается стоять и ходить под грузом, под настилами лесов и в местах, где возможно падение предметов; заходить в рабочие зоны и помещения, огражденные и отмеченные специальными знаками; стоять посторонним лицам вблизи от работающего оборудования; переходить и перебегать дорогу перед движущимся транспортом; загромождать проезды и проходы; прикасаться к электропроводам, особенно оборванным и с поврежденной изоляцией; курить в неустановленных для этой цели местах. Следует быть внимательным, при движении своевременно уступать дорогу транспорту и выполнять общепринятые правила движения, соблюдать чистоту и требования личной гигиены.
Рекомендуется избегать сквозняков, мокрой одежды и обуви, переохлаждения тела и ног, не пить слишком холодную или горячую воду, делать производственную гимнастику, после работы мыться под душем и переодеваться в чистую одежду, мыть с мылом руки перед приемом пищи.
На рабочем месте запрещается выполнять работы и распоряжения администрации, если они противоречат правилам техники безопасности или могут привести к несчастному случаю. Работы повышенной опасности должны выполняться только по наряду-допуску. Необходимо выполнять только ту работу, которая поручена мастером; при работе выполнять требования инструкций по технике безопасности и использовать приемы и способы, указанные мастером; следить за состоянием спецодежды, не допуская оборванных и развивающихся концов; сообщать мастеру о нарушениях техники безопасности; требовать установки настилов на холодные полы, хорошего освещения, устранения сквозняков и т. п.; поддерживать чистоту и порядок, не загромождать рабочего места и проходов к нему.
Перед началом работы следует проверить исправность оборудования, приборов, инструментов, защитных ограждений механизмов (шкивов, колес, муфт, валов), лестниц, настилов; приспособлений, защищающих от движущихся частей машины, которые невозможно закрыть ограждениями (механические отталкиватели рук, фотоэлементная защита); защитных скоб, предохраняющих от случайного ножного включения механизмов; заземления электрооборудования; арматуру электроосвещения и т. п.
Основы электробезопасности
Электробезопасность — система организационных и технических мероприятий и средств, обеспечивающих защиту людей от опасного и вредного воздействия электрического тока, электрической дуги, электромагнитного поля и статического электричества. Действие электрического тока на организм может быть: термическое — ожоги отдельных участков тела, нагрев сосудов, нервов и других тканей; электролитическое — разложение крови и других жидкостей; биологическое — раздражение и возбуждение тканей, сопровождающееся судорогами мышц и нарушением биоэлектрических процессов.
К местным электротравмам относятся: электрические ожоги; электрические знаки — пятна на коже серого или бледно-зеленого цвета диаметром 1…5 мм, металлизация кожи мельчайшими частичками металла, расплавленного элекпродугой; механические повреждения вследствие резких судорог под действием тока; офтальмия — воспаление глаз под воздействием излучения электродуги.
Общие электротравмы (электрические удары) возникают при прохождении тока через живые ткани. Они могут иметь четыре степени. Исход воздействия электрического тока на организм зависит от его силы, времени действия и частоты, индивидуальности человека и его санитарно-гигиенического состояния.
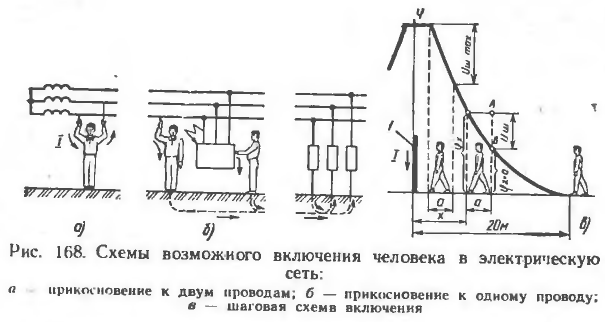
Опасность поражения электрическим током возникает при замыкании электрической цепи через тело человека. Прикосновение к двум проводам трехфазной сети (рис. 168, а) наиболее опасно, так как на человека действует наибольшее в цепи линейное напряжение. Прикосновение к одному проводу или к корпусу оборудования (рис. 168, б) менее опасно, так как действующее напряжение меньше и сила тока ослабляется вследствие сопротивления поля, обуви и т. п. Шаговое напряжение (рис. 168, в) действует на человека в зоне
вокруг провода 1, замкнутого на землю, вследствие разности потенциалов
электрополя:

Основные причины несчастных случаев — прикосновение или приближение на опасное расстояние к токоведущим частям; появление напряжения на металлических частях ввиду пробоя токоведущих частей; ошибочное включение электроустановок, находящихся в ремонте; возникновение шагового напряжения; нарушение правил электросварочных работ.
К основным мерам защиты относятся защитное заземление (рис. 169, а) корпусов электроустановок и не-токоведущих частей оборудования, которые могут оказаться под напряжением, корпус / соединяется проводником 2 с заземлителем 3. При защитном занулении (рис. 169, б) проводник 2 соединяет электрооборудование 1 с глухозаземленной нейтральной точкой обмотки источника тока, автоматические предохранители 3 защищают от токов короткого замыкания. При защитном отключении (рис. 169, в) возникновение на корпусе 1 опасного напряжения предотвращается срабатыванием защитно-отключающего устройства (автомата): катушка 3 приводит в действие выключатель 2 ‘при включении реле 4 максимального напряжения.
Токоведущие части оборудования и привода изолируются, ограждаются и размещаются на недоступной высоте. При работе с ручными переносными электроинструментами, лампами и приборами применяется малое напряжение . Электрические цепи разделяются на отдельные участки с помощью специальных трансформаторов. Опасные зоны блокируются и ограждаются ‘предупредительной сигнализацией.
К индивидуальным средствам защиты относятся изолирующие средства — оперативные и измерительные штанги, указатели напряжений, клещи, лестницы, площадки, диэлектрические перчатки, калоши, боты, коврики, подставки, инструмент с изолирующими накладками; ограждающие средства — переносные клетки и щиты, изолирующие накладки и колпаки, предупредительные плакаты, переносные временные заземления; вспомогательные средства — очки, рукавицы, противогазы, спецодежда и т. п.
Безопасная эксплуатация электроустановок обеспечивается при технической грамотности и сознательной дисциплине обслуживающего персонала. Лица, обслуживающие электроустановки, не должны иметь увечий и болезней, мешающих работе; периодически проходить медосмотр; знать и строго соблюдать безопасные методы работы; правила техники безопасности и оказания первой помощи; пройти проверку этих знаний.
При работе на электроустановках требуется неукоснительно соблюдать следующие правила: 1) на работу должно быть выдано разрешение; 2) работать должны не менее, чем два человека; 3) должны быть выполнены все организационные и технические мероприятия, обеспечивающие безопасность персонала.
При несчастных случаях от электрического тока прежде всего необходимо освободить пострадавшего от действия тока: отключить электроустановку; обрубить провода топором с деревянной (при ) или изолированной ручкой; оторвать пострадавшего от токоведущих частей за сухую одежду (при
) или изолирующими клещами; отбросить провода деревянной палкой (при
) или изолирующей штангой. Человеку, пострадавшему от электрического тока, необходимо оказать первую помощь: обеспечить полный покой или срочно доставить в медпункт. При отсутствии сознания уложить на ровную, мягкую подстилку, расстегнуть пояс и одежду, обеспечить приток свежего воздуха, обрызгать лицо холодной водой, дать понюхать нашатырный спирт, растереть и согреть тело. При редком судорожном дыхании необходимо сделать искусственное дыхание; при отсутствии признаков жизни — искусственное дыхание и наружный массаж сердца.
Основы пожарной безопасности
Пожар (неконтролируемое горение) может нанести большой материальный ущерб и привести к несчастному случаю (травме, отравлению, гибели). Опасные факторы пожара: 1) открытый огонь и искры; 2) повышенная температура воздуха; предметов и т. п.; 3) токсичные продукты сгорания, дым, недостаток кислорода; 4) разрушение и повреждение зданий и сооружений.
Для горения требуется наличие горючего вещества, кислорода и источника зажигания. Пожары начинаются вследствие возгорания, воопламенения, самовозгорания, самовоспламенения, вспышки, взрыва. Источниками зажигания могут служить искры, открытый огонь (спичка, сигарета), нагретые поверхности и т. п. Самовозгорание и самовоспламенение происходят без источников зажигания вследствие тепловых, химических и микробиологических процессов в веществе.
Пожарная опасность — возможность возникновения и развития огня. Она связана с веществами, материалами, оборудованием и процессами, применяемыми на производстве.
На машиностроительных заводах причины пожаров могут быть производственными и электротехническими. Производственными причинами являются нарушение технологического режима работы, коррозия, износ и конструктивные недостатки оборудования, неисправность запорной арматуры аппаратов и трубопроводов; плохая подготовленность оборудования и трубопроводов к ремонту; нарушение сроков ремонтов оборудования. Пожары также могут происходить от самовозгорания промасленных ветоши, металлической стружки, спецодежды и других материалов; вспышки растворителей, применяемых для промывки деталей; от искр и пламени при сварочных работах.
Электротехнические причины пожаров заключаются в неисправности электрооборудования и сетей и в нарушении правил устройства и технической эксплуатации электроустановок. При этом пожары происходят вследствие короткого замыкания, воспламенения проводов при перегрузках сети и больших переходных сопротивлений в местах их плохого контакта, работы нагревательных приборов без присмотра.
Пожарная безопасность обеспечивается пожарной профилактикой и активной защитой от пожара. К пожарной профилактике мероприятия относятся следующие мероприятия:
- Противопожарный инструктаж рабочих и служащих. Каждый работник обязан строго соблюдать правила пожарной безопасности, не допускать действий, которые могут привести к пожару, знать устройство и работу пожарного инвентаря и его местонахождение.
- Выполнение правил противопожарного режима Курить разрешается только в установленных местах с надписью «Место для курения». Нельзя загромождать и перекрывать пожарные проезды и проходы к пожарному инвентарю; захламлять территорию и помещения промасленными концами, тряпками и другими горючими предметами; оставлять неубранной металлическую стружку; использовать электропроводку и электрооборудование для личных целей и т. п.
- Организация добровольных пожарных дружин (ДПД). Члены ДПД обучаются приемам тушения очагов пожаров и страхуются от несчастных случаев при пожаротушении за счет предприятия. За активную борьбу с пожарами они получают ценные подарки, денежные премии, грамоты, дополнительные отпуска.
- Организация пожарно-технических комиссий, которые разрабатывают и осуществляют мероприятия по обеспечению пожарной безопасности.
Для тушения пожара в начальной стадии применяют различные средства: 1) воду из специальных водопроводов с брандспойтами, которую нельзя применять для тушения нерастворимых в ней органических веществ (бензина, керосина, бензола); веществ, реагирующих с водой (селитра, карбид кальция); электроустановок, находящихся под напряжением, 2) воздушно-механическую иену, которую приготовляют в пеногенераторах путем перемешивания воздуха с водными растворами пенообразователей; 3) углекислотные огнетушители (рис. 170), которые приводятся в действие вращением маховика 1 запорного вентиля 2, соединенного шлангом 3 с раструбом 4; 4) углекислотнобромэтиленовые (типа ОБУ), химические пенные (типа ОХП) и другие огнетушители. Для ликвидации очагов пожаров используют также струи водяного пара, сжатого воздуха, инертных газов.
В помещениях особо пожароопасных производств устанавливают стационарные огнегасительные и огне-преградительные установки, которые представляют собой разветвленную заполненную водой систему труб, оборудованную разбрызгивающими головками. При пожаре головки включаются автоматически или вручную датчиками-извещателями, которые одновременно вызывают пожарную команду. При возникновении пожара работник обязан немедленно сообщить в пожарную охрану и приступить к тушению пожара средствами пожаротушения; организовать спасение людей, оказать первую помощь пострадавшим и при необходимости вызвать медицинскую, газоспасательную и другие службы.
При усилении пожара работник должен покинуть помещение в соответствии с планом эваветствии с планом эвакуации и оказать содействие в эвакуации других людей в безопасное место.
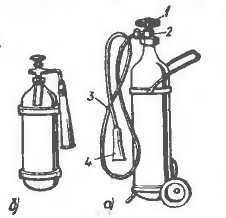
Организация охраны природы в нашей стране
При интенсивном развитии промышленности происходит отравление и загрязнение атмосферы, почв и водоемов, разрушение природных ландшафтов, истощение лесных ресурсов, уменьшение численности животных и растений. Научно обоснованная система государственных, международных и общественных мероприятий по охране, рациональному использованию, воспроизводству природных ресурсов н улучшению окружающей человека среды называется охраной природы. Научной основой охраны природы является экология.
В нашей стране охрана природы является общенародной зада чей. На съездах КПСС постоянно рассматриваются общие вопросы по защите окружающей среды. Действуют законы «Об охране природы» в РСФСР н других союзных республиках. Приняты общесоюзные законодательства по охране н использованию всех видов природных ресурсов — почвы, воздуха, воды, лесэ, недр, животных. Разработана система государственных стандартов, устанавливающая нормы и требования к выбросу вредных веществ в атмосферу, гидросферу н т. п.
Организацией и работой по охране природы занимаются Совет Министров СССР, союзных и автономных республик, исполни тельные комитеты Советов народных депутатов всех уровней, министерства н государственные комитеты. Содействие государствен ным органам в проведении мероприятий по охране природы и про паганде природоохранительных знаний оказывают общества охраны природы. Заключены международные соглашения по защите ок ружающей среды с социалистическими и капиталистическими (США. Франция и др.) странами. Функционируют межправнтельст венная организация «Программа ООН по окружающей среде» (ЮНЕП) и Международный союз охраны природы (МСОП).
Мероприятия по охране природы
Почва — плодородный слой земли, служит для производства органического вещества, в том числе продуктов питания, и необ ходнма для минерализации умерших организмов. К мероприятиям по защите почвы относятся: 1) борьба с эрозией — водной, вет ровой, механической, промышленной; 2) мелиорация — улучшение земель путем устранения избытка или недостатка влаги, снижения засоленности; 3) рекультивация — восстановление плодородия, утраченного вследствие производственной деятельности; 4) борьба с загрязнением почв.
Воздух — источник кислорода для дыхания и разнообразных промышленных реакций окисления; источник углекислого газа для фотосинтеза; защита от космических излучений; аккумулятор тепла и регулятор климатических условий. Мероприятия по защите воздуха от загрязнений, загазованности и заражения: 1) усовершенствование технологических процессов в целях уменьшения выбросов в атмосферу дыма, пыли, газов, радиоактивных веществ; 2) строительство очистных сооружений; 3) улучшение состава топлива и аппаратов дли его сжигания; 4) рациональное размещение источников выброса в атмосферу и расширение площадей зеленых насаждений.
Вода — важнейший и незаменимый природный ресурс, необходимый для жизнедеятельности животных и растений; важный компонент дли промышленного в сельскохозяйственного производства; источник дешевой энергии; среда обитания многих живых существ; регулятор климатических условий. Мероприятия по защите воды включают: 1) использование замкнутого цикла водоснабжения на предприятиях; 2) комплексную очистку сточных вод; 3) утилизацию стоков на полях орошения и специализированных предприятиях; 4) совершенствование технологии орошаемого земледелия; 5) очистку водоемов; 6) предотвращение загрязнения водоемов.
Растительный мир благодаря фотосинтезу обогащает атмосферу кислородом и освобождает от излишков углекислого газа, синтезирует простейшие углеводы, служащие для дальнейшего образования углеводов, белков и жиров. Растения используют как пищевые и кормовые продукты, для изготовления одежды, строительных материалов, лекарств и др. Лес — важнейший растительный ресурс, является главным поставщиком кислорода в атмосферу ; важнейшим климатическим и биологическим фактором; необходимым условием охраны воздуха, воды и почв; источником древесины н других веществ; зоной пчеловодства, охоты и заготовок. Лесоохранные мероприятия заключаются в охране от рубки почво-, водо- и полезащитных лесов; лесовосстановнтельных посадках; в осушении лесных массивов, борьбе с вредителями и болезнями леса; профилактике лесных пожаров и борьбе с ними; защитном лесоразведении.
Животный мир — одно нз основных природных богатств. Мероприятия по охране животных: 1) охрана промысловых животных, морских зверей, рыб и птиц; 2) охрана редких н находящихся на грани исчезновения животных, рыб и птиц; 3) охрана среды обитания, условий размножения и путей миграции; 4) регулирование численности в целях охраны здоровья и предотвращения ущерба народному хозяйству и т. п.
Большое значение для охраны растительного и животного мн ра, а также природных ландшафтов имеют заповедники, заказники и национальные парки.
К природоохранительным мероприятиям машиностроительных поводов относятся: !) очистка выбросов воздуха от пылей и туманов; 2) улавливание вредных газов и паров; 3) рассеяние выбросов воздуха через высотные трубы; 4) комплексная очистка сточных вод от механических н маслосодержащих примесей, металлов и их солей; 5) нейтрализация сточных вод; 6) многократное разбавление стоков; 7) утилизация н ликвидация промышленных отходов; 8) защита населения от шума, инфразвука и вибраций.