Впервые побывал на производстве.
Это как пережить роды, только процесс вынашивания препарирован!
Вы удивитесь узнав, как много поставщиков участвует в производстве и что многие из них сосредоточены в Калуге!
Полный размер
Более наглядной иллюстрации к скандальному заявлению вице-президента АвтоВАЗа по инжинирингу Х. Грюбеля сложно придумать )
Но мой фаворит, конечно, Борское стекло!
Лобовые стекла с грилем оно поставляет всем отечественным сборкам.
И более полезной опции в автомобиле я себе не представляю!
Вот так выглядит ее изнанка
МитсубиЩи (именно окончание ЩИ звучит наиболее близко к названию марки, произнесенном по-японски) Outlander комплектуется такими стеклами по-умолчанию, с самой простой версии на 16″ дисках!
Попадает остекление на готовый автомобиль по-разному, но клей наносит только японский робот
Интимный момент — кузов совокупляется с ходовой, двигателем и трансмиссией
Сварку кузова так же осуществяют роботы, привезенные с родины бренда
Пол Аутлендера определяется в цехе покраски — из него кузов выходит с первичными половыми признаками V6! ))
Красится автомобиль в сборе. Перед внедрением потрохов двери снимают для персональной сборки и возвращают строго на тот же кузов в конце цикла
Рождение нового Outlander Тут его впервые заводят и отправляют на проверку
Выходной контроль включает:
визуальные и инструментальные тесты света, электрики, ходовой
Затем — тропическая камера с проливным дождем для обнаружения протечек.
И завершает цикл проверок тест-пилот, проезжая 2,5 километра по заводскому, достаточно жесткому, испытательному полигону
Вот откуда на вашем новом автомобиле первые километры! )
Количество экспатов на заводе ПСМА Рус самое высокое по отрасли и они очень ревностно следят за соблюдением технологического процесса и техники безопасности. Так что за Outlander калужской сбоки я спокоен. Mitsubishi — Надежно!
Как создается машина с нуля: Описание всего процесса
Как создается автомобиль – От “А до Я”.
Всем нам известно, что автомобили являются техническими сложными устройствами а также, что они производятся на крупных автопромышленных предприятиях. Но мало кто из нас знает, как происходит весь этот процесс начиная от самого начала создания новой модели и заканчивая выходом ее к потребителю. Ведь прежде чем отправиться в серийный выпуск на конвейер, автомобиль необходимо разработать, спроектировать нужный прототип и потом уже провести инженерные испытания и так далее. На самом деле весь процесс создания нового автомобиля по уровню технической сложности почти-что сравним с той разработкой космической “одиссеи на Марс”. Уважаемые читатели, предлагаем вам ознакомиться (если это интересно) и проследить вместе с нами за полным процессом создания автомобиля, начиная прямо с самого начального пути. Этот как-бы гид был составлен анонимным зарубежным источником, который в настоящее время работает в одной из известных автомобильных компаний. Мы со своей стороны сгруппировали и разделили весь происходящий процесс на пять основных категорий.
Обратите ваше внимание, что весь процесс создания новой модели с нуля и до поступления этой новинки в автосалон в среднем занимает около 72-х месяцев. Какие-то автокомпании умеют делать это быстрее, а какие-то чуть медленнее. Все зависит от сложности разработки и наличия больших инвестиций вложенных в проектирование и в создание нового автомобиля. И еще, обратите внимание на следующее, наш анонимный гид раскрывает для всех нас (вас) определенные секреты завода производителя рассказывая о том, что на самом деле происходит внутри компании при создании и разработке новой модели автомобиля, а не говорит о том обновлении существующего как-бы уже автомобиля (рестайлинге) о котором обычно пишут и рассказывают господа журналисты. И так, приступим к изучению.
1). Подготовка к проектированию новой модели авто
Срок работ: от 0 – до 72 месяцев.
- Исследование внутреннего рынка а также и зарубежных рынков, для определения роли данного продукта и его компонентов в глобальном портфеле компании. Также, определение и разделение этого продукта от аналогичных моделей бренда которые продаются на мировом рынке.
- Определение главных особенностей новой модели, ее преимущества и потенциальные продажи на зарубежных рынках.
- Определение конкурентов и естественно целевых клиентов. Установка ограничения веса автомобиля; планирование экономии топлива и планирование объема производства.
- Аналитическая оценка нового проекта.
- Определение силовых агрегатов, которые будут устанавливаться на новую модель.
- Бюджет проекта, финансирование, ценообразование, инвестиционные идеи.
- Инженерный компьютерный анализ.
- Определение списка поставщиков компонентов.
2). Дизайн модели
Срок работ: от 0 – до 72 месяцев (после исследования рынка).
- Интерьер-эскизы, выбор дизайнерских тем, модели сборки, сбор информации об отзывах на дизайн.
- Разработка внешнего дизайна.
- Внешние цвета кузова, цвета интерьера-салона, выбор материалов отделки интерьера.
- Оценка аэродинамических особенностей кузова.
- Создание концепции для демонстрации на автосалонах.
- Создание испытательного прототипа.
- Инженерные тестирования опытного образца и сбор инженерных отзывов.
3). Инжиниринг
Срок работ: от 0 – до 72 месяцев (одновременно с разработкой дизайна).
- Работы с клиентами, направленные на сбор обратной связи по отзывам о будущей модели. Сбор предложений по улучшению автомобиля.
- Разработка передовых технологий двигателей, разработка коробки передач, производство двигателей, создание электронных систем управления, создание компонентов автомобиля (металлопрокат, создание форм пластиковых элементов автомобиля), внедрение новых тенденций.
- Упаковка, оформление исследования.
- Дизайн кузова и работы по созданию ударопрочности кузова, работы для оптимизации веса машины, отладка для долговечности.
- Создание технологий для уменьшения аэродинамического сопротивления воздуха.
- Дизайн, разработка, настройка и проверка (в лаборатории и на дороге) на выносливость и жесткость кузова.
- Решение вопроса об интегрировании в машину информационно-развлекательных технологий, сидений, систем освещения.
- Тестирование машины: в жаркую погоду, в сильный мороз, а также проверка транспортного средства во влажном климате.
- Краш-тесты.
- Оценки экономии топлива.
- Планирование процесса серийного производства, в том числе и сборочных работ.
- Анализ стоимости компонентов автомобиля и себестоимость производства.
- Подписание договоров с поставщиками сторонних компонентов.
- Сертификация на уровень безопасности и выбросы новой модели.
4). Производство
Срок работ: 36 – 72 месяца.
- Производство или приобретение компонентов кузова.
- Постройка или перенастройка производственных мощностей.
- Производство компонентов дизайна кузова и салона.
- Проверка всех компонентов на совместимость.
- Улучшение качества автомобиля за счет подбора надежных узлов.
- Анализ готовности к запуску производства.
- Найм рабочей силы или перевод существующих сотрудников на новую линию.
- Взаимодействие с поставщиками.
- Запуск серийного производства новой модели. (Как правило, сначала выпускается первая ограниченная партия для оценки будующих объемов производства).
5). Запуск массового производства
Срок работ: 60 – 72 месяца.
- Исследование рынка перед стартом массового производства.
- Определение розничной (рыночной) цены автомобиля.
- Разработка маркетингового продвижения.
- Поставка образцов модели автомобилей дилерам.
- Планы по логистике (массовая поставка автомобилей дилерам).
- Создание рекламных материалов.
- Презентации серийного автомобиля. Дебют машины на мировом авто-шоу.
- Привлечение внимания прессы, социальных сми-медиа, дилеров и аналитиков к данной новинке.
Оцените новость:
- 80
- 1
- 2
- 3
- 4
- 5
Следите за нами в соцсетях
Похожие статьи
Сервисы
Популярные
Советы
Как выпускают машины – анатомия автозавода
Производство автомобилей – процесс сложный и состоит из множества стадий. Рассказываем, из каких именно
Технологии производства автомобилей отличаются в зависимости от их предназначения – спецтехника, гоночные машины и эксклюзивные суперкары собираются на небольших специализированных фабриках. А серийный выпуск можно наладить только на полноценном заводе. Как он устроен?
Что такое CKD и SKD
Некоторые автолюбители наверняка слышали термин «отверточная сборка», когда с импортируемых машин снимали, к примеру, бамперы и колеса, перевозили через границу, а затем «на заводе» все прикручивали обратно. Это – крупноузловая сборка, SKD (Semi Knocked Down, «полуразобранный»).
Способ был популярным в России в первой декаде нынешнего века для снижения таможенных платежей, но впоследствии регулирующими органами был определен порядок «промышленной сборки» на территории страны. Введены ограничения на возможность ввоза компонентов для производства автомобилей с нулевой пошлиной.
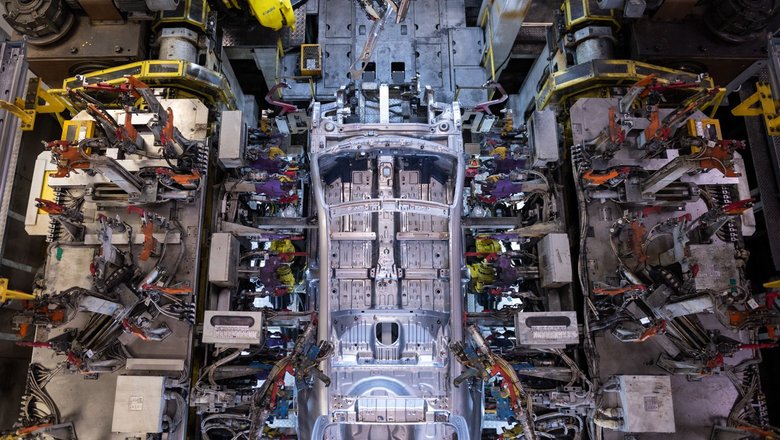
Эти меры вынудили автопроизводителей вкладываться в создание предприятий для выпуска машин по технологии (CKD – Completely Knocked Down, «полностью разобранный»). И их уже можно назвать полноценными автозаводами!
Все начинается с металла
Любой крупный автозавод работающий по полному производственному циклу имеет в своем составе цех штамповки кузовных деталей. Листовой металл на российские предприятия, в основном, поставляет «Северсталь», причем у каждого из автопроизводителей есть свои требования по его прочности и другим характеристикам – в частности, сталь должна быть оцинкованной.
Дальше из металла специальными и очень мощными прессами штампуются кузовные детали. Пресс-формы стоят дорого, поэтому многие автопроизводители уже отказались от выпуска, например, трехдверных хэтчбеков – спрос на них ниже, чем на пятидверные, а боковина кузова требует отдельного штампа.
Некоторые компании (например, Haval) штампуют на своем российском заводе не все детали – панели пола приходят из Китая. Процесс этот автоматизирован и закрыт от глаз, поэтому в цехах штамповки обычно смотреть не на что – только раздается приглушенный грохот из недр прессов.
Собираем кузов
Следующий этап – сварка. Это едва ли не самый эффектный и зрелищный процесс в создании автомобиля. Со склада или цеха штамповки привозят детали, а дальше специальный конвейер в определенном порядке доставляет их на участки сварки, где одни огромные металлические роботизированные «руки» легко подхватывают нужные «железки», а другие – сваривают их между собой со снопами искр.
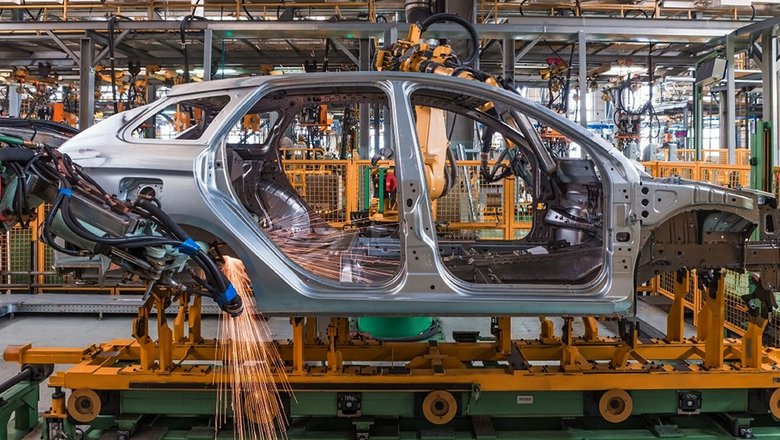
Ручная сварка на современных заводах используется только для совсем простых операций, поэтому вероятность брака минимальна. Кроме того, сварочные линии – достаточно гибкие, что позволяет производить кузова сразу для нескольких моделей.
Антикоррозионная обработка и окраска
После сварки на кузов навешиваются подвижные элементы – двери, капот, крышка багажника. Дальше будущий автомобиль отправляется в окрасочный цех – здесь также все процессы автоматизированы. Сначала остов погружается в специальную ванну для нанесения антикоррозийного покрытия.
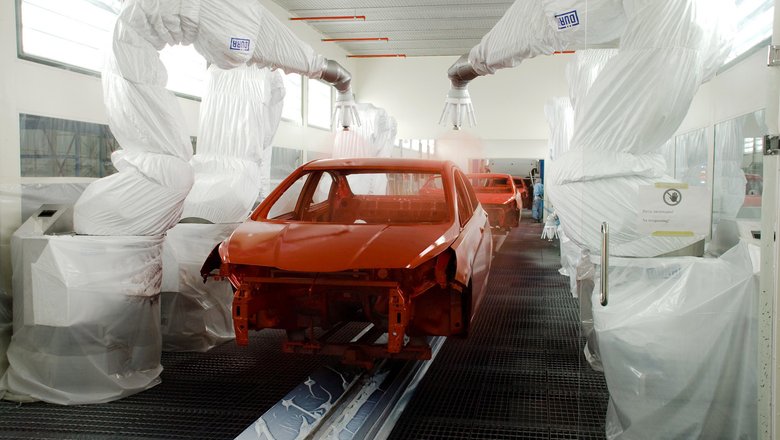
Затем наносятся грунт, основа и лак – например, на заводе в Ижевске, где выпускают автомобили Lada Vesta, на окрасочной линии используется 16 роботов. Производительность линии – 30 кузовов в час, а весь цикл окраски занимает 9,5 часов.
Сборка автомобиля
Окрашенный кузов «переезжает» в сборочный цех. И, пока он медленно едет по конвейеру, к нему прикручивают все недостающие детали. Монтируется передняя панель в сборе (как правило, для этого используется специальный манипулятор), оптика, вклеиваются стекла.
А самое главное событие (его даже называют «свадьбой») – это соединение кузова и ходовой части. На специальной тележке смонтированы двигатель, трансмиссия, передняя и задняя подвески. И в строго определенный момент «низ» начинает подниматься, после чего сборщики фиксируют детали на своих местах.
Наконец, устанавливаются недостающие детали интерьера, сиденья, колеса, в автомобиль заливаются технические жидкости – антифриз, бензин, масло, «тормозуха». А лист со специальными кодами, прикрепленный к каждой машине, позволяет свериться, действительно ли он оказался в нужной комплектации и нужного цвета – это контролируется на каждом участке сборки. Но и это еще не все!
Тестовый участок
Каждый собранный автомобиль попадает на тестовый участок, где регулируется свет фар, регулируются правильные углы установки колес, проводятся испытания на беговых барабанах, чтобы исключить неправильную работу тормозной системы. В специальной «водяной» камере проверяют герметичность уплотнителей.
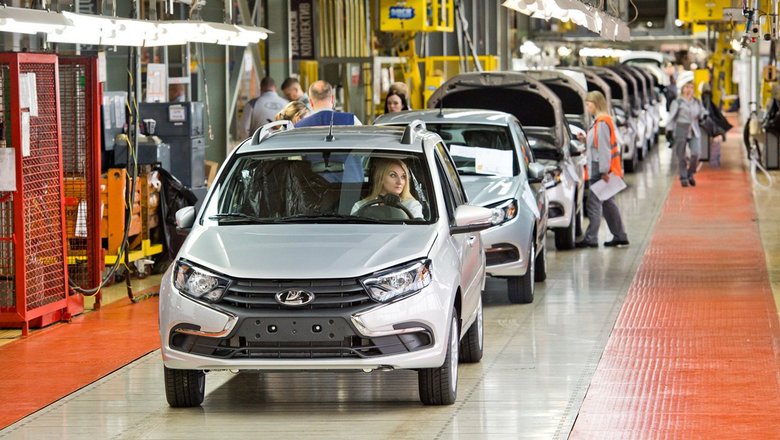
Дальше контролеры проводят осмотр автомобиля и либо ставят специальную отметку о его годности к отгрузке, либо отправляют машину на устранение недостатков. Финальный штрих – ходовые испытания: водители проезжают специальный маршрут, где имитируются разные дорожные условия: брусчатка, «лежачие полицейские» и так далее. И только после этого новоиспеченный автомобиль отправляется на площадку готовой продукции.
Откуда берутся другие детали?
Крупные предприятия включают в себя заводы, которые производят двигатели и элементы трансмиссии. Имеются и цеха пластмассовых изделий. Но это требует огромных энергетических мощностей и приличных размеров территорию. Если такой возможности нет, или бизнес-процессы выстроены иначе, то большую часть деталей поставляют сторонние поставщики.
Например, в рамках автозавода не произведешь шины, различные электронные блоки и экраны, у сторонних поставщиков заказывают сиденья, электропроводку и многие другие элементы. Причем для снижения издержек больших складских запасов не держат – все привозят в соответствии с логистической концепцией «точно в срок» (Just in Time), когда поставка комплектующих идет в соответствии с производственным планом: в определенном количестве, в определенное время и определенное место.
Читайте также
- Топ товаров «АлиЭкспресс» для здоровья авто и его владельца
- Компас автопутешествий: куда поехать на машине?
- «Упрощенная» Lada Granta Classic’22: все подробности
- Lynk & Co представила концепт с четырьмя дверями «крылья бабочки»
- От каких опций и оборудования водители не готовы отказаться?
Как изготавливают автомобили
Производство автомобилей представляет собой сложный и многоплановый процесс. Сначала автомобильный завод производит различные детали и узлы, затем роботизированные системы осуществляют сборку автомобилей. Кроме того, важным этапом является изготовление комплектующих изделий. Только четкая и слаженная работа позволяет массово производить современные автомобили.
Инструкция
Процесс выпуска автомобиля начинается с изготовления деталей кузова на автозаводе. Каждая из них собирается в несколько приемов, после чего они становятся основой так называемых подсборок (основания кузова, боковин и т.д.) – частей кузова. Всего в состав кузова входит около 500 элементов. Они соединяются между собой чаще всего точечной электросваркой. Производящие ее сварочные линии могут иметь протяженность до 200 м.
Сборку кузова и точечную сварку осуществляют более 100 роботов. Они разбиты на определенные группы: одни роботы занимаются сборкой и сваркой заднего пола кузова, другие собирают капот и т.д. Этого позволяет добиться введенная в их электронную память программа. Изменив программу, можно назначить роботам ведение работ по другим деталям.
Обычно на автомобильных заводах имеется комплекс механической обработки, на котором выполняются одни из главных автоматизированных процессов производства: изготовление шестерней, валов, деталей рулевого управления и т.д. Огромная площадь состоит из десятков автоматических линий, множество деталей передвигаются от станка к станку. Здесь также установлены роботы, снимающие детали с конвейера, устанавливающие их на станок, в контрольный или моечный агрегат, а затем возвращающие на конвейер.
Благодаря специальным робокарам произведенные в различных цехах завода и прошедшие термообработку детали загружаются на единый конвейер, где происходит их финальная сборка. Установкой и настройкой сложных электронных механизмов, а также слежением за всеми производственными процессами занимаются уже многочисленные рабочие завода. Собранные автомобили, прежде чем поступить на продажу, занимают места на специально отведенной площадке или тестируются на специализированном треке.
Видео по теме
Войти на сайт
или
Забыли пароль?
Еще не зарегистрированы?
This site is protected by reCAPTCHA and the Google Privacy Policy and Terms of Service apply.
Завод Ford Sollers находится в Набережных Челнах (Республика Татарстан). Кроме него, в городе располагается предприятие «КамAЗ». До 2011 года здесь производились автомобили SsangYong и Fiat, а ещё раньше — «Ока». Сейчас на заводе делают кроссоверы Ford EcoSport, а в 2015 году к ним добавится Ford Fiesta. Всего в России три завода Ford Sollers — ещё два находятся в особой экономической зоне «Алабуга» и во Всеволожске. The Village побывал на предприятии в Набережных Челнах и узнал, как там собирают автомобили.
Завод изобилует яркими цветами: жёлтые сварочные пистолеты, синие тележки, красные монорельсы, оранжевые балантёры и хангеры, разноцветные провода. Интересно, что оформлением пространства занимался промышленный дизайнер — для создания комфортной атмосферы.

Детали для EcoSport завозятся из более чем десяти стран, но сейчас активно работает программа локализации, благодаря которой у завода появилось 50 российских поставщиков. К концу года долю российских комплектующих хотят довести до 40 %. При этом не все поставщики могут сотрудничать с Ford Sollers — их производственная система должна соответствовать требованиям Ford.
Сначала на линиях в цехе сварки подсвариваются отдельные узлы автомобиля — моторный отсек, передний пол, задний пол, днище кузова и боковины. Потом роботизированный комплекс формирует кузов. Этот процесс полностью автоматизирован. После формирования геометрии на кузов устанавливается крыша. Это делают с помощью видеосистемы. На контрольные мониторы выводятся возникающие ошибки, и это помогает корректировать работу.
Каждая пятая конструкция проверяется на предмет соответствия стандартам качества в лаборатории измерения геометрии. Там выясняют, всё ли правильно сварено. В этом помещении температуру воздуха всегда держат на уровне +20 градусов, чтобы компенсировать сезонную погрешность: зимой металл имеет свойство сужаться, а летом расширяться. Измерение происходит по более чем 200 точкам методом механического касания. Допустимый отход от нормы — 1,5 миллиметра. Отчёты с результатами измерений уходят в цех сварки для коррекции линий.
Перед покраской кузов проходит предварительную подготовку в 11 ваннах. Здесь происходит промывка, активация, фосфатирование, катафорезное грунтование поверхности, нанесение противошумной и шовной мастики. После этого кузов сушится и попадает в камеру окраски, где роботы покрывают его вторичным грунтом и цветным покрытием. Сейчас используется восемь цветов, но их количество может меняться — в зависимости от заказов дилеров. После завершающей полировки сверкающий кузов может ехать дальше.
Потом он идёт на ленточный конвейер в цех сборки, который состоит из трёх линий — «Трим», «Шасси» и «Финал». Сначала к кузову присоединяются защитные чехлы, щумоизоляция, моторный отсек, жгутоустановка салонного пучка, подушки безопасности, тормозные трубы, педали, кондиционер, IP-панель. Чтобы рабочий знал, какие детали использовать, к каждой машине прикрепляется манифест — документ с обозначением типа комплектации.
На втором посту линии снимаются двери. Позже они опустятся на ту же машину, с которой их сняли. До этого момента они дополняются стеклоподъёмником, электропроводом, шумо- и виброизоляцией, панелью, динамиками, зеркалами заднего вида и другими частями.
В цехе работает много женщин. По словам руководителя отдела, именно они в основном становятся бригадирами. Вообще, несмотря на то что автомобильное производство принято считать тяжёлым и трудоёмким, ещё в 1914 году половина функций не требовала от людей физического напряжения и могла выполняться одинаково успешно как мужчинами, так и женщинами.
На некоторых постах стойки с деталями снабжены горящими фонариками — по одному в каждом отсеке. Когда рабочий берёт деталь, он выключает фонарик, чтобы снова не схватить её по ошибке при сборе того же автомобиля. Вместе с людьми в цехе трудится один робот: он наносит клей на стекла. Автоматизация процесса позволяет избежать попадания чрезмерного количества клейкой массы и предотвратить протечку.
На линии «Шасси» корпус движется по хангерам, каждый из которых поднимается на определённую высоту — в зависимости от роста человека, который работает на каждом посту. Интересно, что принцип вертикального положения на работе ввёл Генри Форд ровно 100 лет назад: «Поднятие рабочей плоскости на высоту руки и дальнейшее дробление рабочих движений… привели к сокращению рабочего времени до 1,33 часа для шасси», — писал он в своей автобиографической книге. На линии «Шасси-1» устанавливаются трубки кондиционера, теплозащита, топливный бак, амортизаторы, фильтры, клеятся логотипы. Болты на днище кузова маркируются после каждой затяжки — чтобы работник знал, что он не только наживил его, но и затянул. Клиенты порой по незнанию принимают такую маркировку за признак брака.
Важная часть сборки — стыковка кузова с трансмиссией (на заводе его называют «свадьбой» или декингом). Трансмиссия подаётся с помощью автоматических шаттлов, которые передвигаются по напольному кольцевому монорельсовому конвейеру.
Далее идёт установка выхлопной системы, карданного вала, происходит окончательный монтаж механических групп с помощью манипуляторов для электронного программируемого инструмента. На линии «Шасси» также устанавливаются сиденья, бамперы, колёса, запаска, соединяется рулевая рейка. В конце находится пост контроля — там осматривают кузов перед тем, как отправить его на «Финал». Происходит заливка тормозной, омывающей и охлаждающей жидкостей в автомобиль. После этого собирается задняя дверь багажника и передний моторный отсек. Там же устанавливаются фары и крепятся двери, а с помощью сканера проверяется электроника. Контроллер проверяет качество сборки.
Сотрудники завода проверяют электронные системы машины, углы установки колёс и пучки света фар. Потом автомобиль проходит динамические испытания на ролл-тесте — проверяется, как работает двигатель и коробка передач при разгоне до 110 км/ч. В самом конце тестируется скорость закрывания дверей и лакокрасочное покрытие, проверяется устойчивость автомобиля к протечке. Затем машина выезжает на испытательный трек, где происходит её окончательная проверка в действии. Потом автомобиль выезжает на склад готовой продукции, после чего отправляется дилерам.