- Система отверстия
- Система вала
- A
- B
- C
- CD
- D
- E
- EF
- F
- FG
- G
- H1-H6
- H7-H11
- H12-H18
- JS1-JS6
- JS7-JS11
- JS12-JS18
- J
- K
- M
- N
- P
- R
- S
- T
- U
- V
- X
- Y
- Z
- ZA
- ZB
- ZC
Номинал. размер, мм |
H12 | H13 | H14 | H15 | H16 | H17 | H18 |
---|---|---|---|---|---|---|---|
Предельные отклонения, мм | |||||||
До 3 включ. | +0.1 0 |
+0.14 0 |
+0.25 0 |
+0.4 0 |
+0.6 0 |
||
Св. 3 до 6 | +0.12 0 |
+0.18 0 |
+0.3 0 |
+0.48 0 |
+0.75 0 |
+1.2 0 |
+1.8 0 |
Св. 6 до 10 | +0.15 0 |
+0.22 0 |
+0.36 0 |
+0.58 0 |
+0.9 0 |
+1.5 0 |
+2.2 0 |
Св. 10 до 18 | +0.18 0 |
+0.27 0 |
+0.43 0 |
+0.7 0 |
+1.1 0 |
+1.8 0 |
+2.7 0 |
Св. 18 до 30 | +0.21 0 |
+0.33 0 |
+0.52 0 |
+0.84 0 |
+1.3 0 |
+2.1 0 |
+3.3 0 |
Св. 30 до 50 | +0.25 0 |
+0.39 0 |
+0.62 0 |
+1 0 |
+1.6 0 |
+2.5 0 |
+3.9 0 |
Св. 50 до 80 | +0.3 0 |
+0.46 0 |
+0.74 0 |
+1.2 0 |
+1.9 0 |
+3 0 |
+4.6 0 |
Св. 80 до 120 | +0.35 0 |
+0.54 0 |
+0.87 0 |
+1.4 0 |
+2.2 0 |
+3.5 0 |
+5.4 0 |
Св. 120 до 180 | +0.4 0 |
+0.63 0 |
+1 0 |
+1.6 0 |
+2.5 0 |
+4 0 |
+6.3 0 |
Св. 180 до 250 | +0.46 0 |
+0.72 0 |
+1.15 0 |
+1.85 0 |
+2.9 0 |
+4.6 0 |
+7.2 0 |
Св. 250 до 315 | +0.52 0 |
+0.81 0 |
+1.3 0 |
+2.1 0 |
+3.2 0 |
+5.2 0 |
+8.1 0 |
Св. 315 до 400 | +0.57 0 |
+0.89 0 |
+1.4 0 |
+2.3 0 |
+3.6 0 |
+5.7 0 |
+8.9 0 |
Св. 400 до 500 | +0.63 0 |
+0.97 0 |
+1.55 0 |
+2.5 0 |
+4 0 |
+6.3 0 |
+9.7 0 |
Св. 500 до 630 | +0.7 0 |
+1.1 0 |
+1.75 0 |
+2.8 0 |
+4.4 0 |
+7 0 |
+11 0 |
Св. 630 до 800 | +0.8 0 |
+1.25 0 |
+2 0 |
+3.2 0 |
+5 0 |
+8 0 |
+12.5 0 |
Св. 800 до 1000 | +0.9 0 |
+1.4 0 |
+2.3 0 |
+3.6 0 |
+5.6 0 |
+9 0 |
+14 0 |
Св. 1000 до 1250 | +1.05 0 |
+1.65 0 |
+2.6 0 |
+4.2 0 |
+6.6 0 |
+10.5 0 |
+16.5 0 |
Св. 1250 до 1600 | +1.25 0 |
+1.95 0 |
+3.1 0 |
+5 0 |
+7.8 0 |
+12.5 0 |
+19.5 0 |
Св. 1600 до 2000 | +1.5 0 |
+2.3 0 |
+3.7 0 |
+6 0 |
+9.2 0 |
+15 0 |
+23 0 |
Св. 2000 до 2500 | +1.75 0 |
+2.8 0 |
+4.4 0 |
+7 0 |
+11 0 |
+17.5 0 |
+28 0 |
Св. 2500 до 3150 | +2.1 0 |
+3.3 0 |
+5.4 0 |
+8.6 0 |
+13.5 0 |
+21 0 |
+33 0 |
H14, H15, H16, H17, H18 не применяют для номинальных размеров до 1 мм включительно.
Для данного размера
отверстия: Ø16+0,035+0,070определить
значение допуска: TD
= ES
– EI
= 0,070 – 0,030 = 0,040(мм) = 40мкм;
для полученного
расчетного
значения допуска по таблице допусков
(табл.1) подобрать ближайшее стандартное
значение и соответствующий номер
квалитета:
для размера Ø16
(интервал cв.10
до18) ближайший к 40мкм стандартный допуск
– 43мкм,
что соответствует 9-му
квалитету:
IT9
= 43мкм;
2.Определить стандартное значение основного отклонения.
Из двух расчетных
предельных отклонений основным
является ближайшее
к нулевой линии
(в данном случае нижнее)
EI
= +0,03 = 30мкм;
По таблицам основных
отклонений для отверстий
(нижних)
(прилож.3) ближайшее стандартное
значение к 30мкм для размера Ø16 (интервал
cв.14
до18) соответствует 32мкм
(условное обозначение – буква Е)
3.Определить второе предельное отклонение – es .
Зная стандартное
основное отклонение – EI
= 0,032мм (Е)
и стандартный допуск – TD
= 0,043мм (IT9),
определить второе предельное отклонение:
так как TD
= ES
–EI,
тогда
ES
= TD
+EI
= 0,043 + 0,032 = 0,075(мкм).
Следовательно,
буквенное (условное) обозначение поля
допуска и стандартные числовые предельные
отклонения заданного отверстия:
+0,075
+0,032
Ø16Е9(
):
4. Определить систему посадок для отверстия ø16е9:
Определить систему
посадок позволяет выявление основной
детали. Полученное поле допуска (Е9) не
является
полем допуска основного отверстия,
следовательно, основной
деталью в
этом соединении будет вал
(h),
что и определит систему
посадок.
Таким образом,
отверстие с полем допуска Е9
образует с
валом номинального размера Ø16
посадку в системе
вала (вал
– основная деталь(h);
5. Определить предельные отклонения вала:
Чтобы определить
допуск и квалитет вала, необходимо
учесть заданное условие: Т(S)
= 0,070мм, а так
как T(S)
= TD
+ Td,
то, зная величину допуска отверстия
TD
= 0,043мм
(IT6),
можно определить допуск вала:
Td
= T(S)
– TD
= 0,070 – 0,043 = 0,027(мм),
По таблице допусков
ближайшее стандартное значение допуска
вала для размера 16
совпадает с расчетным значением допуска
и соответствует 8-му квалитету IT8
= 0,027мм ;
Так как для основного
вала es
= 0, ei=
– Td,
следовательно
ei
= – 0,027мм
а поле допуска
вала принимает вид: Ø16h8(
– 0,027)
В результате: обозначение на рабочих
чертежах стандартных полей допусков
и предельных отклонений вала и отверстия,
а так же обозначение посадки на сборочном
чертеже:
Приложение 3
ЧИСЛОВЫЕ ЗНАЧЕНИЯ
ОСНОВНЫХ (ВЕРХНИХ es)
ОТКЛОНЕНИЙ ВАЛОВ.
Интервал |
Основные |
||||||||||||
a1 |
b1 |
c |
cd |
d |
e |
ef |
f |
fg |
g |
h |
js2 |
||
Свыше |
До |
Для |
|||||||||||
3 |
–270 |
–140 |
–60 |
–34 |
–20 |
–14 |
–10 |
–6 |
–4 |
–2 |
0 |
Предельные |
|
3 |
6 |
–270 |
‑140 |
–70 |
–46 |
–30 |
–20 |
–14 |
–10 |
–6 |
–4 |
0 |
|
6 |
10 |
–280 |
–150 |
–80 |
–56 |
–40 |
–25 |
–18 |
–13 |
–8 |
–5 |
0 |
|
10 |
14 |
–290 |
‑150 |
–95 |
– |
–50 |
–32 |
– |
–16 |
– |
–6 |
0 |
|
14 |
18 |
||||||||||||
18 |
24 |
–300 |
‑160 |
–110 |
‑ |
–65 |
–40 |
– |
–20 |
– |
–7 |
0 |
|
24 |
30 |
||||||||||||
30 |
40 |
–310 |
–170 |
–120 |
‑ |
–80 |
–50 |
– |
-25 |
– |
–9 |
0 |
|
40 |
50 |
–320 |
–180 |
–130 |
|||||||||
50 |
65 |
–340 |
–190 |
–140 |
‑ |
–100 |
–60 |
– |
–30 |
– |
–10 |
0 |
|
65 |
80 |
–360 |
–200 |
–150 |
|||||||||
80 |
100 |
–380 |
–220 |
–170 |
‑ |
–120 |
–72 |
– |
–36 |
– |
–12 |
0 |
|
100 |
120 |
–410 |
–240 |
–180 |
|||||||||
120 |
140 |
–460 |
–260 |
–200 |
– |
–145 |
–85 |
– |
–43 |
– |
–14 |
0 |
|
140 |
160 |
–520 |
–280 |
–210 |
|||||||||
160 |
180 |
–580 |
–310 |
–230 |
|||||||||
180 |
200 |
–660 |
‑340 |
–240 |
– |
–170 |
–100 |
– |
–50 |
– |
‑15 |
0 |
|
200 |
225 |
–740 |
–380 |
–260 |
|||||||||
225 |
250 |
–820 |
–420 |
–280 |
|||||||||
250 |
280 |
–920 |
–480 |
–300 |
– |
–190 |
–110 |
– |
–56 |
– |
–17 |
0 |
|
280 |
315 |
–1050 |
–540 |
–330 |
|||||||||
315 |
355 |
–1200 |
–600 |
–360 |
– |
–210 |
–125 |
– |
–62 |
– |
–18 |
0 |
|
355 |
400 |
–1350 |
–680 |
–400 |
|||||||||
400 |
450 |
–1500 |
–760 |
–440 |
– |
–230 |
–135 |
– |
–68 |
– |
–20 |
0 |
|
450 |
500 |
–1650 |
–840 |
–480 |
1
Основные отклонения а и b
не предусмотрены для размеров менее 1
мм.
2
Для полей допусков от js7
до js11
нечетные числовые значения IT
могут быть округлены до ближайшего
меньшего четного числа, чтобы предельные
отклонения
были выражены целым числом микрометров.
3
Специальный случай: поле допуска m7
предусмотрено лишь для размеров свыше
3 мм.
ЧИСЛОВЫЕ ЗНАЧЕНИЯ
ОСНОВНЫХ (НИЖНИХ ei)
ОТКЛОНЕНИЙ ВАЛОВ.
Интервал |
Основные |
|||||||||||||||||||
j (для |
k (для |
m3 |
n |
p |
r |
s |
t |
u |
v |
x |
y |
z |
za |
zb |
zc |
|||||
Свыше |
До |
5 |
7 |
8 |
От |
До |
Для |
|||||||||||||
3 |
–2 |
–4 |
–6 |
0 |
0 |
+2 |
+4 |
+6 |
+10 |
+14 |
— |
+18 |
— |
+20 |
— |
+26 |
+32 |
+40 |
+60 |
|
3 |
6 |
–2 |
–4 |
– |
+1 |
0 |
+4 |
+8 |
+12 |
+15 |
+19 |
— |
+23 |
— |
+28 |
— |
+35 |
+42 |
+50 |
+80 |
6 |
10 |
–2 |
–5 |
– |
+1 |
0 |
+6 |
+10 |
+15 |
+19 |
+23 |
— |
+28 |
— |
+34 |
— |
+42 |
+52 |
+67 |
+97 |
10 |
14 |
–3 |
–6 |
– |
+1 |
0 |
+7 |
+12 |
+18 |
+23 |
+28 |
— |
+33 |
— |
+40 |
— |
+50 |
+64 |
+90 |
+130 |
14 |
18 |
+39 |
+45 |
— |
+60 |
+77 |
+108 |
+150 |
||||||||||||
18 |
24 |
–4 |
–8 |
– |
+2 |
0 |
+8 |
+15 |
+22 |
+28 |
+35 |
— |
+41 |
+47 |
+54 |
+63 |
+73 |
+98 |
+136 |
+188 |
24 |
30 |
+41 |
+48 |
+55 |
+64 |
+75 |
+88 |
+118 |
+160 |
+218 |
||||||||||
30 |
40 |
–5 |
–10 |
– |
+2 |
0 |
+9 |
+17 |
+26 |
+34 |
+43 |
+48 |
+60 |
+68 |
+80 |
+94 |
+112 |
+148 |
+200 |
+274 |
40 |
50 |
+54 |
+70 |
+81 |
+97 |
+114 |
+136 |
+180 |
+242 |
+325 |
||||||||||
50 |
65 |
–7 |
–12 |
– |
+2 |
0 |
+11 |
+20 |
+32 |
+41 |
+53 |
+66 |
+87 |
+102 |
+122 |
+144 |
+172 |
+226 |
+300 |
+405 |
65 |
80 |
+43 |
+59 |
+75 |
+102 |
+120 |
+146 |
+174 |
+210 |
+274 |
+360 |
+480 |
||||||||
80 |
100 |
–9 |
–15 |
– |
+3 |
0 |
+13 |
+23 |
+37 |
+51 |
+71 |
+91 |
+124 |
+146 |
+178 |
+214 |
+258 |
+335 |
+445 |
+585 |
100 |
120 |
+54 |
+79 |
+104 |
+144 |
+172 |
+210 |
+254 |
+310 |
+400 |
+525 |
+690 |
||||||||
120 |
140 |
–11 |
–18 |
– |
+3 |
0 |
+15 |
+27 |
+43 |
+63 |
+92 |
+122 |
+170 |
+202 |
+248 |
+300 |
+365 |
+470 |
+620 |
+800 |
140 |
160 |
+65 |
+100 |
+134 |
+190 |
+228 |
+280 |
+340 |
+415 |
+535 |
+700 |
+900 |
||||||||
160 |
180 |
+68 |
+108 |
+146 |
+210 |
+252 |
+310 |
+380 |
+465 |
+600 |
+780 |
+1000 |
||||||||
180 |
200 |
–13 |
–21 |
– |
+4 |
0 |
+17 |
+31 |
+50 |
+77 |
+122 |
+166 |
+236 |
+284 |
+350 |
+425 |
+520 |
+670 |
+880 |
+1150 |
200 |
225 |
+80 |
+130 |
+180 |
+258 |
+310 |
+385 |
+470 |
+575 |
+740 |
+960 |
+1250 |
||||||||
225 |
250 |
+84 |
+140 |
+196 |
+284 |
+340 |
+425 |
+520 |
+640 |
+820 |
+1050 |
+1350 |
||||||||
250 |
280 |
–16 |
–26 |
‑ |
+4 |
0 |
+20 |
+34 |
+56 |
+94 |
+158 |
+218 |
+315 |
+385 |
+475 |
+580 |
+710 |
+920 |
+1200 |
+1550 |
280 |
315 |
+98 |
+170 |
+240 |
+350 |
+425 |
+525 |
+650 |
+790 |
+1000 |
+1300 |
+1700 |
||||||||
315 |
355 |
–18 |
–28 |
‑ |
+4 |
0 |
+21 |
+37 |
+62 |
+108 |
+190 |
+268 |
+390 |
+475 |
+590 |
+730 |
+900 |
+1150 |
+1500 |
+1900 |
355 |
400 |
+114 |
+208 |
+294 |
+435 |
+530 |
+660 |
+820 |
+1000 |
+1300 |
+1650 |
+2100 |
||||||||
400 |
450 |
–20 |
–32 |
‑ |
+5 |
0 |
+23 |
+40 |
+68 |
+126 |
+232 |
+330 |
+490 |
+595 |
+740 |
+920 |
+1100 |
+1450 |
+1850 |
+2400 |
450 |
500 |
+132 |
+252 |
+360 |
+540 |
+660 |
+820 |
+1000 |
+1250 |
+1600 |
+2100 |
+2600 |
1
Основные отклонения а и b
не предусмотрены для размеров менее 1
мм.
2
Для полей допусков от js7
до js11
нечетные числовые значения IT
могут быть округлены до ближайшего
меньшего четного числа, чтобы предельные
отклонения
были выражены целым числом микрометров.
3
Специальный случай: поле допуска m
7 предусмотрено лишь для размеров свыше
3 мм.
ЧИСЛОВЫЕ ЗНАЧЕНИЯ
ОСНОВНЫХ (НИЖНИХ EI)
ОТКЛОНЕНИЙ ОТВЕРСТИЙ.
Интервал |
Основные |
||||||||||||
A1 |
B1 |
C |
CD |
D |
E |
EF |
F |
FG |
G |
H |
Js2 |
||
Свыше |
До |
Для |
|||||||||||
3 |
+270 |
+140 |
+60 |
+34 |
+20 |
+14 |
+10 |
+6 |
+4 |
+2 |
0 |
Предельные |
|
3 |
6 |
+270 |
+140 |
+70 |
+46 |
+30 |
+20 |
+14 |
+10 |
+6 |
+4 |
0 |
|
6 |
10 |
+280 |
+150 |
+80 |
+56 |
+40 |
+25 |
+18 |
+13 |
+8 |
+5 |
0 |
|
10 |
14 |
+290 |
+150 |
+95 |
– |
+50 |
+32 |
– |
+16 |
– |
+6 |
0 |
|
14 |
18 |
||||||||||||
18 |
24 |
+300 |
+160 |
+110 |
‑ |
+65 |
+40 |
– |
+20 |
– |
+7 |
0 |
|
24 |
30 |
||||||||||||
30 |
40 |
+310 |
+170 |
+120 |
– |
+80 |
+50 |
– |
+25 |
– |
+9 |
0 |
|
40 |
50 |
+320 |
+180 |
+130 |
|||||||||
50 |
65 |
+340 |
+190 |
+140 |
‑ |
+100 |
+60 |
– |
+30 |
– |
+10 |
0 |
|
65 |
80 |
+360 |
+200 |
+150 |
|||||||||
80 |
100 |
+380 |
+220 |
+170 |
‑ |
+120 |
+72 |
– |
+36 |
– |
+12 |
0 |
|
100 |
120 |
+410 |
+240 |
+180 |
|||||||||
120 |
140 |
+460 |
+260 |
+200 |
– |
+145 |
+85 |
– |
+43 |
– |
+14 |
0 |
|
140 |
160 |
+520 |
+280 |
+210 |
|||||||||
160 |
180 |
+580 |
+310 |
+230 |
|||||||||
180 |
200 |
+660 |
+340 |
+240 |
– |
+170 |
+100 |
– |
+50 |
– |
+15 |
0 |
|
200 |
225 |
+740 |
+380 |
+260 |
|||||||||
225 |
250 |
+820 |
+420 |
+280 |
|||||||||
250 |
280 |
+920 |
+480 |
+300 |
– |
+190 |
+110 |
– |
+56 |
– |
+17 |
0 |
|
280 |
315 |
+1050 |
+540 |
+330 |
|||||||||
315 |
355 |
+1200 |
+600 |
+360 |
– |
+210 |
+125 |
– |
+62 |
– |
+18 |
0 |
|
355 |
400 |
+1350 |
+680 |
+400 |
|||||||||
400 |
450 |
+1500 |
+760 |
+440 |
– |
+230 |
+135 |
– |
+68 |
– |
+20 |
0 |
|
450 |
500 |
+1650 |
+840 |
+480 |
ЧИСЛОВЫЕ ЗНАЧЕНИЯ
ОСНОВНЫХ (ВЕРХНИХ ES)
ОТКЛОНЕНИЙ ОТВЕРСТИЙ.
Интервал |
Основные |
Δ, мкм |
||||||||||||||
J |
K3 |
M3 |
N3 |
|||||||||||||
Для |
Для |
|||||||||||||||
Свыше |
До |
6 |
7 |
8 |
До |
Св. 8 |
До |
Св. 8 |
До 8 |
Св. 8 |
3 |
4 |
5 |
6 |
7 |
8 |
3 |
+2 |
+4 |
+6 |
0 |
0 |
–2 |
–2 |
–4 |
–4 |
0 |
0 |
0 |
0 |
0 |
0 |
|
3 |
6 |
+5 |
+6 |
+10 |
–1+ |
– |
–4+ |
–4 |
–8+ |
0 |
1 |
1,5 |
1 |
3 |
4 |
6 |
6 |
10 |
+5 |
+8 |
+12 |
–1+ |
– |
–6+ |
–6 |
–10+ |
0 |
1 |
1,5 |
2 |
3 |
6 |
7 |
10 |
14 |
+6 |
+10 |
+15 |
–1+ |
‑ |
–7+ |
–7 |
–12+ |
0 |
1 |
2 |
3 |
3 |
7 |
9 |
14 |
18 |
|||||||||||||||
18 |
24 |
+8 |
+12 |
+20 |
–2+ |
‑ |
–8+ |
–8 |
–15+ |
0 |
1,5 |
2 |
3 |
4 |
8 |
12 |
24 |
30 |
|||||||||||||||
30 |
40 |
+10 |
+14 |
+24 |
–2+ |
‑ |
–9+ |
–9 |
–17+ |
0 |
1,5 |
3 |
4 |
5 |
9 |
14 |
40 |
50 |
|||||||||||||||
50 |
65 |
+13 |
+18 |
+28 |
–2+ |
‑ |
–11+ |
–11 |
–20+ |
0 |
2 |
3 |
5 |
6 |
11 |
16 |
65 |
80 |
|||||||||||||||
80 |
100 |
+16 |
+22 |
+34 |
–3+ |
‑ |
–13+ |
–13 |
–23+ |
0 |
2 |
4 |
5 |
7 |
13 |
19 |
100 |
120 |
|||||||||||||||
120 |
140 |
+18 |
+26 |
+41 |
–3+ |
– |
–15+ |
–15 |
–27+ |
0 |
3 |
4 |
6 |
7 |
15 |
23 |
140 |
160 |
|||||||||||||||
160 |
180 |
|||||||||||||||
180 |
200 |
+22 |
+30 |
+47 |
–4+ |
‑ |
–17+ |
–17 |
–31+ |
0 |
3 |
4 |
6 |
9 |
17 |
26 |
200 |
225 |
|||||||||||||||
225 |
250 |
|||||||||||||||
250 |
280 |
+25 |
+36 |
+55 |
–4+ |
– |
–20+ |
–20 |
–34+ |
0 |
4 |
4 |
7 |
9 |
20 |
29 |
280 |
315 |
|||||||||||||||
315 |
355 |
+29 |
+39 |
+60 |
–4+ |
‑ |
–21+ |
–21 |
–37+ |
0 |
4 |
5 |
7 |
11 |
21 |
32 |
355 |
400 |
|||||||||||||||
400 |
450 |
+33 |
+43 |
+66 |
–5+ |
‑ |
–23+ |
–23 |
–40+ |
0 |
5 |
5 |
7 |
13 |
23 |
34 |
450 |
500 |
ЧИСЛОВЫЕ ЗНАЧЕНИЯ
ОСНОВНЫХ (ВЕРХНИХ ES)
ОТКЛОНЕНИЙ ОТВЕРСТИЙ.
Интервал |
Основные |
1
2
3
4
5 |
||||||||||||
от |
P |
R |
S |
T |
U |
V |
X |
Y |
Z |
ZA |
ZB |
ZC |
||
Свыше |
До |
До 7 квалитета |
Для |
|||||||||||
3 |
Отклонения как |
-6 |
-10 |
-14 |
— |
-18 |
— |
-20 |
— |
-26 |
-32 |
-40 |
-60 |
|
3 |
6 |
-12 |
-15 |
–19 |
— |
-23 |
— |
-28 |
— |
-35 |
-42 |
-50 |
-80 |
|
6 |
10 |
-15 |
-19 |
-23 |
— |
-28 |
— |
-34 |
— |
-42 |
-52 |
-67 |
-97 |
|
10 |
14 |
-18 |
-23 |
-28 |
— |
-33 |
— |
-40 |
— |
-50 |
-64 |
-90 |
-130 |
|
14 |
18 |
-39 |
-45 |
— |
-60 |
-77 |
-108 |
-150 |
||||||
18 |
24 |
-22 |
-28 |
-35 |
— |
-41 |
-47 |
-54 |
-63 |
-73 |
-98 |
-136 |
-188 |
|
24 |
30 |
+41 |
-48 |
-55 |
-64 |
-75 |
-88 |
-118 |
-160 |
-218 |
||||
30 |
40 |
-26 |
-34 |
-43 |
+48 |
-60 |
-68 |
-80 |
-94 |
-112 |
-148 |
-200 |
-274 |
|
40 |
50 |
+54 |
-70 |
-81 |
-97 |
-114 |
-136 |
-180 |
-242 |
-325 |
||||
50 |
65 |
-32 |
-41 |
-53 |
-66 |
-87 |
-102 |
-122 |
-144 |
-172 |
-226 |
-300 |
-405 |
|
65 |
80 |
-43 |
-59 |
-75 |
-102 |
-120 |
-146 |
-174 |
-210 |
-274 |
-360 |
-480 |
||
80 |
100 |
-37 |
-51 |
-71 |
-91 |
-124 |
-146 |
-178 |
-214 |
-258 |
-335 |
-445 |
-585 |
|
100 |
120 |
-54 |
-79 |
-104 |
-144 |
-172 |
-210 |
-254 |
-310 |
-400 |
-525 |
-690 |
||
120 |
140 |
-43 |
-63 |
-92 |
-122 |
-170 |
-202 |
-248 |
-300 |
-365 |
-470 |
-620 |
-800 |
|
140 |
160 |
-65 |
-100 |
-134 |
-190 |
-228 |
-280 |
-340 |
-415 |
-535 |
-700 |
-900 |
||
160 |
180 |
-68 |
-108 |
-146 |
-210 |
-252 |
-310 |
-380 |
-465 |
-600 |
-780 |
-1000 |
||
180 |
200 |
-50 |
-77 |
-122 |
-166 |
-236 |
-284 |
-350 |
-425 |
-520 |
-670 |
-880 |
-1150 |
|
200 |
225 |
-80 |
-130 |
-180 |
-258 |
-310 |
-385 |
-470 |
-575 |
-740 |
-960 |
-1250 |
||
225 |
250 |
-84 |
-140 |
-196 |
-284 |
-340 |
-425 |
-520 |
-640 |
-820 |
-1050 |
-1350 |
||
250 |
280 |
-56 |
-94 |
-158 |
-218 |
-315 |
-385 |
-475 |
-580 |
-710 |
-920 |
-1200 |
-1550 |
|
280 |
315 |
-98 |
-170 |
-240 |
-350 |
-425 |
-525 |
-650 |
-790 |
-1000 |
-1300 |
-1700 |
||
315 |
355 |
-62 |
-108 |
-190 |
-268 |
-390 |
-475 |
-590 |
-730 |
-900 |
-1150 |
-1500 |
-1900 |
|
355 |
400 |
-114 |
-208 |
-294 |
-435 |
-530 |
-660 |
-820 |
-1000 |
-1300 |
-1650 |
-2100 |
||
400 |
450 |
-68 |
-126 |
-232 |
-330 |
-490 |
-595 |
-740 |
-920 |
-1100 |
-1450 |
-1850 |
-2400 |
|
450 |
500 |
-132 |
-252 |
-360 |
-540 |
-660 |
-820 |
-1000 |
-1250 |
-1600 |
-2100 |
-2600 |
Соседние файлы в папке Раздаточный материал
- #
- #
- #
- #
- #
- #
- #
Здравствуйте на этой странице я собрала теорию и практику с примерами решения задач по разделу: допуски и посадки, с решением по каждой теме, чтобы вы смогли подготовиться к экзамену или освежить память перед контрольной работой!
Если что-то непонятно — вы всегда можете написать мне в WhatsApp и я вам помогу!
Допуски и посадки в метрологии
Посадка — это характер соединения двух деталей, определяемый разностью их размеров до сборки.
Зазор — это разность между размерами отверстия и вала до сборки, если отверстие больше размера вала.
Натяг — это разность между размерами вала и отверстия до сборки, если размер вала больше размера отверстия.
Допуск посадки — это сумма допусков отверстия и вала, составляющих соединение.
Посадка с зазором — это посадка, при которой всегда образуется зазор в соединении, т.е. наименьший предельный размер отверстия больше наибольшего предельного размера вала или равен ему.
Посадка с натягом — это посадка, при которой всегда образуется зазор в соединении, т.е. наименьший предельный размер отверстия больше наибольшего предельного размера вала или равен ему.
Переходная посадка — это посадка, при которой возможно получение как зазора так и натяга в соединении, в зависимости от действительных размеров отверстия и вала.
Вал — это термин, условно применяемый для обозначения наружных элементов деталей, включая и нецилиндрические элементы.
Отверстие — это термин, условно применяемый для обозначения внутренних элементов деталей, включая и нецилиндрические элементы.
Размер — это числовое значение линейной величины (диаметра, длины и т.п.) в выбранных единицах измерения.
Квалитет — это совокупность допусков, рассматриваемых как соответствующие одному уровню точности для всех номинальных размеров.
Нормирование точности размеров деталей гладких цилиндрических соединений
Взаимозаменяемость. Основные понятия
Представьте себе, что во время работы какой-то машины износилась или сломалась деталь. Что делать? Изготовить её своими силами? Это потребует много времени, да и не всегда возможно в силу целого ряда причин. Проще взять со склада запасную деталь и заменить ею вышедшую из строя.
Возможно эта страница вам будет полезна:
Конечно, новая деталь должна по своим размерам и форме точно соответствовать заменяемой. Иначе пришлось бы потратить много времени на её подгонку. Такая несложная замена стала возможной в современном производстве машин благодаря применению принципа взаимозаменяемости.
Взаимозаменяемость — это принцип конструирования, производства и эксплуатации машин и других изделий, обеспечивающий их бесподгоночную сборку (или замену при ремонте) из независимо изготовленных сопрягаемых деталей и элементов при соблюдении предъявляемых к машинам и изделиям технических требований.
Взаимозаменяемыми могут быть детали, узлы, изделия в целом. При сборке используются стандартные крепежные детали, подшипники качения, электротехнические, резиновые, пластмассовые изделия и агрегаты, получаемые по кооперации. Есть и другое определение взаимозаменяемости, но суть понятия не изменилась.
Взаимозаменяемость — это свойство независимо изготовленных с заданной точностью деталей и составных частей машин, приборов и других изделий обеспечивать возможность беспригоночной сборки (или замены при ремонте) сопрягаемых деталей в составные части, а составных частей — в изделия при соблюдении предъявляемых к составным частям и изделиям технических требований.
Виды взаимозаменяемости:
- полная — обеспечивает возможность беспригоночной сборки (или замены при ремонте) любых независимо изготовленных с заданной точностью однотипных деталей в сборочные единицы или изделия при соблюдении предъявляемых к ним (сборочным единицам или изделиям) технических требований по всем параметрам качества. При полной взаимозаменяемости упрощается сборка, которая сводится к простому соединению деталей рабочими невысокой квалификации, сборочный процесс точно нормируется во времени, согласуется с темпом работы конвейера, и создаются возможности организации производства поточным методом, появляются возможности для автоматизации процессов изготовления и сборки изделий, упрощается ремонт изделий, т.к. любая износившаяся или поломанная деталь могут быть заменены запасными. Например, замена электрической лампочки или сломанной иглы в швейной машинке не вызывает удивления, хотя патрон для лампочки и лампочка, швейная машинка и игла были изготовлены в разное время, на разных предприятиях и даже, может быть, в разных странах;
- неполная (ограниченная) — когда для получения требуемой точности сборки применяют групповой подбор деталей (селективную сборку), компенсаторы, регулирование положения некоторых частей машин и приборов, пригонку и другие дополнительные технологические мероприятия при обязательном выполнении требований к качеству сборочных единиц и изделий. Если в телевизоре сгорел кинескоп, то новый устанавливают в старый корпус, на то же место (полная взаимозаменяемость по размерам), но, как правило, требуется регулировать некоторые характеристики, подстраивать их до требуемого уровня, т.е. по таким элементам телевизор обладает ограниченной взаимозаменяемостью;
- внешняя — это взаимозаменяемость покупных и кооперируемых изделий и сборочных единиц по эксплуатационным показателям, а также по размерам и форме присоединительных поверхностей. Внешняя взаимозаменяемость присуща только готовым изделиям или узлам. Например, электрические двигатели (по частоте вращения вала и мощности, а также по точности размера между присоединительными крепёжными отверстиями); подшипники качения (по точности самого подшипника, а также по точности размеров посадочных поверхностей — отверстию внутреннего кольца и наружной поверхности наружного кольца);
- внутренняя — это взаимозаменяемость деталей, входящих в узел, или узлов, входящих в изделие. Например, в подшипниках качения — взаимозаменяемость тел качения и колец;
- функциональная — это взаимозаменяемость по основным эксплуатационным показателям работы изделия, определяющим его служебные функции. Одно из главных условий обеспечения функциональной взаимозаменяемости — это установление связей эксплуатационных показателей с функциональными параметрами и независимое изготовление деталей и составных частей по этим параметрам с точностью, определяемой исходя из допускаемых отклонений эксплуатационных показателей в конце срока их службы.
Уровень взаимозаменяемости на производстве определяется коэффициентом взаимозаменяемости:

где — трудоемкость изготовления взаимозаменяемых деталей;
— трудоемкость изготовления изделия в целом.
Две или несколько деталей, подвижно или неподвижно соединенные друг с другом, называются соединением (рис. 1.1).
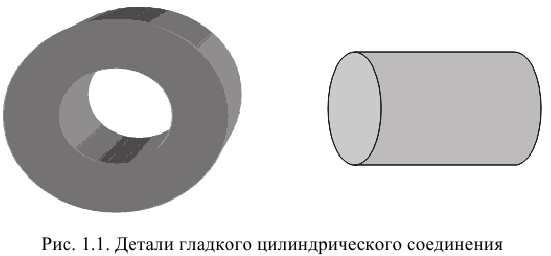
В соединении двух деталей, входящих одна в другую, различают охватывающую и охватываемую поверхности. Для гладких цилиндрических соединений охватывающая поверхность называется отверстием, а охватываемая — валом. Соответствующие им размеры — диаметр отверстия и диаметр вала (рис. 1.2).
Понятие точности, линейные размеры и отклонения
Точностью изготовления называют степень приближения действительных значений геометрических и других параметров деталей и изделий к их заданным значениям, указанным в чертежах или технических требованиях. Достичь заданной точности — значит изготовить детали и собрать механизм так, чтобы погрешности геометрических, электрических и других параметров находились в установленных пределах.
Точность размеров — это степень приближения действительных значений размеров деталей машин к размерам, заданным на чертеже.
На рабочих чертежах деталей проставляют в первую очередь номинальные размеры.
Номинальный размер — это основной размер, определенный исходя из функционального назначения детали и служащий началом отсчета отклонений. Общий для отверстия и вала, составляющих соединение, номинальный размер называется номинальным размером соединения (см. рис. 1.2).
Есть и другое определение номинального размера. Номинальный размер — это размер, относительно которого определяют предельные размеры и который служит также началом отсчета отклонений. — обозначение номинального размера отверстия;
— обозначение номинального размера вала.
Обработать деталь точно по номинальному размеру практически невозможно из-за многочисленных погрешностей, влияющих на процесс обработки. Размеры обработанной детали отличаются от заданного номинального размера, поэтому их ограничивают двумя предельно допустимыми размерами, один из которых (больший) называется наибольшим предельным размером, а другой (меньший) — наименьшим предельным размером. В расчетах используются следующие обозначения: — наибольший предельный размер отверстия;
— наименьший предельный размер отверстия;
— наибольший предельный размер вала;
— наименьший предельный размер вала.
Действительный размер — размер, полученный в результате измерения с допустимой погрешностью. Например: — действительный размер отверстия;
— действительный размер вала.
Деталь является годной, если ее действительный размер больше наименьшего предельного размера, но не превосходит наибольшего предельного размера, т.е.
— условие годности деталей типа «отверстие»;
— условие годности деталей типа «вал». На чертежах вместо предельных размеров рядом с номинальным размером указывают два предельных отклонения — верхнее и нижнее.
Верхнее отклонение размера — это алгебраическая разность между наибольшим предельным и номинальным размерами.
Например:
— верхнее отклонение отверстия;
— верхнее отклонение вала.
Нижнее отклонение размера — это алгебраическая разность между наименьшим предельным и номинальным размерами.
Например:
— нижнее отклонение отверстия;
— нижнее отклонение вала.
Отклонения бывают положительными, отрицательными и равными нулю. Отклонения, равные нулю, в обозначении не указываются. На чертежах номинальные и предельные линейные размеры и их отклонения проставляют в миллиметрах без указания единицы физической величины.
Пример:
Зная предельные отклонения и используя формулы их расчета, можно рассчитать значения предельных размеров:
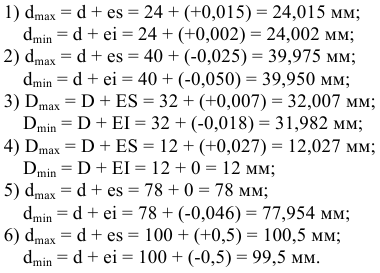
Допуски размеров, посадки и допуск посадки
Допуском размера называется разность между наибольшим и наименьшим предельными размерами или алгебраическая разность между верхним и нижним отклонениями.
Допуск обозначают буквой «Т» (от латинского Tolerance — допуск):
— допуск размера отверстия;
— допуск размера вала.
Для рассмотренных ранее примеров 1 — 6 (раздел 1.2) допуски размеров определятся следующим образом:
Допуск — величина всегда положительная. Допуск характеризует точность изготовления детали. Чем меньше допуск, тем труднее обрабатывать деталь, так как повышаются требования к точности станка, инструмента, приспособлений, квалификации рабочего. Неоправданно большие допуски снижают надежность и качество работы изделия.
В некоторых соединениях при различных сочетаниях предельных размеров отверстия и вала могут возникать зазоры или натяги. Характер соединения деталей, определяемый значениями получающихся в нем зазоров или натягов, называется посадкой. Посадка характеризует большую или меньшую свободу относительного перемещения соединяемых деталей или степень сопротивления их взаимному смещению.
Различают три группы посадок:
1) с гарантированным зазором;
2) переходные;
3) с гарантированным натягом.
Если размеры отверстия больше размеров вала, то в соединении возникает зазор (рис. 1.3).
Зазор — это положительная разность между размерами отверстия и вала:
— зазор;
— наибольший зазор;
— наименьший зазор
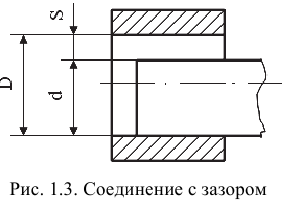
Если до сборки размеры вала больше размеров отверстия, то в соединении возникает натяг.
Натяг — это положительная разность между размерами вала и отверстия:
— натяг;
— наибольший натяг;
— наименьший натяг.
А теперь рассмотрим конкретное соединение:

Сразу сказать, что получится в соединении (зазор или натяг) довольно нелегко. Предположим, что это соединение с зазором. Рассчитаем предельные значения зазоров для данного конкретного соединения:

Как видим, минимальный зазор получился отрицательным. Это значит, что максимальный размер вала больше, чем минимальный размер отверстия
, а положительная разность между максимальным валом и минимальным отверстием — это натяг, причем максимальный

Таким образом, отрицательный минимальный зазор — это положительный максимальный натяг, т.е.

Таким образом, в рассматриваемом соединении при одном сочетании предельных размеров отверстия и вала может получиться зазор, который меняется от 0,025 мм до нуля , а при другом сочетании предельных размеров отверстия и вала может получиться натяг, который меняется от 0,015 мм до нуля
. То есть в данном соединении есть вероятность появления или зазора, или натяга. Причем вероятность появления зазора немного выше, чем вероятность появления натяга.
Такие посадки называются переходными.
Допуск посадки — это допуск зазора для посадок с гарантированным зазором (определяется как разность между наибольшим и наименьшим зазорами) или допуск натяга для посадок с гарантированным натягом (определяется как разность между наибольшим и наименьшим натягами). В переходных посадках допуск посадки — это сумма максимального зазора и максимального натяга.
Обозначение допуска посадки:
— допуск посадки для посадок с гарантированным зазором;
— допуск посадки для посадок с гарантированным натягом;
— допуск посадки для переходных посадок.
Для любой группы посадок допуск посадки можно определить по формуле

Возможно эта страница вам будет полезна:
Основные отклонения
Из двух предельных отклонений стандарт выделяет одно, которое называют основным. Основное отклонение — это одно из двух отклонении (верхнее или нижнее), ближайшее к номинальному размеру.
Для ранее приведенных шести примеров простановки отклонений (см. раздел 1.2) определим числовые значения основных отклонений:
1) +0,002; 2)-0,025; 3)+0,007; 4)0; 5)0; 6) не определено.
В шестом примере определить основное отклонение невозможно, оба отклонения равно удалены от номинального размера.
Основные отклонения обозначают буквами латинского алфавита (рис. 1.4):
- прописными буквами — основные отклонения отверстий

- строчными буквами — основные отклонения валов

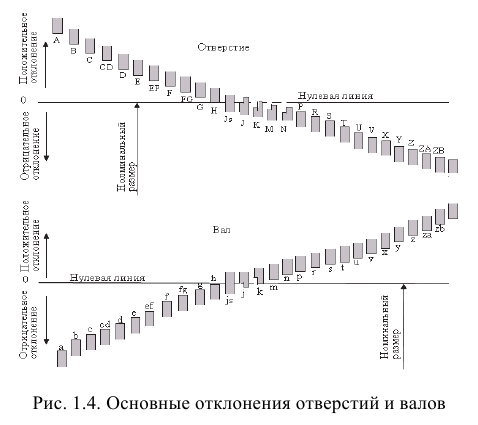
Основные отклонения от до
предназначены для образования посадок с гарантированным зазором. Причем зазор уменьшается от
до
.
Основные отклонения предназначены для образования переходных посадок. Причем основное отклонение
дает большую вероятность появления в соединении зазора и небольшую вероятность появления натяга. А основное отклонение
уже, наоборот, дает большую вероятность появления натяга и небольшую вероятность появления зазора.
Основные отклонения дают примерно равные вероятности появления в соединении зазоров или натягов. Основное отклонение
может иметь индекс
, например:
. Это означает симметричное расположение отклонении относительно номинального размера. В этом случае числовые значения верхнего и нижнего отклонений численно равны, но противоположны по знаку (см. пример 6).
Основные отклонения от до
предназначены для образования посадок с гарантированным натягом. Причем натяг увеличивается от
до
.
Основные отклонения вала и отверстия, обозначенные одноименной буквой (для данного интервала размеров), равны по величине, но противоположны по знаку, например:


Квалитеты
В каждом изделии детали разного назначения изготавливают с различной точностью. Для нормирования требуемых уровней точности установлены квалитеты (степени точности) изготовления размеров деталей. Под квалитетом понимают совокупность допусков, характеризуемых постоянной относительной точностью для всех номинальных размеров данного диапазона (например, от 1 до 500 мм).
Точность в пределах одного квалитета зависит только от номинального размера. Стандартом установлено 20 квалитетов: 01, 0, 1, 2, 3… 18. Квалитет определяет допуск на изготовление, а следовательно, и соответствующие методы и средства обработки и контроля деталей машин. Наивысшей точности соответствует квалитет 01, а низшей — 18 квалитет. Значит, чем больше номер квалитета, тем больше допуск размера.
Квалитеты 01, 0, 1 предназначены для нормирования точности размеров плоскопараллельных концевых мер длины.
Квалитеты 2, 3, 4 — для нормирования точности размеров гладких калибров-пробок и калибров-скоб, деталей измерительных приборов и инструментов.
Квалитеты 5 и 6 предназначены для нормирования точности размеров деталей высокоточных ответственных соединений (шпинделей прецизионных станков, шеек коленчатых валов и др.).
К валите ты 7, 8 являются наиболее распространенными. Они предусмотрены для размеров точных ответственных соединений в машиностроении, например: деталей двигателей внутреннего сгорания, автомобилей, самолетов, металлорежущих станков.
По квалитету 9 преимущественно выполняют размеры деталей тепловозов, паровых машин, подъемно-транспортных механизмов, полиграфических, сельскохозяйственных машин.
Квалитет 10 предназначен для размеров неответственных соединений, например для деталей тракторов, вагонов.
Квалитеты 11, 12 предназначены для нормирования точности размеров деталей, образующих неответственные соединения, в которых допустимы большие зазоры и их колебания, например размеров крышек, фланцев.
Квалитеты 13 — 18 предназначены для неответственных размеров деталей, не входящих в соединения с другими деталями, т.е. для свободных размеров, а также для межоперационных размеров.
Допуск квалитета условно обозначают прописными латинскими буквами с номером квалитета, например:
-допуск 6 квалитета.
Значения допусков для размеров до 500 мм приведены в табл. 1.1.
Система отверстия и система вала
Обозначение посадок
Сочетание основного отклонения и квалитета образует ноле допуска размера детали.
Например:
— поля допусков валов;
— поля допусков отверстий (табл. 1.2, 1.3).
Посадки на чертежах обозначают дробью: в числителе пишут поле допуска отверстия, а в знаменателе — поле допуска вала.
Посадки предусмотрены в двух системах: системе посадок основного отверстия и системе посадок основного вала.
Система посадок основного отверстия или просто система отверстия — это совокупность посадок, в которых предельные отклонения отверстии одинаковы (при одном номинальном размере и квалитете), а различные посадки достигаются изменением предельных отклонении валов.
Основное отверстие — это отверстие, которое обозначается буквой и у которого нижнее отклонение равно нулю
. При обозначении посадок в системе отверстия в числителе всегда будет стоять основное отверстие «
», а в знаменателе — основное отклонение вала, предназначенное для образования той или иной посадки.
Например:
— посадка в системе отверстия с гарантированным зазором;
— посадка в системе отверстия, переходная;
— посадка в системе отверстия с гарантированным натягом.
Система посадок основного вала или просто система вала — это совокупность посадок, в которых предельные отклонения валов одинаковы (при одном номинальном размере и одном квалитете), а различные посадки достигаются путем изменения предельных отклонении отверстии.
Основной вал — это вал, который обозначается буквой и у которого верхнее отклонение равно нулю
.
При обозначении посадок в системе вала в знаменателе (где пишется всегда поле допуска вала) будет стоять основной вал , а в числителе -основное отклонение отверстия, предназначенное для образования той или иной посадки.
Например:
— посадка в системе вала с гарантированным зазором;
— посадка в системе вала, переходная;
— посадка в системе вала с гарантированным натягом.
Стандарт разрешает любое сочетание полей допусков отверстий и валов, например: и др. Такие посадки будем называть комбинированными.
И в то же время для всех диапазонов размеров установлены рекомендуемые посадки и для размеров 1 — 500 мм из них выделены предпочтительные, например: и т.п. (см. табл. 1.2 и 1.3).
Унификация посадок позволяет обеспечить однородность конструктивных требований к соединениям и облегчить работу конструкторов по назначению посадок. Комбинируя различные варианты предпочтительных полей допусков валов и отверстий, можно значительно расширить возможности системы по созданию различных посадок без увеличения набора инструментов, калибров и другой технологической оснастки. В каждой отрасли можно сократить число полей допусков и посадок, введя ограничительный стандарт (отраслевой или стандарт предприятия).
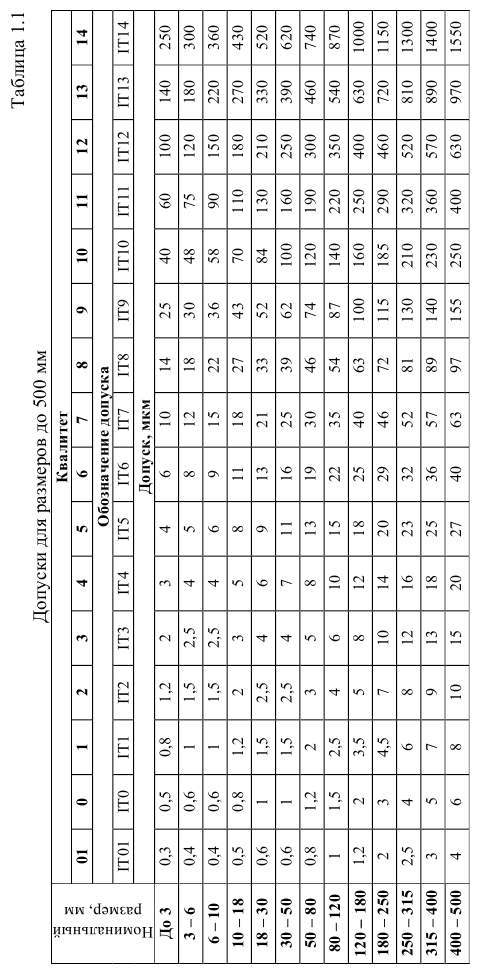
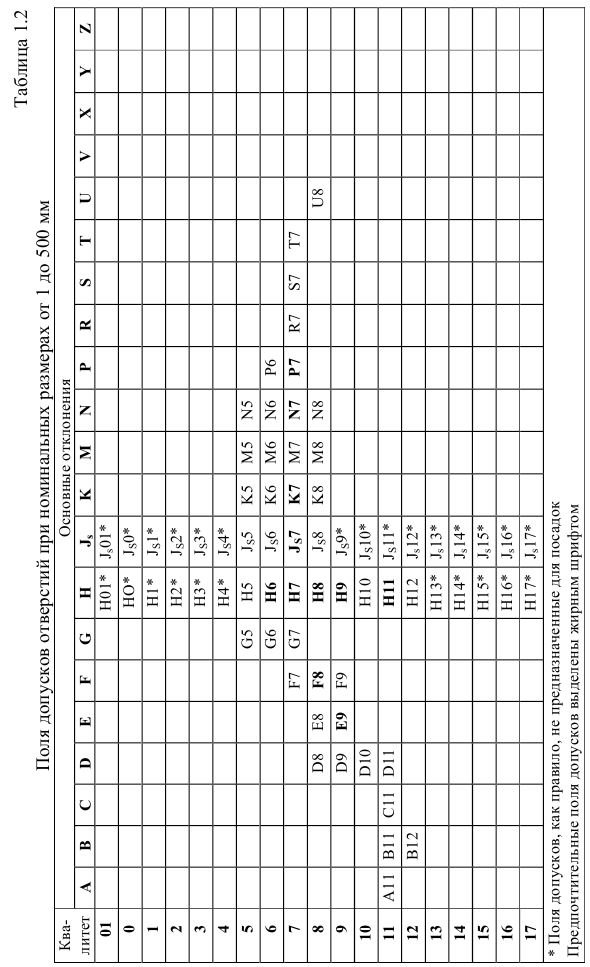
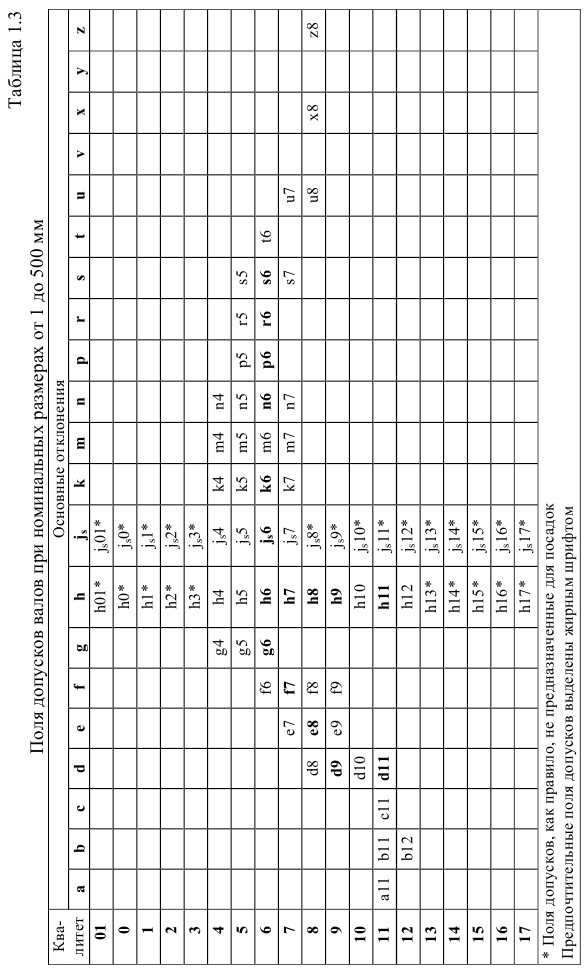
По экономическим соображениям носадки следует назначать, главным образом, в системе отверстия и реже в системе вала. Это сокращает номенклатуру режущих и измерительных инструментов, предназначенных для обработки и контроля отверстий. Точные отверстия обрабатывают дорогостоящим режущим инструментом (зенкерами, развертками, протяжками). Каждый из них применяют для обработки только одного размера с определенным полем допуска. Валы независимо от их размеров обрабатывают одним и тем же резцом или шлифовальным кругом. В системе отверстия различных по предельным размерам отверстий меньше, чем в системе вала, а следовательно, меньше номенклатура режущего инструмента, необходимого для обработки отверстий.
Однако в некоторых случаях по конструктивным соображениям приходится применять систему вала, например, когда требуется чередовать соединения нескольких отверстий одинакового номинального размера, но с различными посадками на одном валу, или гнездо в корпусе для установки подшипника выполняется по системе вала.
В рекомендуемых и предпочтительных посадках точных квалитетов для размеров от 1 до 3150 мм допуск отверстия, как правило, на один-два квалитета больше допуска вала, поскольку точное отверстие технологически получить труднее, чем точный вал, вследствие худших условий отвода теплоты, недостаточной жесткости, повышенной изнашиваемости и сложности направления режущего инструмента для обработки отверстий.
Увеличение допуска отверстия при сохранении допуска посадки повышает срок службы разверток и протяжек, так как при этом допускается больший их износ по диаметру и большее число заточек.
Стандарт в технически обоснованных случаях допускает применение посадок, отличающихся от рекомендуемых, но образованных из числа полей допусков валов и отверстий, предусмотренных этим стандартом. Однако в этих случаях посадка должна в первую очередь относиться к системе отверстия или к системе вала.
К 1980 г. ЕСДП должна была полностью заменить действующую ранее в СССР систему допусков и посадок ОСТ, но в старых документах (до 1977 — 1980 гг.) — конструкторской документации, справочниках, учебной литературе даны обозначения по ОСТ, поэтому в табл. 1.4 и 1.5 представлены сопоставления полей допусков по ОСТ и ЕСДП.
Возможно эта страница вам будет полезна:
Схематичное изображение полей допусков
Для упрощения допуски можно изображать графически в виде полей допусков. Поле допуска — пространство, ограниченное двумя линиями, соответствующими наибольшему и наименьшему размерам. Оно определяется величиной допуска и его положением относительно нулевой линии. Нулевая линия — это линия, соответствующая номинальному размеру соединения. Вверх от этой линии откладывают положительные отклонения, а вниз — отрицательные (рис. 1.5, 1.6).
Условное обозначение предельных отклонений и посадок
Предельные отклонения линейных размеров указывают на чертежах условными (буквенными) обозначениями полей допусков или числовыми значениями предельных отклонений, а также буквенными обозначениями полей допусков с одновременным указанием справа в скобках числовых значений предельных отклонений (рис. 1.7, а — в).
Посадки и предельные отклонения размеров деталей, изображенных на чертеже в собранном виде, указывают дробью: в числителе — буквенное обозначение поля допуска или числовые значения предельных отклонений отверстия либо буквенное обозначение поля допуска с указанием справа в скобках числовых значений предельных отклонений отверстия, в знаменателе — аналогичное обозначение поля допуска вала (рис. 1.7, г, г)). Иногда для обозначения посадки указывают предельные отклонения только одной из сопрягаемых деталей (рис. 1.7, е).
В условных обозначениях полей допусков нужно обязательно указывать числовые значения предельных отклонений в следующих случаях:
- для размеров, не включенных в ряд нормальных линейных размеров, например 41,5 Н7(‘°’02>);
- при назначении предельных отклонений, условные обозначения которых не предусмотрены ГОСТ 25347-82, например для пластмассовой детали (см. рис. 1.7, д).
Предельные отклонения следует назначать для всех размеров, проставленных на рабочих чертежах, включая несопрягаемые и неответственные размеры. Если предельные отклонения для размера не назначены, возможны лишние затраты (когда стремятся получить этот размер более точным, чем нужно) или увеличение массы детали.
Для линейных размеров от 1 до 10 ООО мм неуказанные предельные отклонения назначают по ГОСТ 30893.1-2002 ОНВ. Общие допуски. Предельные отклонения линейных и угловых размеров с неуказанными допусками.
Предельные отклонения линейных размеров (табл. 1.6), кроме размеров притуплённых кромок (наружных радиусов скругления и высот фасок), нормируют по классам точности общих допусков:
точный — ; средний —
; грубый —
; очень грубый —
.
На чертежах неуказанные предельные отклонения размеров задаются текстом в виде технических условий, например для среднего класса точности: «Общие допуски по ГОСТ 30893.1 — ш» или «ГОСТ 30893.1 — ш». ГОСТ 30893.1 устанавливает дополнительные варианты назначения предельных отклонений линейных размеров с неуказанными допусками (табл. 1.7). Назначение дополнительных вариантов предельных отклонений линейных размеров с неуказанными допусками при новом проектировании рекомендуется ограничить.
Обозначение соответствует обозначению
. Обозначение
соответствует обозначению
. Обозначение
соответствует обозначению
. Обозначение
соответствует обозначению
.
Обозначение неуказанных допусков по дополнительным вариантам (для класса точности — средний):
Вариант 1 — «Общие допуски по ГОСТ 30893.1: »; «Общие допуски по ГОСТ 30893.1:
».
Вариант 2 — «Общие допуски по ГОСТ 30893.1: ».
Кроме того, используется ГОСТ 30893.2-2002 ОНВ. Общие допуски. Допуски формы и расположения поверхностей, не указанные индивидуально. Введён 01.01.2004.
Общие допуски цилиндричности, точности формы продольного сечения, наклона, перекоса осей, позиционного отклонения, полного радиального и торцевого биения, формы заданного профиля и формы заданной поверхности не устанавливаются. Отклонения этих видов косвенно ограничиваются допусками на линейные и угловые размеры или другими видами допусков формы и расположения, в том числе и общими.
Общий допуск круглости для элементов с неуказанными на чертеже предельными отклонениями размеров равен допуску на диаметр, но не должен превышать общий допуск на радиальное биение.
Классы точности для неуказанных предельных отклонений формы и расположения поверхностей: (табл. 1.8).
Указание на чертежах:
«Общие допуски формы и расположения — ГОСТ 30893.2 — » или «ГОСТ 30893.2-
»;
«Общие допуски ГОСТ 30893.2 — » или «ГОСТ 30893.2 —
», где
— класс точности «средний» общих допусков размеров по ГОСТ 30893.1;
— класс точности допусков формы и расположения поверхностей.
Методы выбора посадок и области их применения
Выбор посадок производится в зависимости от назначения деталей и их поверхностей, условий работы соединения одним из трех методов.
- Метод прецедентов или аналогов. Посадка выбирается по аналогии с посадкой в надежно работающем узле. Сложность метода заключается в оценке и сопоставлении условий работы посадки в проектируемом узле и аналоге.
- Метод подобия — развитие метода прецедентов. Посадки выбираются на основании рекомендаций отраслевых технических документов и литературных источников. Недостатком метода является, как правило, отсутствие точных количественных оценок условий работы сопряжений.
- Расчетный метод является наиболее обоснованным методом выбора посадок. Посадки рассчитываются на основании полуэмпирических зависимостей. Однако формулы не всегда учитывают сложный характер физических явлений, происходящих в соединении.
В любом случае новые опытные образцы изделий перед запуском в серийное производство проходят целый ряд испытаний, по результатам которых отдельные посадки могут быть подкорректированы. Квалификация конструктора, в частности, определяется и тем, потребовалась ли корректировка посадок в разработанном им узле.
Применение посадок с зазором. Посадки — «скользящие». Наименьший зазор в посадках равен нулю. Они установлены во всем диапазоне точностей сопрягаемых размеров (с 4-го по 12-й квалитеты). В точных квалитетах они применяются как центрирующие посадки, т.е. обеспечивают высокую степень совпадения оси вала с осью сопрягаемого с ним отверстия. Допускают медленное вращение и продольное перемещение, чаще всего используемое при настройках и регулировках.
Посадка применяется в неподвижных соединениях при высоких требованиях к точности центрирования часто разбираемых деталей: сменные зубчатые колеса на валах, фрезы на оправках, центрирующие корпуса под подшипники качения, сменные кондукторные втулки и т.д. Для подвижных соединений применяется посадка шпинделя в корпусе сверлильного станка.
- — предпочтительная посадка.
Посадки имеют примерно то же назначение, что и посадка
, но характеризуются более широкими допусками, облегчающими изготовление детали.
Посадки в более грубых квалитетах (с 9-го по 12-й) предназначены для неподвижных и подвижных соединений малой точности. Применяются для посадки муфт, звездочек, шкивов на валы, для неответственных шарниров, роликов и т.п.
Посадки — «движения». Обладают минимальным по сравнению с другими посадками гарантированным зазором. Установлены только в точных квалитетах с 4-го по 7-й. Применяются для плавных, чаще всего возвратно-поступательных перемещений, допускают медленное вращение при малых нагрузках.
Посадки применяются в плунжерных и золотниковых парах, в шпинделе делительной головки и т.п.
Посадки — «ходовые». Характеризуются умеренным гарантированным зазором. Применяются для обеспечения свободного вращения в подшипниках скольжения общего назначения при легких и средних режимах работы со скоростями не более 150 рад/с и в опорах поступательного перемещения.
Посадки применяются в подшипниках скольжения коробок передач различных станков, в сопряжениях поршня с цилиндром в компрессорах, в гидравлических прессах и т.п.
Посадки — «легкоходовые». Обладают значительным гарантированным зазором, вдвое большим, чем у ходовых посадок. Применяются для свободного вращательного движения при повышенных режимах работы со скоростями более 150 рад/с, а также для компенсации погрешностей монтажа и деформаций, возникающих во время работы.
Посадки применяются для подшипников жидкостного трения турбогенераторов, больших электромашин, коренных шеек коленчатых валов.
Посадки — «широкоходовые». Характеризуются большим гарантированным зазором, позволяющим компенсировать значительные отклонения расположения сопрягаемых поверхностей и температурные деформации и обеспечить свободное перемещение деталей или их регулировку и сборку.
Посадки применяются для соединений при невысоких требованиях к точности, для подшипников трансмиссионных валов, для поршней в цилиндрах компрессоров.
Посадка применяется для крышек подшипников и распорных втулок в корпусах, для шарниров и роликов на осях.
Применение переходных посадок. Переходные посадки применяются только в точных квалитетах — с 4-го по 8-й, используются как центрирующие и предназначены для неподвижных, но разъемных соединений, так как обеспечивают легкую сборку и разборку, требуют, как правило, дополнительного крепления соединяемых деталей шпонками, штифтами, болтами и т.п.
Посадки — «плотные». Вероятность получения натяга
, и, следовательно, в сопряжении образуются преимущественно зазоры. Обеспечивают легкую собираемость.
Посадка применяется для сопряжения стаканов подшипников с корпусами, небольших шкивов и ручных маховиков с валами.
Посадки — «напряженные». Вероятность получения натяга
. Однако из-за влияния отклонений формы, особенно при большой длине соединения, зазоры в большинстве случаев не ощущаются. Обеспечивают хорошее центрирование. Сборка и разборка производится без значительных усилий, например при помощи ручных молотков.
Посадка широко применяется для сопряжения зубчатых колес, шкивов, маховиков, муфт с валами.
Посадки — «тугие». Вероятность получения натяга
. Обладают высокой степенью центрирования. Сборка и разборка осуществляется при значительных усилиях. Разбираются, как правило, только при ремонте.
Посадка применяется для сопряжения зубчатых колес, шкивов, маховиков, муфт с валами, для установки тонкостенных втулок в корпуса, кулачков на распределительном валу.
Посадки — «глухие». Вероятность получения натяга
. Обладают высокой степенью центрирования. Сборка и разборка осуществляется при значительных усилиях: применяются прессы. Разбираются, как правило, только при капитальном ремонте.
Посадка применяется для сопряжения тяжелонагруженных зубчатых колес, муфт, кривошипов с валами, для установки постоянных кондукторных втулок в корпусах кондукторов, штифтов и т.п.
Применение посадок с натягом. Они используются для передачи крутящих моментов и осевых сил без дополнительного крепления, а иногда для создания предварительно напряженного состояния у сопрягаемых деталей.
Посадки предназначены для неподвижных и неразъемных соединений. Относительная неподвижность деталей обеспечивается силами трения, возникающими на контактирующих поверхностях вследствие их упругой деформации, создаваемой натягом при сборке соединения.
Преимущество посадок — отсутствие дополнительного крепления, что упрощает конфигурацию деталей и их сборку. Посадки обеспечивают высокую нагрузочную способность сопряжения, которая резко возрастает с увеличением диаметра сопряжения. В то же время прочность и качество сопряжения зависят от материала сопрягаемых деталей, шероховатостей их поверхностей, формы, способа сборки (сборка под прессом или способ термических деформаций) и т.п.
Посадки — «легкопрессовые». Имеют минимальный гарантированный натяг. Обладают высокой степенью центрирования. Применяются, как правило, с дополнительным креплением.
Посадка применяется для сопряжения тяжелонагруженных зубчатых колес, втулок, установочных колец с валами, для установки тонкостенных втулок и колец в корпуса.
Посадки — «прессовые средние». Имеют умеренный гарантированный натяг в пределах
. Применяются как с дополнительным креплением, так и без него. При сопряжении возникают, как правило, упругие деформации.
Посадки применяются для сопряжения зубчатых и червячных колес с валами в условиях тяжелых ударных нагрузок с дополнительным креплением (для стандартных втулок подшипников скольжения предусмотрена посадка
).
Посадки — «прессовые тяжелые». Имеют большой гарантированный натяг в пределах
. Предназначены для соединений, на которые воздействуют большие, в том числе и динамические нагрузки. Применяются, как правило, без дополнительного крепления соединяемых деталей. В сопряжении возникают упругопластические деформации. Детали должны быть проверены на прочность.
Посадки наиболее распространенные из числа тяжелых посадок. Примеры применения: вагонные колеса на осях, бронзовые венцы червячных колес на стальных ступицах, пальцы эксцентриков и кривошипов с дисками.
Возможно эта страница вам будет полезна:
Пример 1
Дано:

Определить:

Решение:
Построим для заданной посадки схему полей допусков и обозначим на схеме данные по условию задачи:

по условию, так как отверстие основное; тогда


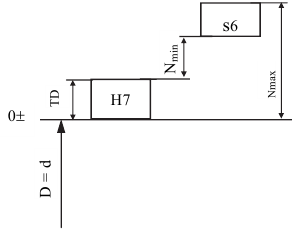
Ответ:

Пример 2
Дано:

Определить:

Решение:
Построим для заданной посадки схему полей допусков и обозначим на схеме данные по условию задачи:

по условию, так как вал основной;


по условию, так как квалитеты одинаковые, тогда

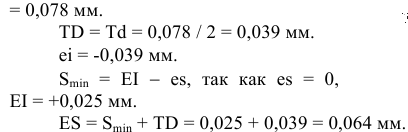
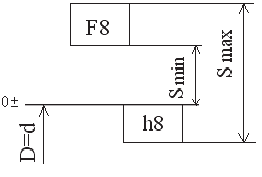
Ответ:

Нормирование точности подшипниковых соединений
Классы точности и поля допусков подшипников
Подшипник качения представляет собой сложный узел (рис. 2.1), состоящий из внутреннего 1 и наружного 3 колец, тел качения 2, которыми являются шарики, ролики или иглы. Посадочные размеры, по которым подшипник качения соединяется с валом и корпусом, следующие: внутренний диаметр внутреннего кольца и наружный диаметр
наружного кольца.
Подшипники качения являются стандартными изделиями, которые изготавливают на специализированных подшипниковых заводах. Они обладают полной внешней взаимозаменяемостью по присоединительным поверхностям колец и ограниченной внутренней взаимозаменяемостью между телами качения и кольцами. Комплекты шариков, роликов и кольца подшипников подбирают селективным методом.
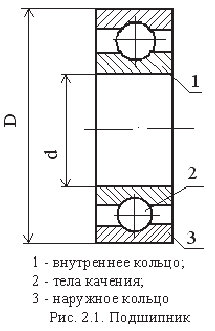
Основные присоединительные размеры подшипников качения, по которым они монтируются на валах (осях) и в корпусах машин и приборов, установлены ГОСТ 520-2002.
По ГОСТ 520-2002 на подшипники установлены классы точности, которые характеризуются значениями предельных отклонений размеров, формы, взаимного положения поверхностей. Для шариковых и роликовых радиальных и шариковых радиально-упорных подшипников установлены следующие классы в порядке повышения точности:
8, 7, нормальный, 6, 5, 4, Т, 2.
Допуски подшипников 8 и 7-го классов точности устанавливают в нормативных документах.
Для роликовых конических подшипников установлены классы точности:
8, 7, 0, нормальный, 6Х, 6, 5, 4, 2.
Для упорных и упорно-радиальных подшипников установлены классы: 8, 7, нормальный, 6, 5, 4, 2.
В большинстве узлов машин применяют подшипники качения «нормального» класса точности.
Класс точности «нормальный» соответствует классу точности 0 (нуль).
Класс точности проставляется перед обозначением подшипника (класс «О» не указывается), например: 5-208 или 208.
В общем машиностроении в основном используются подшипники О и 6 классов точности. В подшипниках качения оба кольца принимают в качестве основных деталей системы допусков, т.е. соединение «внутреннее кольцо — вал» выполняется в системе основного отверстия; соединение «наружное кольцо — корпус» выполняется в системе основного вала.
Предельные отклонения для подшипников качения назначают на средние диаметры посадочных поверхностей, которые обозначают: .
Основное отклонение для среднего диаметра отверстия подшипника обозначают . Основное отклонение для среднего наружного диаметра подшипника обозначают
.
Поля допусков ( и
) посадочных размеров подшипника (рис. 2.2) расположены одинаково в «минус» от их номинальных средних диаметров (
и
), т.е. верхнее отклонение равно нулю.
Поле допуска на наружный диаметр кольца подшипника () располагается аналогично полю допуска основного вала
и обозначается:
(в зависимости от класса точности).
Поле допуска на внутренний диаметр () располагается не в «плюс» (как для основного отверстия
), а в «минус» от нулевой линии и обозначается:
. Такое перевернутое расположение поля допуска позволяет получать с небольшим гарантированным натягом соединения подшипника с вращающимся валом, не прибегая к специальным посадкам, а используя для валов стандартные поля допусков переходных посадок
4-6 квалитетов.
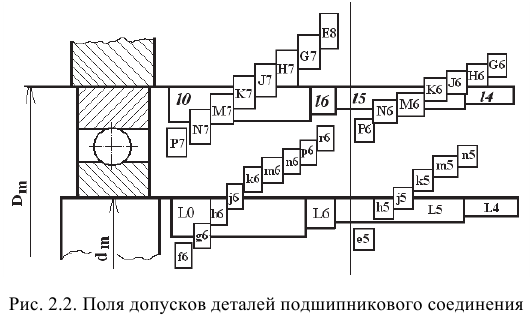
Посадки с большими натягами не применяют из-за тонкостенной конструкции колец подшипников.
Предельные отклонения диаметров даны отдельно для наружных и внутренних колец для средних диаметров ( или
), для номинальных диаметров (
или
).
Виды нагружения колец подшипника. Выбор посадок
При назначении посадок колец подшипника на вал и в отверстие корпуса следует учитывать условия работы механизма: какая деталь вращается (вал или корпус), число оборотов вращающейся детали, характер нагрузки (величину, направление и характер действующих на подшипник нагрузок), режим работы (легкий, средний, тяжелый), а также класс точности, тип и размеры подшипника, условия его установки и эксплуатации, требования к точности вращения и т.п.
С вращающейся деталью кольцо подшипника должно соединяться по посадке с натягом (для исключения обкатки и проскальзывания), а с неподвижной деталью — по посадке с небольшим зазором (для обеспечения регулировки подшипника и компенсации температурных расширений валов или корпусов).
В зависимости от условий работы различают три вида нагружения колец: местное, циркуляционное и колебательное (рис. 2.3).
При местном нагружении (рис. 2.3, а) кольцо воспринимает результирующую радиальную нагрузку одним ограниченным участком дорожки качения и передает её соответствующему участку посадочной поверхности вала или корпуса (кольцо неподвижно).
При циркуляционном погружении (рис. 2.3, 6) кольцо воспринимает действующую на подшипник результирующую радиальную нагрузку последовательно всей поверхностью дорожки качения и передает ее последовательно всей посадочной поверхности вала или корпуса (кольцо вращается).
При колебательном погружении (рис. 2.3, в) неподвижное кольцо воспринимает ограниченным участком дорожки качения равнодействующую двух радиальных нагрузок: постоянной по направлению
и вращающейся
, причем
. Равнодействующая
совершает колебательное движение.
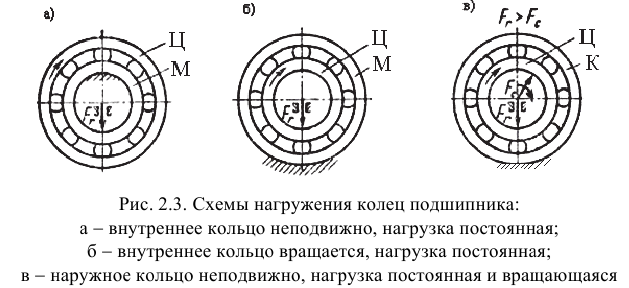
В зависимости от вида нагружения колец шариковых и роликовых подшипников в табл. 2.1 приведены рекомендуемые поля допусков посадочных мест валов и отверстий корпусов.

Примеры обозначения посадок подшипников качения на чертежах: — подшипник класса точности 0 на вал с номинальным диаметром , с симметричным расположением поля допуска вала

- то же в отверстие корпуса с номинальным диаметром 90 мм, с полем допуска

Допускается на сборочных чертежах подшипниковых узлов указывать размер, поле допуска или предельные отклонения на диаметр, сопряженный с подшипником, например для вала и для отверстия в корпусе
.
Пример решения задачи
Выбрать и рассчитать посадки на соединения подшипника с корпусом и валом в узле редуктора. Назначить отклонения формы и шероховатость посадочных поверхностей. Построить схемы полей допусков соединений. Начертить эскиз узла и деталей соединения подшипника с простановкой посадок, отклонений формы, шероховатости поверхностей.
Пример 3
Условие: подшипник шариковый, радиальный,

вращается вал, режим работы — нормальный, класс точности 0.
Решение:
1) Определяем предельные отклонения поля допуска внутреннего кольца подшипника , предельные размеры кольца при
(приложение 1):
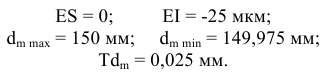
2) Определяем предельные отклонения поля допуска наружного кольца подшипника , предельные размеры кольца при
(приложение 2):
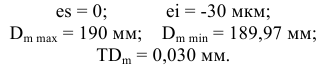
3) Определяем вид нагружения колец. Так как вращается вал, а корпус неподвижен (т.е. внутреннее кольцо вращается, а наружное неподвижно), то внутреннее кольцо нагружено циркуляционно, наружное — местно.
4) Определяем поля допусков посадочных поверхностей (приложения 3, 4):
вал — , отверстие в корпусе —
;
соединение:
внутреннее кольцо — вал ; наружное кольцо — корпус
;
5) Определяем предельные отклонения посадочных поверхностей вала и отверстия корпуса и их предельные размеры (приложения 5 — 8):
вал


отверстие


6) Определяем предельные зазоры и натяги соединений.
Внутреннее кольцо — вал — посадка в системе отверстия с натягом:
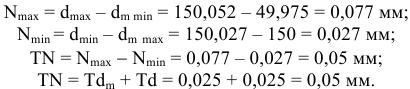
Наружное кольцо — корпус — посадка в системе вала с зазором:
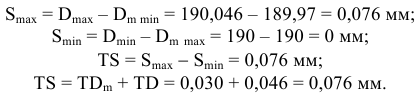
7) Определяем шероховатость посадочных поверхностей (приложение 9):
вала — ; отверстия —
; торцы заплечиков валов и отверстий корпусов —
. Отклонение от цилиндричности составляет 20 % от допуска на размер:
, поэтому допуск цилиндричности вала равен 0,005 мм;
, поэтому допуск цилиндричности отверстия равен 0,010 мм.
8) Построим схемы полей допусков деталей подшипникового соединения, обозначим зазоры и натяги (рис. 2.4).
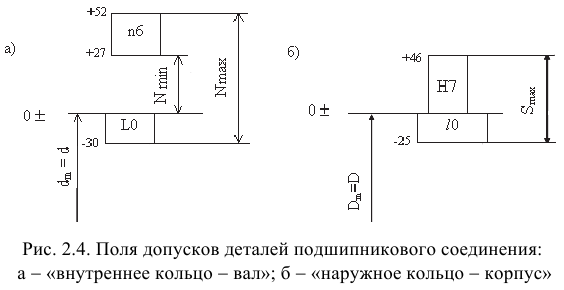
9) Выполним чертежи деталей подшипникового соединения и сборочный чертеж (рис. 2.5).
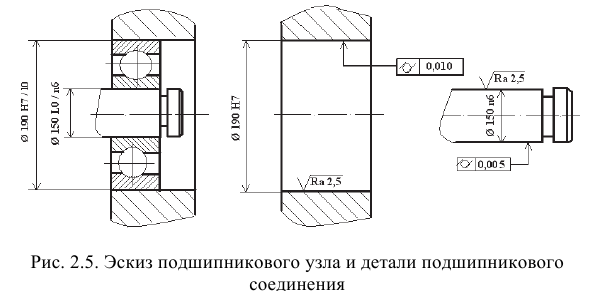
Нормирование точности шпоночных соединений
Допуски и посадки шпоночных соединений
Шпоночное соединение — это соединение с валом различных деталей (зубчатых колес, муфт, роликов, маховиков, втулок и др.) с помощью шпонки, которая входит в пазы вала и втулки.
Шпонки служат для передачи крутящего момента, предотвращения проворачивания втулки на валу, обеспечения фиксации взаимного положения деталей в узле; с их помощью достигается сравнительно легкая разборка и сборка узла при небольших требованиях к точности центрирования соединяемых деталей.
В машиностроении наиболее распространены шпоночные соединения с призматическими (рис. 3.1) и сегментными шпонками.
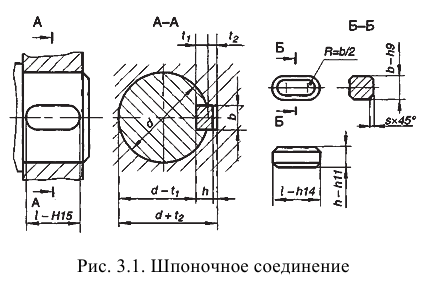
Основной посадочный размер шпоночного соединения — ширина шпонки и пазов вала и втулки, т.е. размер .
Поля допусков для обоих типов шпонок одинаковы, посадки выполняют по системе основного вала, т.е. по ширине шпонка изготавливается с полем допуска
. Это позволяет ограничить номенклатуру размеров калиброванной стали и облегчает получение требуемой точности.
Стандарт устанавливает соединение призматических шпонок с пазами валов и втулок трех видов (рис. 3.2): свободное (для направляющих шпонок), нормальное (для массового и серийного производства), плотное (для единичного производства).
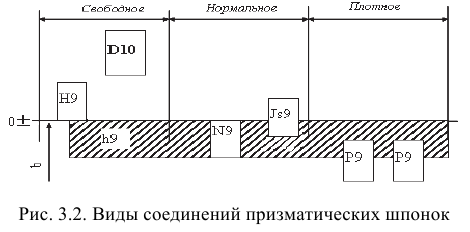
Для свободных соединений установлены поля допусков: для пазов на валу и во втулке
, что дает посадки с зазором
, для нормальных соединений соответственно
и
, что дает переходные посадки
, для плотных соединений
и
, что дает также переходные посадки
, применяемые при редкой разборке узла, реверсивном вращении.
Для сегментных шпонок применяют только нормальные и плотные соединения.
Все остальные размеры шпоночного соединения (см. рис. 3.1) являются непосадочными, на них установлены следующие поля допусков:
Предельные отклонения на глубину паза вала или на размер
и на глубину паза втулки
или на размер
зависят от ширины шпонки
и определяются по ГОСТ 23360-78.
Предельные отклонения полей допусков определяют по ГОСТ 25347-82 и ГОСТ 25348-82. Поля допусков
и
являются дополнительными и отклонения их определяют по тем же стандартам, но в таблицах дополнительных полей допусков.
Пример 4
Для соединения зубчатого колеса с валом призматической шпонкой длиной
подобрать номинальные размеры шпонки и пазов для нее, назначить посадки и предельные отклонения на все детали шпоночного нормального соединения, построить схемы полей допусков по размеру
.
Решение:
1) По таблицам ГОСТ 23360-78 находим размеры (приложение 10):
2) По таблице для призматических шпонок при нормальном соединении поля допусков по размеру принимаются (приложение 11):
для шпонки — ; для паза вала —
; для паза втулки —
.
3) По таблицам находим предельные отклонения (см. приложения 5 — 8):

Размеры вала и втулки
будут иметь отклонения (приложение 12):

4) Определяем натяги и зазоры между пазом втулки и шпонкой :


5) Определяем натяги и зазоры между пазом вала и шпонкой :
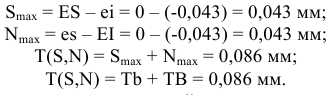
6) Строим схему расположения полей допусков деталей шпоночного соединения (рис. 3.3).
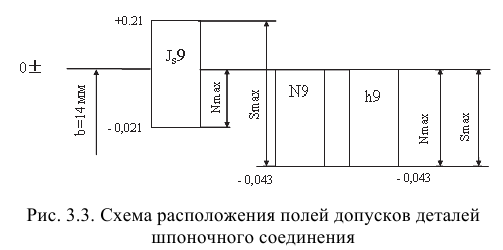
Нормирование точности шлицевых соединений
Допуски и посадки шлицевых соединений
Шлицевые соединения предназначены для передачи крутящих моментов с одновременной возможностью осевого перемещения втулки вдоль вала. Шлицевые соединения, по сравнению со шпоночными, имеют следующие преимущества: лучшее центрирование и направление посаженных на вал деталей, более равномерное распределение нагрузки по высоте зуба (шлица), меньшую концентрацию напряжений.
В зависимости от профиля зубьев различают шлицевые соединения трех видов: прямобочные, эвольвентные и треугольные (рис. 4.1).
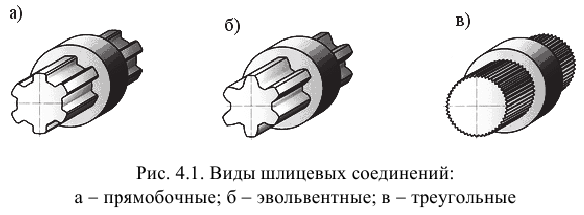
Наибольшее распространение получили шлицевые соединения с прямобочным профилем и четным числом зубьев (ГОСТ 1139-80′).
Шлицевые соединения с эвольвентным профилем зубьев по сравнению с прямобочными обладают существенными преимуществами: они имеют большую нагрузочную способность и циклическую прочность, обеспечивают лучшее центрирование и направление деталей, проще в изготовлении, так как их можно фрезеровать методом обкатки и т.п.
Шлицевые соединения с треугольным профилем нестандартизованы, их чаще применяют вместо посадок с натягом, а также при тонкостенных втулках для передачи небольших крутящих моментов.
Шлицевые соединения называют подвижными, когда детали, насаживаемые на вал, имеют возможность осевого перемещения (например, зубчатые колеса коробок передач, муфты сцепления и другие узлы), и неподвижными, если втулка не может перемещаться относительно вала.
Посадки шлицевых соединений назначают в зависимости от способа центрирования. Существует три способа центрирования: по наружному , по внутреннему
диаметрам, по боковым сторонам зубьев
, (в эвольвентных
) (рис. 4.2).
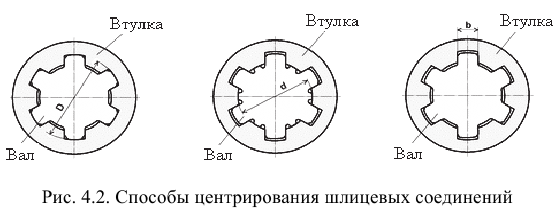
Центрирование но наружному диаметру рекомендуется, когда втулку термически не обрабатывают или когда твердость материала втулки после термической обработки допускает калибровку протяжкой
, а твердость вала допускает фрезерование до получения окончательных размеров зубьев. Такой способ прост и экономичен. Его применяют для быстроходных неподвижных соединений, а также для подвижных, воспринимающих небольшие нагрузки.
Центрирование по внутреннему диаметру целесообразно, когда втулка имеет высокую твердость
и ее нельзя обработать чистовой протяжкой. Способ обеспечивает точное центрирование и применяется обычно для быстроходных подвижных соединений.
Центрирование но боковым сторонам зубьев целесообразно при передаче знакопеременных нагрузок, больших крутящих моментов, а также при реверсивном движении в тихоходных высоконагруженных соединениях. Этот метод не обеспечивает высокой точности центрирования и поэтому редко применяется.
Посадки шлицевых прямобочных соединении (ГОСТ 1139-80*) назначают в системе отверстия по центрирующей цилиндрической поверхности и боковым поверхностям впадин втулки и зубьев вала (т.е. по и
или
и
, или только по
). Допуски и основные отклонения размеров
назначают по ГОСТ 25346-82.
Посадки назначают в зависимости от способа центрирования по ГОСТ 1139-80*. Поля допусков на нецентрирующие диаметры прямобоч-ного шлицевого соединения:
Допуски и посадки шлицевых эвольвент пых соединении установлены ГОСТ 6033-80*. Центрирование осуществляется по боковым поверхностям зубьев (), по наружному диаметру
и по внутреннему диаметру
(см. рис. 4.2). На ширину впадины втулки
и толщину зуба вала (
) устанавливают суммарный допуск:
. Допуски на нецентрирующие диаметры принимают такими, чтобы исключить контакт по этим диаметрам.
Шлицевые соединения с треугольным профилем зубьев центрируют только по боковым сторонам зубьев (см. рис. 4.2).
Примеры обозначения посадок шлицевых соединений
Соединения с прямобочным профилем
Центрирование по :

это означает: число зубьев , внутренний диаметр
, наружный диаметр
, ширина зубьев
.
Условное обозначение деталей этого соединения:
- втулки:
- вала:
Центрирование по :

это означает: число зубьев , внутренний диаметр
; наружный диаметр
; ширина зубьев
.
Условное обозначение деталей этого соединения:
- втулки:
;
- вала:
.
Центрирование по :

это означает: число зубев , внутренний диаметр
, наружный диаметр
; ширина зубьев
.
Условное обозначение деталей этого соединения:
- втулки:
- вала:
Соединения с эвольвентным профилем
Центрирование но :

это означает: номинальный диаметр соединения , модуль
, посадка по центрирующему параметру
.
Условное обозначение деталей соединения:
- втулки:
;
- вала:
.
Центрирование но :

это означает: номинальный диаметр соединения , модуль
, посадка по центрирующему диаметру
, посадка по нецентрирующим поверхностям зубьев
.
Условное обозначение деталей соединения:
- втулки:
;
- вала:
.
Центрирование но внутреннему диаметру :

это означает: номинальный диаметр соединения , модуль
, посадка по центрирующему диаметру
, посадка по нецентрирующим поверхностям зубьев
.
Условное обозначение деталей соединения:
- втулки:
;
- вала:
.
Нормирование шероховатости поверхности, точности формы и расположения поверхностей
Шероховатость поверхности
Шероховатость поверхности — это совокупность неровностей поверхности с относительно малыми шагами, выделенная с помощью базовой длины (ГОСТ 2789-73).
Условно границу между отклонениями формы поверхности различных порядков можно установить по значению отношения шага к высоте неровностей
:
при — отклонения относятся к шероховатости поверхности;
при — отклонения относятся к волнистости;
при — отклонения относятся к отклонениям формы поверхности.
Базовая длина — длина базовой линии, используемая для выделения неровностей, характеризующих шероховатость поверхности.
В качестве параметров (критериев) для оценки шероховатости в России и в большинстве стран мира принято шесть параметров:
- высотные параметры:
1) — среднее арифметическое отклонение профиля;
2) — высота неровностей профиля по десяти точкам;
3) — наибольшая высота неровностей профиля;
- шаговые параметры:
4) — средний шаг неровностей;
5) — средний шаг местных выступов профиля;
- опорный параметр:
6) — относительная опорная длина профиля.
При обозначении шероховатости на чертежах все высотные параметры задаются числовыми значениями в микрометрах (мкм) без указания единицы величины, все шаговые параметры задаются числовыми значениями в миллиметрах (мм) без указания единицы, опорный параметр задается числовыми значениями в процентах (%) и тоже без указания единицы величины. Рассмотрим каждый из этих параметров.
Среднее арифметическое отклонение профиля определяется следующим образом:

где — число выбранных точек профиля на базовой длине;
— отклонение профиля или расстояние между точкой профиля и средней линией.
Средняя линия профиля — базовая линия, имеющая форму геометрического профиля и параллельная основному направлению профиля по всей базовой длине, так что в пределах базовой длины суммы площадей, заключенных между этой линией и профилем, по обе ее стороны одинаковы, т.е.

(если — четное число).
Средняя линия профиля обозначается буквой (рис. 5.1).
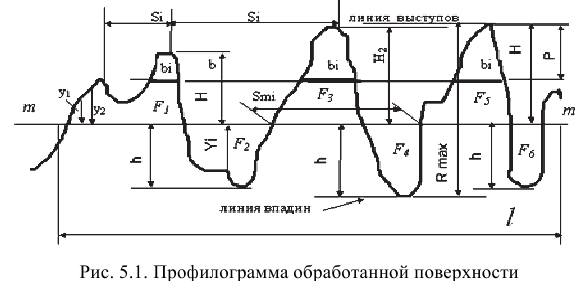
Высота неровностей профиля по десяти точкам определяется по формуле
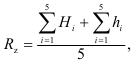
где — расстояния от пяти точек выступов до средней линии профиля;
-расстояние от пяти точек впадин до средней линии профиля (см. рис. 5.1).
Максимальная высота неровностей профиля () — это расстояние от линии выступов профиля до линии впадин в пределах базовой длины (см. рис. 5.1).
Линия выступов — линия, параллельная средней линии и проходящая через наивысшую точку профиля в пределах базовой длины.
Линия впадин профиля — линия, параллельная средней линии и проходящая через низшую точку профиля в пределах базовой длины.
Средний шаг неровностей определяется по формуле
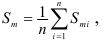
где —
-й шаг неровностей (отрезок средней линии профиля, между точками пересечения соседних одноименных сторон профиля и средней линией);
— число шагов неровностей профиля по средней линии (см. рис. 5.1). Средний шаг местных выступов определяется по формуле

где —
-й шаг местных выступов профиля, т.е. отрезок средней линии между проекциями на нее наивысших точек соседних местных выступов профиля (см. рис. 5.1).
Относительная опорная длина профиля определяется по формуле

где — относительная опорная длина профиля, %;
— значение уровня сечения;
— опорная длина профиля;
— базовая длина неровностей.
Опорная длина профиля определяется суммой длин отрезков
отсекаемых на заданном уровне
в материале профиля линией, параллельной средней линии в пределах базовой длины:

Значение уровня сечения () определяется по формуле
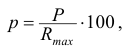
где — уровень сечения профиля (расстояние от линии выступов профиля до линии, пересекающей профиль параллельно средней линии профиля);
— максимальная высота неровностей (см. рис. 5.1).
Обозначение шероховатости на чертежах
Стандарт устанавливает три знака для обозначения шероховатости поверхности (рис. 5.2):

Первый знак применяют, когда способ обеспечения шероховатости конструктором не определен.
Второй знак применяют, когда шероховатость поверхности должна быть обеспечена удалением слоя металла.
Третий знак применяют для обозначения шероховатости поверхности, полученной литьем, ковкой, штамповкой, прокаткой и т.п., т.е. без удаления слоя металла. Последний знак применяют также в обозначении шероховатости поверхности, к обработке которой требования не установлены.
Обозначения шероховатости поверхностей на изображении изделия располагают на линиях контура, выносных линиях (по возможности ближе к размерной линии) или на полках линий-выносок. Допускается при недостатке места располагать обозначения шероховатости на размерных линиях или на их продолжениях, на рамке допуска формы, а также разрывать выносную линию (рис. 5.3).
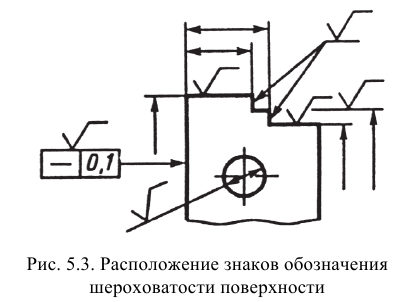
Шероховатость обозначают на чертеже для всех выполняемых по данному чертежу поверхностей изделия, независимо от методов их образования, кроме поверхностей, шероховатость которых не обусловлена требованиями конструкции.
Структура обозначения шероховатости поверхности приведена на рис. 5.4.
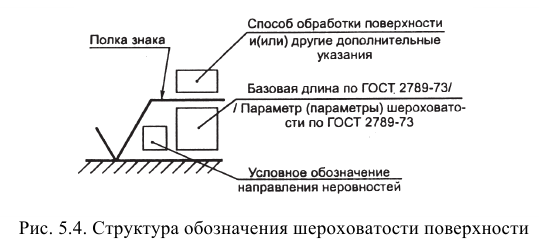
Значение параметра шероховатости указывают в обозначении шероховатости после соответствующего символа, например:


Примечание. В примере указана относительная опорная длина профиля
при значении уровня сечения профиля
.
При указании наибольшего значения параметра шероховатости в обозначении приводят параметр шероховатости без предельных отклонений, например:
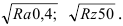
При указании наименьшего значения параметра шероховатости после обозначения параметра следует указывать «min», например:
При указании диапазона значений параметра шероховатости поверхности в обозначении шероховатости приводят пределы значений параметра, размещая их в две строки, например:

В верхней строке приводят значение параметра, соответствующее более грубой шероховатости.
При указании номинального значения параметра шероховатости поверхности в обозначении приводят это значение с предельными отклонениями, например:

При указании двух и более параметров шероховатости поверхности в обозначении шероховатости значения параметров записывают сверху вниз в следующем порядке (рис. 5.5): параметры высоты неровностей профиля, параметры шага неровностей профиля, относительная опорная длина профиля.

Из параметров шероховатости и
в обозначении может присутствовать только один и предпочтение отдают параметру
.
Над полкой знака шероховатости записывают вид обработки поверхности только в том случае, когда он является единственным для получения требуемого качества поверхности (рис. 5.6).
Под полкой знака указывают базовую длину только тогда, когда высотные параметры и
определяются в пределах базовой длины, отличающейся от стандартной.
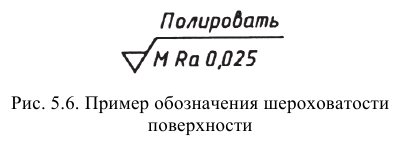
Допускается применять упрощенное обозначение шероховатости поверхностей с разъяснением его в технических требованиях чертежа по примеру, указанному на рис. 5.7. В упрощенном обозначении используют знак и строчные буквы русского алфавита в алфавитном порядке, без повторений и, как правило, без пропусков.
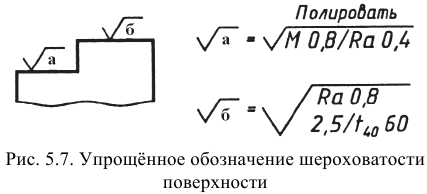
Условные обозначения направления неровностей должны соответствовать приведенным в табл. 5.1. Условные обозначения направления неровностей приводят на чертеже при необходимости (см. рис. 5.6).
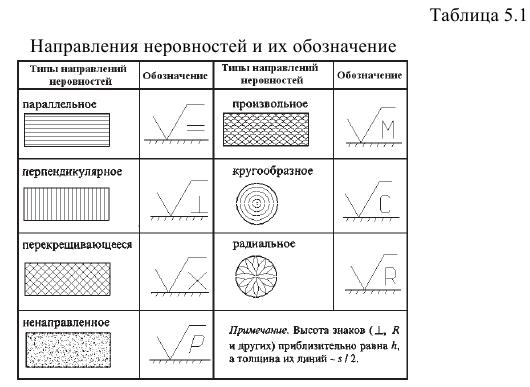
При обозначении изделия с разрывом обозначение шероховатости наносят только на одной части изображения, по возможности ближе к месту указания размеров (рис. 5.8). При указании одинаковой шероховатости для всех поверхностей изделия обозначение шероховатости помещают в правом верхнем углу чертежа и на изображение не наносят (рис. 5.9).
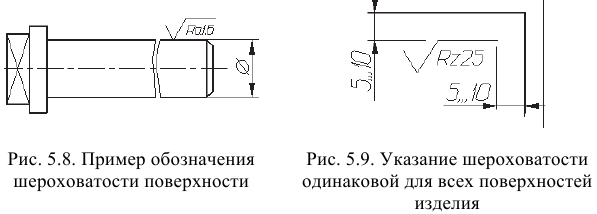
Если шероховатость поверхности детали должна быть разной, то в правом верхнем углу чертежа наносят обозначение преобладающей по числу поверхностей шероховатости и знак в скобках, который означает, что все остальные поверхности детали, кроме обозначенных на изображении, должны иметь шероховатость, указанную перед скобкой (рис. 5.10, 5.11).
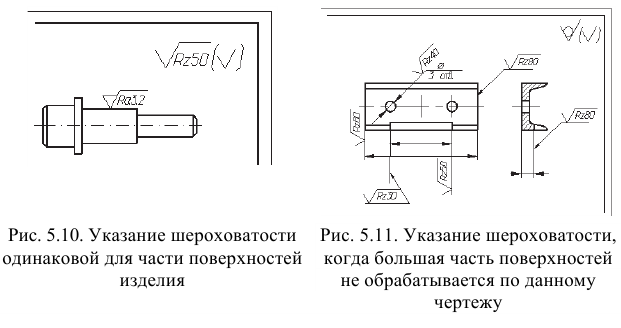
Если шероховатость одной и той же поверхности различна на отдельных участках, то эти участки разграничивают сплошной тонкой линией с нанесением соответствующих размеров и обозначения шероховатости (рис. 5.12). Через заштрихованную зону линию границы между участками не проводят (рис. 5.13).
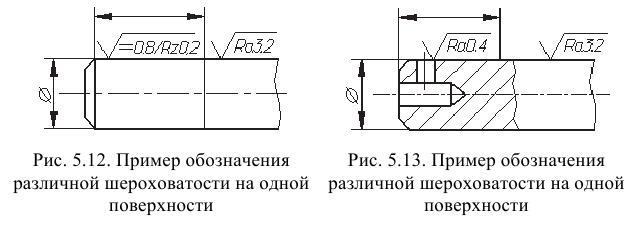
Обозначение шероховатости рабочих поверхностей зубьев зубчатых колес и эвольвентных шлиц условно наносят на линии делительной поверхности (рис. 5.14).
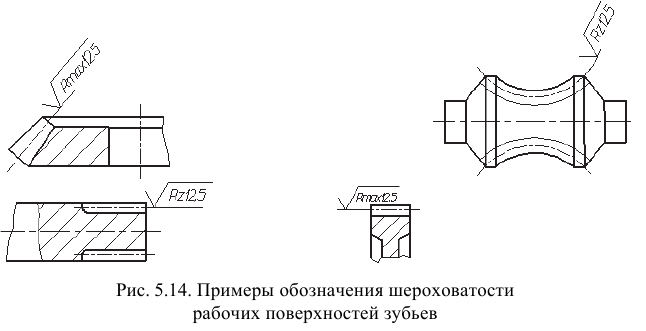
Обозначение шероховатости поверхности профиля резьбы наносят по общим правилам при изображении профиля или условно на выносной линии для указания размера резьбы (рис. 5.15), на размерной линии или на ее продолжении (рис. 5.16).
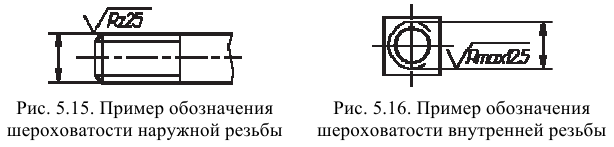
Если шероховатость контура должна быть одинаковой, то обозначение наносится один раз со знаком окружности о (рис. 5.17). Диаметр знака равен 4…5 мм. В обозначении одинаковой шероховатости поверхностей, плавно переходящих одна в другую, знак о не приводят (рис. 5.18).
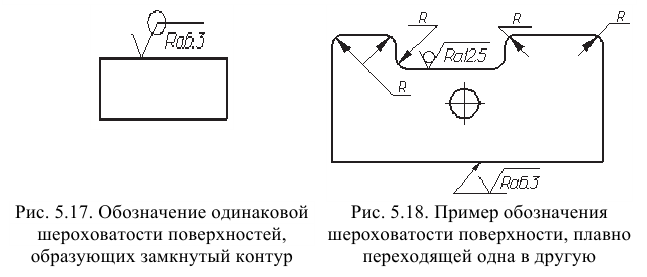
Обозначение шероховатости поверхностей повторяющихся элементов изделия (отверстий, пазов, зубьев и т.п.), количество которых указано на чертеже, а также обозначение шероховатости одной и той же поверхности наносят один раз, независимо от числа изображений.
Обозначение шероховатости симметрично расположенных элементов симметричных изделий наносят один раз.
Допускаемые значения и
в зависимости от допуска размера и формы установлены по четырем уровням относительной геометрической точности, определяемых соотношением допусков формы и размера соответственно:

Существуют три основных метода измерения шероховатости поверхности:
1) определение параметров шероховатости сравнением с образцами;
2) бесконтактный метод при использовании приборов светового сечения, двойного микроскопа, микроинтерферометра и др.;
3) контактный метод с использованием щуповых приборов различных моделей, например профилографа-профилометра и др.
В конструкторской документации, справочниках, учебной литературе, выпущенной до 1980 г. и разработанной до введения ГОСТ 2789-73 и ГОСТ 2.309-73, требования к шероховатости указывались по классам и разрядам шероховатости. В табл. 5.3 приведены ранее применявшиеся условные обозначения классов и разрядов шероховатости и соответствующие им числовые значения параметров и
.
Отклонения и допуски формы поверхностей
Под отклонением формы поверхности понимают отклонение формы реальной поверхности от формы номинальной поверхности.
Номинальная поверхность — идеальная поверхность, номинальная форма которой задана чертежом или другой технической документацией. Реальные поверхности у детали получаются после изготовления. В основу нормирования и количественной оценки отклонений формы и расположения положен принцип прилегающих прямых, поверхностей и профилей.
Прилегающая прямая — прямая, соприкасающаяся с реальным профилем и расположенная вне материала детали так, чтобы отклонения от нее до наиболее удаленной точки реального профиля было минимальным (рис. 5.19, а).
Прилегающая окружность — это окружность минимального диаметра, описанная вокруг реального профиля наружной поверхности вращения или максимального диаметра, вписанного в реальный профиль внутренней поверхности вращения (рис. 5.19, б, в). Различают также прилегающую плоскость, прилегающий цилиндр и т.п.
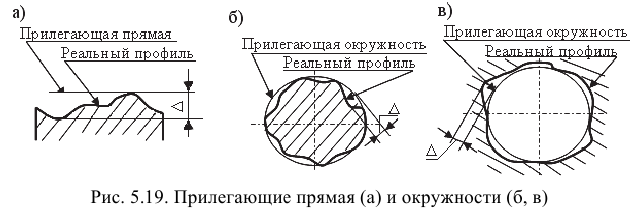
Приняты следующие буквенные обозначения:
— отклонение формы или расположения поверхностей;
— допуск формы или допуск расположения;
— длина нормируемого участка.
Отклонения формы плоских поверхностей
Комплексный показатель, характеризующий точность формы плоских поверхностей, — это отклонение от плоскостности (рис. 5.20). Отклонение от плоскостности определяют как наибольшее расстояние от точек реальной поверхности до прилегающей плоскости в пределах нормируемого участка (см. рис. 5.19, а).
Частными видами отклонений от плоскостности являются выпуклость и вогнутость. Условных обозначений эти показатели не имеют, поэтому на чертеже обозначают поверхность (русскими прописными буквами), а в технических требованиях делают соответствующую запись (рис. 5.21).

Показателем, характеризующим также точность формы плоских поверхностей, является отклонение от прямолинейности (-). Отклонение от прямолинейности плоскости определяют как наибольшее расстояние () от точек реального профиля до прилегающей прямой (рис. 5.22, в). Рассмотрим несколько возможных вариантов простановки отклонения от прямолинейности.
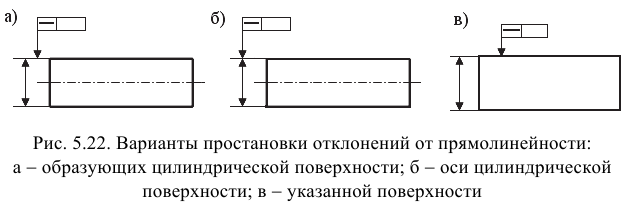
Отклонения формы цилиндрических поверхностей
Комплексным показателем точности формы цилиндрической поверхности является отклонение от цилиндричности (). Отклонение от цилиндричности — наибольшее расстояние (
) от точек реальной поверхности до прилегающего цилиндра в пределах нормируемого участка (
). Это отклонение определяет точность цилиндрической поверхности в двух сечениях — продольном и поперечном. Однако чаще точность формы цилиндрической поверхности рассматривают отдельно в каждом из этих сечений.
Рассмотрим показатели точности формы цилиндрической поверхности в продольном сечении:
- комплексный показатель — отклонение профиля продольного сечения (
);
- частные виды отклонений, характеризующих точность формы в продольном сечении — конусообразность, бочкообразность, седлообразность.
Отклонение профиля продольного сечения — наибольшее расстояние () от точек образующих (образующих цилиндрической поверхности) реальной поверхности, лежащих в плоскости, проходящей через ее ось, до соответствующей стороны прилегающего профиля в пределах нормируемого участка (
) (рис. 5.23).
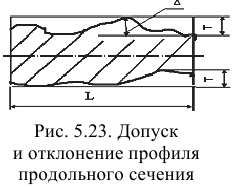
Поле допуска () отклонения профиля продольного сечения показано на рис. 5.23. Отклонение профиля продольного сечения характеризует отклонения от прямолинейности и параллельности образующих.
Конусообразность — отклонение продольного сечения, при котором образующие прямолинейны, но не параллельны (рис. 5.24, а).
Бочкообразность — отклонение профиля продольного сечения, при котором образующие непрямолинейны, и диаметры увеличиваются от краев к середине сечения (рис. 5.24, 6).
Седлообразностъ — отклонение профиля продольного сечения, при котором образующие непрямолинейны, и диаметры уменьшаются от краев к середине сечения (рис. 5.24, в).
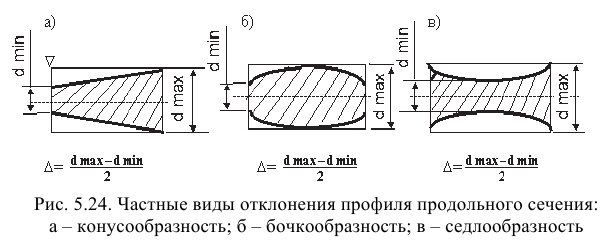
Бочкообразность чаще всего возникает при обтачивании тонких длинных валов в центрах без люнетов (в средней части под влиянием сил резания возникают большие упругие прогибы, чем по краям). Толстые короткие валы чаще получаются седлообразными из-за большого смещения вала по краям (составляющие силы резания распределяются между обоими центрами более равномерно). Бочкообразность и седлообразность могут возникнуть также вследствие погрешности направляющих станин станков и других причин. Причиной конусообразности являются износ резца, несовпадение геометрических осей шпинделя и пиноли задней бабки станка (смещение центров), отклонение от параллельности оси центров направляющим станины.
Рассмотрим показатели точности формы цилиндрической поверхности в поперечном сечении. Комплексный показатель — отклонение от круглости () — наибольшее расстояние (
) от точек реального профиля до прилегающей окружности (рис. 5.25).
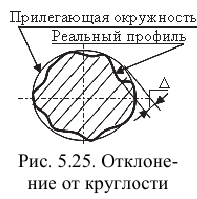
Допуск круглости () — наибольшее допускаемое значение отклонения от круглости.
Частными видами отклонений от круглости являются овальность и огранка.
Овальность — отклонение от круглости, при котором реальный профиль представляет собой овалообразную фигуру, наибольший и наименьший диаметры которой находятся во взаимно перпендикулярных направлениях (рис. 5.26, а).
Огранка — отклонение от круглости, при котором реальный профиль представляет собой многогранную фигуру. Огранка может быть с четным и нечетным числом граней и характеризуется равенством размера (рис. 5.26, 6).
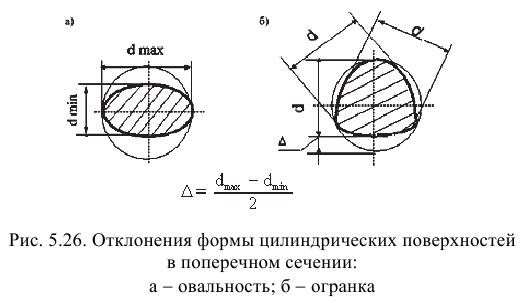
Овальность детали возникает, например, вследствие биения шпинделя токарного или шлифовального станка, дисбаланса детали и других причин. Появление огранки вызвано изменением положения мгновенного центра вращения детали, например при бесцентровом шлифовании.
Примеры обозначений отклонений формы цилиндрических поверхностей представлены на рис. 5.27 и 5.28.
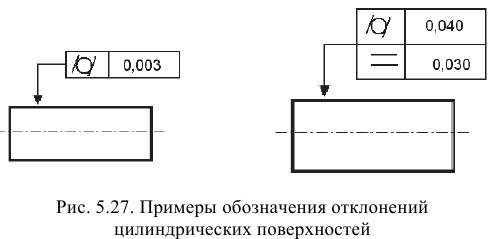
Отклонения расположения поверхностей
Отклонением расположения поверхности или профиля называют отклонение реального расположения поверхности (профиля) от его номинального расположения.
Рассмотрим примеры отклонений расположения поверхностей.
Отклонение от параллельности плоскостей (осей, оси и плоскости) — разность () наибольшего и наименьшего расстояний между прилегающими плоскостями в пределах нормируемого участка (рис. 5.29 и 5.30).
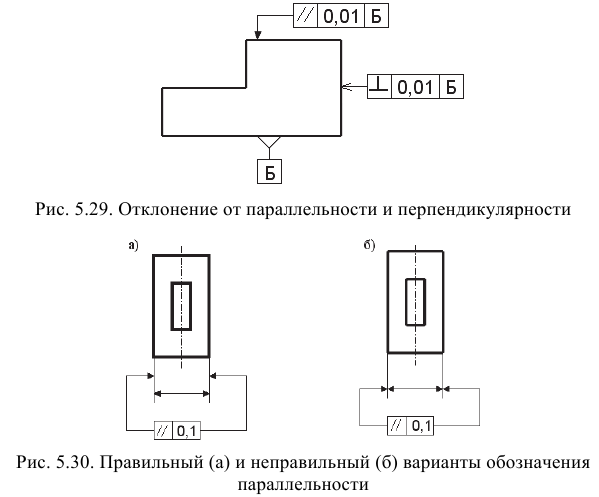
Отклонение от перпендикулярности плоскостей (осей, оси и плоскости) — отклонение угла между плоскостями от прямого угла (90°), выраженное в линейных единицах на длине нормируемого участка (см. рис. 5.29).
Отклонение от соосности относительно общей оси — это наибольшее расстояние () между осью рассматриваемой поверхности вращения и общей осью двух или нескольких поверхностей вращения на длине нормируемого участка. Отклонение от соосности всегда относится к осям (рис. 5.31).
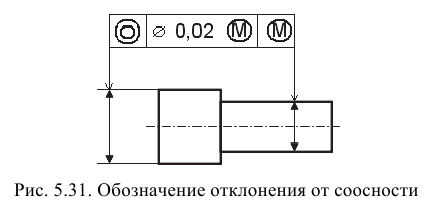
Допуск соосности в диаметральном выражении равен удвоенному наибольшему допускаемому значению отклонения от соосности, а в радиусном выражении — наибольшему допускаемому значению этого отклонения. Поле допуска соосности — область в пространстве, ограниченная цилиндром, диаметр которого равен допуску соосности в диаметральном выражении или удвоенному допуску соосности в радиусном выражении
, а ось совпадает с базовой осью. Двоякая количественная оценка соосности (в диаметральном и радиусном выражении) принята по рекомендации ИСО также для симметричности и пересечения осей.
Ранее эти отклонения определяли только в радиусной мере.
Отклонение от симметричности относительно базовой плоскости -наибольшее расстояние () между плоскостью симметрии рассматриваемой поверхности и базовой плоскостью симметрии в пределах нормируемого участка (рис. 5.32).
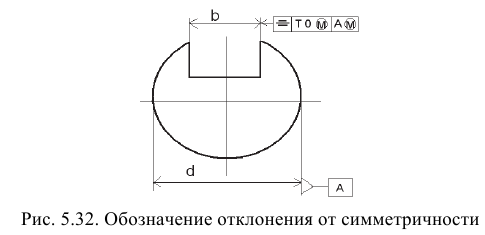
Отклонение от пересечения осей, которые номинально должны пересекаться, определяют как наименьшее расстояние между рассматриваемой и базовой осями (рис. 5.33).
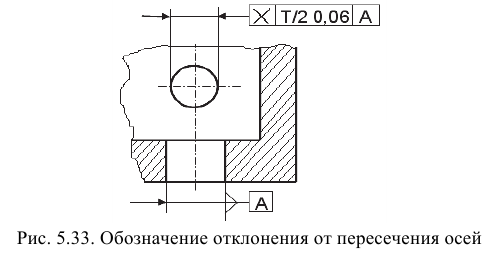
Позиционное отклонение — наибольшее расстояние () реального расположения элемента (его центра, оси или плоскости симметрии) от его номинального расположения в пределах нормируемого участка. Позиционное отклонение и позиционный допуск были введены вместо термина смещение оси (или плоскости симметрии) от номинального расположения (рис. 5.34).
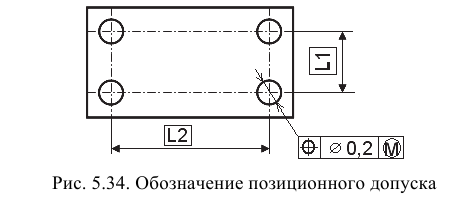
Отклонение наклона плоскости (оси, прямой) относительно плоскости (оси, прямой) — отклонение угла между плоскостью и базовой плоскостью от номинального угла, выраженное в линейных единицах на длине нормируемого участка (рис. 5.35).
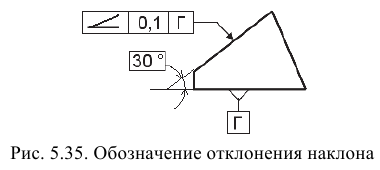
Суммарные отклонения и допуски формы и расположения поверхностей
Радиальное биение поверхности вращения относительно базовой оси является результатом совместного проявления отклонения от круглости профиля рассматриваемого сечения и отклонения его центра относительно базовой оси.
Если определяют разность наибольшего и наименьшего расстояний от всех точек реальной поверхности в пределах нормированного участка до базовой оси, то находят полное радиальное биение:

Оно является результатом совместного проявления отклонения от цилиндричности поверхности и отклонения от ее соосности относительно базовой оси (рис. 5.36).
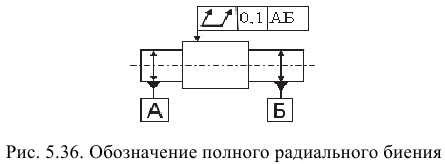
Торцовое биение (полное) — разность () наибольшего и наименьшего расстояний от точек всей торцовой поверхности до плоскости, перпендикулярной базовой оси. Оно является результатом совместного проявления отклонения от плоскостности рассматриваемой поверхности и отклонения от перпендикулярности ее относительно базовой оси (рис. 5.37).
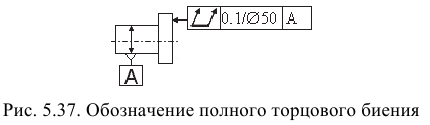
Отклонение формы заданного профиля — наибольшее отклонение точек реального профиля, определяемое по нормали к нормируемому профилю в пределах нормируемого участка
.
Отклонение формы заданной поверхности — наибольшее отклонение точек реальной поверхности от номинальной поверхности, определяемое по нормали к номинальной поверхности в пределах нормируемых участков
(рис. 5.38).
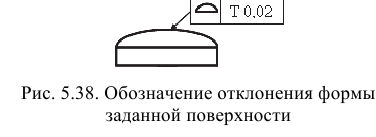
Зависимый и независимый допуски расположения (формы)
Допуски расположения или формы, устанавливаемые для валов или отверстий, могут быть зависимыми и независимыми.
Зависимым называют переменный допуск расположения или формы, минимальное значение которого указывается в чертеже или в технических требованиях и которое допускается превышать на величину, соответствующую отклонению действительного размера поверхности детали от проходного предела (наибольшего предельного размера вала или наименьшего предельного размера отверстия) (рис. 5.39).
Допуск расположения или формы может быть зависимым как от точности размеров рассматриваемых поверхностей, так и от точности размеров базовой поверхности.
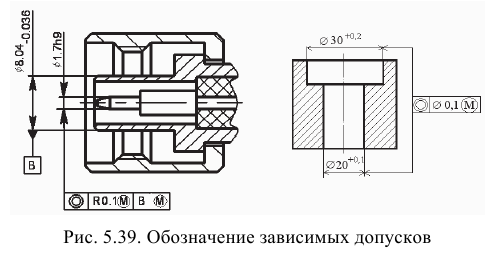
Независимым называют допуск расположения или формы поверхностей, числовое значение которого постоянно и не зависит от действительных размеров рассматриваемых поверхностей.
Нормирование точности формы и расположения поверхностей
Согласно ГОСТ 24643-81, для каждого вида допуска формы и расположения поверхностей установлено 16 степеней точности. Числовые значения допусков увеличиваются от одной степени к другой. Существует связь между точностью размеров деталей (квалнтетом) и точностью формы или расположения поверхностей (степенью точности).
Допуск формы поверхности не может быть больше допуска па размер этой поверхности. Таким образом, для нормирования точности формы используется часть от допуска на размер. Стандарт устанавливает следующие уровни относительной геометрической точности формы:
— нормальная относительная геометрическая точность, допуски формы или расположения составляют примерно 60 % допуска размера;
— повышенная относительная геометрическая точность, допуски формы или расположения составляют примерно 40 % допуска размера;
— высокая относительная геометрическая точность, допуски формы или расположения составляют примерно 25 % допуска размера.
Допуски формы цилиндрических поверхностей, соответствующие уровням составляют примерно 30, 20 и 12 % допуска размера, так как допуск формы ограничивает отклонение радиуса, а допуск размера -отклонение диаметра поверхности.
Допуски формы и расположения можно ограничивать полем допуска размера (см. раздел 1.8).
На чертежах допуски формы и расположения поверхностей указывают только, когда они должны быть меньше допусков размера или неуказанных допусков по ГОСТ 25670-83.
Назначение степени точности формы в зависимости от квалитета размера можно осуществлять, пользуясь табл. 5.4.
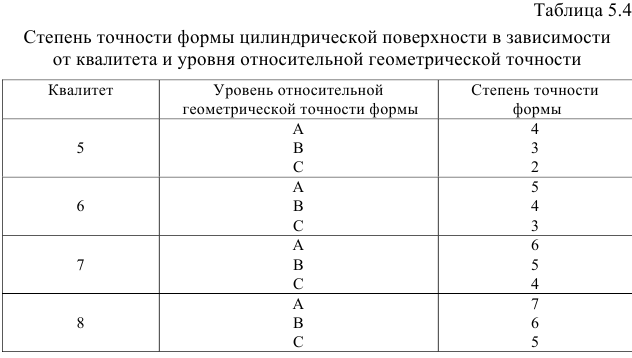
Степень точности формы и расположения для уровня всегда на единицу меньше номера квалитета, поэтому легко дальше продолжить табл. 5.4 для любых квалитетов.
Рассмотрим пример нормирования отклонения от цилиндричности (рис. 5.40). Вал обрабатывается под подшипник качения, поэтому диаметр и поле допуска вала выбраны верно. Как получено отклонение от цилиндричности?
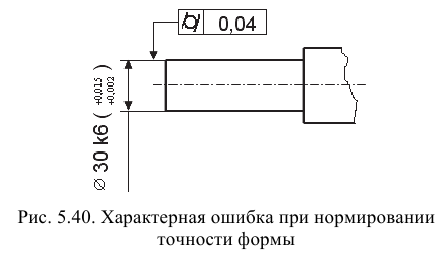
По правилам нормирования для поверхности под подшипник необходимо выбрать повышенные требования к точности формы. То есть от допуска на размер нужно взять 20 % для определения допуска формы

В соответствии с табл. 5.4 определим степень точности формы вала. Для 6 квалитета и повышенного уровня точности формы получаем 4 степень точности формы. По таблицам отклонений цилиндричности для диаметра 30 и степени точности формы 4 допуск цилиндричности равен 3 мкм или 0,003 мм, что подтверждает полученное расчётом значение.
Таким образом, на чертеже вала должно стоять отклонение от цилиндричности, равное 0,003 мм.
Обозначение на чертежах допусков формы и расположения поверхностей деталей
Вид допуска формы и расположения принято обозначать на чертеже знаками (графическими символами), приведенными в табл. 5.5. Знак и числовое значение допуска вписывают в рамку (размеры рамки произвольные), указывая на первом месте знак, на втором — числовое значение допуска в миллиметрах (без указания единицы) и на третьем (при необходимости) — буквенное обозначение базы или поверхности, с которой связан допуск расположения (см. примеры обозначения). Рамку соединяют с элементом, к которому относится допуск, сплошной линией, заканчивающейся стрелкой. Если допуск относится к оси или плоскости симметрии, соединительная линия должна быть продолжением размерной; если допуск относится к общей оси (плоскости симметрии), соединительную линию проводят к общей оси.
Перед числовым значением допуска следует указывать:
1) символ , если поле допуска задано его диаметром (см. рис. 5.39);
2) символ , если поле допуска задано радиусом (см. рис. 5.39);
3) символ , если допуски симметричности, пересечения осей, формы заданной поверхности, а также позиционные заданы в диаметральном выражении (см. рис. 5.38);
4) символ для тех же видов допусков, если они заданы в радиусном выражении (см. рис. 5.33);
5) слово «сфера» и символы и
, если поле допуска сферическое (задача 5 из раздела 5.8)
Если допуск относится к участку поверхности заданной длины (площади), то ее значение указывают рядом с допуском, отделяя от него наклонной линией (задача 7 из раздела 5.8). Если необходимо назначить допуск на всей длине поверхности и на заданной длине, то допуск на заданной длине указывают под допуском на всей длине (задача 8 из раздела 5.8).
Суммарные допуски формы и расположения поверхности, для которых не установлены отдельные графические знаки, обозначают знаками составных допусков: сначала знак допуска расположения, затем знак допуска формы (задача 9 из раздела 5.8).
Базу обозначают зачерненным треугольником, который соединяют соединительной линией с рамкой допуска. Чаще базу обозначают буквой и соединяют ее с треугольником.
Если базой является ось или плоскость симметрии, треугольник располагают в конце размерной линии соответствующего размера поверхности. В случае недостатка места стрелку размерной линии допускается заменять треугольником.
Обозначение зависимых допусков:
Если допуск расположения или формы не указан как зависимый, то его считают независимым.
Зависимые допуски расположения и формы обозначают условным знаком (буквой в кружке), который помещают:
1) после числового значения допуска, если зависимый допуск связан с действительными размерами рассматриваемых поверхностей (задача 6 из раздела 5.8);
2) после буквенного обозначения базы или без буквенного обозначения базы в третьей части рамки, если этот допуск связан с действительными размерами базовой поверхности (см. рис. 5.34);
3) после числового значения допуска и буквенного обозначения базы или без буквенного обозначения базы, если зависимый допуск связан с действительными размерами рассматриваемого и базового элемента (см. рис. 5.39).
Возможно эта страница вам будет полезна:
Нормирование точности резьбовых соединений
Виды и основные параметры резьб
В зависимости от эксплуатационного назначения резьбы делятся на общие и специальные.
К резьбам общего назначения относятся: крепежные (метрическая, дюймовая), кинематические (трапецеидальная, прямоугольная, упорная), трубные (цилиндрическая, коническая), арматурные.
Резьбы специального назначения (круглая, окулярная и т.д.) применяются только в определенных изделиях.
Резьбы подразделяются:
- по профилю витков на треугольные, трапецеидальные, упорные (пилообразные), прямоугольные, круглые;
- по числу заходов на однозаходные, многозаходные;
- в зависимости от направления вращения контура осевого сечения на правые и левые;
- по принятой единице измерения линейных размеров на метрические и дюймовые.
Из всего многообразия резьб нами будет рассмотрена крепежная цилиндрическая метрическая резьба. Номинальные размеры параметров резьбы общие как для наружной (болта), так и для внутренней (гайки) резьб. Основные параметры цилиндрической резьбы (ГОСТ 11708-82) следующие (рис. 6.1):

- наружный диаметр
;
- средний диаметр
;
- внутренний диаметр
;
- шаг резьбы
;
- угол профиля резьбы
;
- высота исходного треугольника
;
- угол подъема
;
- длина свинчивания
.
Допуски и посадки метрических резьб
В зависимости от эксплуатационных требований к степени подвижности резьбовых соединений стандартами установлены поля допусков, образующие посадки трех групп: с зазором (ГОСТ 16093-81), переходные (ГОСТ 24834-81) и с натягом (ГОСТ 4608-81).
Наружная резьба (болт) нормируется по среднему и наружному диаметрам ( и
), внутренняя резьба (гайка) — по среднему и внутреннему диаметрам (
и
). Допуски этих диаметров резьбы устанавливаются по степеням точности, которые обозначаются цифрами. Степени точности диаметров резьбы приведены в табл. 6.1.
Допуски диаметров и
не устанавливаются.
Положение поля допуска диаметра резьбы определяется основным отклонением (верхним для наружной резьбы и нижним
для внутренней) и обозначается буквой латинского алфавита: строчной для наружной резьбы и прописной для внутренней. Основные отклонения диаметров резьбы для посадок с зазором приведены в табл. 6.2.
Длины свинчивания резьбы подразделяются на три группы: короткие , нормальные
и длинные
.
Поле допуска диаметра резьбы образуется сочетанием степени точности и основного отклонения. Поле допуска резьбы образуется сочетанием поля допуска среднего диаметра (d2, D2) с полем допуска диаметра выступов (диаметров d и D|).
Обозначение поля допуска диаметра резьбы состоит из цифры, обозначающей степень точности, и буквы, обозначающей основное отклонение. Например:

Обозначение поля допуска резьбы состоит из обозначения поля допуска среднего диаметра, помещенного на первом месте, и обозначения поля допуска диаметра выступов. Например:
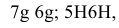
где — поле допуска диаметра
;
— поле допуска диаметра
;
— поле допуска диаметра
;
— поле допуска диаметра
.
Если обозначение поля допуска диаметра выступов совпадает с обозначением поля допуска среднего диаметра, то оно в обозначении поля допуска резьбы не повторяется. Например:

где — поле допуска диаметров
и
;
— поле допуска диаметров
и
.
В условном обозначении резьбы обозначение поля допуска должно следовать за обозначением размера резьбы. Примеры обозначения резьбы
С крупным шагом:

С мелким шагом:

Левой резьбы:

В соответствии со сложившейся во многих странах практикой поля допусков сгруппированы в три класса точности: точный, средний и грубый. Понятие о классах точности условное (на чертежах и калибрах указывают не классы, а поля допусков), его используют для сравнительной оценки точности резьбы.
Длина свинчивания () в условном обозначении резьбы не указывается. Длина свинчивания, к которой относится допуск резьбы, должна быть указана в миллиметрах в обозначении резьбы в следующих случаях:
1) если она относится к группе ;
2) если она относится к группе , но меньше, чем вся длина резьбы. Пример обозначения резьбы с длиной свинчивания, отличающейся от нормальной:
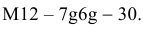
Посадка в резьбовом соединении обозначается дробью, в числителе которой указывают обозначение поля допуска внутренней резьбы, а в знаменателе — обозначение поля допуска наружной резьбы. Например:
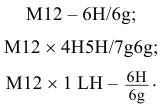
Переходные посадки в резьбовых соединениях применяются, если необходимо обеспечить их неподвижность в процессе работы без создания большого натяга и предназначаются для наружных резьб (резьба на ввинчиваемом конце шпильки).
Для переходных посадок предусмотрены поля допусков:
Посадки с натягом в резьбовых соединениях применяются, когда необходимо устранить возможность самоотвинчивания без применения дополнительных элементов заклинивания (только за счет натяга), предназначены эти посадки для нагруженных резьб.
Для посадки с натягом предусмотрены поля допусков:
Незначительное увеличение натяга в резьбовом соединении может вызвать быстрый рост напряжений и появление пластических деформаций, поэтому возникает необходимость проведения селективной сборки с сортировкой резьбовых деталей на две или три размерные группы (рис. 6.2).
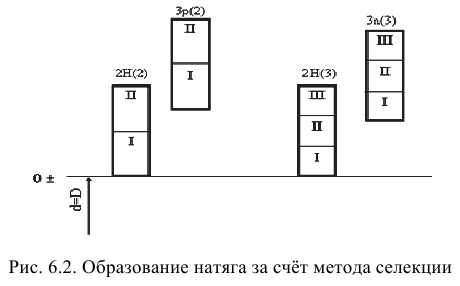
При обозначении посадок с натягом резьбовых соединений в скобках указывается число сортировочных групп по среднему диаметру. Например:

где в скобках указано число сортировочных групп по среднему диаметру.
Пример 5
Расшифровать обозначение посадки резьбового соединения.
Условие: Дано резьбовое соединение .
Решение:
Резьба метрическая, наружный диаметр резьбы — 24 мм. Поле допуска резьбы гайки , т.е. поле допуска среднего диаметра
и поле допуска внутреннего диаметра
. Поле допуска резьбы болта
, т.е. поле допуска среднего диаметра
, поле допуска наружного диаметра
.
Возможно эта страница вам будет полезна:
Нормирование точности цилиндрических зубчатых передач
Погрешности изготовления и сборки зубчатых передач вызывают динамические нагрузки, шум, вибрации, нагрев, концентрацию напряжений на отдельных участках зубьев. При назначении допусков на зубчатые колеса и точность монтажа для достижения качественной работы передачи преследуются следующие цели:
- обеспечить кинематическую точность, т.е. согласованность углов поворота ведущего и ведомого колес передачи;
- обеспечить плавность работы, т.е. ограничить циклические погрешности, многократно повторяющиеся за один оборот колеса;
- обеспечить полноту контакта зубьев, т.е. такое прилегание зубьев по длине и высоте, при котором нагрузка от одного зуба к другому передается по контактным линиям, максимально использующим всю активную поверхность зуба;
- обеспечить боковой зазор для устранения заклинивания зубьев при работе и ограничения мертвых ходов в передаче.
В связи с этим для зубчатых колес и передач по ГОСТ 1643-81 установлены нормы: кинематической точности, плавности работы, контакта зубьев и бокового зазора.
Этот стандарт распространяется на эвольвентные цилиндрические зубчатые передачи внешнего и внутреннего зацепления с диаметром делительной окружности до 6300 мм, модулем от 1 до 55 мм, шириной венца до 1250 мм.
ГОСТ 1643-81 устанавливает 12 степеней точности зубчатых колес и передач, которые обозначаются в порядке убывания точности цифрами 1, 2, 3… 12. Для каждой степени точности (кроме 1 и 2) установлены независимые нормы допустимых отклонений параметров, определяющих кинематическую точность (табл. 7.1), плавность работы (табл. 7.2) и контакт зубьев передачи (табл. 7.3).
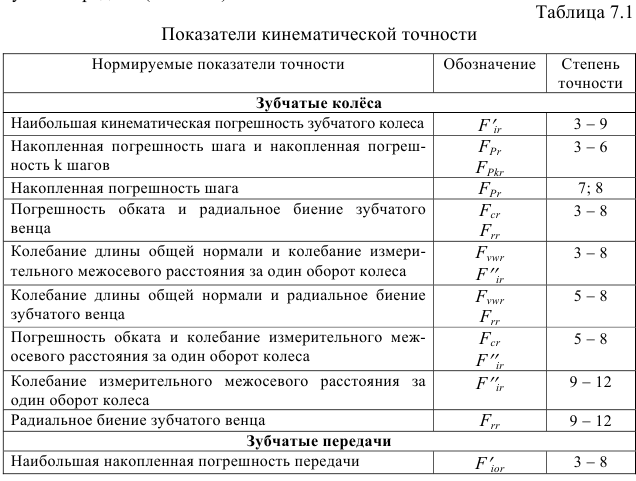
Допуски зубчатых передач
Системой допусков на зубчатые передачи устанавливают гарантированный боковой зазор (), который называют наименьшим предписанным боковым зазором. Его величину определяют вне зависимости от степени точности колес и передач.
Для зубчатых передач с модулем свыше 1 мм установлено шесть видов сопряжений:

которые определяют величину гарантированного наименьшего бокового зазора . На каждый вид сопряжения установлен допуск
бокового зазора, обозначенный строчной буквой латинского алфавита:
Вместо предусмотренных допусков для каждого вида сопряжений при необходимости могут быть использованы увеличенные допуски .
Для нерегулируемых передач с модулем свыше 1 мм установлено шесть классов отклонений межосевого расстояния, обозначаемых в порядке убывания точности римскими цифрами:

Гарантированный боковой зазор в каждом сопряжении обеспечивается при соблюдении предусмотренных классов отклонений межосевого расстояния (табл. 7.4):
В обоснованных случаях это соответствие между видом сопряжения и классом отклонений межосевого расстояния может изменяться.
Условные обозначения точности зубчатых колес и передач
При обозначении точности зубчатых колес и передач указывают степени точности по трем основным погрешностям зубчатых колес (кинематической, плавности, боковому контакту), вид сопряжения зубьев колес в передаче и вид допуска на боковой зазор. Вид допуска на боковой зазор в обозначении не указывается, если соблюдено соответствие с видом сопряжения (см. табл. 7.4).
Если все погрешности назначены по одной степени точности, то обозначение производится одной цифрой и буквой. Например:

где 7 — степень точности по всем нормам точности (кинематической, плавности работы и контакта зубьев); С — вид сопряжения; с — допуск на боковой зазор (в обозначении не указан).
При комбинировании норм из разных степеней точности обозначение примет следующий вид:

где 8 — степень точности по нормам кинематической точности; 7 — степень точности по нормам плавности; 6 — степень точности по нормам контакта зубьев; В — вид сопряжения; а — вид допуска на боковой зазор.
При изменении соответствия между видом сопряжения и классом отклонения межосевого расстояния в обозначении после вида сопряжения и вида допуска через косую черту указывается класс отклонения межосевого расстояния и через тире — рассчитанный гарантированный боковой зазор (), в микрометрах. Например:

Если в цилиндрических зубчатых передачах на какую-либо из норм точности степень точности не задастся, то вместо номера этой степени точности ставится буква , например 7 —
— 6 Н ГОСТ 1643-81.
Контроль элементов зубчатых колес
Контроль колес по всем показателям не является необходимым. Устанавливаются взаимно равноправные комплексы нормируемых показателей, подлежащих контролю. Один из комплексов приведен в табл. 7.5.
Размерные цепи
Качество машин и приборов обеспечивается, в числе других мер, точностью расположения деталей, узлов и механизмов, образующих конечное изделие. При этом число операций, связанных с подгонкой деталей и регулированием их положения в процессе сборки, должно сводиться к минимуму. Зазоры, предельные размеры и другие параметры, координирующие взаимное положение собираемых объектов, как правило, зависят от режимов работы, конструктивных, технологических и эксплуатационных особенностей деталей, узлов и конечных изделий, поэтому часто взаимосвязь между предельными размерами и допусками собираемых деталей и узлов устанавливают с помощью расчетов, основанных на теории размерных цепей.
Размерная цепь — совокупность размеров, образующих замкнутый контур и непосредственно участвующих в решении поставленной задачи.
С помощью размерных цепей можно решать конструкторские, технологические, измерительные и прочие задачи. Расчет размерных цепей позволяет обоснованно назначать допуски на взаимосвязанные размеры деталей и сборочных единиц; облегчает правильную простановку размеров на чертежах, согласованную с порядком обработки деталей и сборки механизмов. Размерные цепи применяют для определения операционных допусков, пересчета конструкторских баз на технологические, для выбора измерительных баз и т.д.
Звено размерной цепи — один из размеров, образующих размерную цепь. Один и тот же механизм, даже одна деталь, могут иметь несколько размерных цепей.
Размерные цепи обозначают прописными буквами русского алфавита и т.д. Звенья, образующие размерную цепь, делятся на составляющие и замыкающее. Составляющие звенья обозначают буквой, принятой для размерной цепи, с порядковыми цифровыми индексами:
;
и т.д. Замыкающее звено в размерной цепи обозначают той же буквой с индексом «О»:
и т.д.
Замыкающее звено — звено размерной цепи, которое получается последним в процессе изготовления или сборки.
Составляющие звенья могут быть увеличивающими или уменьшающими:
-увеличивающее звено — звено, с увеличением которого увеличивается и замыкающее звено;
-уменьшающее звено — звено, с увеличением которого замыкающее звено уменьшается.
Увеличивающие звенья обозначают буквой со стрелкой вправо, например:
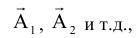
уменьшающие — со стрелкой влево, например:
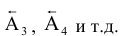
В качестве замыкающих звеньев используют детали (например, комплект прокладок), зазоры, натяги и т.п. Поэтому числовые значения указанных звеньев могут быть положительными, отрицательными и равными нулю.
При решении размерных цепей встречаются два вида задач:
Первая задача:
По заданным номинальным размерам и предельным отклонениям составляющих звеньев цепи определить номинальный размер и предельные отклонения замыкающего звена. Например:
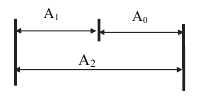
Дано:

Определить:

Вторая задача:
По заданным номинальным размерам всех звеньев цепи и заданным предельным отклонениям замыкающего звена определить допуски и предельные отклонения составляющих звеньев цепи. Например:
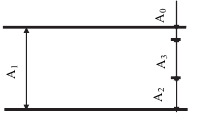
Дано:

Определить:

Методы решения размерных цепей
Существуют следующие методы решения размерных цепей:
1) метод, обеспечивающий полную взаимозаменяемость, или метод «максимума-минимума»;
2) методы, обеспечивающие неполную взаимозаменяемость:
- теоретико-вероятностный;
- групповой подборки деталей (селективная сборка);
- регулирования;
- пригонки.
Основные расчетные формулы метода «максимум-минимум»
Метод «максимума-минимума» основан на предположении, что при сборке механизма возможно сочетание увеличивающих звеньев, изготовленных по наибольшим предельным размерам, с уменьшающими звеньями, изготовленными по наименьшим предельным размерам, или наоборот.
Этот метод расчета обеспечивает полную взаимозаменяемость в процессе сборки и эксплуатации изделий. Однако допуски составляющих размеров, вычисленные по этому методу, особенно для размерных цепей, содержащих много звеньев, могут получиться в техническом и экономическом отношениях неоправданно малыми. Поэтому данный метод применяют для проектирования размерных цепей, имеющих малое число составляющих звеньев невысокой точности.
Первая задача
Номинальный размер замыкающего звена можно определить по формуле (см. пример первой задачи):
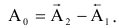
Если принять общее количество звеньев цепи , то количество составляющих будет
— 1. Примем:
— количество увеличивающих звеньев,
— количество уменьшающих, тогда
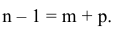
В общем виде формула для расчета номинального размера замыкающего звена будет такой:
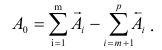
Для примера (раздел 8.1)

На основании равенства (8.1) получим
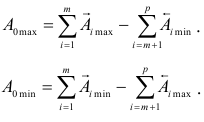
Вычтем почленно из равенства (8.2) равенство (8.3), получим
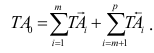
Так как сумма увеличивающих и уменьшающих звеньев есть все составляющие звенья цепи, то полученное равенство можно упростить
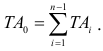
Таким образом, допуск замыкающего звена равен сумме допусков всех составляющих звеньев в цепи.
Чтобы вывести формулы для расчета предельных отклонений замыкающего звена, вычтем почленно из равенства (8.2) равенство (8.1) и из равенства (8.3) равенство (8.1), получим
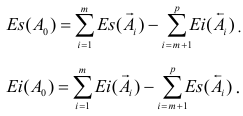
Таким образом, верхнее отклонение замыкающего размера равно разности сумм верхних отклонений увеличивающих и нижних отклонений уменьшающих размеров; нижнее отклонение замыкающего размера равно разности сумм нижних отклонений увеличивающих и верхних отклонений уменьшающих размеров.
Для примера первой задачи (см. раздел 8.1) получим
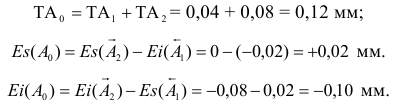
Таким образом,
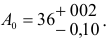
Определим допуск замыкающего звена через полученные предельные отклонения

Это значение совпадает с ранее найденным значением допуска, что подтверждает правильность решения задачи.
Вторая задача
При решении второй задачи допуски составляющих размеров определяют по заданному допуску замыкающего размера одним из следующих способов: равных допусков или допусков одного квалитета.
1) При решении способом равных допусков — на составляющие размеры назначают примерно равные допуски, руководствуясь средним допуском.
Итак, предполагаем, что

тогда сумма допусков всех составляющих размеров равна произведению числа составляющих звеньев на средний допуск, т.е.
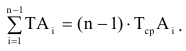
Подставим это выражение в равенство (8.4):

отсюда
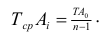
По найденному значению устанавливают допуски на составляющие размеры, учитывая величину и ответственность каждого размера.
При этом должны быть выполнены следующие условия: принятые допуски должны соответствовать стандартным допускам, сумма допусков составляющих размеров должна равняться допуску замыкающего размера, т.е. должно выполняться равенство (8.4). Если при стандартных допусках равенство (8.4) не может быть обеспечено, то на один составляющий размер устанавливают нестандартный допуск, определяя его значение по формуле
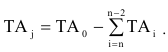
Способ равных допусков прост и дает хорошие результаты, если номинальные размеры составляющих звеньев размерной цепи находятся в одном интервале.
Решим пример второй задачи (см. раздел 8.1) способом равных допусков по формуле (8.7)

Получим
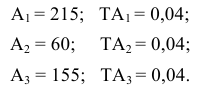
В этом примере равенство (8.4) соблюдается, и корректировать допуск одного из составляющих размеров нет необходимости.
Распишем равенство (8.5) для данного примера

Числовые значения предельных отклонений составляющих размеров выбраны условно.
Получим

Проверим соблюдение равенства (8.6)
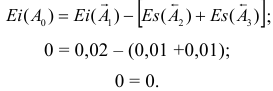
Таким образом, получим ответ

2) Более универсальным и упрощающим подбор допусков при любом разнообразии размеров составляющих звеньев является способ допусков одного квалитета.
При этом способе на размеры всех составляющих звеньев (кроме корректирующего ) назначают допуски из одного квалитета с учетом номинальных размеров звеньев.
Рекомендуется на охватывающие размеры назначать допуски с основным отклонением , а на охватываемые размеры — с основным отклонением
.
Для вывода формулы исходной зависимостью служит равенство (8.4)
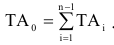
Однако допуск любого размера можно вычислить по формуле

где — число единиц допуска, постоянное в пределах одного квалитета (табл. 8.1);
— единица допуска зависит от номинального размера составляющего звена (табл. 8.2).
Подставим в формулу (8.4) вместо допусков составляющих размеров произведение:
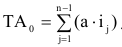
Так как

то

отсюда
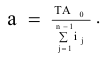
По найденному числу единиц допуска (а) подбирают ближайший квалитет, по которому назначают допуски составляющих размеров. Для удовлетворения условия (8.4) на один из составляющих размеров, как и в предыдущем способе, допуск назначают по формуле (8.8).
Решим пример второй задачи способом назначения допусков одного квалитета по формуле (8.9)
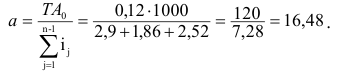
Принимаем: , что соответствует седьмому квалитету
.
По таблицам справочников назначаем допуски составляющих звеньев цепи по седьмому квалитету:

Равенство (8.4) не соблюдается, так как

В качестве корректирующего используем звено . Тогда по формуле (8.8) допуск этого звена будет равен

Итак, получим

Верхнее отклонение замыкающего звена определяется по формуле
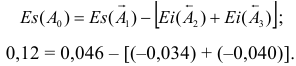
Получим
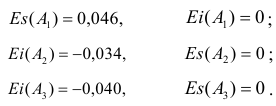
Нижнее отклонение замыкающего звена
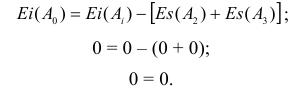
Таким образом, получим ответ

Выводы
Так как допуск замыкающего звена зависит от числа составляющих размеров, то основное правило проектирования размерных цепей можно сформулировать так: при конструировании деталей, узлов сборочных единиц и механизмов необходимо стремиться к тому, чтобы число размеров, образующих размерную цепь, было минимальным. Это принцип кратчайшей размерной цепи.
На чертежах указывают только составляющие размеры с предписанными отклонениями. Замыкающие размеры обычно получаются автоматически в результате обработки деталей или сборки, поэтому их не контролируют и на чертежах не обозначают.
Проставлять на чертежах размеры замкнутыми цепочками не рекомендуется. Особенно недопустимо проставлять замыкающие размеры с отклонениями, так как при изготовлении детали это вызывает брак.
В качестве замыкающих размеров следует принимать наименее ответственные размеры, которые могут иметь большие отклонения.
Возможно эта страница вам будет полезна:
Рекомендации по выбору посадок
В курсе «Детали машин» изучают конструкции деталей и сборочных единиц машин и методы их расчета. При выполнении самостоятельных работ по дисциплине «Нормирование точности и технические измерения» на чертежах общих видов и рабочих чертежах задаются посадки цилиндрических сопряжений, а также допуски размеров, допуски формы и расположения поверхностей.
При выборе посадок, допусков размеров деталей, а также допусков формы и расположения следует учитывать: назначение детали в сборочной единице, роль отдельных ее поверхностей (цилиндрических, конических, торцовых), влияние отклонений размеров, формы и расположения осей или поверхностей детали на смежные с ней детали, влияние суммы отклонений точностных параметров всех деталей на качественные показатели изделия (точность и плавность вращения, бесшумность, долговечность).
Детали подшипниковых узлов
Кольца, втулки
Между подшипниками и базовыми торцами валов или корпусов часто расположены дистанционные кольца и втулки. Условимся называть втулками детали, у которых отношение длины к посадочному диаметру (
или
):
, и кольцами, если это отношение меньше 0,8 (рис. 9.1). Число 0,8 в отношении
принято из опыта изготовления и эксплуатации изделий машиностроения. Следует иметь в виду, что оно дает лишь грубую, приближенную оценку того, какая поверхность детали является основной базой: цилиндр или торец.
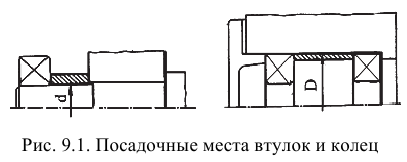
С уверенностью можно лишь сказать, что при и посадке с натягом основной базой является цилиндр, а при
и любой посадке базой является торец. Чтобы повысить точность расположения базового торца надо кольцо заменить втулкой, увеличив длину посадочной поверхности до
, при этом следует назначить переходную посадку с минимальным зазором или небольшим натягом. Например, для посадки па вал и в корпус.

Если выбор полей допусков отверстия и вала ничем не обусловлен, рекомендуется принимать посадки колец па вал: или
. При высокой частоте вращения вала
в целях снижения возможного дисбаланса посадки колец на вал следует принимать посадки:

Если поля допусков валов заданы в связи с установкой соседних деталей, следует применять для гарантии зазора поля допусков отверстий колец: или
.
Поле допуска наружного диаметра колец, установленных в отверстиях корпусов, во всех случаях следует принимать .
При длине кольца для него задают посадку с зазором
. Такая посадка облегчит также и установку колеса на вал.
Стаканы
В стаканах обычно размещают подшипники фиксирующей опоры вала червяка и опоры вала конической шестерни. Иногда стаканы применяют для удобства сборки. Для легкости установки стаканов в корпусные детали желательно применение посадок с зазором. Но иногда возможно их смещение в пределах зазоров, что вызовет изменение положения оси вращения вала и, как следствие, увеличение концентрации нагрузки, поэтому в соединении стаканов с корпусом зазоры нежелательны. В связи с этим рекомендуется применять следующие переходные посадки для стаканов:
- нерегулируемые в осевом направлении —
- регулируемые в осевом направлении —
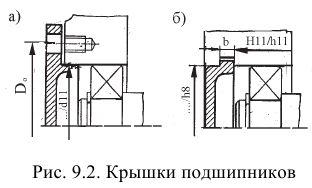
Крышки подшипников
На рис. 9.2 показаны накладная и закладная крышки без отверстия для прохода вала. Торцовые поверхности крышек свободны и не используются в качестве базовых для установки подшипников качения. Единственное назначение таких крышек -закрыть отверстие корпусной детали.
Точное центрирование таких крышек по отверстию корпуса не требуется, поэтому поле допуска центрирующей поверхности накладной крышки принимают по (рис. 9.2, а).
Поле допуска центрирующей поверхности закладных крышек любой конструкции в целях уплотнения против вытекания смазки принимают . Общей для всех закладных крышек является посадка выступа крышки в пазу корпуса, которую принимают
(рис. 9.2, 6).
Зубчатые и червячные передачи
Передача нагрузки с колеса на вал соединением с натягом
Соединение обеспечивает точную установку колеса на вал и высокую нагрузочную способность, поэтому соединения с натягом получают все большее распространение, особенно в редукторостроении, несмотря на высокую концентрацию напряжений, вызываемую соединением.
Основным способом сборки для осуществления соединения с натягом колес с валами является нагрев колеса.
Рекомендуемые посадки:

Передача момента шпоночным соединением
При передаче через шпоночное соединение вращающего момента возникают значительные местные деформации вала и ступицы около шпоночного паза, а также деформации самой шпонки. Наличие шпоночного паза приводит к асимметричной деформации вала и ступицы, в результате чего давление по рабочим граням шпонки и шпоночным пазам вала и ступицы распределяется неравномерно.
Рекомендуемые посадки:
- для цилиндрических прямозубых колес —
6;
- для цилиндрических косозубых и червячных колес —
;
- для конических колес —
;
- для неподвижных колес коробок передач (при необходимости сборки внутри корпуса) —
.
Передача момента шлицевым соединением
При одинаковых габаритах шлицевые соединения имеют большую нагрузочную способность и обеспечивают большее сопротивление усталости вала, чем шпоночное соединение. Они обеспечивают хорошее центрирование и направляют детали по валу, поэтому они являются основными для соединения с валом подвижных вдоль вала зубчатых колес коробок передач. Рекомендуемые посадки представлены в табл. 9.1.
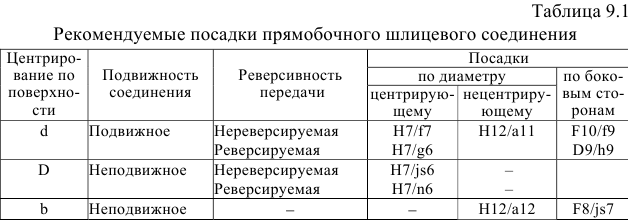
Муфты, шкивы, звездочки
Муфты, шкивы, звездочки — эти детали, как правило, надевают на консольные концы валов. В большинстве случаев их монтаж осуществляется после того, как собран основной узел, поэтому одним из основных требований, предъявляемых к соединениям муфт, шкивов, звездочек с валами, является легкость сборки.
Рекомендуемые посадки при применении шпоночных соединений:
- для муфт —
- для звездочек —
- для шкивов —
Кстати тут дополнительная теория из учебников.
Всё о технических измерениях
«Измеряй все доступное измерению и делай доступным все недоступное ему»
Галилео Галилей
Нет ни одной области практической деятельности человека, где можно было бы обойтись без количественных оценок, получаемых в результате измерений. Роль измерений непрерывно возрастает во всех областях науки и техники. И это естественно: каждому продвижению вперед в области естественных и технических наук, каждому открытию, созданию новых машин, изделий и материалов предшествует большое число многообразных измерений. Как следствие, растут требования к качеству измерений. Большое значение приобретает также достоверность и надежность измерений. Все больше возрастает и роль метрологии — науки об измерениях, методах и средствах обеспечения их единства и способах достижения требуемой точности.
Измерения являются одним из путей познания природы человеком. Измерения количественно характеризуют окружающий материальный мир, раскрывая действующие в природе закономерности. Об этом очень образно сказал основоположник отечественной метрологии Д. И. Менделеев: «Наука начинается с тех пор, как начинают измерять». Известно аналогичное высказывание и основоположника английской метрологии Томсона: «Каждая вещь известна лишь в той степени, в какой её можно измерить».
Без измерений невозможно существование современной науки, промышленности, сельского хозяйства, медицины, торговли. Измерения необходимы в военном деле, в быту, в спорте и во многих других видах деятельности человека. Они выполняются не только в разных земных условиях, но и в атмосфере, в космосе, на других планетах. Измерения позволяют управлять технологическими процессами, предприятиями, народным хозяйством в целом. Огромное значение имеют измерения в повышении качества продукции. Много измерительных приборов применяются в быту. Измерительная информация стала неотъемлемой спутницей человека. Можно с уверенностью сказать, что измерения сопровождают нас в течение всей жизни.
Принимая во внимание, что в машиностроении ежегодно выполняются десятки миллиардов измерений, что требования к качеству продукции непрерывно повышаются, следует рассматривать метрологическое обеспечение как один из крупных резервов повышения эффективности машиностроительного производства. Массовость и значимость измерений обусловили превращение метрологии в активный инструмент повышения качества работ и эффективности производства.
Основные термины и определения
Основные термины и определения даны в соответствии с РМГ 29-99. Постановлением Государственного комитета Российской Федерации по стандартизации и метрологии от 17 мая 2000 г. № 139-ст межгосударственные Рекомендации РМГ 29-99 введены в действие непосредственно в качестве Рекомендаций по метрологии Российской Федерации с 1 января 2001 г. (взамен ГОСТ 16263-70).
Измерение — это совокупность операций по применению технического средства, хранящего единицу физической величины, обеспечивающих нахождение соотношения (в явном или неявном виде) измеряемой величины с ее единицей и получение значения этой величины.
В простейшем случае, прикладывая линейку с делениями к какой-либо детали, по сути, сравнивают ее размер с единицей, хранимой линейкой, и, произведя отсчет, получают значение величины (длины, высоты, толщины и других параметров детали).
С помощью измерительного прибора сравнивают размер величины, преобразованной в перемещение указателя, с единицей, хранимой шкалой этого прибора, и проводят отсчет.
Приведенное определение понятия «измерение» удовлетворяет общему уравнению измерений, что имеет существенное значение в деле упорядочения системы понятий в метрологии. В нем учтена техническая сторона (совокупность операций), раскрыта метрологическая суть измерений (сравнение с единицей) и показан гносеологический аспект (получение значения величины).
От термина «измерение» происходит термин «измерять», которым широко пользуются на практике. Все же нередко применяются такие термины, как «мерить», «обмерять», «замерять», «промерять», не вписывающиеся в систему метрологических терминов. Их применять не следует. Не следует также применять такие выражения, как «измерение значения» (например, мгновенного значения напряжения или среднего квадратического значения), так как значение величины — это уже результат измерений.
В тех случаях, когда невозможно выполнить измерение (не выделена величина как физическая и не определена единица измерений этой величины), практикуется оценивание таких величин по условным шкалам.
Измерения, отнесенные к линейным, радиусным и угловым величинам, называют техническими измерениями.
Физическая величина — это одно из свойств физического объекта (физической системы, явления или процесса), общее в качественном отношении для многих физических объектов, но в количественном отношении индивидуальное для каждого из них.
Размер физической величины — это количественная определенность физической величины, присущая конкретному материальному объекту, системе, явлению или процессу.
Значение физической величины — это выражение размера физической величины в виде некоторого числа принятых для нее единиц.
Числовое значение физической величины — это отвлеченное число, входящее в значение величины.
Истинное значение физической величины — это значение физической величины, которое идеальным образом характеризует в качественном и количественном отношении соответствующую физическую величину. Истинное значение физической величины может быть соотнесено с понятием абсолютной истины. Оно может быть получено только в результате бесконечного процесса измерений с бесконечным совершенствованием методов и средств измерений.
Возможно эта страница вам будет полезна:
Действительное значение физической величины — это значение физической величины, полученное экспериментальным путем и настолько близкое к истинному значению, что в поставленной измерительной задаче может быть использовано вместо него.
Система физических величин — это совокупность физических величин, образованная в соответствии с принятыми принципами, когда одни величины принимают за независимые, а другие определяют как функции независимых величин.
В названии системы величин применяют символы величин, принятых за основные. Так, система величин механики, в которой в качестве основных приняты длина , масса
и время
, должна называться системой
. Система основных величин, соответствующая Международной системе единиц (СИ), должна обозначаться символами
, обозначающими соответственно символы основных величин: длины —
, массы —
, времени —
, силы электрического тока —
, температуры —
, количества вещества —
, силы света —
.
Основная физическая величина — это физическая величина, входящая в систему величин и условно принятая в качестве независимой от других величин этой системы.
Производная физическая величина — это физическая величина, входящая в систему величин и определяемая через основные величины этой системы. Примеры производных величин механики системы :
Размерность физической величины — это выражение в форме степенного одночлена, составленного из произведений символов основных физических величин в различных степенях и отражающее связь данной физической величины с физическими величинами, принятыми в данной системе величин за основные с коэффициентом пропорциональности, равным 1.
Степени символов основных величин, входящих в одночлен, в зависимости от связи рассматриваемой физической величины с основными, могут быть целыми, дробными, положительными, отрицательными. Понятие размерность распространяется и на основные величины. Размерность основной величины в отношении самой себя равна единице, т.е. формула размерности основной величины совпадает с ее символом. В соответствии с международным стандартом ИСО 31/0, размерность величин следует обозначать знаком dim. В системе величин размерность величины х будет:
, где
— символы величин, принятых за основные (соответственно длины, массы, времени).
Показатель размерности физической величины — это показатель степени, в которую возведена размерность основной физической величины, входящая в размерность производной физической величины. Показатели степени называют показателями размерности производной физической величины
. Показатель размерности основной физической величины в отношении самой себя равен единице.
Размерная физическая величина — это физическая величина, в размерности которой хотя бы одна из основных физических величин возведена в степень, не равную нулю. Например, сила в системе
является размерной величиной

Безразмерная физическая величина — это физическая величина, в размерность которой основные физические величины входят в степени, равной нулю.
Аддитивная физическая величина — это физическая величина, разные значения которой могут быть суммированы, умножены на числовой коэффициент, разделены друг на друга. К аддитивным величинам относятся длина, масса, сила, давление, скорость, время и др.
Нсаддитивная физическая величина — это физическая величина, для которой суммирование, умножение на числовой коэффициент или деление друг на друга ее значений не имеет физического смысла. Например, термодинамическая температура.
Единица физической величины — это физическая величина фиксированного размера, которой условно присвоено числовое значение, равное единице, и применяемая для количественного выражения однородных с ней физических величин.
Система единиц физических величин — это совокупность основных и производных единиц физических величин, образованная в соответствии с принципами для заданной системы физических величин, например международная система единиц (СИ), принятая в 1960 г.
В зависимости от метрологического назначения измерения делятся на технические и метрологические. Данный классификационный признак не предусмотрен РМГ 29-99 и дается для общего обозрения.
Технические измерения проводятся рабочими СИ. Они являются наиболее массовым видом измерений. Например, измерение давления пара в котле при помощи манометра.
Метрологические измерения выполняются при помощи эталонов с целью воспроизведения единиц физических величин для передачи их размера рабочим СИ.
Выбор измерительных средств
При выборе измерительных средств для контроля изделий учитывают совокупность метрологических (цена деления, погрешность измерения и др.), эксплуатационных и экономических показателей. К эксплуатационным и экономическим показателям относятся: повторяемость измеряемых размеров (массовость) и доступность их для контроля; стоимость и надежность измерительных средств; продолжительность работы (до ремонта); время, затрачиваемое на настройку и процесс измерения; масса, габариты и рабочая нагрузка.
Выбор измерительных средств в зависимости от точности измерении
При выборе средств измерения точность средств измерений должна быть достаточно высокой по сравнению с заданной точностью выполнения измеряемого размера, а трудоемкость измерений и их стоимость должны быть, возможно, более низкими, обеспечивающими наиболее высокие производительность труда и экономичность.
Правильный выбор измерительных средств с учетом допускаемых погрешностей измерений размеров до 500 мм регламентирует ГОСТ 8.051-81. Стандарт предусматривает значения допускаемых погрешностей измерений в зависимости от допусков на обработку. Значения допускаемых погрешностей измерений приведены в табл. 10.1.
Пределы допускаемых погрешностей измерений установлены из расчета (в среднем) от 20 до 35 % значения допуска (с учетом квалитетов).
Погрешность измерительного средства должна быть меньше допускаемой погрешности измерения. Предельные погрешности различных СИ приведены в табл. 10.2 и 10.3.
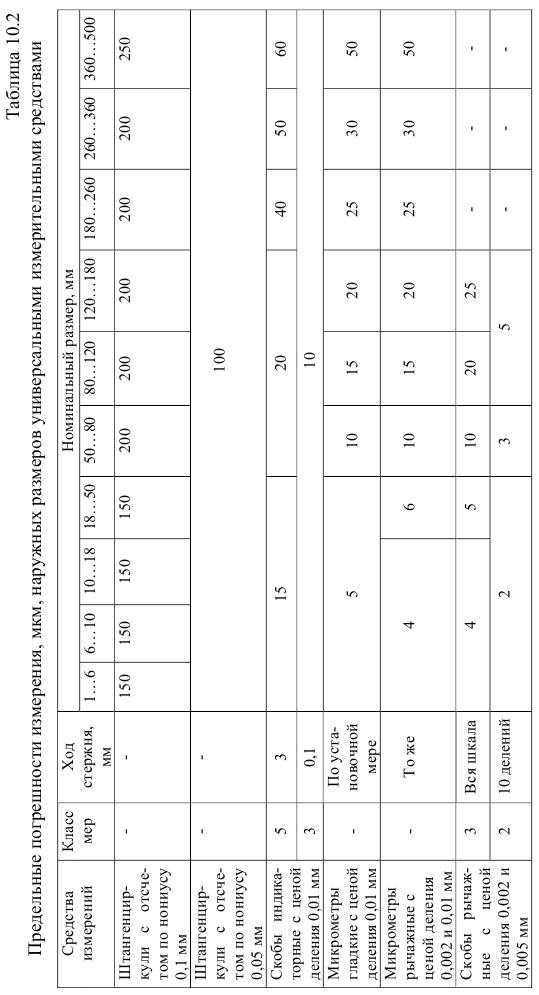
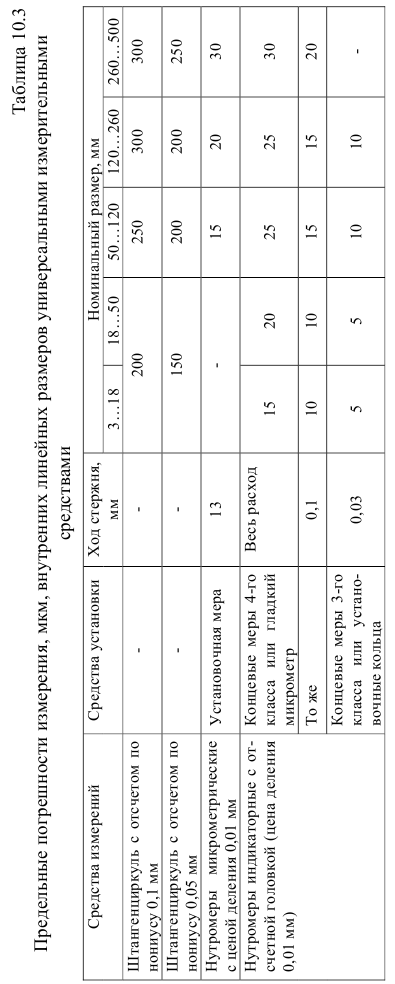
Пример. Выбрать средство для измерения в условиях серийного производства диаметра элемента вала .
По табл. 10.1 находим допуск размера вала и допускаемую погрешность измерения
.
По табл. 10.2 подбираем средство измерений наружных размеров. Здесь указаны предельные погрешности измерения различными средствами. Подбираем по этой таблице средство, имеющее диапазон измерения, включающий в себя номинальный диаметр 50 мм, и имеющее предельную погрешность измерения, близкую к 40 мкм, т.е. к допускаемой погрешности измерения рассматриваемой ступени вала. Лучше всех этим требованиям удовлетворяет скоба индикаторная с диапазоном измерения 0…50 мм, ценой деления 0,01 мм и предельной погрешностью измерения 15 мкм. Эта скоба подходит и по производительности измерения для условий серийного производства.
Выбор измерительных средств в зависимости от организационно-технических форм контроля
Детали в процессе их изготовления могут подвергаться сплошному 100%-му контролю и выборочному контролю.
Сплошному контролю подлежат детали и узлы по так называемым аварийным параметрам и таким, которые определяют эксплуатационные показатели машин или приборов в целом.
При стабильном технологическом процессе изготовления деталей и сборки узлов и изделий, когда появление брака маловероятно, целесообразно применять выборочный контроль деталей, узлов и изделий. Наиболее часто применяют статистический метод выборочного контроля. Этот метод применяется для приемки готовых изделий (приемочный контроль) и для управления точностью в процессе производства (управляющий контроль).
Сплошной и выборочный приемочный контроль относятся к пассивным формам контроля, при которых только регистрируются результаты измерения, а на ход технологического процесса эти измерения не влияют. При пассивных формах контроля используют универсальные измерительные приборы и инструменты.
Для повышения качества машин, сокращения потерь от брака и повышения производительности труда необходимо применять активные формы контроля, при которых результаты измерения используются для регулирования точности технологических процессов.
Рассмотрим систему централизованного статистического контроля (СЦСК — 1). Эта система предназначена для автоматического регулирования точности технологических процессов с целью недопущения появления брака и сокращения количества подналадок технологического процесса.
Эта система контроля позволяет также анализировать точность работы станков и технологической оснастки.
СЦСК — 1 состоит из ряда измерительных позиций, установленных на соответствующих станках, и управляющей счетной машины УСМ — 5, установленной на центральном контрольном пункте (рис. 10.1).
На измерительных позициях определяют отклонения действительных размеров от заданных. Эти отклонения затем первично преобразуются в соответствующие им числа электрических импульсов.
Счетная машина имеет два счетчика: счетчик-повторитель (СП), который производит вторичное преобразование отклонений в число импульсов, и счетчик-накопитель, суммирующий все импульсы при измерении всех деталей.
Накопленное число импульсов автоматически сравнивается с пределом, заданным для данной измерительной позиции и хранящимся в памяти счетной машины. Если число, накопленное на счетчике-накопителе, превысит это предельное число, то срабатывают специальная схема совпадения и реле исполнительного органа (ИО), контакты которого включают сигнализацию о браке; подается команда на прекращение обработки или на подналадку станка.
Связь счетной машины с соответствующими измерительными позициями осуществляется с помощью программного счетчика ПС — 1 по определенной программе.
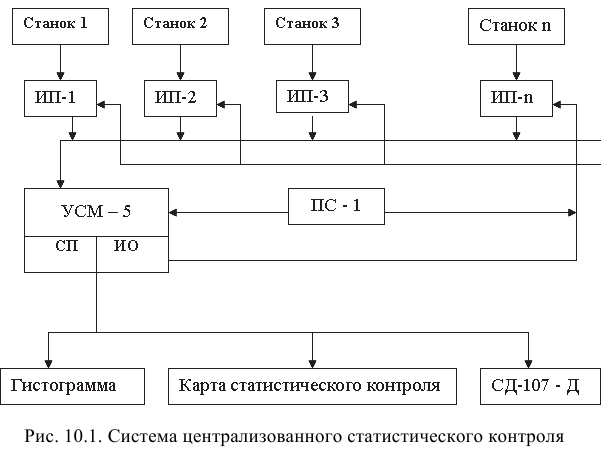
Система централизованного статистического контроля является универсальной системой, так как к ней могут быть подключены измерительные позиции, стоящие на любых станках. К счетной машине могут быть подключены построитель гистограммы, карты статистического контроля, а также суммирующая десятиклавишная машина с дистанционным управлением типа СД — 107 — Д.
Выбор измерительных средств в зависимости от масштабов производства
При индивидуальном и мелкосерийном производстве объекты производства часто меняются, высокое качество изделий не гарантируется ходом технологического процесса, а зависит от индивидуальных навыков и квалификации рабочего. Поэтому при индивидуальном и мелкосерийном производстве необходимы тщательный пооперационный контроль деталей, соответствующие универсальные измерительные средства и контролеры высокой квалификации.
При серийном производстве изготавливаются взаимозаменяемые детали, узлы и изделия, номенклатура которых не изменяется в течение длительного времени. Однородность деталей по качеству достигается применением специализированного оборудования, инструмента, оснастки. Работа ведется по отработанной пооперационной технологии. Поэтому пооперационный контроль не обязателен. Контроль осуществляется после ряда операций или после окончательного изготовления деталей универсальными измерительными средствами, специализированными контрольными приспособлениями, жесткими предельными калибрами и шаблонами.
При массовом производстве номенклатура изделий постоянна. Качество изделий обеспечивается отработанной технологией, широким применением специализированного оборудования, приспособлений и инструмента, а также контрольными операциями, которые являются составной частью единого технологического процесса. При массовом производстве широко применяются высокопроизводительные механизированные и автоматические контрольно-измерительные средства.
Выбор измерительных средств в зависимости от конструктивных особенностей контролируемой детали
Конструктивная форма, число контролируемых параметров, габариты и масса детали также влияют на выбор типа измерительного средства.
Детали больших габаритов и большой массы контролируются переносными измерительными средствами.
При большом количестве контролируемых параметров рекомендуется применять многомерные контрольно-измерительные устройства.
Автоматы особо эффективны при контроле деталей простой геометрической формы, небольшого веса, с небольшим числом контролируемых параметров.
При выборе средства измерения необходимо учитывать также материал контролируемой детали, жесткость ее конструкции и шероховатость поверхности.
Размеры тонкостенных деталей предпочтительно контролировать бесконтактным методом или на приборах с небольшим измерительным усилием.
ЗАДАНИЯ К РАЗДЕЛУ 10.2: Выбрать средство для измерения в условиях серийного производства следующего размера по своему варианту (номер варианта соответствует последней цифре номера зачетной книжки).
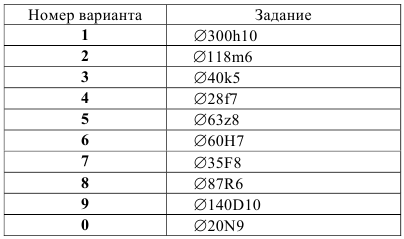
Средства измерений линейных размеров
Меры длины концевые плоскопараллельные
Концевые меры длины — это однозначные меры, размер которых образован противоположными измерительными поверхностями. Наиболее распространены в машиностроении плоскопараллельные концевые меры длины (КМД). Особенность КМД заключается в том, что их измерительные поверхности имеют высокую плоскостность, параллельны между собой и обладают весьма малой шероховатостью. Эти свойства обеспечивают одинаковое для данной меры расстояние между измерительными поверхностями в любом месте. Конструкция всех КМД практически одинакова — это пластины с двумя противоположными плоскопараллельными измерительными поверхностями.
Материалом для изготовления КМД служат, в подавляющем большинстве, хромистые закаленные стали, применяют также и твердый сплав ВК6М.
Концевые меры длины делятся на рабочие и образцовые.
Рабочие концевые меры длины предназначены для регулировки и настройки на размер показывающих измерительных приборов (рис. 10.2), для непосредственных измерений, а также для выполнения особо точных разметочных работ и наладки станков.
Рабочие КМД разделяются по классам точности. Класс точности меры показывает, какое отклонение имеет действительный размер данной меры от ее номинального размера. Классы точности концевых мер — это ряды допусков на изготовление их действительных размеров в зависимости от значений их номинальных размеров. Концевые меры длины выпускают по следующим классам точности: 0, 1,2, 3.
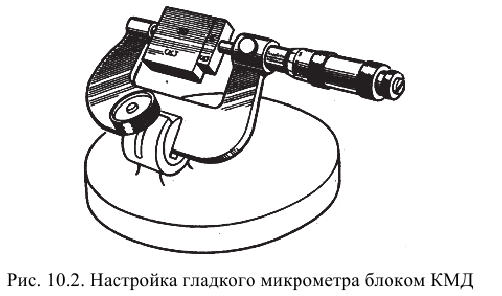
Кроме того, установлены дополнительные классы точности: 00, 01. Эти классы применяют по согласованию между потребителем и изготовителем.
Для мер, находящихся в эксплуатации, установлены также классы точности 4 и 5. Они присваиваются концевым мерам, значительно изношенным и изменившим размер.
Образцовые меры применяют для передачи размера единицы длины от первичного эталона концевым мерам меньшей точности и для поверки и градуировки измерительных приборов длины. Образцовые КМД делят по разрядам: 1, 2, 3, 4.
Разряд концевых мер длины показывает, с какой погрешностью измерения производится аттестация действительного размера длины концевой меры. Разряды — это ряды значений погрешностей измерения, допускаемых при аттестации КМД.
Притираемость измерительных поверхностей концевой меры — это способность измерительных поверхностей КМД сцепляться друг с другом при смещении в плотно прижатом состоянии. Такое сцепление (притирание) КМД происходит благодаря высокой плоскостности и малой шероховатости их измерительных поверхностей и позволяет собирать из отдельных мер блоки КМД. Суммарный размер такого блока равен сумме размеров мер, вошедших в него. Блоки из КМД можно получить практически любого требуемого размера.
Инструментальные заводы выпускают КМД, скомплектованные в наборы и уложенные в отдельные футляры для того, чтобы из них можно было собирать блоки необходимых размеров. Особенность комплектовки всех наборов заключается в том, что в набор должны быть вложены меры одного класса точности. При поверке мер во время эксплуатации набору присваивается единый класс точности, равный низшему классу точности меры из числа вложенных в данный набор.
Примеры условного обозначения КМД:
- Набор № 2 концевых мер длины из стали, класса точности 1: Концевые меры 1 — Н2 ГОСТ 9038-90;
- Набор № 3 концевых мер из твердого сплава, класса точности 2: Концевые меры 2 — НЗ — Т ГОСТ 9038-90;
- Концевая мера длиной 1,49 мм из стали, класса точности 3: Концевая мера 3-1,49 ГОСТ 9038-90;
- Комплект образцовых концевых мер длины 1-го разряда: Концевые меры образцовые 1 — КО ГОСТ 9038-90;
- Набор № 3 образцовых концевых мер 2-го разряда: Концевые меры образцовые 2 — НОЗ ГОСТ 9038-90.
Штангенинструменты
Штангенинструментами называют средства измерений линейных размеров, основными частями которых являются штанга со шкалой и нониус — вспомогательная шкала для уточнения отсчета показаний.
Штангенциркули
Штангенциркули предназначены для измерения наружных и внутренних размеров изделий, некоторыми из них можно еще измерять глубину выемок и высоту уступов. Основные типы штангенциркулей предусмотрены ГОСТ 166-89 «Штангенциркули. Технические условия» и приведены в табл. 10.4. Конструкция основных типов штангенциркулей приведена на рис. 10.3.
Штангенциркули с отсчетом по нониусу 0,1 мм делятся на классы точности: 1 и 2.
Примеры условного обозначения штангенциркулей:
- 1) штангенциркуль ШЦ — II — 250 — 0,05 ГОСТ 166-89;
- 2) штангенциркуль ШЦ — II — 250 — 630 — 0,1 — 1 ГОСТ 166-89;
- Тип II с диапазоном измерения 250 — 630 мм, значением отсчета по нониусу 0,1 мм, класс точности 1;
- 3) штангенциркуль ШЦК — 1 — 150 — 0,02 ГОСТ 166-89;
- 4) штангенциркуль ШЦЦ -1 — 125 — 0,01 ГОСТ 166-89.
Штангенглубиномеры
Штангенглубиномеры (рис. 10.4) применяются для прямого измерения глубины выемок и высоты уступов. Штангенглубиномеры бывают нормальные (ШГ), с острием (2ШГ), с уступом (ЗШГ). Отсчет по нониусу для всех штангенглубиномеров составляет 0,05 мм.
Примеры условного обозначения штангенглубиномеров:
- 1) ШГ — 200 ГОСТ 162-90;
- 2) 2ШГ- 160 ГОСТ 162-90;
- 3) ЗШГ-160-400 ГОСТ 162-90.
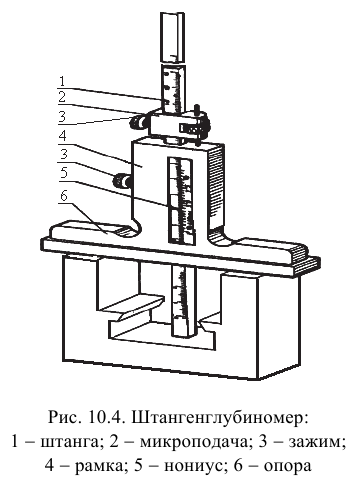
Штангенрейсмасы
Штангенрейсмасы (рис. 10.5) применяются для пространственной разметки и прямых измерений на точной плите расстояний от базовых поверхностей до выемок, выступов и осей отверстий. Типы штангенрейсмасов: ШР — с отсчетом по нониусу;
ШРК — с отсчетным устройством с круговой шкалой; ШРЦ — с электронным цифровым отсчетным устройством. Примеры условного обозначения штангенрейсмасов:
- 1) ШР-250-0,05 ГОСТ 164-90;
- 2) ШРК-250-0,02 ГОСТ 164-90;
- 3) ШРЦ-250-0,01 ГОСТ 164-90.
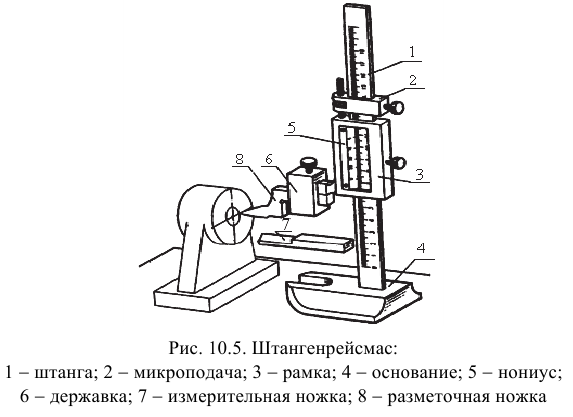
Микрометрические инструменты
Микрометрическими инструментами называют средства измерений линейных размеров, основанные на использовании винтовой пары, называемой микропарой.
Микрометры
Основные типы микрометров представлены в ГОСТ 6507-90 «Микрометры. Технические условия» и приведены в табл. 10.5. Конструкция микрометров приведена на рис. 10.6.
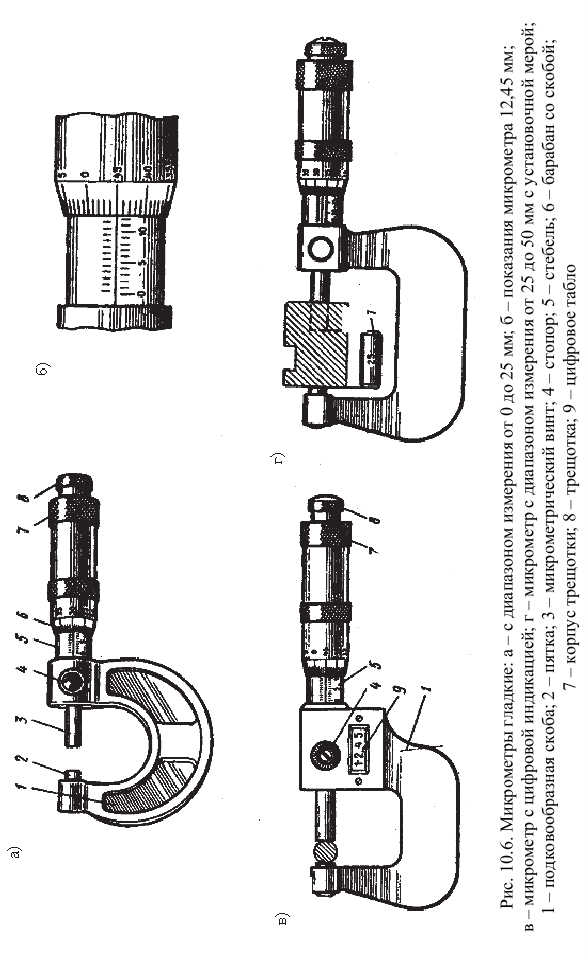
Для удобства и ускорения отсчета показаний промышленность выпускает гладкий микрометр с цифровой индикацией (рис. 10.6, в). Цена деления шкалы барабана — 0,01 мм. Микрометры выпускают классов точности 1 и 2.
Примеры условного обозначения микрометров:
- 1) МК 50 — 1 ГОСТ 6507-90. Микрометр гладкий с диапазоном измерений 25 — 50, 1 класса точности;
- 2) МК Ц 75 ГОСТ 6507-90. Микрометр гладкий с электронным цифровым отсчетным устройством, диапазон измерений 50 — 75 мм;
- 3) МЛ-10 ГОСТ 6507-90.
Микрометрические глубиномеры
Микрометрические глубиномеры (рис. 10.7) применяются для измерения глубины выемок и высоты уступов в деталях машин.
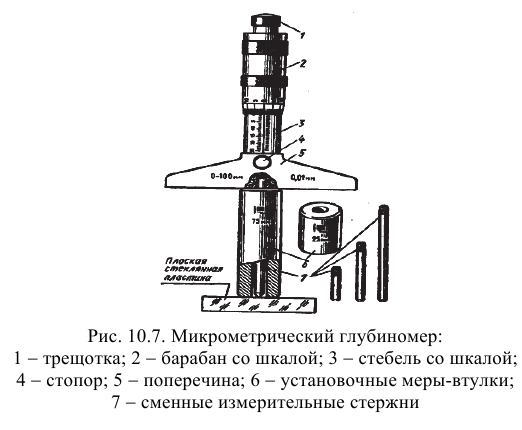
Пример условного обозначения микрометрического глубиномера:
ГМ — 100 ГОСТ 7470-92. Глубиномер микрометрический, диапазон измерений 0-100 мм.
Микрометрические нутромеры
Микрометрическими нутромерами (рис. 10.8) измеряют размеры отверстий, ширину пазов и другие внутренние линейные размеры и отклонения формы деталей машин. Максимальный размер, измеряемый микрометрической головкой с индикатором и удлинителем, — 10 000 мм.
Примеры условного обозначения микрометрических нутромеров:
- 1) НМ 75 ГОСТ 10-88;
- 2) ИМИ 2500-4000 ГОСТ 10-88.
Микрометры рычажные
Типы рычажных микрометров установлены ГОСТ 4381-87: MP и МРИ. Рычажный микрометр (рис. 10.9) в отличие от гладкого не имеет трещотки для ограничения усилия измерения. Измерительное усилие ограничивает пружина, которая прижимает подвижную пятку к поверхности детали, а деталь к торцу микровинта.
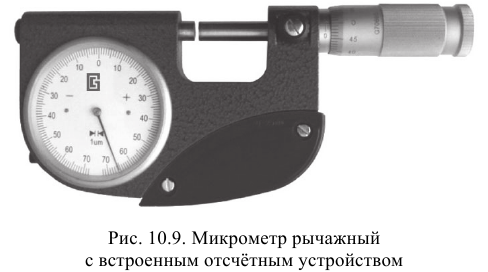
Условное обозначение рычажных микрометров:
MP 50 ГОСТ 4381-87;
МРИ 400-0,01 ГОСТ 4381-87.
Индикаторные инструменты
Индикаторные или рычажно-механические приборы предназначены для контроля линейных размеров и отклонений формы и расположения поверхностей. Используют эти приборы главным образом для относительных измерений.
Индикаторы часового типа
Из рычажно-механических приборов наиболее широко применяются индикаторы часового типа (ГОСТ 577-67) от 0 до 10 мм и малогабаритные от 0 до 2 мм.
Индикаторами часового типа (рис. 10.10) оснащают ряд измерительных приборов общего и специального назначения. Интервалы измерений: от 0 до 5 мм.
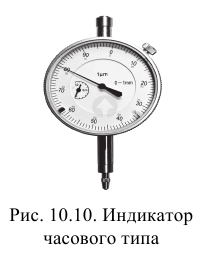
Скобы с отсчетным устройством Типы, основные параметры и технические требования к скобам установлены ГОСТ 11098-75: CP и СИ (скобы рычажные и скобы индикаторные). Рычажная скоба не имеет собственного размерного устройства, и измерение ею производится методом сравнения с мерой (рис. 10.11).
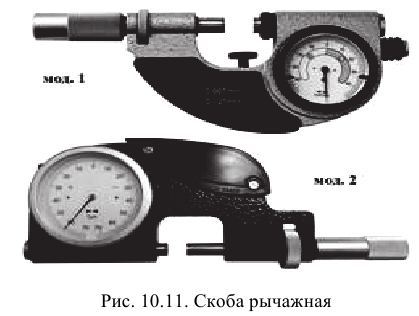
Индикаторные скобы (рис. 10.12) служат для измерения линейных размеров деталей цилиндрической формы в серийном производстве машин. Они удобны в применении, производительны, но обладают относительно невысокой точностью. Чаще всего ими измеряют гладкие валы после токарной обработки резцами или после круглой шлифовки, но при допусках на размер не менее 0,05 мм. Условное обозначение скоб: CP 50 ГОСТ 11098-75; СИ 50 ГОСТ 11098-75.
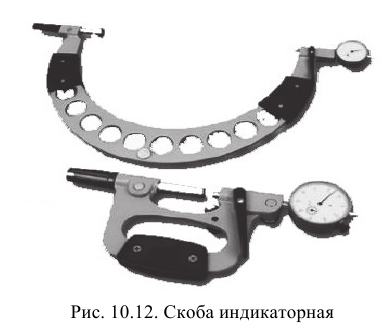
Нутромеры индикаторные
Технические условия на индикаторные нутромеры предусмотрены ГОСТ 868-82. Индикаторные нутромеры имеют цену деления 0,01 мм и делятся на два класса точности: 1 и 2.
Второй класс точности предусмотрен для диапазона измерения свыше 250 мм.
Условное обозначение индикаторного нутромера:
НИ 10 — 18 — 1 ГОСТ 868-82 (диапазон измерения 10-18 мм; 1 класс точности).
Глубиномеры индикаторные
Технические условия и условное обозначение глубиномеров индикаторных (рис. 10.13) предусмотрены ГОСТ 7661-67.
Пример условного обозначения глубиномера индикаторного:
ГИ- 100 ГОСТ 7661-67.
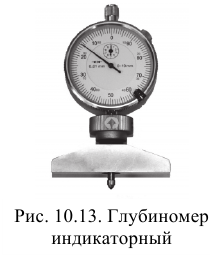
Индикаторы многооборотные
Технические условия на многооборотные индикаторные головки (МИГ) предусмотрены ГОСТ 9696-82. Стандартом предусмотрено два типа
головок: 1 и 2. Первый тип (рис. 10.14) имеет цену деления 0,001 мм, второй тип — 0,002 мм. МИГ делятся на классы точности: 0 и 1. Кроме того, предусмотрены индикаторы повышенной точности.
Примеры условного обозначения многооборотных индикаторных головок:
1 МИГ — 1 ГОСТ 9696-82 (тип 1, класс точности 1);
1 МИГ П ГОСТ 9696-82 (тип 1, повышенной точности).
Нутромеры с ценой деления 0,001 и 0,002 мм
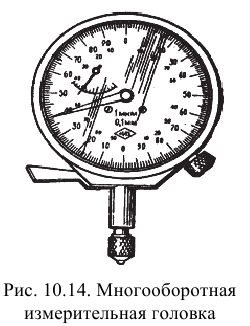
Технические условия на нутромеры предусмотрены ГОСТ 9244-75. Цена деления шкалы 0,001 мм предусмотрена для нутромеров с диапазоном измерения от 2 до 10 мм, а цена деления 0,002 мм для нутромеров с диапазоном от 10 до 260 мм.
Примеры условного обозначения нутромеров:
Нутромер 6-10 ГОСТ 9244-75;
Нутромер 10-18 ГОСТ 9244-75.
Специальные измерительные средства (калибры гладкие)
Классификация калибров
Калибром по ГОСТ 27284-87 называется техническое средство контроля, воспроизводящее геометрические параметры элементов изделия, определяемые заданными предельными линейными или угловыми размерами, и контактирующее с элементом изделия по поверхностям, линиям или точкам.
Калибры бывают нормальные и предельные.
Нормальный калибр — это калибр, воспроизводящий заданный линейный или угловой размер и форму сопрягаемой с ним поверхности контролируемого элемента изделия. О годности деталей судят по равномерности зазора между проверяемым профилем и рабочим профилем нормального калибра.
Предельный калибр — это калибр, воспроизводящий проходной и (или) непроходной пределы геометрических параметров элементов изделия. Предельные калибры предназначены для контроля деталей с точностью от IT6 по ITM и позволяют установить, находится ли проверяемый размер в пределах допуска.
Предельные калибры для отверстий и валов подразделяют на проходной калибр (ПР), контролирующий предел максимума материала, и непроходной (НЕ), контролирующий предел минимума материала.
По назначению калибры подразделяются следующим образом:
- рабочие калибры (Р-ПР, Р-НЕ) пробки и скобы, применяемые для контроля деталей при их изготовлении;
- контрольные калибры (контркалибры), предназначенные для контроля размеров рабочих калибров-скоб проходных (К-ПР) и непроходных (К-НЕ) в процессе их изготовления, а также для контроля износа (К-И) проходных рабочих калибров-скоб при их эксплуатации (они являются непроходными).
Для контроля гладких цилиндрических отверстий предназначены ка-либры-пробки (рис. 10.15), для валов — калибры-скобы (рис. 10.16), состоящие из проходной (ПР) и непроходной (НЕ) сторон.
Деталь считают годной, если проходной калибр под действием собственной массы проходит, а непроходной калибр не проходит по контролируемой поверхности детали.
Для контроля отверстий номинальных размеров свыше 100 мм изготовляют неполные калибры-пробки (рис. 10.15, б). Чаще всего полные пробки делают двусторонними (рис. 10.15, а), а неполные — односторонними (см. рис. 10.15, б).
Если проходной калибр не проходит, брак детали является исправимым, если непроходной калибр проходит — брак неисправим.
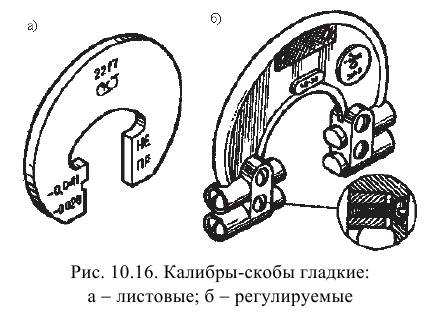
Калибры-скобы бывают жесткие листовые и регулируемые. На инструментальных заводах чаще всего изготовляют регулируемые скобы с литым или штампованным корпусом, со вставками, переставляемыми на разные номинальные размеры по блокам КМД.
Допуски гладких предельных калибров
Номинальным размером проходной пробки является минимальный предельный размер контролируемого отверстия , проходной скобы -максимальный предельный размер контролируемого вала
.
Номинальным размером непроходной пробки является максимальный размер контролируемого отверстия , непроходной скобы — минимальный размер вала
.
Предельные отклонения калибров отсчитываются от соответствующих номинальных размеров, т.е. от предельных размеров контролируемых деталей. Для проходных калибров, износ которых вызывает искажение характера посадки, устанавливается также граница допустимого износа.
При назначении предельных отклонений калибров для отверстий и валов с размерами свыше 180 мм учитывается компенсация погрешностей контроля, вызываемых упругими деформациями калибров и деталей.
На схемах полей допусков (рис. 10.17 и 10.18) и в формулах для определения размеров калибров приняты следующие обозначения:
— предельные размеры отверстия;
— предельные размеры вала;
— допуск на изготовление калибра-пробки;
— допуск на изготовление калибра-скобы;
— допуск контрольных калибров для скоб;
— допуск калибров со сферическими измерительными поверхностями;
— отклонение середины поля допуска на изготовление проходного калибра-пробки относительно
;
— отклонение середины поля допуска на изготовление проходного калибра-скобы относительно
;
— допустимый выход изношенного проходного калибра-пробки за границу поля допуска отверстия, начиная с
;
— допустимый выход изношенного калибра-скобы за границу поля допуска вала, начиная с
;
и
— величина для компенсации погрешности контроля калибрами соответственно отверстий и валов с размерами свыше 180 мм.
Формулы для расчета предельных размеров рабочих и контрольных калибров приведены ниже.
Рабочие калибры-пробки:
Рабочие калибры-скобы:
Контрольные калибры:
В приведённых формулах значения и
нужно прибавить или отпять, т.е. просто убрать скобки.
При размерах до 180 мм (см. рис. 10.17) для проходных калибров, контролирующих отверстия и валы 6, 7 и 8 квалитетов, допускается выход размера изношенного калибра за поле допуска изделия на величину соответственно или
. Для изделий от 9 до 18 квалитетов граница износа проходных калибров совпадает с пределом максимума материала изделия
.
При размерах свыше 180 мм (см. рис. 10.18) поле допуска непроходного калибра и граница износа проходного калибра смещаются внутрь поля допуска изделия на величину, учитывающую погрешность контроля калибрами ( и
).
Маркировка калибров
При маркировке на калибр наносятся номинальный размер с буквенным обозначением поля допуска контролируемой детали, цифровые значения предельных отклонений детали в миллиметрах, тип калибра (например: ПР, НЕ, К И) и товарный знак завода изготовителя (рис. 10.19).
Размер калибра, проставленный на его чертеже, называется исполнительным. В качестве исполнительного размера калибра-пробки принимается её наибольший предельный размер с отрицательным нижним отклонением, равным допуску на изготовление, а скобы — её наименьший предельный размер с положительным верхним отклонением, равным допуску на изготовление.
Числовые значения допусков и отклонений калибров выбираются по табл. 10.6 в зависимости от квалитета и номинального размера контролируемого изделия.
Координатные измерительные машины
Координатными измерительными машинами (КИМ) называют автоматические средства для определения линейных и угловых размеров, а также отклонений формы и расположения поверхностей и осей сложных корпусных деталей.
КИМ позволяет осуществлять перечисленные виды измерений в двух, трех и четырех координатах: и
(рис. 10.20, а);
(рис. 10.20, 6);
плюс поворот на угол
в плоскости
(рис. 10.20, в).
Работают машины в двух режимах: либо осуществляется перемещение измерительного наконечника до контакта с измеряемой поверхностью, и с помощью отсчетных устройств определяется ее положение в системе координат, либо измерительный наконечник по заданной программе перемещается в точки, соответствующие номинальным значениям определяемых размеров, а отсчетные устройства позволяют оценить отклонения положения действительных поверхностей от номинального значения. Чаще КИМ работают в первом режиме.
Основными узлами машин являются направляющие, по которым перемещается измерительная каретка с наконечником, отсчетные и счетно-решающие системы. Для уменьшения погрешности измерения КИМ снабжены либо направляющими качения, либо аэростатическими (на воздушной подушке) направляющими. Аэростатические направляющие высокоточных машин иногда изготовляют из твердых каменных пород, не подверженных (в отличие от металлических) температурным деформациям.
В качестве отсчетных устройств в КИМ используют специальные устройства — индуктосины. Они представляют собой электрическую машину со статором, развернутым в виде линейки, на поверхность которой печатным способом нанесены обмотки. Для этих же целей могут применяться и растровые фотоэлектрические преобразователи.
Современные КИМ оснащены ЭВМ, осуществляющими обработку результатов измерений, пересчет полученных значений размеров в зависимости от положения произвольно расположенной на столе машины контролируемой детали, печатание результатов измерений с указанием действительных значений измеренных параметров или их отклонений от заданных и их цифровую индикацию на специальных табло. Кроме того, ЭВМ руководит перемещениями каретки с измерительным наконечником, обеспечивая его последовательное автоматическое касание всех поверхностей, подлежащих контролю.
Раньше эта операция осуществлялась в соответствии с предварительно составленной программой (для каждого типоразмера деталей), введенной в ЭВМ. Существенным недостатком такого метода является необходимость затрачивать время на написание программы, ее запись на программоноситель и отладку, что требует привлечения к процессам измерения программистов.
Современные конструкции машин позволяют оператору без программы быстро «обучить» машину выполнять измерения интересующих параметров конкретной детали. Для этого надо вручную переместить каретку с измерительным наконечником, касаясь этим наконечником поверхностей, подлежащих контролю. Машина запоминает эти движения и сама записывает их в виде управляющей программы, которую потом использует для измерения аналогичных деталей. При необходимости эта программа заносится в память машины и может быть использована в любое время. КИМ находят также широкое применение при разметке корпусных деталей.
Координатная измерительная машина ВЕ-111 (рис. 10.20, в) позволяет проводить измерения и разметку по четырем координатам. Измеряемую деталь 4 устанавливают на самоустанавливающихся домкратах 5 стола 6, осуществляющего поворот детали вокруг вертикальной оси. Устройство 3 измерительным наконечником или разметочной головкой перемещается по осям и
с помощью каретки 2, которая поднимается и опускается по направляющим колонки 1. На каретке имеются направляющие, обеспечивающие перемещение штанги с устройством 3 в горизонтальном направлении по оси
. Для измерений по оси
вся колонка перемещается по направляющим основания 7. Перемещение каретки 2 по оси
осуществляется вручную, а по осям
и
— с помощью электродвигателя.
Результаты измерений по четырем координатам считывают с цифрового отсчетного устройства 9 ЭВМ или печатаются на бумажной ленте принтера 8. Данная машина обеспечивает возможность измерения и разметки деталей размером до 750 х 460 х 630 мм.
Существующие модели координатных измерительных машин позволяют измерять и размечать детали размерами от 400…500 мм до 10… 16 м. Наибольшее распространение получили машины для измерения деталей размером не более 500… 1000 мм.
Для заполнения таблицы выберите отклонения из списка выше
ГОСТ 25346-2013 отражает общие положения Единой системы допусков и посадок
(ЕСДП), термины, ряды допусков и основных отклонений размеров, правила образования полей допусков
и посадок, условные обозначения основных отклонений и посадок для гладких элементов деталей, образующих
соединения, а так же для свободных размеров деталей.
Взаимозаменяемость – свойство частей изделия, создающее возможность их
нормальной сборки и замены при эксплуатации и ремонте с соблюдением требуемых качеств работ изделия.
Для обеспечения взаимозаменяемости в первую очередь нужно выдержать геометрические параметры изделия (размеры).
В процессе изготовления действительные размеры детали отличаются от заданных на величину погрешности.
Точность – степень приближения действительных размеров к заданным. Размеры бывают свободными и сопряженными.
ГОСТ 25347-2013 распространяется на гладкие элементы деталей с
номинальными размерами до 3150 мм и устанавливает поля допусков для этих элементов.
Данный ГОСТ приводит выборочные числовые значения предельных отклонений
отверстий и валов. Что соответствует ISO 286-2:2010. Поля допусков отраженные в ГОСТ 25347-2013
являются полями допусков для общего применения. Разнообразие полей допусков в ГОСТ 25346-2013 выше.
Числовые значения
предельных отклонений отверстий и валов для размеров свыше 3150 мм до 10000 мм
приведены в ГОСТ 25348-82.
Числовые значения
предельных отклонений отверстий и валов изделий из пластмасс для размеров до 3150 мм
приведены в ГОСТ 25349-88.
Система допусков ИСО на линейные размеры распространяется на цилиндры и
две параллельные противолежащие плоскости.
Термины «отверстие» и «вал» применяют для описания как размерного элемента —
цилиндра (например, при установлении допуска диаметра отверстия или вала), так и для двух
параллельных противолежащих плоскостей (например, при установлении допуска на толщину шпонки или
ширину шлицевого паза).
Отверстие – внутренний размерный элемент детали
(включая внутренние размерные элементы, не являющиеся цилиндрическими).
Вал – наружный размерный элемент детали
(включая наружные размерные элементы, не являющиеся цилиндрическими).
Номинальный размер – размер геометрического
элемента идеальной формы, определенной чертежом.
Предельный размер – предельно допустимый
размер размерного элемента.
Действительный размер – размер полученный в
результате измерений.
Допуск – разность между верхним и нижним предельными размерами. Это абсолютная величина – не имеет знака.
Квалитет – группа допусков на линейные размеры,
характеризующаяся общим обозначением. (обозначается цифрами 01 0 1 2 3 4 5 6 7 8 9 10
11 12 13 14 15 16 17 18)
Области ориентировочного применения квалитетов:
– 4 и 5 применяются сравнительно редко в особо точных соединениях (посадки приборных подшипников, высокоточных зубчатых колес)
– 6 и 7 применяются для ответственных соединений (посадки подшипников качения нормальной точности, зубчатых колес высокой и
средней точности, подшипников скольжения и др.)
– 8 и 9 применяются для посадок с меньшими требованиями к однородности зазоров или натягов, обеспечивающих среднюю точность сборки и
компенсирующих погрешности формы и расположения сопрягаемых деталей
– 10 применяется для посадок с более грубыми требованиями, чем для 8 и 9 квалитетов
– 11 и 12 применяются в соединениях с большими зазорами (крышки, фланцы, дистанционные кольца и др.)
Основное отклонение – предельное отклонение, определяющее
расположение интервала допуска относительно номинального размера. (обозначается буквами латинского алфавита)
Для отверстий: A, B, C, CD, D, E, EF, F, FG, G, H – для образования посадок с зазором.
Для отверстий: J, JS, K, M, N – для образования переходных посадок.
Для отверстий: P, R, S, T, U, V, X, Y, Z, ZA, ZB, ZC – для образования посадок с натягом.
Для валов: a, b, c, cd, d, e, ef, f, fg, g, h – для образования посадок с зазором.
Для валов: j, js, k, m, n – для образования переходных посадок.
Для валов: p, r, s, t, u, v, x, y, z, za, zb, zc – для образования посадок с натягом.
Основные отклонения отверстий и валов являются зеркальным отображением друг друга.
Исключения составляют J, K, M, N, P, R, S, j, k, m, n, p, r, s.
Класс допуска – сочетание основного отклонения и квалитета.
Предпочтительные классы допуска отверстий: A11, B11, C10, C11, D9, D10, D11, E8, E9,
E10, F7, F8, F9, G6, G7, H6, H7, H8, H9, H10, H11, JS6, JS7, JS8, K6, K7, K8, M6, M7, M8, N6, N7, N8, P6,
P7, P8, R6, R7, R8, S6, S7, T6, T7, U7, X7.
Предпочтительные классы допуска валов: a11, b9, b11, c9, c11, d8, d9, d10, e7, e8, e9, f6, f7 ,f8,
g5, g6, h5, h6, h7, h8, h9, h10, h11, js5, js6, js7, k5, k6, k7, m5, m6, m7, n5, n6, n7, p5, p6, p7,
r5, r6, r7, s5, s6, s7, t5, t6, t7, u6, u7, x6.
Зазор – разность между размерами отверстия и вала,
когда диаметр вала меньше диаметра отверстия.
Натяг – разность размеров отверстия и вала до сборки,
когда диаметр вала больше диаметра отверстия.
Переходная посадка – посадка, при которой в соединении отверстия
и вала возможно получение как зазора, так и натяга.
Посадка в системе отверстия – посадка, в которой основное
отклонение (нижнее предельное отклонение) отверстия равно нулю.
Посадка в системе вала – посадка, в которой основное
отклонение (верхнее предельное отклонение) вала равно нулю.
Пример посадки
Ø32 H7/k6,
где Ø32 – размер элемента изделия (может быть и не диаметр);
H7 – поле допуска по ЕСДП для отверстия;
k6 – поле допуска по ЕСДП для вала.
поле допуска вала по ОСТ | поле допуска вала по ЕСДП | поле допуска отверстия по ОСТ | поле допуска отверстия по ЕСДП |
---|---|---|---|
С1 вал = B1 | h5 | С1 отв. = А1 | H6 |
С вал = B | h6 | С отв. = А | H7 |
С2а вал = B2а | h7 | С2а отв. = А2а | H8 |
С3 вал = B3 | h8(h9) | С3 отв. = А3 | H8(H9) |
С3а вал = B3а | h10 | С3а отв. = А3а | H10 |
С4 вал = B4 | h11 | С4 отв. = А4 | H11 |
С5 вал = B5 | h12 | С5 отв. = А5 | H12 |
С7 вал = B7 | h14 | С7 отв. = А7 | H14 |
С8 вал = B8 | h15 | С8 отв. = А8 | H15 |
С9 вал = B9 | h16 | С9 отв. = А9 | H16 |
СМ7 вал | js14 | СМ7 отв. | JS14 |
СМ8 вал | js15 | СМ8 отв. | JS15 |
СМ9 вал | js16 | СМ9 отв. | JS16 |
Г1 вал | n5 | Г1 отв. | N6 |
Г вал | n6 | Г отв. | N7 |
Г2а вал | n7 | Г2а отв. | N8 |
Гр вал | u7 | Гр отв. | U7(U8) |
Д1 вал | g5 | Д1 отв. | G6 |
Д вал | g6 | Д отв. | G7 |
Л1 вал | e8 | Л1 отв. | E8 |
Л4 вал | b11 | Л4 отв. | B11 |
Н1 вал | k5 | Н1 отв. | K6 |
Н вал | k6 | Н отв. | K7 |
Н2а вал | k7 | Н2а отв. | K8 |
П1 вал | j5(js5) | П1 отв. | J6(JS6) |
П вал | j6(js6) | П отв. | J7(JS7) |
П2а вал | j7(js7) | П2а отв. | J8(JS8) |
Пр отв. | R7 | ||
Пр11 вал | r5 | ||
Пр12а вал | s7 | ||
Пр21 вал | s5 | ||
Пр22а вал | u8 | Пр22а отв. | U8 |
Т1 вал | m5 | Т1 отв. | M6 |
Т вал | m6 | Т отв. | M7 |
Т2а вал | m7 | Т2а отв. | M8 |
Х1 вал | f6 | Х1 отв. | F6 |
Х вал | f7 | Х отв. | F8 |
Х2а вал | f8 | ||
Х3 вал | f9(e9) | Х3 отв. | F9(E9) |
Х4 вал | d11 | Х4 отв. | D11 |
Х5 вал | b12 | Х5 отв. | B12 |
Ш вал | d8 | Ш отв. | D8 |
Ш3 вал | d9(d10) | Ш3 отв. | D9(D10) |
Ш4 вал | a11 | Ш4 отв. | A11 |
ТХ вал | c8 |
Частные посадки в машиностроении
- Венец шестерни (червячного колеса) – H7/s7 (натяг)
- Манжета резиновая армированная для валов – h10/L0, l0/H9
- Подшипник при вращающемся вале (основные посадки в машиностроении) – k6/L0, l0/H7
- Подшипник при вращающемся корпусе (основные посадки в машиностроении) – h6/L0, l0/M7
- Штифты по ГОСТ 24296-93 – H7/m6
- Шпонка (свободная посадка) – H9/l0 (для вала), D10/l0 (для втулки)
- Шпонка (нормальная посадка) – N9/l0 (для вала), JS9/l0 (для втулки)
- Шпонка (плотная посадка) – P9/l0 (для вала), P9/l0 (для втулки)
Допуски и посадки отверстий и валов в машиностроении.
В машиностроении применяется единая система допусков и посадок (ЕСДП). Поскольку наш каталог предназначен для технических работников и специалистов, уже имеющих общее представление о металлообработке, мы не будем начинать с азов и разъяснения общих терминов.
Приводим самый необходимый материал – сводную таблицу допусков и посадок отверстий и валов, называемую также квалитетом, в зависимости от интервала размеров. По нашему мнению именно эта информация должна быть под рукой при чтении чертежей и изготовлении деталей, в том числе и для редукторов.
Там же приведено соответствие устаревших обозначений допусков по ОСТ, встречающихся в некоторых чертежах, современным стандартам по ГОСТ 25346-89, ГОСТ 25347-82, ГОСТ 25348-89.
Предельные отклонения размеров (допуски и посадки) отверстий и валов, мкм.
Ближайшее поле допуска по ОСТ | Поля допусков отверстий и валов | Интервал размеров отверстий и валов, мм | |||||||||
От 1 до 3 включительно | Свыше 3 до 6 включительно | Свыше 6 до 10 включительно | Свыше 10 до 14 включительно | Свыше 14 до 18 включительно | |||||||
Д | g6 | -2 | -8 | -4 | -12 | -5 | -14 | -6 | -17 | -6 | -17 |
С | h6 | 0 | -6 | 0 | -8 | 0 | -9 | 0 | -11 | 0 | -11 |
П | js6 | 3 | -3 | 4 | -4 | 4,5 | -4,5 | 5,5 | -5,5 | 5,5 | -5,5 |
Н | k6 | 6 | 0 | 9 | 1 | 10 | 1 | 12 | 1 | 12 | 1 |
Т | m6 | 8 | 2 | 12 | 4 | 15 | 6 | 18 | 7 | 18 | 7 |
Г | n6 | 10 | 4 | 16 | 8 | 19 | 10 | 23 | 12 | 23 | 12 |
Пл | p6 | 12 | 6 | 20 | 12 | 24 | 15 | 29 | 18 | 29 | 18 |
Пр | r6 | 16 | 10 | 23 | 15 | 28 | 19 | 24 | 23 | 24 | 23 |
s6 | – | – | – | – | – | ||||||
А | H7 | 10 | 0 | 12 | 0 | 15 | 0 | 18 | 0 | 18 | 0 |
Х | f7 | -6 | -16 | -10 | -22 | -13 | -28 | -16 | -34 | -16 | -34 |
П2а | js7 | 5 | -5 | 6 | -6 | 7 | -7 | 9 | -9 | 9 | -9 |
Пр12а | s7 | 24 | 14 | 31 | 19 | 38 | 23 | 46 | 28 | 46 | 28 |
А2а | H8 | 14 | 0 | 18 | 0 | 22 | 0 | 27 | 0 | 27 | 0 |
Ш | d8 | -20 | -34 | -30 | -48 | -40 | -62 | -50 | -77 | -50 | -77 |
Л | e8 | -14 | -28 | -20 | -38 | -25 | -47 | -32 | -59 | -32 | -59 |
С3 | h8 | 0 | -14 | 0 | -18 | 0 | -22 | 0 | -27 | 0 | -27 |
Пр22а | u8 | 32 | 18 | 41 | 23 | 50 | 28 | 60 | 33 | 60 | 33 |
А3 | H9 | 25 | 0 | 30 | 0 | 36 | 0 | 43 | 0 | 43 | 0 |
Ш3 | d9 | -20 | -45 | -30 | -60 | -40 | -76 | -50 | -93 | -50 | -93 |
Х3 | f9 | -6 | -31 | -10 | -40 | -13 | -49 | -16 | -59 | -16 | -59 |
А4 | H11 | 60 | 0 | 75 | 0 | 90 | 0 | 110 | 0 | 110 | 0 |
Ш4 | a11 | -270 | -330 | -270 | -345 | -280 | -370 | -290 | -400 | -290 | -400 |
Л4 | b11 | – | – | – | – | – | |||||
c11 | -60 | -120 | -70 | -145 | -80 | -170 | -95 | -205 | -95 | -205 | |
Х4 | d11 | -20 | -80 | -30 | -105 | -40 | -130 | -50 | -160 | -50 | -160 |
С4 | h11 | 0 | -60 | 0 | -75 | 0 | -90 | 0 | -110 | 0 | -110 |
А5 | H12 | 100 | 0 | 120 | 0 | 150 | 0 | 180 | 0 | 180 | 0 |
Ч5 | b12 | -140 | -240 | -140 | -260 | -150 | -300 | -150 | -330 | -150 | -330 |
С5 | h12 | 0 | -100 | 0 | -120 | 0 | -150 | 0 | -180 | 0 | -180 |
А7 | H14 | 250 | 0 | 300 | 0 | 360 | 0 | 430 | 0 | 430 | 0 |
В7 | h14 | 0 | -250 | 0 | -300 | 0 | -360 | 0 | -430 | 0 | -430 |
СМ7 | js14 | 125 | -125 | 150 | -150 | 180 | -180 | 215 | -215 | 215 | -215 |
продолжение таблицы
Ближайшее поле допуска по ОСТ | Поля допусков отверстий и валов | Интервал размеров отверстий и валов, мкм | |||||||||
Свыше 18 до 24 включительно | Свыше 24 до 30 включительно | Свыше 30 до 40 включительно | Свыше 40 до 50 включительно | Свыше 50 до 65 включительно | |||||||
Д | g6 | -7 | -20 | -7 | -20 | -9 | -25 | -9 | -25 | -10 | -29 |
С | h6 | 0 | -13 | 0 | -13 | 0 | -16 | 0 | -16 | 0 | -19 |
П | js6 | 6,5 | -6,5 | 6,5 | -6,5 | 8 | -8 | 8 | -8 | 9,5 | -9,5 |
Н | k6 | 15 | 2 | 15 | 2 | 18 | 2 | 18 | 2 | 21 | 2 |
Т | m6 | 20 | 8 | 20 | 8 | 25 | 9 | 25 | 9 | 30 | 10 |
Г | n6 | 28 | 15 | 28 | 15 | 33 | 17 | 33 | 17 | 39 | 20 |
Пл | p6 | 35 | 22 | 35 | 22 | 42 | 26 | 42 | 26 | 51 | 32 |
Пр | r6 | 41 | 28 | 41 | 28 | 50 | 34 | 50 | 34 | 60 | 41 |
s6 | – | – | – | ||||||||
А | H7 | 21 | 0 | 21 | 0 | 25 | 0 | 25 | 0 | 30 | 0 |
Х | f7 | -20 | -41 | -20 | -41 | -25 | -50 | -25 | -50 | -30 | -60 |
П2а | js7 | 10 | -10 | 10 | -10 | 12 | -12 | 12 | -12 | 15 | -15 |
Пр12а | s7 | 56 | 35 | 56 | 35 | 68 | 43 | 68 | 43 | 83 | 53 |
А2а | H8 | 33 | 0 | 33 | 0 | 39 | 0 | 39 | 0 | 46 | 0 |
Ш | d8 | -65 | -98 | -65 | -98 | -80 | -119 | -80 | -119 | -100 | -146 |
Л | e8 | -40 | -73 | -40 | -73 | -50 | -89 | -50 | -89 | -60 | -106 |
С3 | h8 | 0 | -33 | 0 | -33 | 0 | -39 | 0 | -39 | 0 | -46 |
Пр22а | u8 | 74 | 41 | 81 | 48 | 99 | 60 | 109 | 70 | 133 | 37 |
А3 | H9 | 52 | 0 | 52 | 0 | 62 | 0 | 62 | 0 | 74 | 0 |
Ш3 | d9 | -65 | -117 | -65 | -117 | -80 | -142 | -80 | -142 | -100 | -174 |
Х3 | f9 | -20 | -72 | -20 | -72 | -25 | -87 | -25 | -87 | -30 | -104 |
А4 | H11 | 130 | 0 | 130 | 0 | 160 | 0 | 160 | 0 | 190 | 0 |
Ш4 | a11 | -300 | -430 | -300 | -430 | -310 | -470 | -320 | -480 | -340 | -530 |
Л4 | b11 | – | -170 | -330 | -180 | -340 | -190 | -380 | |||
c11 | -110 | -240 | -110 | -240 | – | ||||||
Х4 | d11 | -65 | -195 | -65 | -195 | -80 | -240 | -80 | -240 | -100 | -290 |
С4 | h11 | 0 | -130 | 0 | -130 | 0 | -160 | 0 | -160 | 0 | -190 |
А5 | H12 | 210 | 0 | 210 | 0 | 250 | 0 | 250 | 0 | 300 | 0 |
Ч5 | b12 | -160 | -370 | -160 | -370 | -170 | -420 | -180 | -430 | -190 | -490 |
С5 | h12 | 0 | -210 | 0 | -210 | 0 | -250 | 0 | -250 | 0 | -300 |
А7 | H14 | 520 | 0 | 520 | 0 | 620 | 0 | 620 | 0 | 740 | 0 |
В7 | h14 | 0 | -520 | 0 | -520 | 0 | -620 | 0 | -620 | 0 | -740 |
СМ7 | js14 | 260 | -260 | 260 | -260 | 310 | -310 | 310 | -310 | 370 | -370 |
продолжение таблицы
Ближайшее поле допуска по ОСТ | Поля допусков отверстий и валов | Интервал размеров отверстий и валов, мкм | |||||||||
Свыше 65 до 80 включительно | Свыше 80 до 100 включительно | Свыше 100 до 120 включительно | Свыше 120 до140 включительно | Свыше 140 до 160 включительно | |||||||
Д | g6 | -10 | -29 | -12 | -34 | -12 | -34 | -14 | -39 | -14 | -39 |
С | h6 | 0 | -19 | 0 | -22 | 0 | -22 | 0 | -25 | 0 | -25 |
П | js6 | 9,5 | -9,5 | 11 | -11 | 11 | -11 | 12,5 | -12,5 | 12,5 | -12,5 |
Н | k6 | 21 | 2 | 25 | 3 | 25 | 3 | 28 | 3 | 28 | 3 |
Т | m6 | 30 | 10 | 35 | 13 | 35 | 13 | 40 | 15 | 40 | 15 |
Г | n6 | 39 | 20 | 45 | 23 | 45 | 23 | 52 | 27 | 52 | 27 |
Пл | p6 | 51 | 32 | 59 | 37 | 59 | 37 | 68 | 43 | 68 | 43 |
Пр | r6 | 62 | 43 | 73 | 51 | 76 | 54 | – | |||
s6 | 93 | 71 | 101 | 79 | 117 | 92 | 125 | 100 | |||
А | H7 | 30 | 0 | 35 | 0 | 35 | 0 | 40 | 0 | 40 | 0 |
Х | f7 | -30 | -60 | -36 | -71 | -36 | -71 | -43 | -83 | -43 | -83 |
П2а | js7 | 15 | -15 | 17 | -17 | 17 | -17 | 20 | -20 | 20 | -20 |
Пр12а | s7 | 89 | 59 | 106 | 71 | 114 | 79 | 132 | 92 | 140 | 100 |
А2а | H8 | 46 | 0 | 54 | 0 | 54 | 0 | 63 | 0 | 63 | 0 |
Ш | d8 | -100 | -146 | -120 | -174 | -120 | -174 | -145 | -208 | -145 | -208 |
Л | e8 | -60 | -106 | -72 | -126 | -72 | -126 | -85 | -148 | -85 | -148 |
С3 | h8 | 0 | -46 | 0 | -54 | 0 | -54 | 0 | -63 | 0 | -63 |
Пр22а | u8 | 148 | 102 | 178 | 124 | 198 | 144 | 233 | 170 | 253 | 190 |
А3 | H9 | 74 | 0 | 87 | 0 | 87 | 0 | 100 | 0 | 100 | 0 |
Ш3 | d9 | -100 | -174 | -120 | -207 | -120 | -207 | -145 | -245 | -145 | -245 |
Х3 | f9 | -30 | -104 | -36 | -123 | -36 | -123 | -43 | -143 | -43 | -143 |
А4 | H11 | 190 | 0 | 220 | 0 | 220 | 0 | 250 | 0 | 250 | 0 |
Ш4 | a11 | -360 | -550 | -380 | -600 | -410 | -630 | -460 | -710 | -520 | -770 |
Л4 | b11 | -200 | -390 | -220 | -440 | -240 | -460 | -260 | -510 | -280 | -530 |
c11 | – | – | |||||||||
Х4 | d11 | -100 | -290 | -120 | -340 | -120 | -340 | -145 | -395 | -145 | -395 |
С4 | h11 | 0 | -190 | 0 | -220 | 0 | -220 | 0 | -250 | 0 | -250 |
А5 | H12 | 300 | 0 | 350 | 0 | 350 | 0 | 400 | 0 | 400 | 0 |
Ч5 | b12 | -200 | -500 | -220 | -570 | -240 | -590 | -260 | -660 | -280 | -680 |
С5 | h12 | 0 | -300 | 0 | -350 | 0 | -350 | 0 | -400 | 0 | -400 |
А7 | H14 | 740 | 0 | 870 | 0 | 870 | 0 | 1000 | 0 | 1000 | 0 |
В7 | h14 | 0 | -740 | 0 | -870 | 0 | -870 | 0 | -1000 | 0 | -1000 |
СМ7 | js14 | 370 | -370 | 435 | -435 | 435 | -435 | 500 | -500 | 500 | -500 |
продолжение таблицы
Ближайшее поле допуска по ОСТ | Поля допусков отверстий и валов | Интервал размеров отверстий и валов, мкм | |||||||||
Свыше 160 до180 включительно | Свыше 180 до 200 включительно | Свыше 200 до 225 включительно | Свыше 225 до 250 включительно | Свыше 250 до 280 включительно | |||||||
Д | g6 | -14 | -39 | -15 | -44 | -15 | -44 | -15 | -44 | -17 | -49 |
С | h6 | 0 | -25 | 0 | -29 | 0 | -29 | 0 | -29 | 0 | -32 |
П | js6 | 12,5 | -12,5 | 14,5 | -14,5 | 14,5 | -14,5 | 14,5 | -14,5 | 16 | -16 |
Н | k6 | 28 | 3 | 33 | 4 | 33 | 4 | 33 | 4 | 36 | 4 |
Т | m6 | 40 | 15 | 46 | 17 | 46 | 17 | 46 | 17 | 52 | 20 |
Г | n6 | 52 | 27 | 60 | 31 | 60 | 31 | 60 | 31 | 66 | 34 |
Пл | p6 | 68 | 43 | 79 | 50 | 79 | 50 | 79 | 50 | 88 | 56 |
Пр | r6 | – | – | – | |||||||
s6 | 133 | 108 | 151 | 122 | 159 | 130 | 169 | 140 | 190 | 158 | |
А | H7 | 40 | 0 | 46 | 0 | 46 | 0 | 46 | 0 | 52 | 0 |
Х | f7 | -43 | -83 | -50 | -96 | -50 | -96 | -50 | -96 | -56 | -108 |
П2а | js7 | 20 | -20 | 23 | -23 | 23 | -23 | 23 | -23 | 26 | -26 |
Пр12а | s7 | 148 | 108 | 168 | 122 | 176 | 130 | 186 | 140 | 210 | 158 |
А2а | H8 | 63 | 0 | 72 | 0 | 72 | 0 | 72 | 0 | 81 | 0 |
Ш | d8 | -145 | -208 | -170 | -242 | -170 | -242 | -170 | -242 | -190 | -271 |
Л | e8 | -85 | -148 | -100 | -172 | -100 | -172 | -100 | -172 | -110 | -191 |
С3 | h8 | 0 | -63 | 0 | -72 | 0 | -72 | 0 | -72 | 0 | -81 |
Пр22а | u8 | 273 | 210 | 308 | 236 | 330 | 258 | 356 | 284 | 396 | 315 |
А3 | H9 | 100 | 0 | 115 | 0 | 115 | 0 | 115 | 0 | 130 | 0 |
Ш3 | d9 | -145 | -245 | -170 | -285 | -170 | -285 | -170 | -285 | -190 | -320 |
Х3 | f9 | -43 | -143 | -50 | -165 | -50 | -165 | -50 | -165 | -56 | -186 |
А4 | H11 | 250 | 0 | 290 | 0 | 290 | 0 | 290 | 0 | 320 | 0 |
Ш4 | a11 | -580 | -830 | -660 | -950 | -740 | -1030 | -820 | -1110 | -920 | -1240 |
Л4 | b11 | -310 | -560 | – | – | ||||||
c11 | – | -240 | -530 | -260 | -550 | -280 | -570 | -300 | -620 | ||
Х4 | d11 | -145 | -395 | -170 | -460 | -170 | -460 | -170 | -460 | -190 | -510 |
С4 | h11 | 0 | -250 | 0 | -290 | 0 | -290 | 0 | -290 | 0 | -320 |
А5 | H12 | 400 | 0 | 460 | 0 | 460 | 0 | 460 | 0 | 520 | 0 |
Ч5 | b12 | -310 | -710 | -340 | -800 | -380 | -840 | -420 | -880 | -480 | -1000 |
С5 | h12 | 0 | -400 | 0 | -460 | 0 | -460 | 0 | -460 | 0 | -520 |
А7 | H14 | 1000 | 0 | 1150 | 0 | 1150 | 0 | 1150 | 0 | 1300 | 0 |
В7 | h14 | 0 | -1000 | 0 | -1150 | 0 | -1150 | 0 | -1150 | 0 | -1300 |
СМ7 | js14 | 500 | -500 | 575 | -575 | 575 | -575 | 575 | -575 | 650 | -650 |
продолжение таблицы
Ближайшее поле допуска по ОСТ | Поля допусков отверстий и валов | Интервал размеров отверстий и валов, мкм | |||||||||
Свыше 280 до 315 включительно | Свыше 315 до 355 включительно | Свыше 355 до 400 включительно | Свыше 400 до 450 включительно | Свыше 450 до 500 включительно | |||||||
Д | g6 | -17 | -49 | -18 | -54 | -18 | -54 | -20 | -60 | -20 | -60 |
С | h6 | 0 | -32 | 0 | -36 | 0 | -36 | 0 | -40 | 0 | -40 |
П | js6 | 16 | -16 | 18 | -18 | 18 | -18 | 20 | -20 | 20 | -20 |
Н | k6 | 36 | 4 | 40 | 4 | 40 | 4 | 45 | 5 | 45 | 5 |
Т | m6 | 52 | 20 | 57 | 21 | 57 | 21 | 63 | 23 | 63 | 23 |
Г | n6 | 66 | 34 | 73 | 37 | 73 | 37 | 80 | 40 | 80 | 40 |
Пл | p6 | 88 | 56 | 98 | 62 | 98 | 62 | 108 | 68 | 108 | 68 |
Пр | r6 | – | |||||||||
s6 | 202 | 170 | 226 | 190 | 244 | 208 | 272 | 232 | 292 | 252 | |
А | H7 | 52 | 0 | 57 | 0 | 57 | 0 | 63 | 0 | 63 | 0 |
Х | f7 | -56 | -108 | -62 | -119 | -62 | -119 | -68 | -131 | -68 | -131 |
П2а | js7 | 26 | -26 | 28 | -28 | 28 | -28 | 31 | -31 | 31 | -31 |
Пр12а | s7 | 222 | 170 | 247 | 190 | 265 | 208 | 295 | 232 | 315 | 252 |
А2а | H8 | 81 | 0 | 89 | 0 | 89 | 0 | 97 | 0 | 97 | 0 |
Ш | d8 | -190 | -271 | -210 | -299 | -210 | -299 | -230 | -327 | -230 | -327 |
Л | e8 | -110 | -191 | -125 | -214 | -125 | -214 | -135 | -232 | -135 | -232 |
С3 | h8 | 0 | -81 | 0 | -89 | 0 | -89 | 0 | -97 | 0 | -97 |
Пр22а | u8 | 431 | 350 | 479 | 390 | 524 | 435 | 587 | 490 | 637 | 540 |
А3 | H9 | 130 | 0 | 140 | 0 | 140 | 0 | 155 | 0 | 155 | 0 |
Ш3 | d9 | -190 | -320 | -210 | -350 | -210 | -350 | -230 | -385 | -230 | -385 |
Х3 | f9 | -56 | -186 | -62 | -202 | -62 | -202 | -68 | -223 | -68 | -223 |
А4 | H11 | 320 | 0 | 360 | 0 | 360 | 0 | 400 | 0 | 400 | 0 |
Ш4 | a11 | -1050 | -1370 | -1200 | -1560 | -1350 | -1710 | -1500 | -1900 | -1650 | -2050 |
Л4 | b11 | – | |||||||||
c11 | -330 | -650 | -360 | -720 | -400 | -760 | -440 | -840 | -480 | -880 | |
Х4 | d11 | -190 | -510 | -210 | -570 | -210 | -570 | -230 | -630 | -230 | -630 |
С4 | h11 | 0 | -320 | 0 | -360 | 0 | -360 | 0 | -400 | 0 | -400 |
А5 | H12 | 520 | 0 | 570 | 0 | 570 | 0 | 630 | 0 | 630 | 0 |
Ч5 | b12 | -540 | -1060 | -600 | -1170 | -680 | -1250 | -760 | -1390 | -840 | -1470 |
С5 | h12 | 0 | -520 | 0 | -570 | 0 | -570 | 0 | -630 | 0 | -630 |
А7 | H14 | 1300 | 0 | 1400 | 0 | 1400 | 0 | 1550 | 0 | 1550 | 0 |
В7 | h14 | 0 | -1300 | 0 | -1400 | 0 | -1400 | 0 | -1550 | 0 | -1550 |
СМ7 | js14 | 650 | -650 | 700 | -700 | 700 | -700 | 775 | -775 | 775 | -775 |